With raw material prices remaining volatile, manufacturers are constantly on the lookout for reliable suppliers of industrial ingredients.
In light of this, some garment makers have taken to sourcing recycled material as a way to lower costs, as well as to create a more sustainable end product.
One such cooperation is between the German industrial chemical giant BASF and global fashion retailer Inditex who have manufactured a jacket composed entirely of a nylon 6 created from 100% textile waste.

As the industry journal Plastics Today reports, “Every component of the jacket, made by Inditex brand Zara and available worldwide, is created solely from loopamid, BASF’s new polyamide 6.” This was made possible by using what the companies have called a ‘design for recycling’ approach, which enabled the fabric, buttons, filling, hook and loop, and even the zipper to be made from entirely from recycled textile waste.
The recycled textile is made by chemically breaking down the feedstock into a monomer liquid called caprolactam. This is then purified and polymerized into polyamide 6 resin which can be spun into new materials or fibres.
The waste was reclaimed from a combination of both post-industrial and post-consumer sources, which BASF claims “exhibits the same characteristics as virgin polyamide and can be recycled multiple times.” Helpfully for other garment manufacturers considering making the switch towards more circular raw materials, the reclaimed fabric is compatible other materials, such as elastane and PA6, allowing textile-to-textile recycling.
“BASF has reached an important milestone toward circularity in the fashion industry and pioneered an approach to close the loop for nylon textiles," said Dr Ramkumar Dhruva, president of BASF’s monomers division. "Our loopamid has the potential to revolutionize the PA6 market for the better. We are in the process of scaling up our technology to serve our customers with commercial quantities. The capsule jacket together with Inditex is the proof that circularity is possible, and we are eager to further drive the sustainable transformation of the textile industry.”
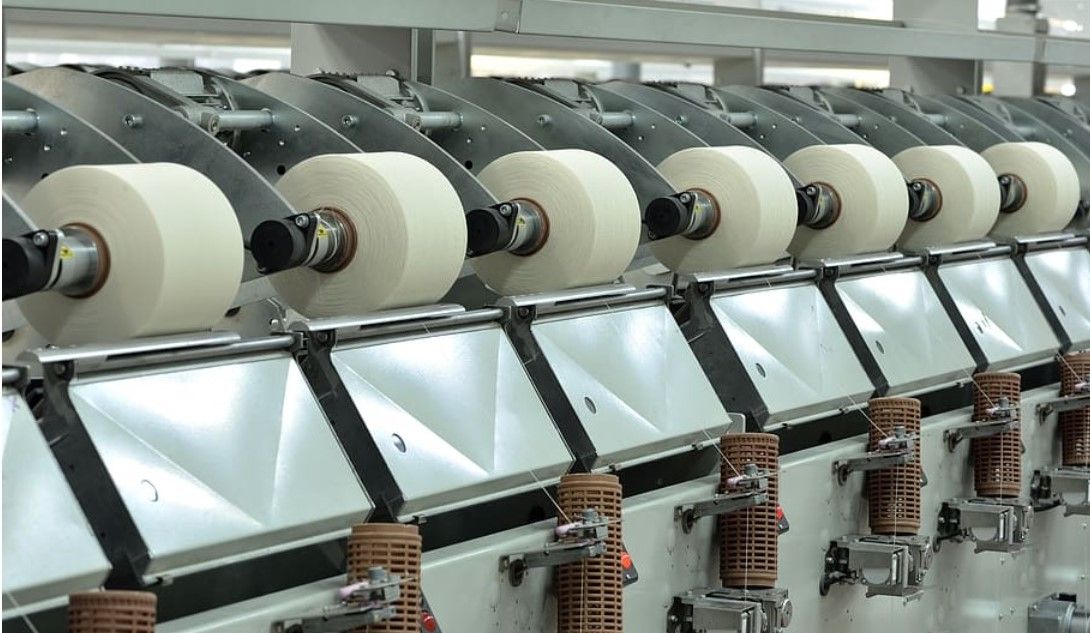
A further example of the manufacturing sector adopting more sustainable raw material sourcing is evident in the use of waste and residue from biomass-derived products or recycled raw materials to produce a carbon fibre called Tenex made with sustainable acrylonitrile (AN).
Manufactured by Teijin Ltd. at the company’s Mishima plant in Japan, the carbon fibre has already received ISCC Plus–certification, with the company claiming it to be comparable with fossil fuel-derived alternatives.
“The sustainable AN has the same physical properties as petroleum-derived AN, while Tenax carbon fiber based on this material delivers the same performance and processing attributes as equivalent fossil-based Tenax products,” the press release states. “This similarity allows customers to easily drop in Tenax carbon fiber made with bio-based or circular materials, helping to reduce greenhouse gas (GHG) emissions throughout the product's lifecycle.”
