The problem of plastic waste is a global issue. Of the total 350m tonnes produced each year more than half goes to landfill while 19 m tonnes enters the natural environment. Even when out of sight, the waste breaks down into microplastics which contaminate the water supply and enters the food chain.
In a perfect world, all plastics would be compostable and simply rot away into an organic and biofriendly form, in the way that plant matter does.
Knowing that some kinds of bacteria have been found to use polyesters and polyurethanes as a carbon source, nanomaterials engineer Jonathan K. Pokorski and bioengineer Adam M. Feist of the University of California, San Diego, and their colleagues decided to harness this power for a sustainable goal. To do so, the researchers looked at a number of different bacteria strains before selecting Bacillus subtilis, a component of probiotics. By using lab-based evolution and selection they were able to develop this bacterial strain into one that could withstand the high temperatures (up to 135oC) of polymer manufacture and moulding.
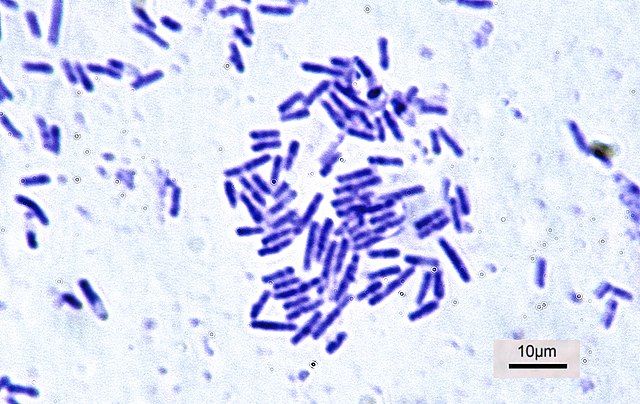
They then combined the bacteria’s dormant spores into molten thermoplastic polyurethane (TPU) to create a plastic which is not only stronger, but which also naturally and rapidly decomposes.
“Just as carbon nanofiber reinforces composites, so the spores increased the toughness of the TPU by up to 37%,” explains Pokorski. “Placed in sterile compost, the strips degraded by more than 90% in 5 months. As long as enough moisture and nutrients are around, the bacteria should wake up and degrade the polymer.”
Thermoplastic Polyurethane or TPU is just one of many varieties of polyurethane. It is a melt-processable thermoplastic elastomer with excellent durability, flexibility, and abrasion resistance. Like other thermoplastics, it can be shaped via extrusion, injection moulding, and blow moulding.
Due to its desirable qualities, TPU is widely used throughout the manufacturing sector, most commonly in automobiles (such as body parts, soundproofing padding, doors, floor mats, headrests, steering wheels, seats, etc.), in footwear, in electric cable sheathing, in adhesives, in paints and coatings, hoses, in furniture, elastic textile fibres, mobile phone casings, and sports equipment.
