Japan’s petrochemical industry is in trouble. Again.
The last round of cutbacks and shutdowns occurred in the mid-2010s when ethylene production capacity fell from 7.6 million metric tons per year in 2014 to 6.4 million tons in 2016.
Back then, however, the closures resulted in a boost to the bottom line, with two of the country’s largest petrochemical businesses Mitsubishi and Sumitomo both doubling their profits.
Now, the situation looks even more serious with the Japanese economy mired in decades long minimal growth, an aging population which is getting smaller, unstable crude oil prices, the political and public pressure to lower carbon emissions, and a burgeoning competitor in China who is rapidly expanding production.
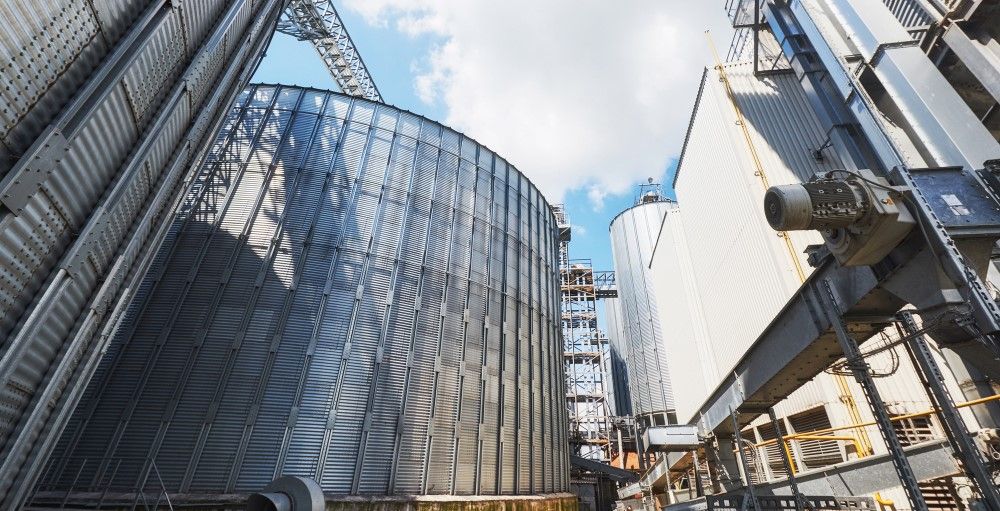
The result is that Japanese petrochemical businesses are losing money or barely breaking even. Which has led to industry talk of plant closures, layoffs, and cutbacks, as the sector aims to re-organise itself into economic health.
As Mitsubishi Chemical Group’s incoming CEO, Manabu Chikumoto, made clear when he said, “We cannot survive unless we undergo a major transformation.”
Other Japanese petrochemical companies are also considering reorganising their structures and business models. With Mitsui Chemicals’ CEO Osamu Hashimoto, “considering optimal production of ethylene and polyolefins through collaboration with other companies.”
It is a logical move, given the economic challenges facing the sector. Mitsui Chemicals also has a facility located in an industrial hub in Chiba on Japan’s east coast where Sumitomo Chemical, Idemitsu Kosan, and Maruzen Petrochemical also have chemical production plants.
“We will implement what we can,” adds Hashimoto, “including rationalization and streamlining of facilities.”
