Scientists have found a way to produce fluorochemicals at scale in a safe and more sustainable manner - a discovery which could reduce feedstock costs for agriculture, pharmaceuticals, refrigeration, electric vehicle construction, and other manufacturing sectors.
The novel process involves the use of oxalic acid to extract a variety of fluorine compounds from the raw material fluorspar. According to the chemists behind the discovery, it is easily scalable for industrial production as it functions under mild conditions at room temperature.
The current industrial method used to produce the fluorine compounds the manufacturing sector requires fluorspar and concentrated sulphuric acid in a process which works at temperatures of more than 200°C. The result is the feedstock hydrogen fluoride, which can then be converted into a number of fluorochemicals. However, in addition to the damage to the environment from the energy needed to heat the reaction, the handling and synthesis of hydrogen fluoride is dangerous and expensive due to its extreme toxicity and corrosiveness.
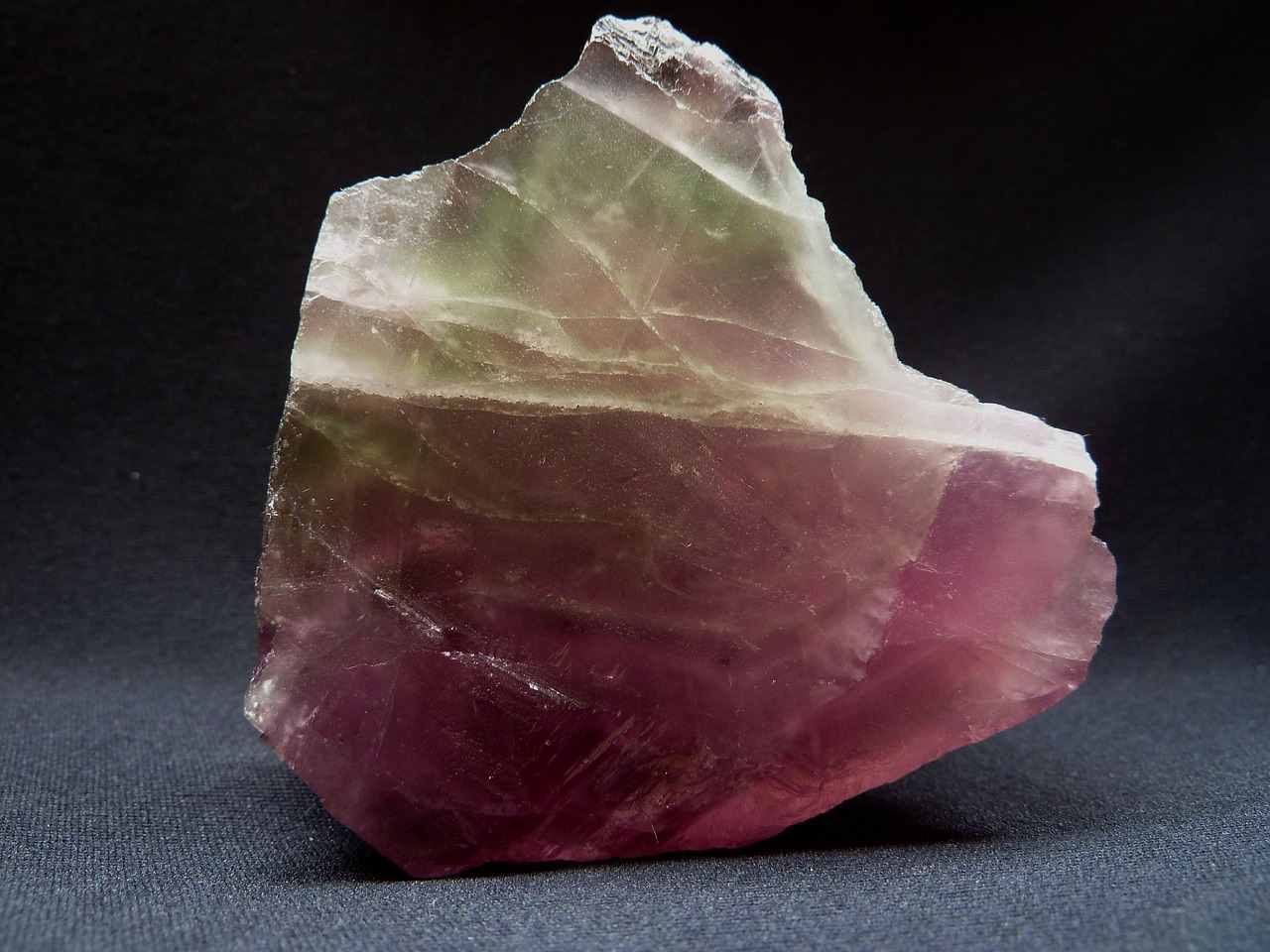
The research team, working at Véronique Gouverneur’s lab at Oxford University, have now published their findings in the journal Nature, where they describe how their discovery could fundamentally change the supply chain for many chemicals. Specifically stating that, “The production of fluorochemicals directly from fluorspar offers the possibility of decentralized manufacturing—an attractive model for the fluorochemical industry. With the renewed interest in innovative methods to synthesize oxalic acid via carbon dioxide capture and biomass, and the challenges posed by our dependence on fossil fuels for sulfur and therefore sulfuric acid supply, our technology may represent a departure towards a sustainable fluorochemical industry.”