The move is part of Teijin’s plans to move towards a wider variety of sustainable products, including the carbon fibre precursor polyacrylonitrile (PAN), as well as intermediate products such as prepregs and short fibres.
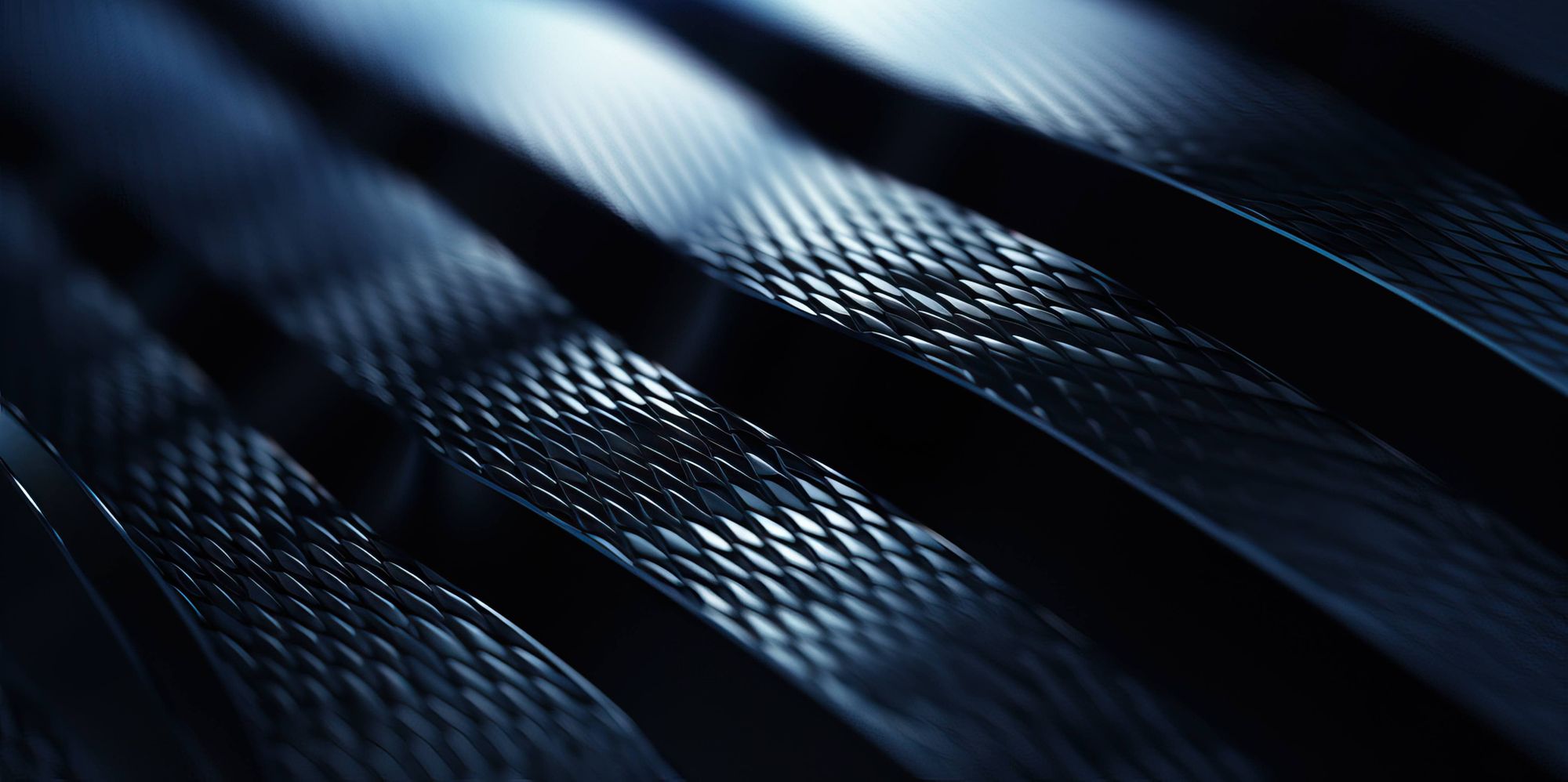
Other practices being adopted by manufacturers include the use of organic cotton instead of conventional cotton as it can significantly reduce pesticide use and water consumption. Additionally, implementing eco-friendly dyeing techniques and recycling textile waste can further contribute to sustainability. These measures not only benefit the environment but also promote ethical practices and enhance industry's reputation.
The textile and manufacturing industries have a significant impact on the environment. For this reason, adopting more sustainable processes and raw materials is of the utmost importance.
Key to this is the use of recycled feedstock in the textile and carbon fibre industry which can reduce carbon footprints, conserve water resources, and minimize waste generation. It also helps manufacturers reduce their reliance on virgin raw materials, which often require extensive extraction and processing, leading to environmental degradation.
Photo credit: Vecstock on Freepik, Pixexid, Wikimedia, & Wallpaperflare