In an age of increasing environmental awareness, governmental emissions targets, student climate change strikes, and Extinction Revolution protests, the plastics industry is facing strong criticism.
However, the development of a new process for the 100% recycling of polystyrene is evidence that plastics companies are moving in the right direction. A sign that the chemical industry technology which created many of the problems for the health of our planet, is also able to provide the solutions.
The breakthrough was made by a team from the ResolVe project, an operation joint funded by the German Federal Ministry for Education and INEOS Manufacturing, which is focused on improving recycling processes for chemical industry waste streams. The project is being jointly executed by Ineos Styrolution, the German-based company Neue Materialien, as well as the Institute for Processing and Recycling, and the Institute of Plastics Processing at the University of Aachen. Together these companies and educational institutions have found a practical solution for the processing of polystyrene waste into its purest form.

As the project’s press release reports, “The ResolVe project team now has proof of concept of closed loop recycling. The process converts waste polystyrene back to pure styrene via a depolymerisation process which results in a quality identical to virgin polystyrene.” This was achieved due to, “[Polystyrene’s] Technical properties such as its low ceiling temperature which enables recycling under conditions that can be achieved in a twin-screw extruder.”
Adding that, “Polystyrene is one of very few polymers that can be converted back into its specific monomer.”
While the process isn’t simple, it is highly effective, and begins with a straightforward milling of the mixed and cleaned polystyrene to pieces less than 30 mm in any dimension.
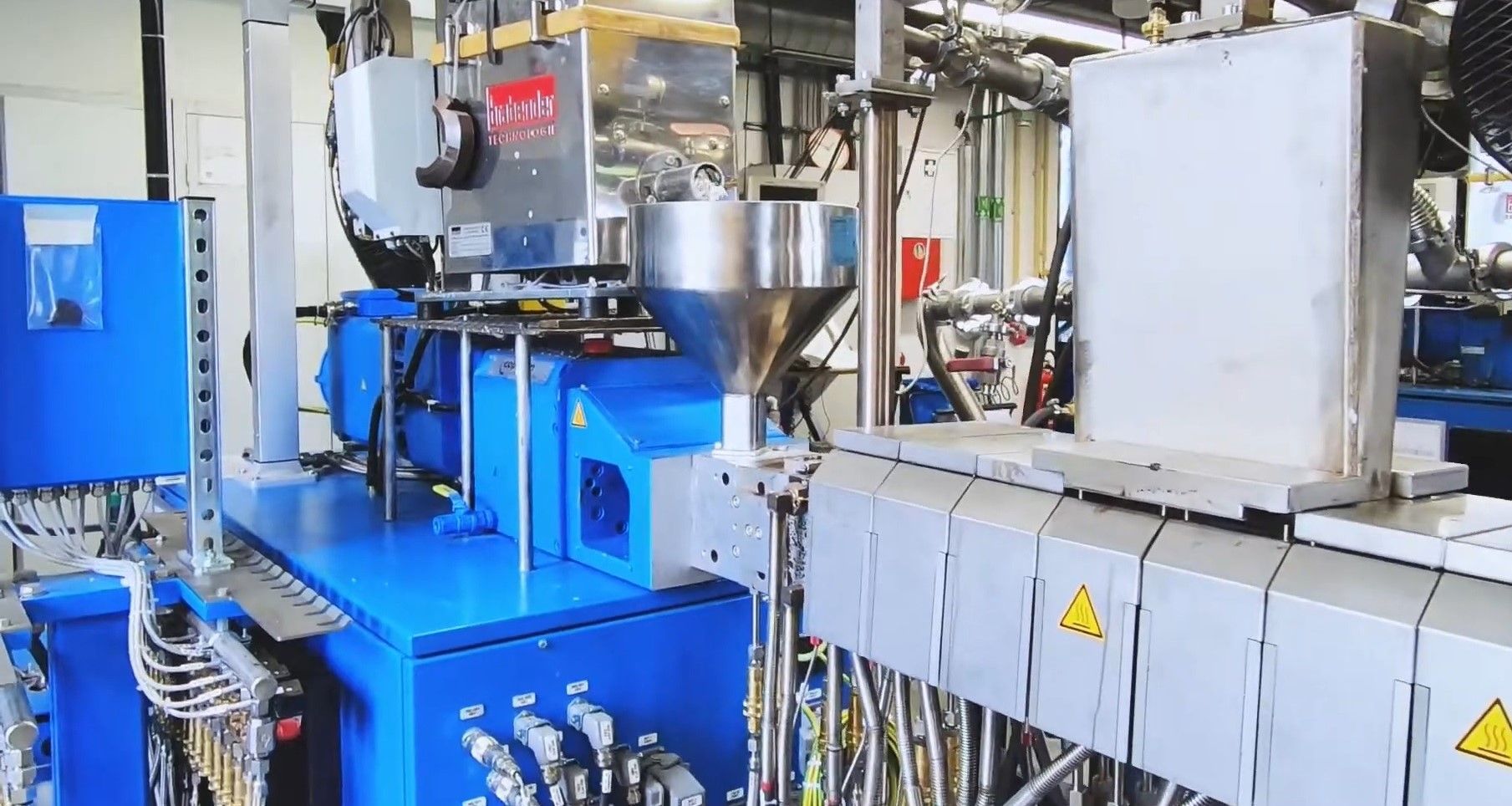
Once the milled polystyrene is poured into the extruder’s hopper, it is taken to a furnace that heats it to its melting point. The process continues through several further stages, as Philipp Schafer, a Ph.D. researcher at the Institute of Plastics Processing, explains, “Then, at the first vacuum dome a vacuum pump removes moisture and oxygen from the process. The actual depolymerization process begins afterwards. The polystyrene is heated far above its melting temperature, a high energy input that allows the polymer chains to be broken, resulting in styrene monomer. This is present in gaseous form and is drawn off from the twin-screw extruder with a vacuum via the second and third domes. The gas is then transported to a separator where it condenses and can be bottled as styrene oil.”
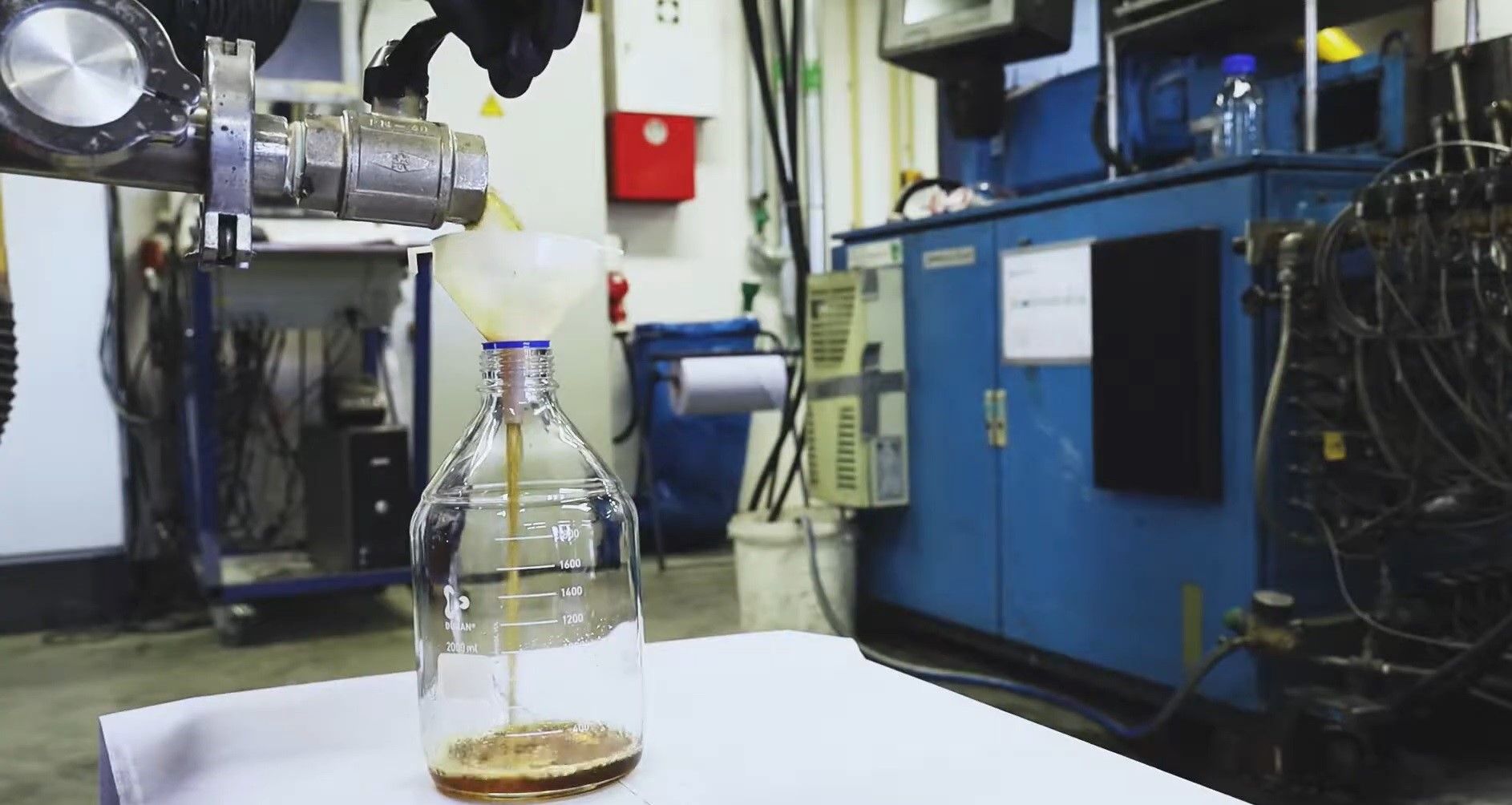
