In today’s intense business climate, there is a fine margin between profit and loss for chemical companies. Every nudge in pricing, every blip in supply logistics, and every kilo of wasted raw material compile and compound to find the difference between failure and success.
Pushing the envelope of efficiency requires employing an army of chemical industry workers to manage computerised chemical processes, data analysis, sales support, and in-depth research of chemical products and markets.
And coordinating this pool of talent and resources requires its own special tool.
Step forward Enterprise Resource Planning (ERP) systems—a single, centralized platform which can smoothly integrate all of a chemical manufacturer’s or supplier’s key business processes.
At its core, an ERP system coordinates—inventory management, production planning, procurement, finance, compliance, and customer relationship management—into a single, management structure. For chemical manufacturers and suppliers, this centralized approach helps streamline operations, minimize manual input, and reduce the risk of human error. Meaning that tasks which once required multiple spreadsheets or disconnected systems can now be managed with real-time data flow across departments.
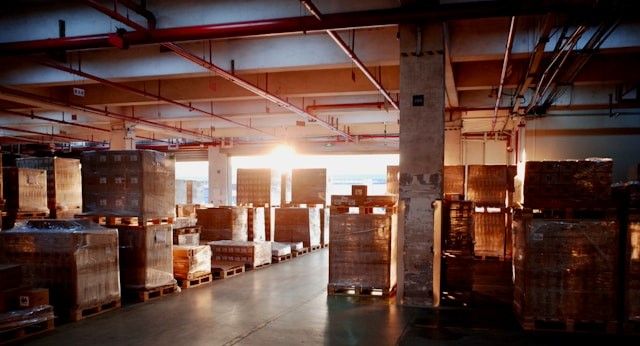
From stringent safety and environmental regulations to complex supply chain requirements and the need for precise quality control, chemical businesses which utilise ERP systems operate with increased precision, efficiency, and agility.
However, the advantages are most notable in four key areas.
Boosting Supply Chain Visibility
ERP systems provide real-time visibility into the entire supply chain, from suppliers and inventory levels to customer orders and delivery logistics. This is especially important in the chemical sector, where delays or disruptions can be costly and dangerous.
For example, ERP systems can automatically adjust procurement schedules based on raw material availability and production forecasts. This reduces overstocking or understocking issues, saving both space and money. In addition, production runs can be better coordinated with delivery schedules and customer demands, ensuring a smoother workflow from start to finish.
Related articles: How Chemical Companies Should Handle the Scope 3 Emission Guidelines or Survey finds Chemical Industry Logistics Fears are Growing
With an ERP system, chemical business managers can make better-informed decisions based on accurate data. They can identify bottlenecks, conduct real-time inventory tracking, control chemical product expiry dates, manage batch and lot tracking, predict potential disruptions, and have a better overview of what is needed when and where.
A recent report in the UK’s Chemical Industry Journal even highlights an example of transferring from a manual oversight of chemical product procurement to an ERP system, noting the benefits gained at Bernard Laboratories, a US-based chemical manufacturer.
“Everything is linked together so you can find the piece of data you’re looking for by using various criteria,” says Alece Piper, the chemical company’s Vice President. “You can’t achieve this level of efficiency with spreadsheets.”
Improving Customer Service and Business Agility
Today’s customers expect more than just on-time delivery—they want transparency, responsiveness, and customized solutions. This is why ERP systems give sales and customer service teams access to up-to-date information on order status, inventory, pricing, and customer history, enabling them to respond quickly and accurately to customer inquiries.
Moreover, the flexibility of ERP platforms allows chemical companies to adapt to market changes or customer demand. Whether it’s launching a new product, entering a new region, or responding to supply chain disruptions, ERP systems support faster decision-making and execution.
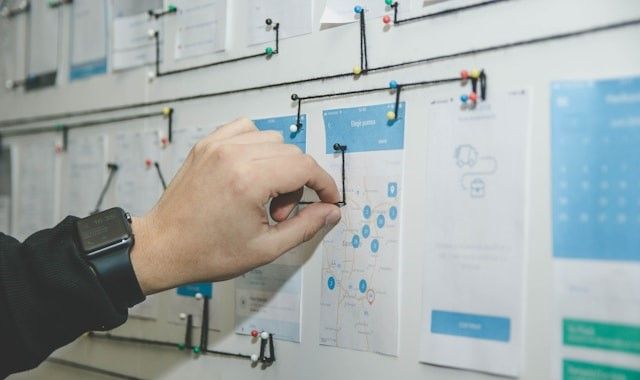
Assistance with Regulatory Compliance
The chemical industry is among the most regulated sectors in the world. Companies must comply with local and international standards such as REACH, GHS, OSHA, and ISO certifications. An ERP system can be customized to monitor compliance with these regulations and maintain documentation for audits. This includes automatic generation of regulatory reports, tracking safety data sheets (SDS) and hazardous materials, and ensuring that labelling is accurate and kept in line with industry requirements.
At Stakam, a Scottish chemical manufacturer struggling with REACH and REACH UK compliance, Alistair Watson, the Managing Director, describes the adoption of an ERP system as ‘like striking gold.’
“It’s become such an asset,” he said, “that I often grapple between wanting to keep it as our secret weapon and the desire to showcase our robust systems.”
Improved Planning and Streamlined Production
Cost control is essential for SMEs in the chemical sector as changing raw material prices and accumulated waste can easily affect profitability. With ERP software in place, chemical companies can take advantage of automated cost computation, accurate sales tracking, waste reduction, comprehensive financial reporting, and forecasting for improved decision-making.
