As demand for TiO2 rises, so does demand for TiO2 replacement products which also possess the key quality of opacity, such as high white, fine particle size structured, calcined kaolins.
As the market tracking firm, MarketWatch, published by Dow Jones & Co, notes in its ‘Titanium Dioxide (TiO2) Market Research Report to 2023’, “the rising prices of TiO2 and its negative effects on humans are pushing end-user industries to use substitute products. This will hinder the growth of the titanium dioxide market during the forecast period.”
However, paint and coating manufacturers have generally found that most alternatives do not have the same high-quality colouring, and those that do, lack other TiO2 properties. As Andrew Pleeth, director at Cadam, a Brazilian-based supplier of chemical feedstock for coatings, notes, many TiO2 extension products and fillers, “are pure white, but those that have good whiteness still cannot match TiO2 for opacity or hiding power.”
Titanium Dioxide Alternatives
All too often, African paint and coating markets focus too heavily on lowering costs, but then pay the price in poor quality. Chemical raw materials that are frequently sourced by the paint and coating industry include hydrous kaolin, synthetic silicates, calcium carbonates, talc, barium sulphate, and opaque polymer. However, care needs to be taken not to substitute TiO2 with simple cheap fillers.
As Pleeth explains, “[Although] natural occurrence minerals such as clay, talc and carbonate are often used, they are regarded as a cheap way of reducing the cost of a can of paint. For the paint maker the aim is to reduce costs, but you need at the same time to maintain the necessary acceptable quality, and this is the challenge that can be most successfully achieved with the use of so-called functional extenders rather than straight forward fillers.”
Adding that, “It is clear to us all that TiO2 is not 100 percent replaceable by filler. For example, to do so you may need a thicker layer by a factor of eight to 10 to maintain comparable opacity, which is not realistic option.”
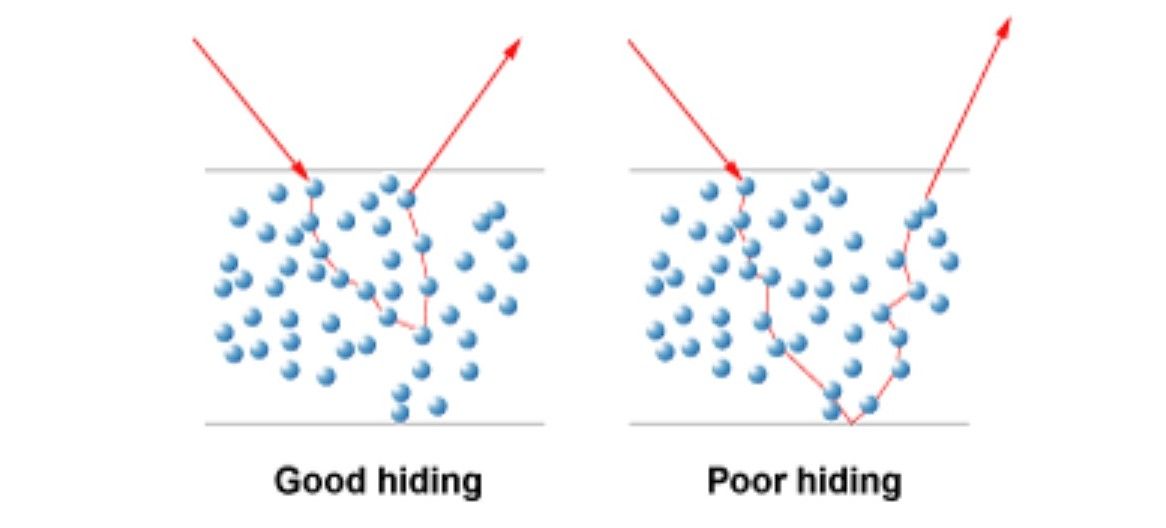
While there is no perfect replacement for TiO2, there are a number of substitute chemical products which, if handled correctly, can improve the performance of products.
For example, Pleeth explains how paint and coating manufacturers can utilize, “fine extenders for spacing and functional extenders for air entrapment together with carefully selected dispersants and functional binders.”
Additionally, optimized calcined kaolins are a practical ingredient that has been specifically designed for high PVC paint, providing significant cost savings.
Titanium dioxide is, and possibly throughout our lifetimes, will remain THE key ingredient for so many products requiring whiteness. But with prices showing no sign of decreasing, or even stabilising, chemical suppliers will need to be increasingly creative with the products they provide and the range of functional fillers and extender pigments they make available.
