Sodium tripolyphosphate or STPP (Na5P3O10) is a concentrate form of phosphate with numerous important applications in industry, mostly notably in the manufacture of industrial and domestic dishwashing and laundry detergents.
This is due to its high cleaning efficiency when used as a filler supplemented with surfactants. But more than just filling volume, STPP also adds alkalinity, sequesters calcium and magnesium, stabilizes metal oxide colloids, and provides a surface charge to allow for peptisation and the suspension of dirt.
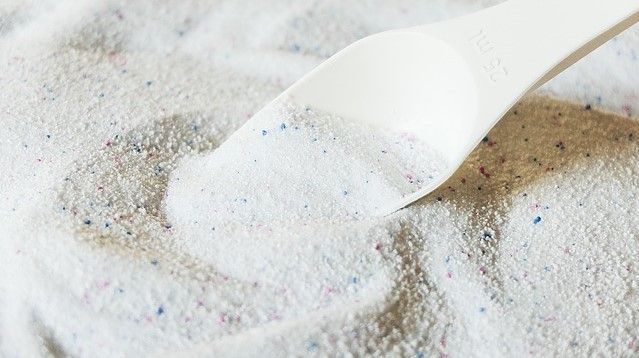
Other conventional raw materials for detergents often focus only on neutralising the calcium and magnesium ions in the water or grime. This is a practical cleaning method, as the ions prohibit anionic surfactants (such as soap and linear alkylbenzene sulfonate) from dissolving and working effectively. But as STPP can do this and so much more, it has become one of the key raw materials for detergent production.
For such a functional industrial chemical, the process for producing sodium tripolyphosphate is surprisingly straight forward, but it is important to understand the details as they can severely impact product quality.
How STPP is made
The production process typically consists of three main steps.
1. A sodium compound, for example sodium carbonate (Na2 CO3) or sodium hydroxide (NaOH) reacts with phosphoric acid to form a mixture which contains monosodium phosphate (NaH2 PO4) and disodium phosphate (Na4 HPO4). The phosphoric acid is achieved through either a wet process or a furnace process.
2. The mixture is precipitated from solution to a solid and insoluble impurities are removed.
3. The mixture is heated until it thermally decomposes or calcinates the monosodium and disodium phosphates into sodium tripolyphosphate (Na5 P3 O10). The heating also ensures that excess water is removed through volatilization.
The product must then be milled into a powder, sieved, and packed before it is ready for sale.
This process can also produce different sodium phosphate products, such as sodium dihydrogen phosphate, trisodium phosphate, and disodium hydrogen phosphate, among others.
STPP from wet process or furnace process phosphoric acid?
Sodium tripolyphosphate made from furnace process phosphoric acid is more expensive than that made from wet process phosphoric acid as the furnace incurs larger heating costs. However, STPP made from the wet process product is likely to contain more impurities. The most notable contaminants are magnesium and silicon which may prevent the STPP from being used in some end products.
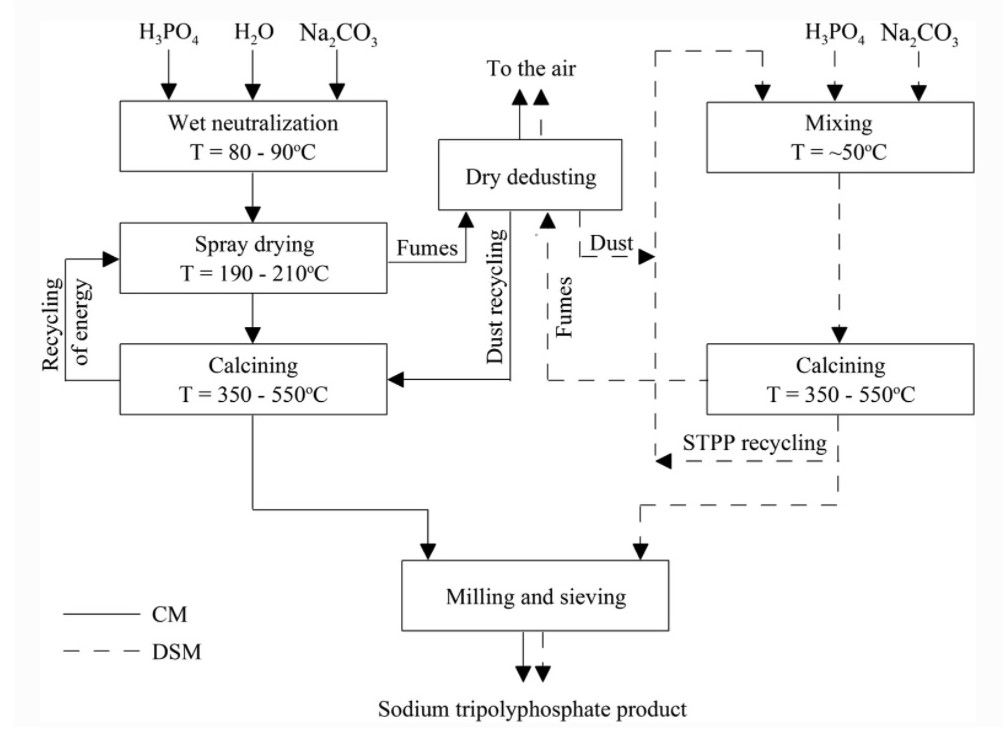
For example, silicon can cause aqueous solutions containing STPP to appear cloudy. For this reason, food processing companies often favour STPP made from furnace process acid despite the higher cost.
