The security of raw materials is a critical concern for nations as it underpins the viability and resilience of key industries like manufacturing and defence. Without a stable, reliable supply of essential industrial feedstocks, these vital sectors could grind to a halt, wreaking havoc on the wider economy.
Whether due to geopolitical conflicts, natural disasters, trade disputes, or other factors, supply chain disruptions can cripple production capabilities, undermine national security, and leave countries vulnerable to external shocks. A situation which has never been more apparent than today.
Following two decades of material sourcing based on principals of globalisation and ‘Just in Time’ deliveries, the COVID pandemic, the Evergreen Suez blockage, and the Ukraine/Russia war, manufacturers and national governments are now looking at ways to ensure supply chain resilience and dependability over simply buying from the cheapest source.
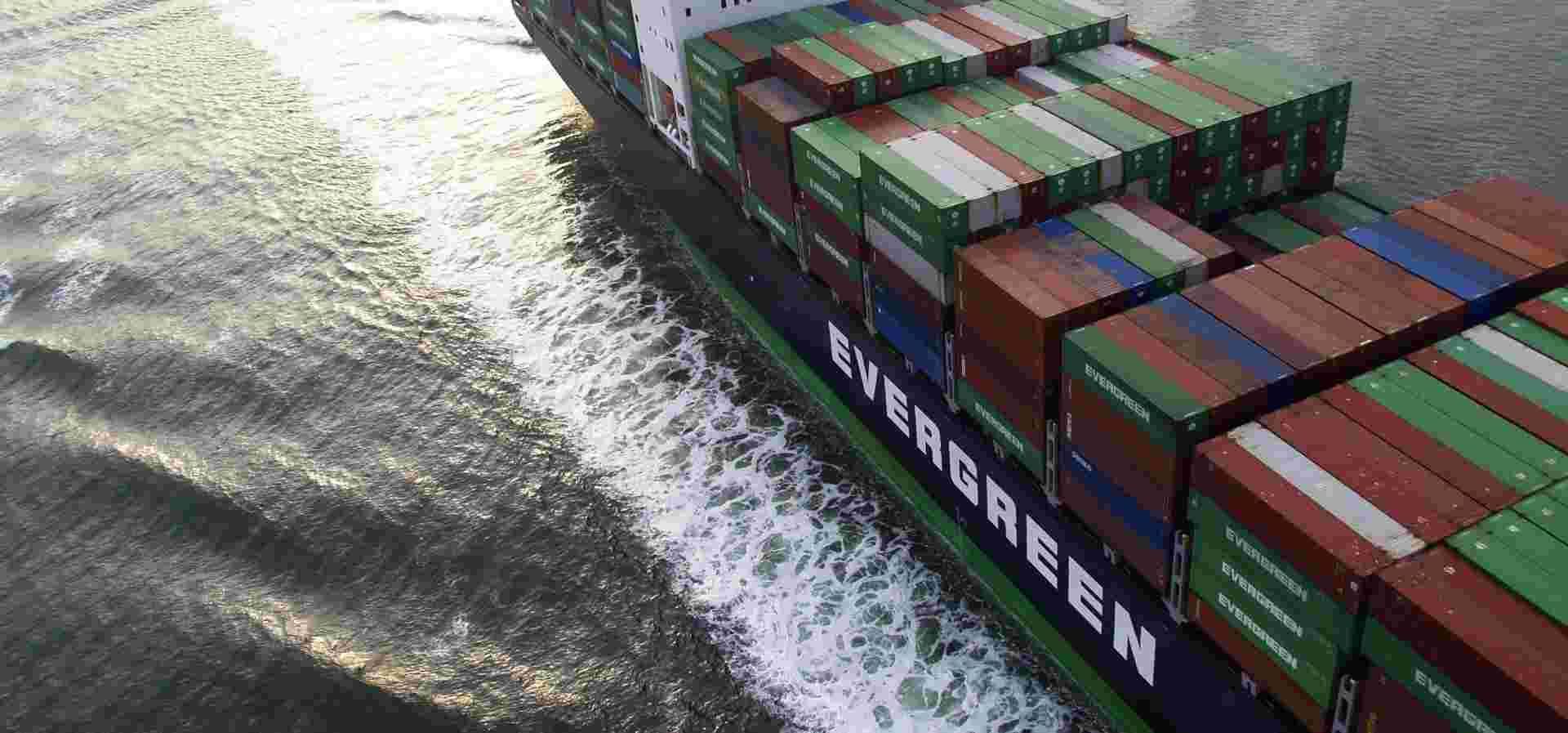
However, environmentalists, who have long been viewed as opponents to manufacturing success and expansion are now offering circularity and recycling as beneficial not only to nature but to chemical companies, national security, and wider economic health.
As Iain Gulland, the chief executive of Zero Waste Scotland, says, “we need to make better use of the materials already circulating within the economy.”
He even reports on the data of where raw materials are leaking from British economy, stating how in 2023, the UK exported an incredible 37,100 metric tonnes of electrical and electronic waste, containing a sizable amount of vital raw materials.
