Following years with insufficient raw materials, a lack of cheap energy, and not enough logistical options, the chemical industry is now facing a new shortage – skilled labour.
As an intensive, production sector, the chemical industry is heavily reliant on a highly skilled and knowledgeable workforce to maintain its complex operations and drive innovation. However chemical companies are currently facing a significant challenge as younger generations increasingly seek careers in other fields, leaving an aging labour force that will be difficult to replace even with advances in technology.
As experienced workers near retirement, the industry must grapple with the loss of decades of accumulated expertise and institutional knowledge. This looming skills gap threatens to disrupt chemical production, research and development, and the ability to adapt to evolving market demands.
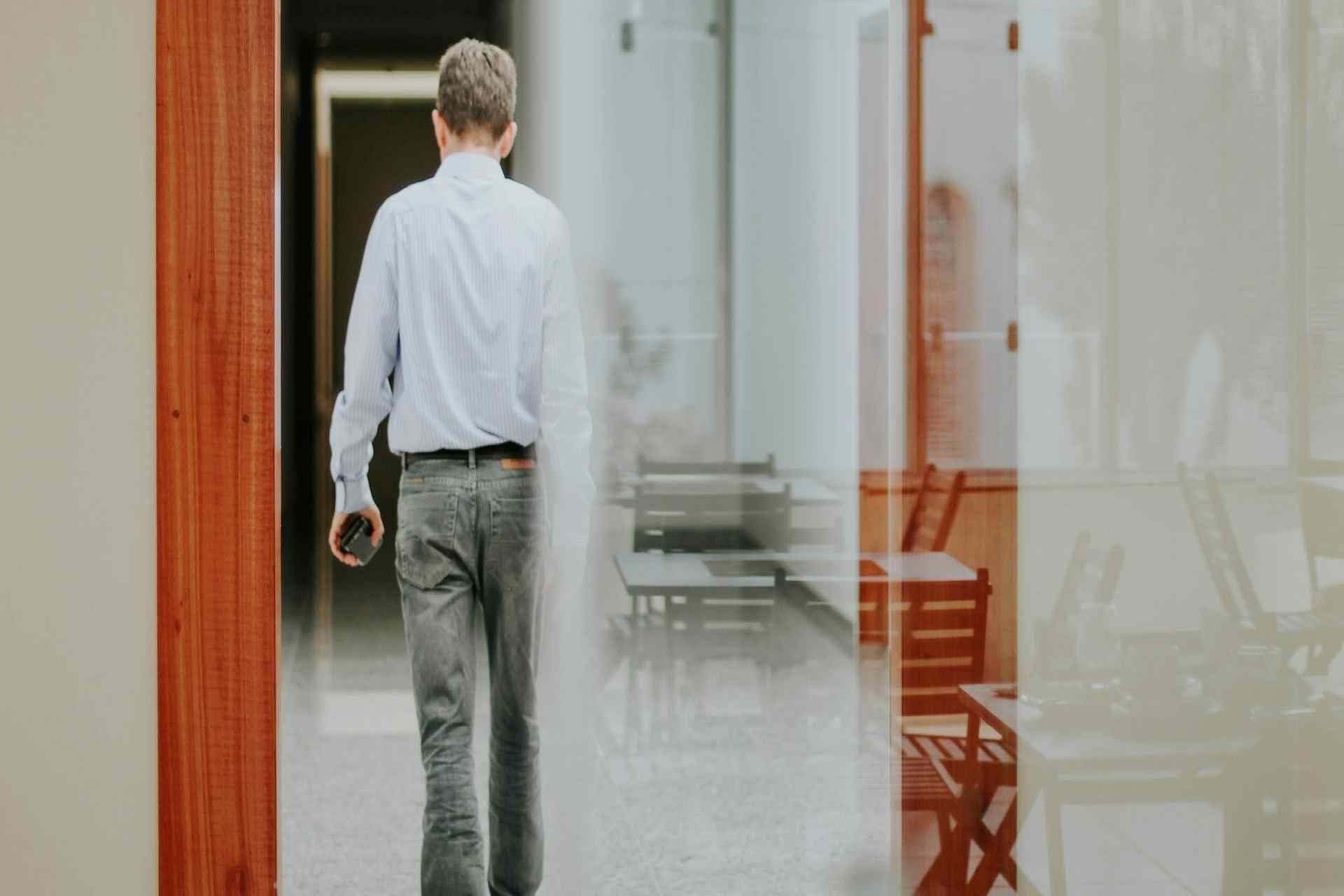
The issue was highlighted with the publication of a study by Accenture which analysed how labour productivity (calculated as revenue per full-time equivalent or FTE) has stagnated over recent years. According to the research, FTE has increased by less than 1% per annum during each of the last fifteen years, and while this figure has been slightly higher in Europe (1.6% annually), it is still lagging behind the 2.4% average annual inflation rate.
