Due to the wide variety of applications, ammonia is a very important feedstock. Yet it is an industrial chemical which comes with a significant environmental price tag.
That may change however, as chemical researchers from the University of Illinois Chicago (UIC) believe that they have found a way to greatly reduce the climate change impact of manufacturing ammonia, while at the same time reducing its production cost.
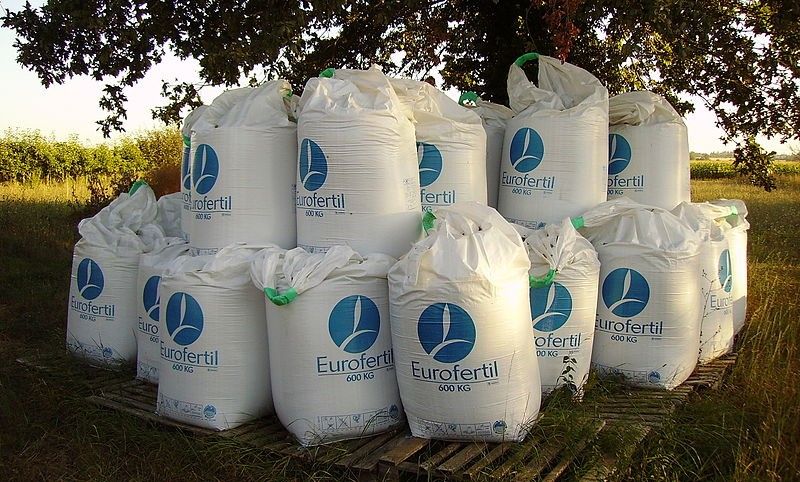
Ammonia feeds the world, as it is commonly used in the production of fertilizers providing a source of nitrogen for plants to promote growth. Ammonia is also used in the manufacturing of various household cleaning products, such as glass and floor cleaners. In the food industry, ammonia is used as a refrigerant in cold storage facilities and in the production of certain food products. Additionally, ammonia is used in the production of plastics, textiles, explosives, dyes, and pharmaceuticals. Due to its unique properties and versatility, ammonia plays a crucial role in various industries.
Yet, ammonia has a negative impact on the environment, as when it is released into the atmosphere it contributes to greenhouse gas emissions as well as the formation of acid rain. Ammonia can also contaminate water sources, leading to eutrophication and harm to aquatic life.
While proper storage and handling practices can minimize the environmental impact of ammonia, accidents, leaks, and spills still happen. Technologies such as scrubbers and catalytic converters can help reduce ammonia emissions from industrial processes, but most of the environmental damage caused is due to the high heat and large energy consumption used in its production.
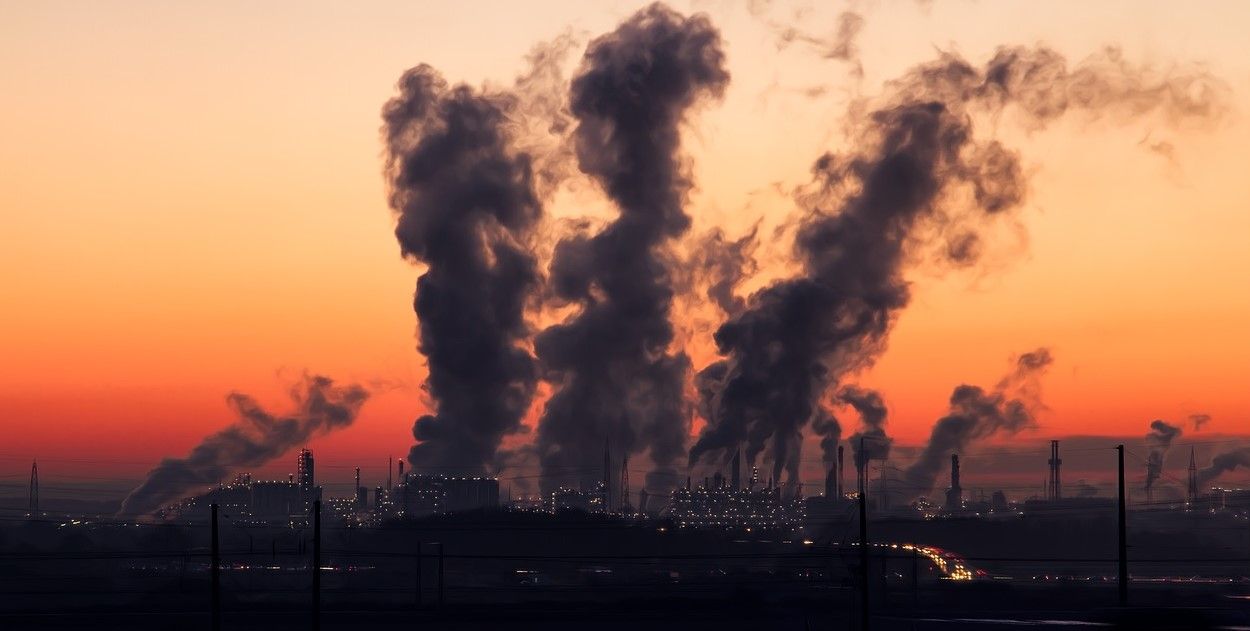
To avoid this damage, a team of chemical engineers from UIC have created an alternative production process using a well-known electrochemical reaction which they have optimized with a ‘symphony’ of lithium, nitrogen, and hydrogen atoms for industrial use.
