The chemical industry is a vital cog in the global economic machine, responsible for producing a vast array of essential products that power modern life. Yet, the productivity of the workers within this complex environment is often overlooked.
While throughout its history the chemical industry has boasted of its high investment levels and attention to R&D, but this has proved less effective in staying competitive with other sectors. As the chemical industry journal CheManager reports, “During the last 15 years, European companies have invested up to 7% of their annual revenues in new plants, better equipment, digital technologies and continuous improvement. However, productivity has remained disappointingly low. In contrast, at a global level, several other asset-intensive industries have achieved up to six times greater improvements in labor productivity in that same period.”
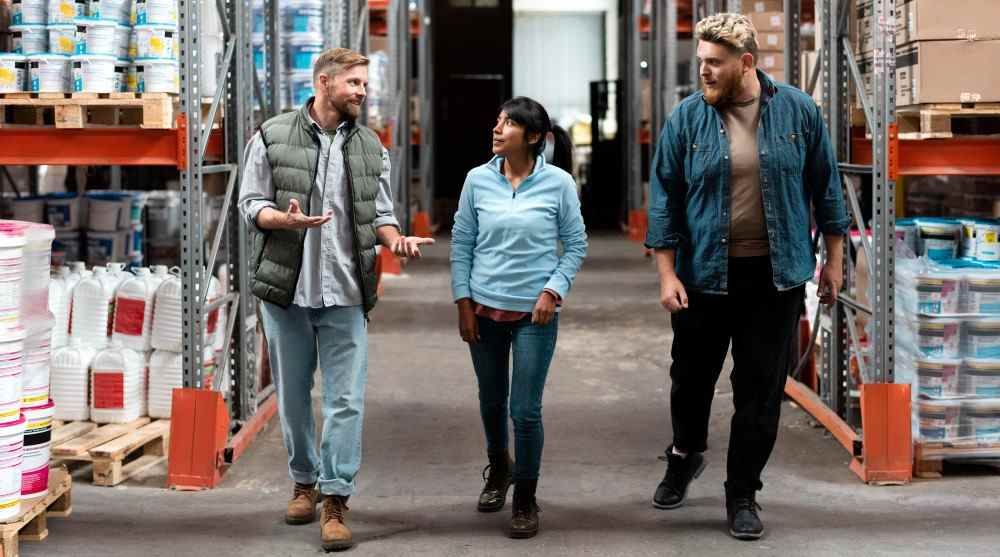
Maximizing the output and efficiency of chemical industry employees is a multifaceted challenge, requiring a delicate balance of advanced training, cutting-edge technology, stringent safety protocols, and a relentless focus on continuous improvement. But a recent report on the issue by chemical industry analysts at Accenture has outlined three key approaches that chemical industry executives should consider if their businesses are to survive the crisis.
These solutions are laid out in brief as follows:
1. Reorganising to Boost Worker Productivity.
When constructing new facilities, chemical companies frequently copy existing workflows and plant designs. While this approach can minimise construction and architecture costs, they ignore potential savings which could be gained through increased workforce output, as they do not reimagine or reorganise worker roles or their rethink how personnel relate to updated machinery and chemical processes.
In this way, new technologies result in only small, incremental changes in work processes, leading chemical companies to miss out on bigger productivity benefits.
The report even presents an example, noting how a company which has invested in a technology might be able to automate 20% of a role. Noting how, “If the work isn’t reorganized, the people in the role will do something else with the time gained. But if the company combines roles, it can free one FTE position for every five workers. And that really adds up. If companies can save a few hours for each person across several thousands of roles, they will achieve considerable savings and reduce the need to replace employees as they retire, easing pressure on recruitment.”
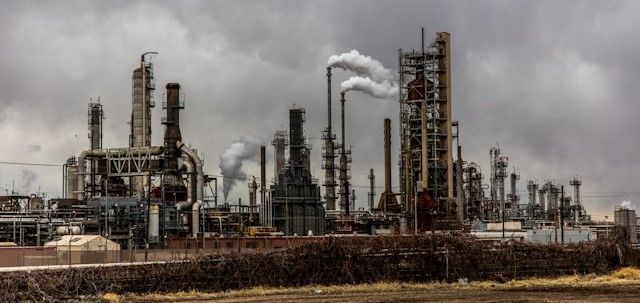
2. Investing in Specialised Training.
Successful chemical businesses require comprehensive plans that address the following:
· determining the skills needed and developing them through training.
· gathering knowledge from departing personnel.
· disseminating that knowledge to new hires or those assuming new roles.