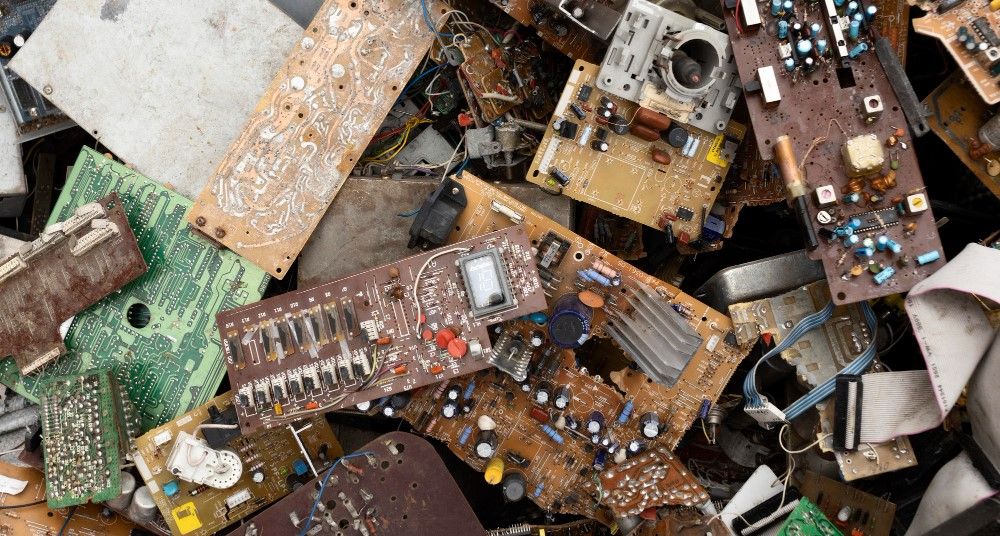
Yet he believes that it doesn’t have to be this way.
“Establishing circular value chains for these materials and the technologies they are embedded within can help to increase domestic economic activity and create jobs, while simultaneously reducing our vulnerability to supply chain risks,” explains Gulland. Adding that, “Research from the Coalition for Wind Industry Circularity has shown that remanufacturing just ten components for wind turbines using well established supply chains could create a UK market worth £9.6 billion, with more than 20,000 full time equivalent jobs created by 2035 and over 800,000 tonnes of avoided material to scrap.”
While such an elevated level of recycling may sound over complicated and expensive, in many ways securing these resources for reuse is not only better for the planet, but also a form of national security.
With the war in Ukraine now proceeding with an attritional phase, it is clear how both sides are attempting to use economic advantages to gain victory. The West’s sanctions on Russian trade limits their access to hard currency and restricts imports of high-end manufactured goods, such as electronic components and military hardware. In response, Moscow hopes to limit European growth through raw material supply delays and grain export blockades.
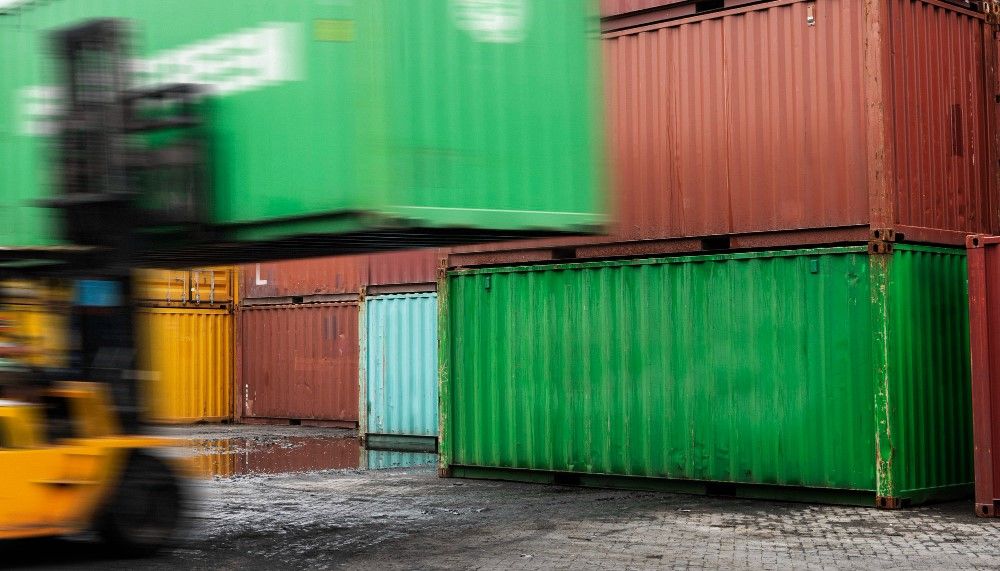
More than just raw material sourcing, supply chains have become a new battlefront. A warzone that while not active at present could involve large parts of the manufacturing sector and chemical industry without warning.
“We may no longer be subject to price hikes and supply shocks for oil and gas,” notes Gulland, “but instead find ourselves competing for access to critical raw materials.”
When the geopolitics has calmed down, when the supply chain delays are all smoothed out, when the Suez Canal is freely open from rebel Houthi attacks, then manufacturers will still need stable access to industrial feedstocks.
Be it through more localised feedstock sourcing or an increase in recycling, procurement departments and company purchasers need to have a hard think about the long-term strategy and safety of their raw material suppliers.
Photo credit: Auto.goodfon, Rawpixel, Freepik, & Freepik