Classic spray method vs Dry, single-stage method
It is also worth noting when considering grades of STPP that it can be produced through two main approaches: a classic spray method and a dry, single stage method – both of which have their advantages and disadvantages.
In the classic spray method, once the phosphoric acid has been neutralized with caustic soda (NaOH) or soda ash (Na2 CO3) it is dehydrated via a spray drying process. The dried mixture is then calcined in a rotary kiln to obtain sodium tripolyphosphate.
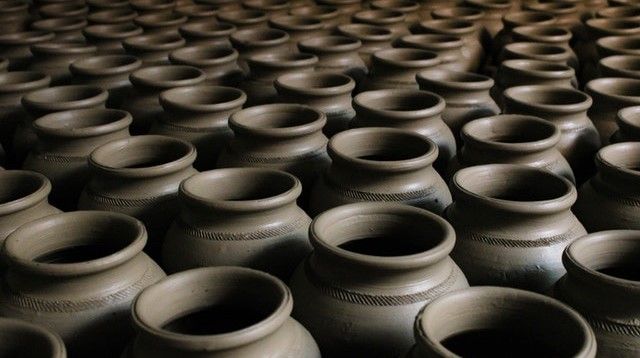
Alternatively, the dry, single-stage method neutralises the phosphoric acid with soda ash but also includes in this mixture a portion of recycled STPP. This substance is then dried and calcined in a rotary kiln in a single technical process.
Including recycled STPP to the mixture improves the process’s flow rate and protects against an agglomeration of the powder. More significantly, costs are lowered in the dry, single-stage approach as the spray method requires more energy for both drying and calcining as the phosphoric acid must be diluted for the neutralization process.
A recent study by a team from the University of Krakow and the Polish Academy of Sciences concluded that, “the dry single-stage method of sodium tripolyphosphate production to be the advantageous technological variant.” While a 2010 study published in the Polish Journal of Chemistry found that, “the production of STPP with the dry one-step method has the lowest impact on the environment among three assessed solutions.”
The quality of any raw material is very significant both in terms of price and its possible application.
It is therefore vital to only buy sodium tripolyphosphate from a trusted and respected trader or producer. It is also important to know if the phosphoric acid used was gained from a wet or furnace process, and to also consider the environmental costs of classic spray versus dry, single-stage methods.

Also key to the final quality of STPP is the quality of the raw materials used in its production, such as the phosphorus ore, silica, caustic soda, soda ash, and coke.
Unfortunately, less scrupulous suppliers of STPP may adulterate any of these input materials as well as the final STPP product to increase their short-term profits.
AG CHEMI GROUP is a trusted and well-respected supplier of sodium tripolyphosphate. They have been supplying industrial raw materials to manufacturers since 1994 and can provide high grade quality STPP (food grade) for delivery across Europe, Africa, Asia, and the Americas.
If you would like to know more about sourcing STPP please visit AG CHEMI GROUP or contact Timur on +420 777 227 387 or Timur.Khafizov@agchemigroup.eu
Photo credit: Pixabay, Vansh Sharma from Pexels, Frank Habel from Pixabay, & David Dibert from Pexels