“The process, which uses lithium to synthesize ammonia from nitrogen gas and ethanol, meets government goals for energy efficiency and low cost,” explains a recent UIC press release. With Meenesh Singh, one of the leading researchers noting that, “the process could be made even greener if powered by solar energy and fed with sustainable ingredients.”
As the online science journal Phys.org explains, “The process, called lithium-mediated ammonia synthesis, combines nitrogen gas and a hydrogen-donating fluid such as ethanol with a charged lithium electrode. Instead of cracking apart nitrogen gas molecules with high temperature and pressure, nitrogen atoms stick to the lithium, then combine with hydrogen to make the ammonia molecule.”
The new chemical process is cheaper and greener because it works at low temperatures, while also being regenerative - it restores the original raw materials with each cycle of ammonia production.
“There are two loops that happen. One is regeneration of the hydrogen source and second is the regeneration of the lithium,” notes Prof. Singh. “There is a symphony in this reaction, due to the cyclic process. What we did was understand this symphony in a better way and try to modulate it in a very efficient way, so that we can create a resonance and make it move faster.”
Incredibly, the discovery is based on a chemical reaction that has been known for almost a century.
“The lithium-based approach can actually be found in any organic chemistry textbook. It's very well-known,” says Singh. “But making this cycle run efficiently and selectively enough to meet economically feasible targets was our contribution.”
According to Sing, if the technology is scaled up, it would yield ammonia at about $450 per tonne, 60% less expensive than previous lithium-based approaches and other suggested green methods.
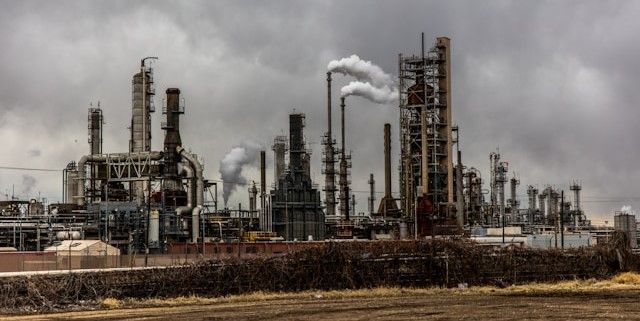
However, selectivity is also crucial because numerous attempts to clean up the ammonia production process have instead resulted in significant amounts of undesired hydrogen gas. Yet the UIC researchers seem to have also solved this challenge, satisfying US Department of Energy requirements for ammonia production on an industrial scale. Furthermore, production can be carried out in a modular reactor.
The process could also help to increase the use of hydrogen across the economy – a key environmental aim as it is a clean fuel. Hydrogen is an ideal fuel as burns easily and cleanly, but its flammability also makes it difficult to be safely and economically transported to where it is needed.
“You want hydrogen to be generated, transported, and delivered to hydrogen pumping stations, where hydrogen can be fed to the cars. But it's very dangerous,” observes Singh. “Ammonia could function as a carrier of hydrogen. It's very cheap and safe to transport, and at the destination you can convert ammonia back to hydrogen.”
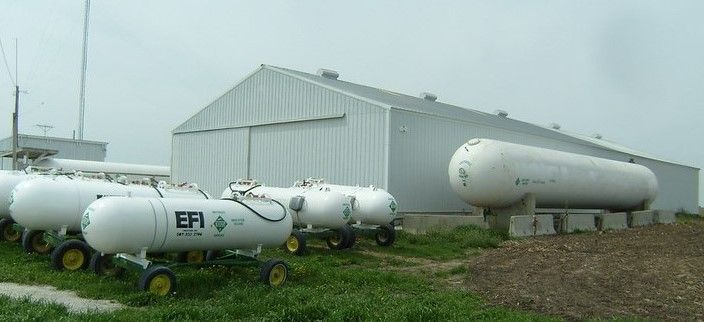
Lowering the heat required to manufacture ammonia would have significant economic and environmental benefits. With reduced energy consumption, costs can be lowered, making ammonia more affordable for various industries. This could lead to increased production of fertilizers, which are essential for agriculture and currently unaffordable in parts of the world with the greatest food shortages.
Additionally, lowering the heat for ammonia manufacture would reduce greenhouse gas emissions, contributing to a more sustainable and environmentally friendly chemical industry. A greener, cheaper chemical and a win-win process.
Photo credit: David zzyd on Freepik, Patrick Hendry on Unsplash, Wikimedia, Flickr, & Ralf Vetterle on Pixabay