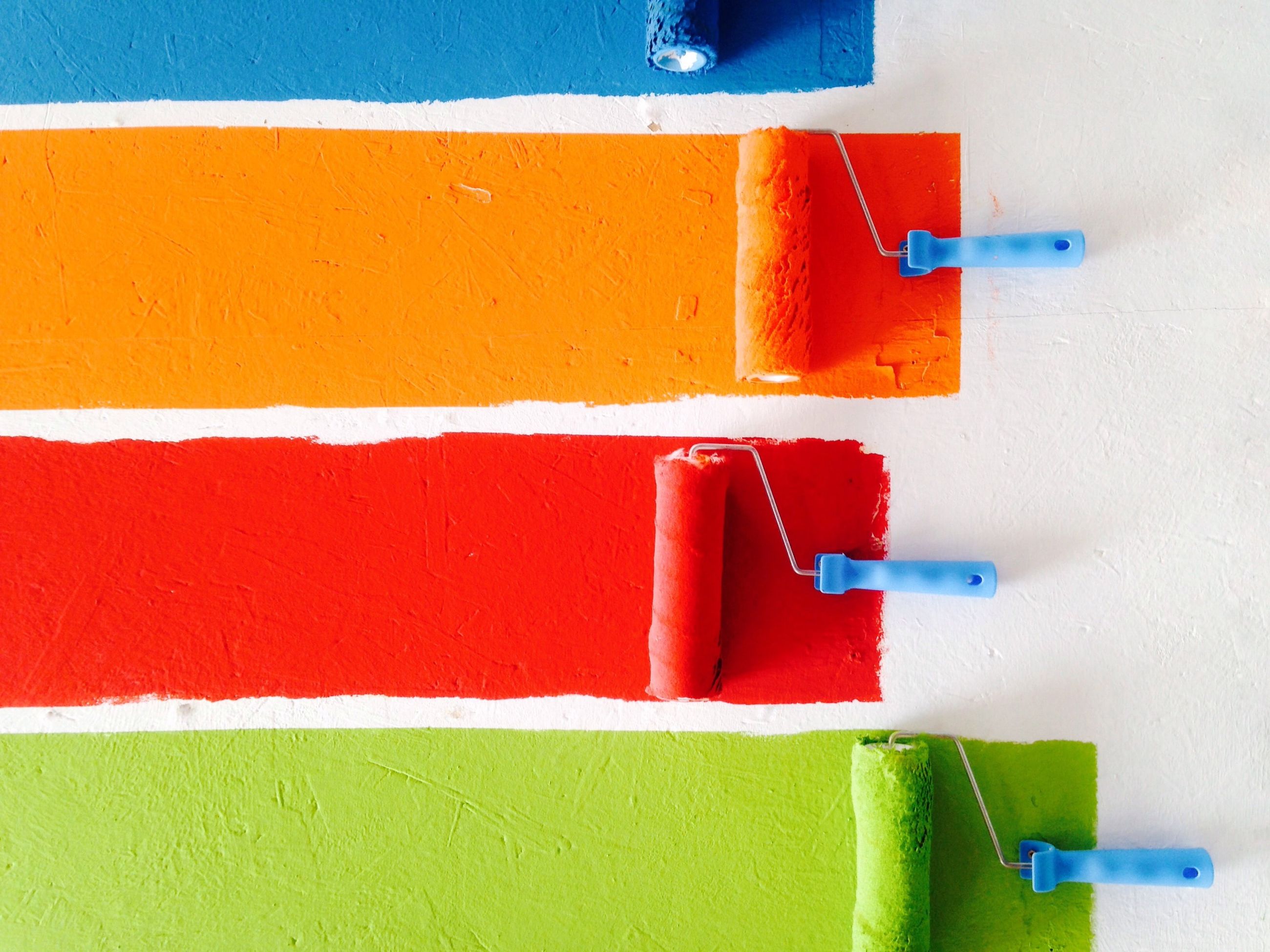
In time, TiO2 sources will dwindle, so paint manufacturers need to begin searching for alternatives and improved formulations today, if they are to maintain competitive prices tomorrow.
This is something that Pleeth believes is already happening. Stating that, “Paint makers across the globe are expanding and modernizing their production facilities with increasing technical sophistication resulting in improved quality and decreased costs of production. This, implemented together with careful selection of the latest raw materials, is now a key focus of the industry.”
Concluding that, “Today more than ever, the paint sector buyers and technical departments have a responsibility to cut costs and with the relentless increasing prices in TiO2, there are real opportunities.”
Photo credit: Coatingsgroup, Coating, Youtube, Weforum, OKchem, Miningnewsnorth, Ausimmbulletin, Handprint, Homeguides, BrandSA, & Coatings Pixabay, unsplash