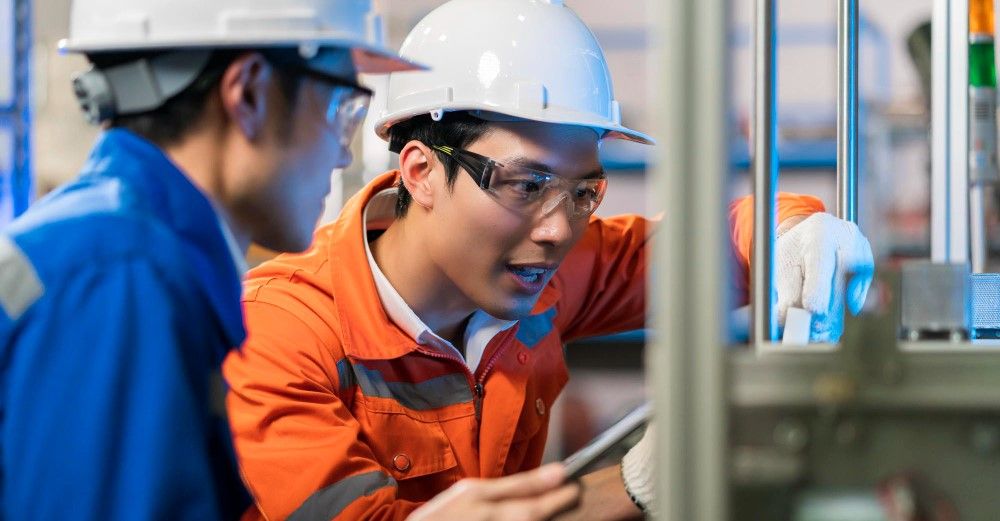
Koshiro Kudo, President of Asahi Kasei (a major chemical producer with global sales in excess of $18 billion) is like-minded. Recently announcing that, “We have begun to consider collaboration with other companies in western Japan with regard to optimization of naphtha cracker capacity.” While Keiichi Iwata, Sumitomo’s president, also claims to be, “studying rationalization through joint operations by multiple companies.”
But much of the collaboration talk hides the fact that the sector is down-sizing. In March of last year, Mitsui shutdown a polypropylene factory at its Chiba location and Asahi Kasei is selling a portion of its commodity chemical capacity with a combined annual revenue of roughly $700 million.
It is a situation which Masanori Kawakami, a petrochemical industry consultant describes as “unprecedented shuffling”.
However, most eyes are on the health of Mitsubishi Chemical Group which is still looking for stable economic conditions despite its 2021 pledge to divest its petrochemical and coal-chemical units.
That plan was laid out by Jean-Marc Gilson, the group’s Belgian CEO and much-lauded first non-Japanese CEO. With years of experience at Dow Corning and Roquette, Gilson looked to be the business leader needed to re-model the petrochemical giant. Now, three years’ later, he is to be replaced by the 35-year Mitsubishi veteran, Manabu Chikumoto who has a new vision for the business.
“My biggest mission is to participate in the reorganization of the petrochemical industry,” he declared at a recent press conference. “The momentum for reorganization in the industry is stronger than ever.”
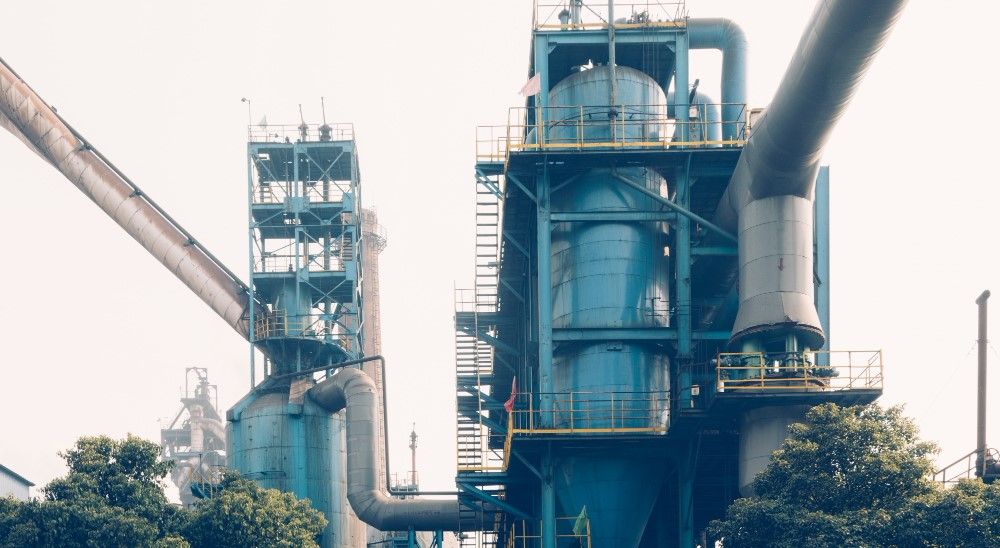
However, Japanese industry does not modernise as quickly as its neighbours.