“The synthesis of fluorochemicals from fluorspar with no reliance on the complex supply chain of hydrogen fluoride is one of the biggest challenges in fluorine chemistry,” explains the study’s co-author Anirban Mondal. “We have overcome this challenge with methods producing new and known fluorinating reagents.”
At the heart of the sustainable process is the need to remove the calcium content and access the fluorine from the mineral feedstock fluorspar. After testing a variety of acids, the researchers found that fluorspar, oxalic acid, and either silicon dioxide or boric acid could be used. Not only were these raw materials readily available, but they were also solids which were easy to handle and transport at an industrial scale.

“When the three solids were mixed in water at room temperature the oxalic acid reacted with fluorspar to produce calcium oxalate, an insoluble salt,” explains a report on the breakthrough in the journal Chemistry World. “Meanwhile, the boric acid or silicon dioxide formed strong boron–fluorine or silicon–fluorine bonds. The calcium oxalate was then removed easily by filtration, leaving behind an aqueous solution of either fluoroboric acid or hexafluorosilicic acid.”
Related articles: Low Cost, One Hour Process Recycles PET from Mixed Plastic Waste or Plastic to Soap: Young Chemist’s Eco-Dream Turns to Reality
From these industrial ingredients it is possible to produce many chemical raw materials needed by industry, such as tetrafluoroboric acid, tetraalkylammonium fluorides, alkali metal fluorides, and fluoro(hetero)arenes.
“This work demonstrates unequivocally that the supply chain of hydrogen fluoride is not necessary for the production of fluorochemicals accessible upon nucleophilic fluorination,” observes Mondal. He also highlights the sustainable nature of the process and how it could revolutionise the way that fluorochemicals are produced. Noting that, “Our protocol based on oxalic acid aligns well with the current challenges facing the chemical industry including pathways to decarbonisation and defossilisation.”
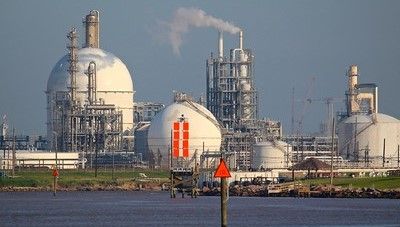
While the use of fluorspar as a raw material for producing fluorochemicals is not a new concept, this environmentally friendly process offers a significant improvement over traditional methods by minimizing the environmental impact and hazards associated with the production of these essential industrial chemicals.
The primary advantage of this greener process lies in its reduced reliance on harsh, corrosive chemicals. Sulfuric acid poses serious safety and disposal challenges, often leading to the release of toxic by-products that can contaminate surrounding ecosystems. In contrast, oxalic acid, though currently more expensive, is a milder and more manageable reagent, allowing for a cleaner, safer, and more sustainable fluorochemical manufacturing operation.
This shift towards a more eco-friendly production method is a welcome development, as fluorochemicals play a crucial role in a wide range of industries, from refrigeration and air conditioning to the manufacture of specialized plastics and pharmaceuticals. By adopting this innovative approach, companies can not only reduce their environmental footprint but also contribute to the growing demand for sustainable, responsible practices in the chemical sector.