The ultimate goal is to move away from manual, transactional labour and towards analytical, design, and execution-focused work.
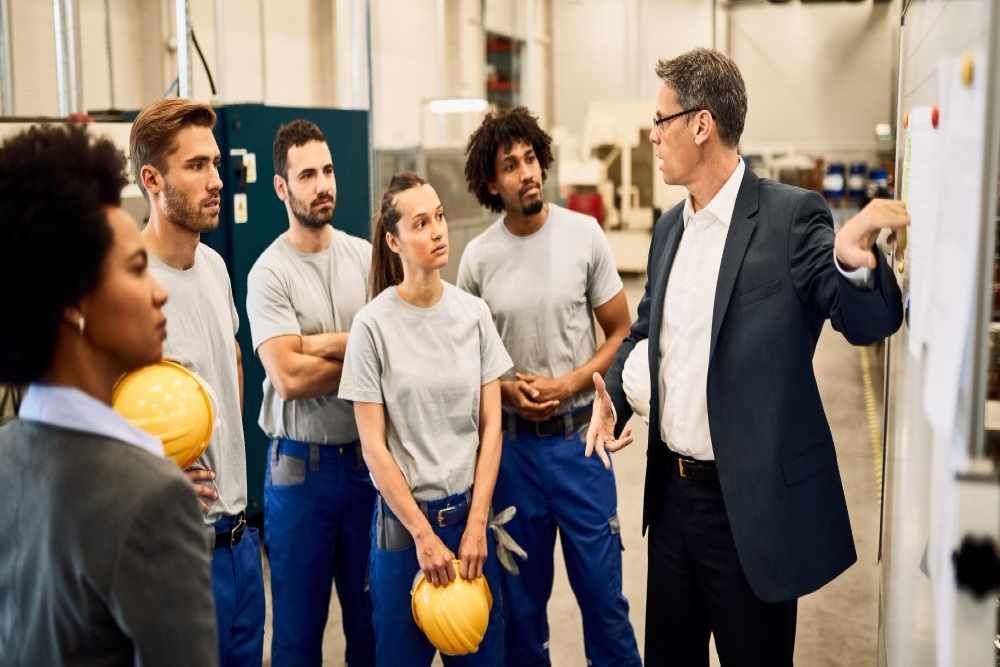
3. Developing the Know-how to Consistently Reorganise Workflows.
Since change is constant, reorganising is a permanent task. For this reason, chemical industry executives must develop the capacity to constantly innovate how workers integrate with modern technology as it develops and opens up new avenues. This entails assigning personnel with the skills necessary to create new teams, reorganise work according to job descriptions, and maximise labour productivity.
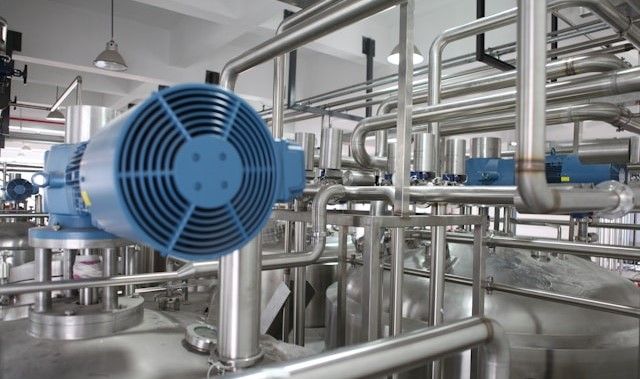
In addition to these recommendations, it is also important for chemical companies to foster a positive, collaborative work culture, as employees who feel engaged, supported, and recognized for their contributions will naturally be more motivated to excel. Embracing digital technologies like automation, data analytics, and collaborative software can further augment human capabilities, automating mundane activities, and revealing insights to guide decision-making.
Related: EU Leaders Talk Openly about Chemical Sector Decline and The Chemical Industry’s Next Great Shortage: Skilled Labour
Ultimately, a multifaceted approach targeting both the human and technological aspects of the workplace is essential for chemical firms seeking to unlock new levels of productivity and stay ahead of the curve in their fast-paced, innovation-driven industry.
For if chemical companies are to handle the worsening crisis of an older workforce which will soon retire without sufficient chemical engineering graduates to replace them, then a re-think of how workers are employed will be required. For with as many as 30% of chemical industry employees aged fifty and over, then a solution to the issue must be found, and it must be found soon.
Photo credit: Drazen Zigic, Freepik, Patrick Hendry on Unsplash, Macrovector, & Crystal Kwok