“The essential structure of the industry, which still operates 12 ethylene crackers, is unchanged,” explains Katsumori Matsuoka, a petrochemical analyst at C&EN. “The industry continues to depend on exports from old, small, and uncompetitive facilities.”
The Japan Petrochemical Industry Association points to the continued success of its export market, valued at $10 billion worth of petrochemicals in 2021 against only $2.4 billion of imports. But many believe that this hides the coming storm, with China, “a traditional export destination for Japanese petrochemicals” expanding its chemicals sector rapidly. This expansion includes the construction of an additional 32 million tons of ethylene capacity and 43 million tons of propylene capacity over the next half decade.
“The supply-demand gap will not be resolved for several years,” says Kawakami.
That is not to say that Japan’s chemical industry is sunk, and it certainly won’t go down without a fight. Plans are already underway to modernise and refocus towards a more sustainable model, and the sector has declared its environmental goals, including a carbon neutrality target date of 2050.
“In order to solve the problems of research and development, limited resources, and time, we need to show the best performance as an industry, involving the government rather than fighting on an individual-company basis,” says Chikumoto. “It is important to have many companies participate.”
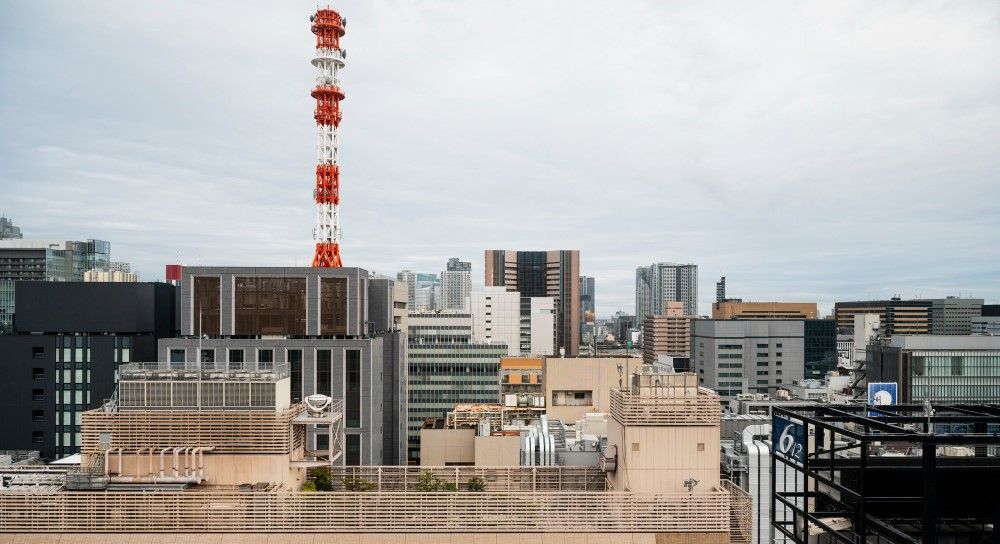
In this sense, the Japanese chemical industry is not alone. Like Europe, it is has been plagued with economic stagnation while being squeezed by foreign competitors with easy access to fossil fuels. And just like Europe, with its bold Green Deal, it hopes to re-invigorate its entire manufacturing and chemicals industries based on sustainability, innovation, and a circular economy.
But just like Europe, that leaves a major challenge for the massive petrochemical conglomerates with decades of doing business by turning gas and oil into consumer goods.
However, while the big names of Europe, like BASF and Bayer, look to set up new petrochemical facilities in more profitable markets, the Japanese sector looks set to remodel in place.
“I expect that a trend will emerge to build one large, competitive, carbon-neutral ethylene supply base each in the east and west,” says Kawakami. “It will take a certain amount of time to realize, but Japan has the technology to do so.”
It would be a bold move to invest against the flowing tide of trade. But such an ambitious project could also be the reinvigoration that both the chemical industry and the wider Japanese economy needs.
It could even be the Oriental wisdom which the European chemical sector needs to learn from.
Photo credit: Standret on Freepik, Freepik, Fanjianhua, Lifestylememory, & eveningtao