The chemical industry is a great innovator. It is also a major consumer of fossil fuels as both an energy source and as a raw material feedstock.
For a long time, chemical companies have strived to find new industrial chemical processes to lower energy consumption, reduce carbon emissions, and primarily to save money. In fact, the International Energy Agency (IEA), has published data showing that the chemical industry is the “second-largest consumer of industrial energy and is the third-largest direct emitter of CO2.”
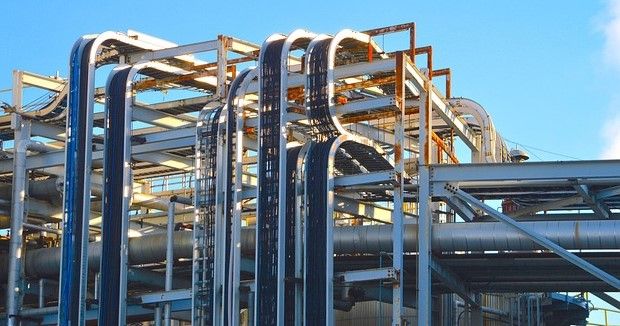
However, some researchers are now taking a different approach by focusing not on the chemistry, but on the mechanics of the chemical processes. By improving the design of the pumps and motors which drive industrial chemical production it is hoped that greenhouse gas emissions can be lowered and profits boosted.
While this may seem to be a niche approach to reducing chemical company costs or achieving net zero, industrial equipment can be highly inefficient, with some processing and manufacturing facilities operating pumps with efficiency of less than 40%.
“Across industry,” writes Stefan Floeck, a motor and pump specialist for ABB Motion, “pumping systems consume a significant amount of electricity, accounting for 10 per cent of the world’s total electrical energy consumption and approximately 20 per cent of industrial electricity usage.”
The problem originates from the short-term economic thinking used to construct many chemical facilities with cheaper, less efficient motors. However, data on the total cost of ownership (TCO) by analysts at the Business Reporter, shows that while savings can be made with lower initial capital expenditures (CapEx) around 97 per cent of a synchronous reluctance (SynRM) motor’s costs arise from the electricity it uses throughout its service life. CapEx actually amounts to only 2% of costs, with maintenance comprising the final 1%.
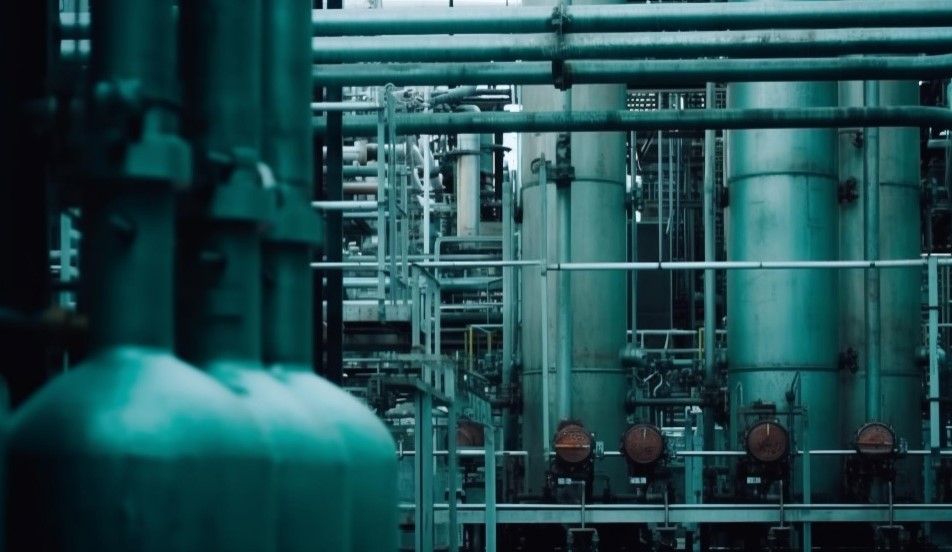
These inefficiencies are most evident in process-intensive industries, like the chemical industry, which often have high base production flows managed by centrifugal pumps running at constant speed.
It is an issue reported by the industry journal EngineerLive, which recommends using Variable Speed Drives (VSD) to lower costs and adjust flow.
“Flow control can be more precise and energy savings very large due to the ‘Cube Law’, which describes the relationship between flow output and energy input for centrifugal pumps or fans,” the report notes. “For instance, a 20% drop in motor speed can reduce its energy consumption by 50%.” Adding that, “Energy savings can be further increased by replacing induction motors with advanced synchronous motor technologies such as SynRM and ferrite-assisted synchronous reluctance (FA-SynRM).”