Prior to this discovery, several polymer research teams had already studied bio-based materials as a way to create recyclable or biodegradable TPUs. However, the end results always had poor mechanical qualities and did not compare to the durability and flexibility of conventional TPU.
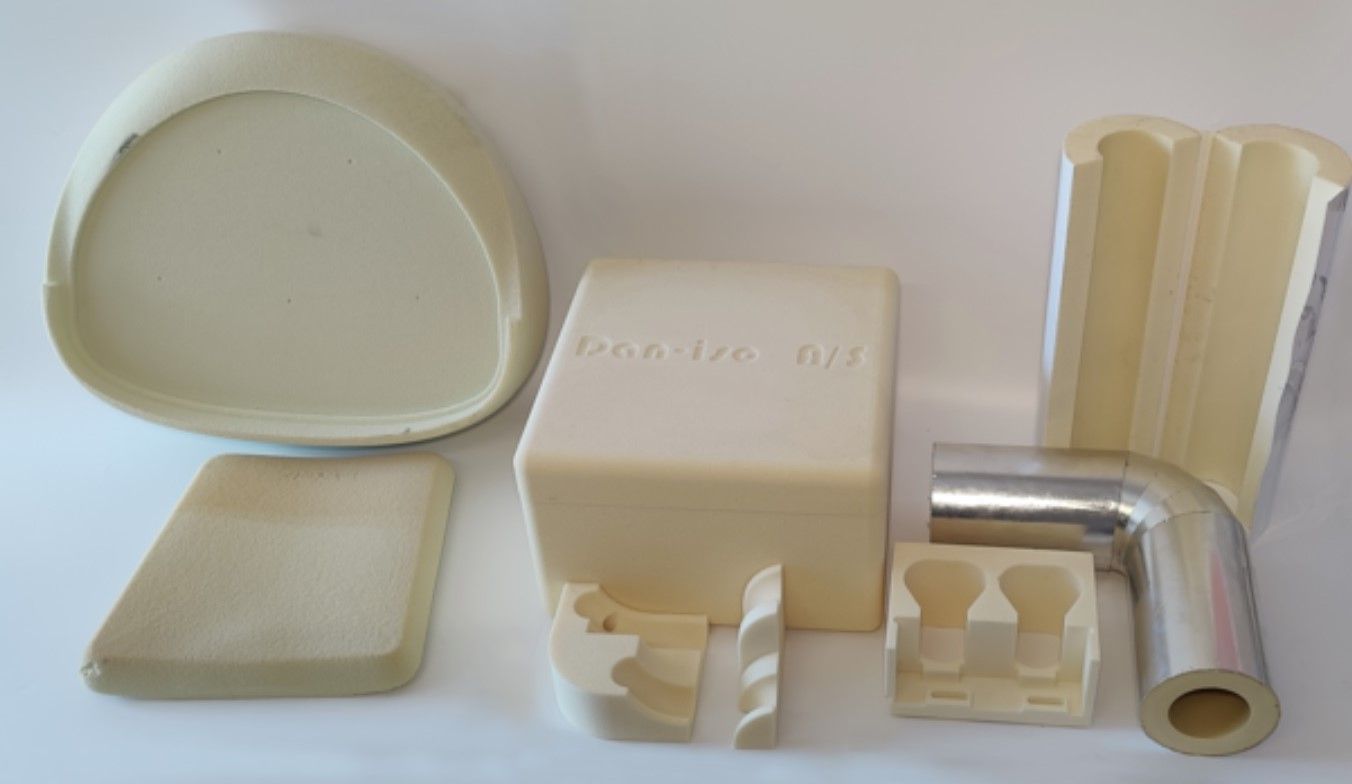
This issue may now have been resolved with spores from a polymer-eating bacteria embedded directly into a thermoplastic.
Katrina Knauer, a polymer scientist at the National Renewable Energy Laboratory has praised the discovery, noting that it was a scalable approach for manufacturing biocomposites, which was “pushing the boundaries of material science and bridging the gap with biochemistry.”
While plastic-eating bacteria are already well-known, the practicality of employing them to clean-up plastic waste has been complicated by issues of waste sorting and upscaling. This latest breakthrough avoids these pitfalls by placing the bacteria directly in the polymer. This means that they are exactly where they are needed whatever happens to the plastic product at the end of its life.
It is a discovery which may lead to even more sustainable practices or improved polymer products. As the study, now published in the journal Nature Communications, states, “Introducing live cells into polymer composites as a sustainable and smart filler material has the potential to greatly improve both material properties and their ecological footprint.” Adding that, “Live cells have ideal features as smart polymer additives such as self-replication, self-regulation, and programmable stimuli-responsiveness.”
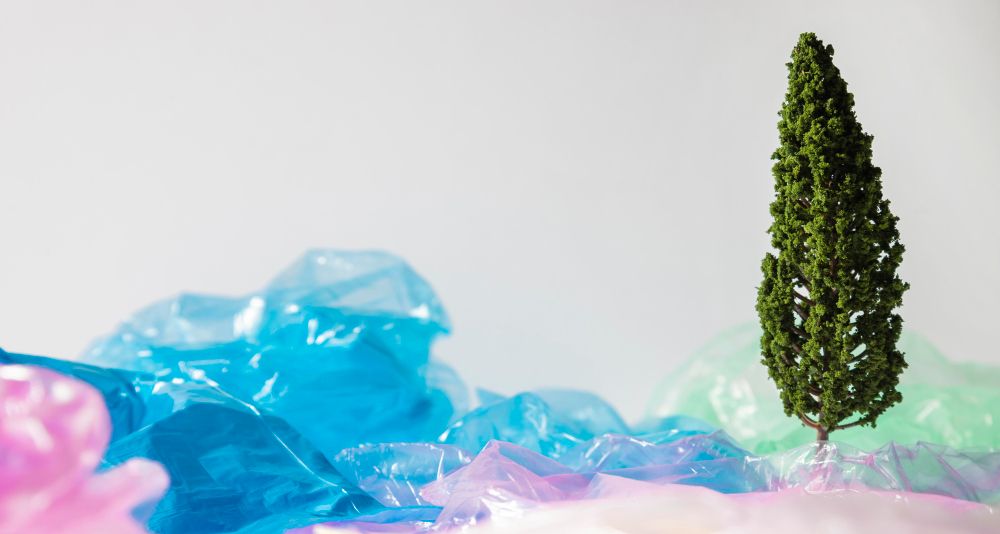
Looking ahead, the polymer researchers hope to expand the use of bacteria in other plastics. “We plan to figure out the exact enzymes and pathways involved, the end products, and the range of different polymers we can apply this towards,” says Fiest.
While there might be reservations about applying bacteria in some plastic products, such as food packaging, it could prove ideal for other manufacturing sectors. “A little bit of spores in your shoe insoles?” asks Pokorski. “I mean your feet are already pretty dirty.”