Specifically, the report states how the issue will develop in two phases. “First, chemical companies will be swept by waves of retirement, as around 30% of employees in the industry are 50 years of age or more and due to retire within the next decade or so.
“Second, there are shortages at the other end of the talent supply chain, as student enrollment declines in key disciplines for the chemical industry such as engineering and business. For example, looking at historically important talent pools for the chemical industry, between 2013-2022, engineering degrees awarded dropped 12% in the US and engineering enrollment dropped 37% in India. The decrease means chemical companies will face challenges recruiting the skills they need and replenishing the retiring workforce.”
The issue is particularly prevalent in the German chemical industry, where 38% of the labour force is over fifty.
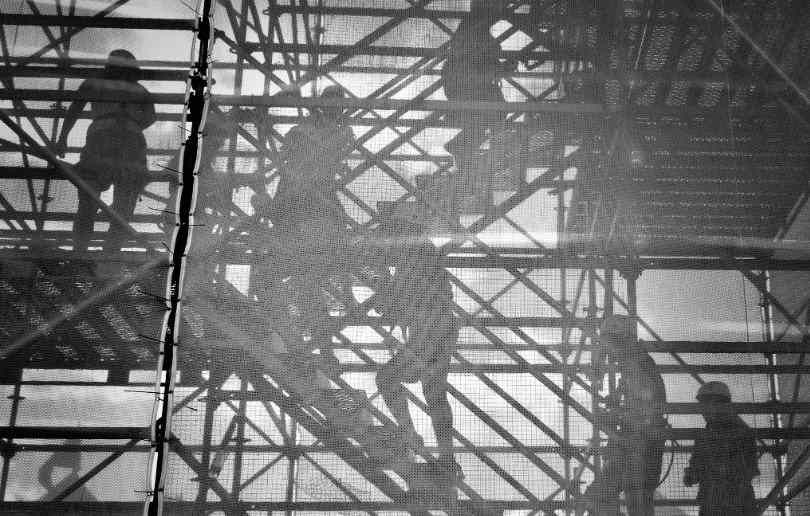
Bernd Elser, Senior Managing Director, Global Chemicals & Natural Resources Lead at Accenture, is quick to highlight how much of the problem lies in how the chemical industry has invested heavily in technology at the cost of training new workers.
For a long time, the corporate thinking was that Big Data, AI adoption, and automation were key to driving efficiencies and creating facilities which can make more chemical product for less money. Now it seems that there may be no skilled workers to operate the machines. As Elser states, “Technology alone does not automatically lead to greater labor productivity.”
Other articles on this topic: The Chemical Industry 20, 40, 60 Years from Now and Germany’s Chemical Industry Woes Continue
Improving worker productivity is a constant goal for chemical companies, as increasing the output and efficiency of their employees can significantly boost profitability and competitiveness.
Looking ahead to address this workforce crisis will require the chemical industry to actively attract, train, and retain a new generation of talented individuals who possess the specialized technical skills, problem-solving abilities, and hands-on experience needed to sustain and grow this vital sector of the economy.
Failure to do so could jeopardize the industry's competitiveness and long-term viability in the face of a complex and dynamic global landscape.
Photo credit: John Salvino, Jornada Produtora, & Viktor Kiryanov on Unsplash