It is a point supported by Floeck, who can envisage the advantages of the chemical industry switching powering systems for the countless pumps, fans, compressors, and other applications present across the chemicals sector.
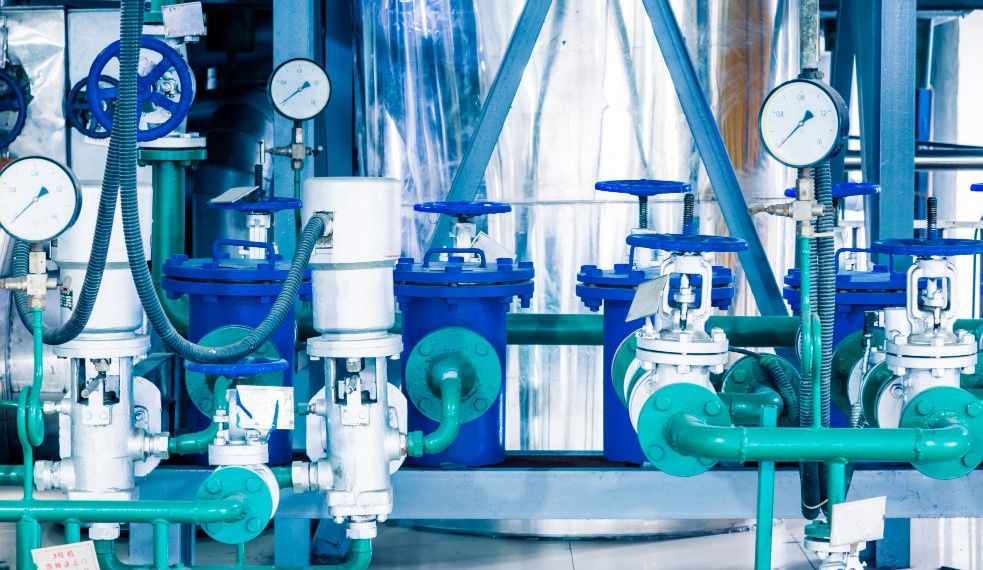
“Considering the chemical industry’s energy-intensive nature and its escalating demands, the role of motors and variable speed drives (VSD) becomes critical,” he writes. “Synchronous reluctance (SynRM) motors and drive packages eclipse the alternatives in achieving the highest levels of efficiency (IE5) currently attainable.”
Adding that such motors offer as much as, “40 per cent lower energy losses compared to commonly used IE3 motors, helping businesses save energy and boost productivity.”
Evidence of these savings can be seen in the example of the world’s largest nitrogen-based complex fertiliser producer which replaced thousands of its old, energy-inefficient motors for newer design SynRM motors. This change resulted in an annual electricity reduction of 40 GWh and a CO2 emissions reduction of 19 kilotons (equivalent to the emissions produced by nearly 14,000 standard cars).
Naturally, the latest motors and chemical pumps are all designed and built with safety as a key priority, especially in environments where explosive gas, vapour or dust may be present.
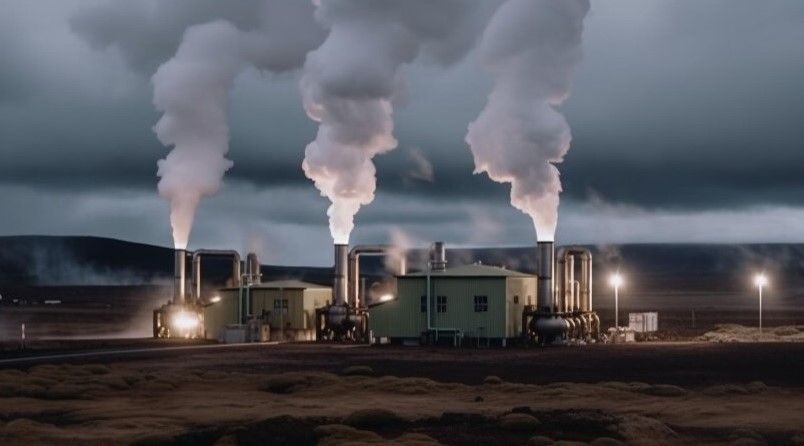
To stop the worst effects of climate change, significant adjustments must be made to how energy is supplied and consumed across the chemical industry. As an energy-intensive sector, even small changes and investments can return sizeable benefits.
Fortunately, there is a wide array of commercially viable solutions, such as high efficiency motors and VSDs, which can aid the adoption of energy efficiency measures. Doing so may enable the chemical industry to achieve Net Zero while also reducing net costs.
Photo credit:Fanjianhua, Sylvain Acher from Pixabay, Fanjianhua on Freepik, Vecstock, & Vecstock