In general, “The depolymerization process operates at a temperature range of between 350 and 600 degrees Celsius in which the polystyrene is thermally overstressed and degrades. This project used a string screw extruder to study the degradation process and to evaluate the different input materials.”
To achieve this breakthrough required years of research and the analysis of fundamental questions on the make-up and recycling of plastics. As the industry journal Plastics Today, explains, “… this includes the yield of styrenics in the chemical recycling process and the impact of non-styrenic waste contamination.” Adding that, “It turns out that the chemical recycling process of polystyrene is sensitive to PET contamination. On the other hand, it is hardly impacted by contamination with polyolefins of up to 10%.”
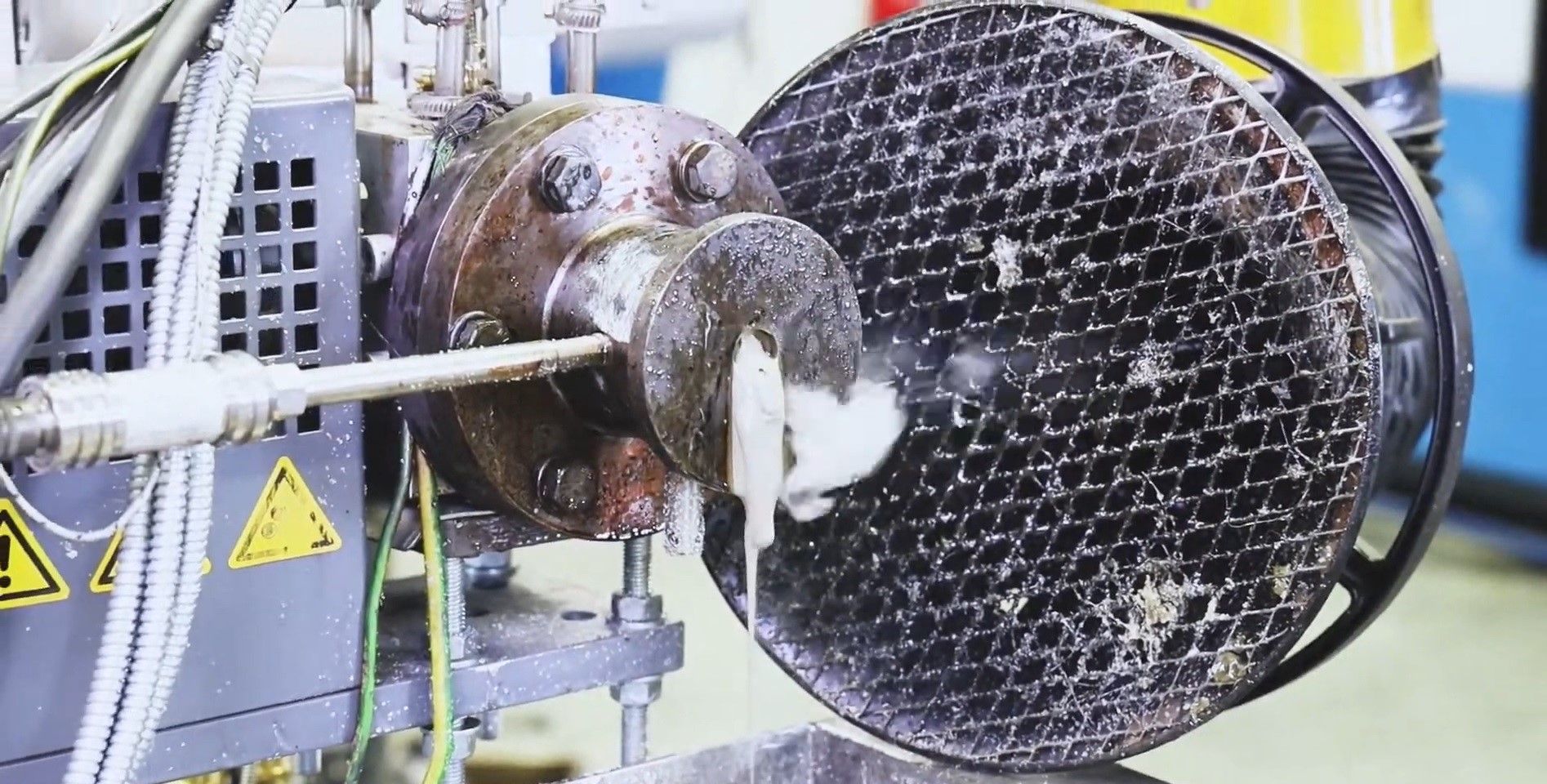
The team is now liaising with waste collectors and sorters, as well as working on a path to up-scaling the process to an industrial and economically viable size.
Meanwhile, the rest of the plastics community is already showing interest in the accomplishment, including the presentation of the project’s findings at the Bayreuth Polymer Symposium in Sept 2019.
As Norbert Niessner, Director of Global R&D and Intellectual Property at Ineos Styrolution, notes, “We can clearly say that polystyrene is indeed made for recycling. Together with today’s progress in sorting technologies of post-consumer waste, I am confident that there is no longer a reason for polystyrene not to be recycled.”
However, the breakthrough is just one part of an industry wide analysis of how plastics manufacturers can reduce their environmental impact, either by limiting plastic waste in rivers, oceans, and landfill, or by restricting fossil fuel consumption and CO2 emissions.
Alongside other chemical companies, INEOS has realized the importance of closed loop raw material sourcing on three levels; as an economic route to savings; as a positive affect on brand image; and as the right thing to do towards the planet's health.
As a result, INEOS has put sustainability at the core of its mission, with a “Supplier Code of Conduct that extends its compliance with environmental, health or safety standards and fair business practices up the supply chain”. This includes the establishment of a R&D system which includes, “An innovation process - from the sampling of ideas to the launch of the finished product - based on stage gate logic.”
These are changing times, certainly for industry and the chemicals and plastics industry in particular. However, technological advances, such as the recycling of polystyrene will help them inch ever closer to joining the circular economy; and that’s something that ecologists, businesses, and raw material suppliers can all be pleased about.
Photo credit: Ineos Styrolution, YouTube, & Packagingdigest