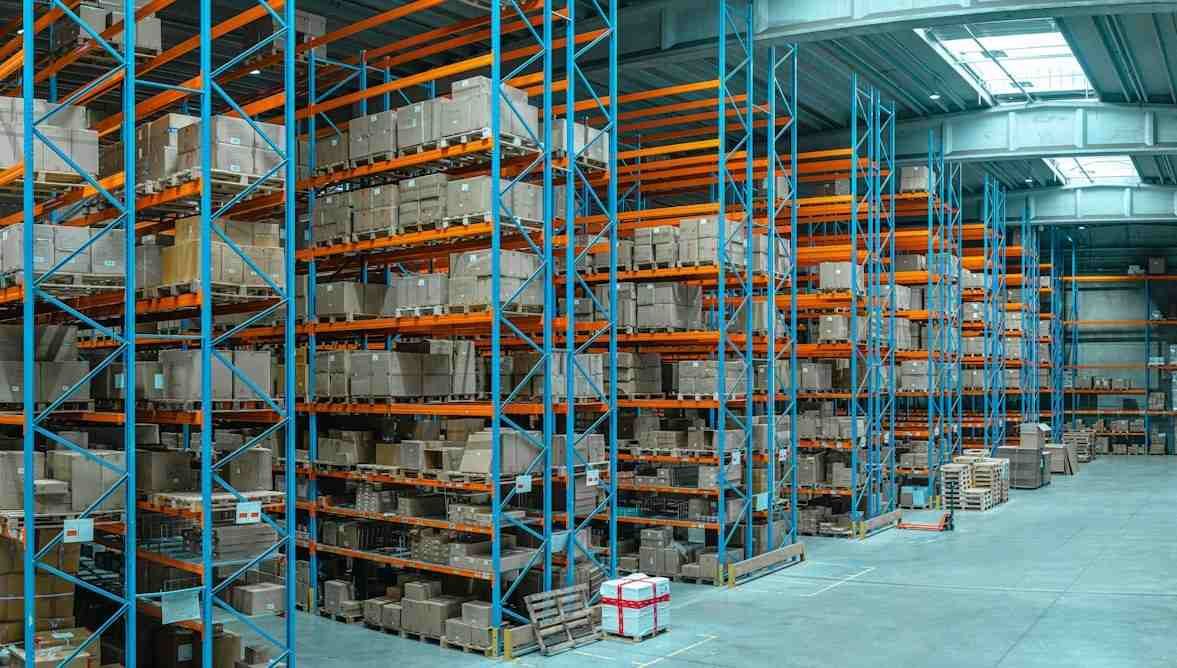
ERP software also helps manage traceability by keeping detailed records of every batch, from raw materials to finished goods. If a quality issue arises, the system can quickly identify the source and affected products, allowing for swift corrective action and limiting potential damage to the brand or customer trust.
Potential Drawbacks to Consider
While ERP systems offer significant advantages, they are not without challenges. The initial cost of implementation can be high, especially for small to mid-sized chemical companies, with the process often requiring substantial time and resources. Customizing the system to suit industry-specific needs—such as complex formulas, hazardous materials handling, or regulatory compliance—can also add further complexity.
Additionally, if not properly managed, ERP rollouts can disrupt existing workflows and lead to employee resistance. Without proper training and change management, even the most advanced system can fall short of expectations. Therefore, businesses must approach ERP adoption strategically, ensuring they choose the right provider and allocate sufficient support for a smooth transition.
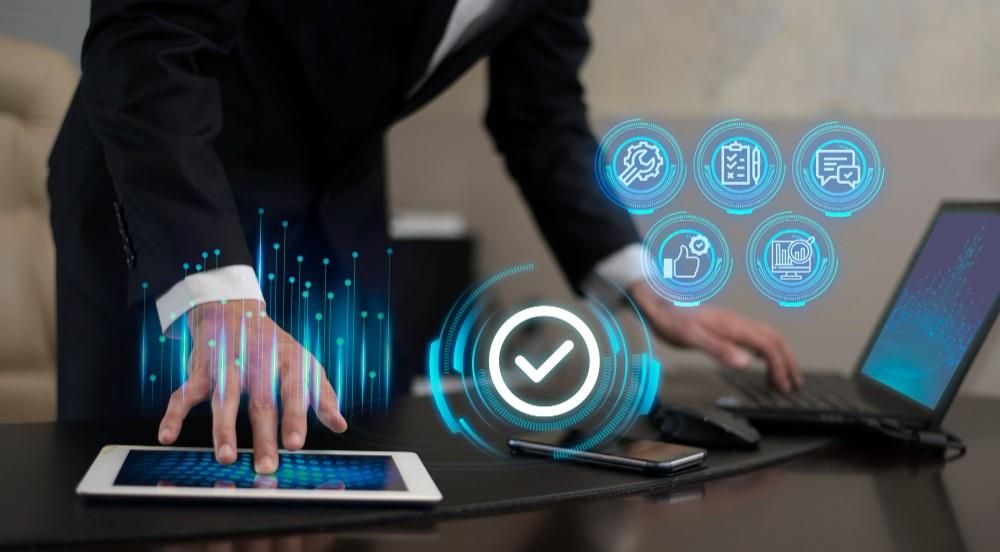
That said, many chemical businesses face rising pressures—from global competition and shifting regulations to increased customer expectation and fluctuating raw material costs. By centralizing operations and improving traceability, ERP platforms put all of these factors in a manageable context—enabling data-driven decision-making and a clearer pathway to success.
That is why many chemical companies and raw material suppliers no longer see ERP systems as a luxury, but as a strategic necessity.
Photo credit: Vida Huang on Unsplash, Jacques Dillies, Alvaro Reyes, Freepik, & Freepik