One of the holy grails for the chemical industry is solving the issue of plastic waste.
As a material and as a feedstock it is priceless for making just about everything. However, it is typically made from crude oil and requires vast amounts of energy to manufacture using processes which create enormous amounts of CO2 emissions. Furthermore, the strength and durability which makes plastic so desirable, also makes it notoriously hard and expensive to recycle. The result is millions of tons of plastic ending up in landfill, incineration facilities, or the ocean.
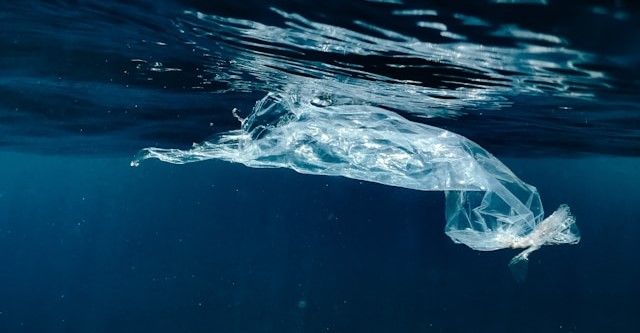
However, some of the smartest brains in chemical research have recently outlined simple ways in which the chemical industry could improve recycling efficiency as well as setting out ‘three pillars’ for a circular plastics sector.
Stirring
Mechanical recycling involves a loss of quality after each cycle, which ultimately leads to a polymer which is not strong enough to be reused and must be disposed of. Chemical recycling on the other hand is a process where the long-chain plastic molecules (polymers) are broken down into their basic building parts (monomers), which can then be reassembled to create new, high-quality polymers, resulting in a cycle that is genuinely sustainable.
However, a closer look at the mechanics of chemical recycling by researchers from Federal Institute of Technology (ETH) in Zurich has found that the approach to stirring the polymer mixtures can be improved to increase recycling efficiency.
As the university press release notes, “Through experiments and computer simulations, the research team demonstrated that the plastic is best stirred using an impeller with blades parallel to the axis. Compared to a propeller with angled blades or a turbine-shaped stirrer, this results in more even mixing and fewer flow vortices. The stirring speed is equally crucial. It must be neither too slow nor too fast; the ideal speed is close to 1,000 revolutions per minute.”

“The molten plastic is a thousand times thicker than honey. The key is how you stir it in the tank to ensure the catalyst powder and hydrogen get mixed right through,” explains Antonio José Martín, one of the leading scientists in the research group.
Different stirring heads, such as a propeller shape, a cog-looking ‘turbine,’ and an ‘impeller,’ were all compared to observe the difference and improvements in recycling technique possible.
The result is a formula which allows future recycling scientists to accurately calculate the mixing control and the influence it will have on the catalysts that they use. It also allows for the same scientific principles to be applied to industrial scale recycling facilities.
“It’s every chemical engineer’s dream to have a formula like this at hand for their process,” says lead researcher Prof. Javier Pérez-Ramírez.
A dream that will hopefully result in a completely circular plastics industry.
Recycling, Carbon Capture, and Biomass Feedstock
A broader study into how the plastics industry can achieve circularity was conducted by Prof. André Bardow and his colleagues from ETH Zurich, assisted by researchers from RWTH Aachen University and the University of California, Santa Barbara. Together they took a holistic look at how much plastic the planet’s landfill, waterways, and environment can handle in terms of waste and emissions before collapsing. Deducing that 74% of all plastic produced must be recycled if the chemical industry is to remain within, what the team call ‘planetary boundaries.’
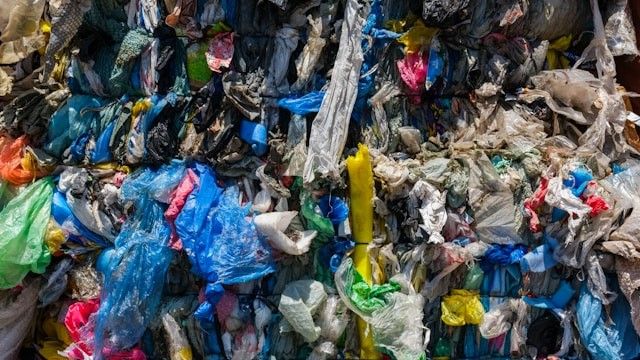
“Increasing the recycling rate to 74 percent worldwide is a very ambitious goal,” Bardow admits.
Currently, according to the study, only 15% of plastic is recycled in Europe, the largest recycling region on the planet.
For this reason, the team has highlighted three routes (or pillars) to plastic recycling which must be maintained for environmental balance. These are, as follows, recycling, carbon capture, and biomass feedstock.
Three Pillars to Circular Plastic
Only fourteen products, including polypropylene, polyethylene, and polyvinyl chloride, make up 90% of the plastic manufactured. Yet all of these polymers are recyclable.
“Recycling efforts should be intensified wherever possible,” says Bardow. “More recycling of plastic always leads to more sustainability.”
The remaining 10% is made up of other polymers which are hard or uneconomical to recycle, such as polyurethane foams.
According to Bardow, new industrial methods for recycling these products need to be developed. However, in the meantime, two more pillars should be utilised - carbon capture and utilization (CCU) and the use of biomass as a polymer feedstock.
“Recycling alone won’t do it; we need all three pillars,” adds Bardow.
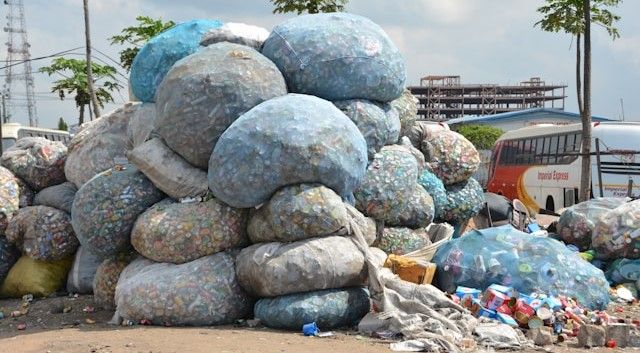
To achieve this goal, the researchers highlight the need for greater cooperation between plastic manufacturers and users. In this way, responsibility for plastic would not end at the factory gate but would continue by considering disposal methods and sustainability.
“Plastic is considered cheap, which for a long time was a blessing but has now become a curse,” says Bardow. “Given its outstanding properties, we should view plastic as the high-quality material it truly is. That way, it would be okay for it to cost a little more, and its recycling, too.”
Whether or the goal of a 100% circular plastics industry is achievable, polymer producers, manufacturers, and end consumers must all do more to improve recycling rates and lessen the environmental damage of plastic waste and the emissions made in production.
Only then can plastic remove its toxic image.
Photo credit: Naja Bertolt Jensen, Brian Yurasits, Ryan Brooklyn, Engin Akyurt on Unsplash, & Gencraft