At present only 9% of the 450 million tons of global plastic waste created each year is recycled. Most of it is burnt or buried, or worse still, ends up in oceans and waterways.
A major part of the problem is the inefficiency of current plastic recycling—most of which is done mechanically. However, over time the polymer chains from mechanically recycled plastic degrade and lose their value and usefulness.
Chemical recycling is more efficient in returning the raw materials back to their monomer forms, but the processes are specific for each individual plastic type. What is needed is a universal process which can recycle all manner of plastic waste in a way that adds value to the polymers.
Fortunately, a team of chemical researchers from Oak Ridge National Laboratory (ORNL) have now found a way to generate new macromolecules with more valuable properties than those of the starting material by way of molecular editing.
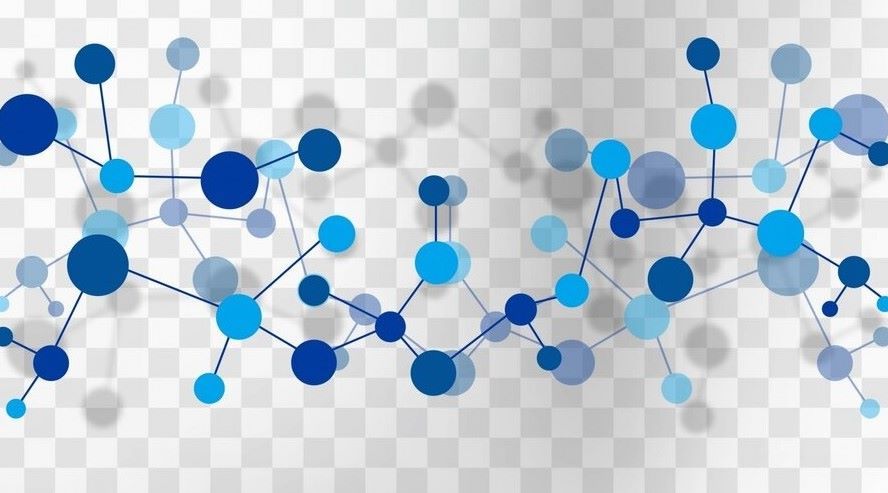
Two Nobel Prizes in Chemistry have already been awarded for molecular editing because of its immense promise. The first was won in 2005 by the creators of the metathesis reaction, which creates and breaks double bonds between carbon atoms in rings and chains. This process allows the subunits of these rings and chains to swap, creating new molecules in any form desired. The second was won in 2020 by the creators of CRISPR, the so-called ‘genetic scissors’ which can modify strands of DNA.
It is this ability to alter molecular chains which is the basis for this novel solution to plastic recycling.
“This is CRISPR for editing polymers,” explains Jeffrey Foster, who led the study at ORNL. “However, instead of editing strands of genes, we are editing polymer chains. This isn’t the typical plastic recycling ‘melt and hope for the best’ scenario.”
Related articles: The Many Routes to Oil-Free Plastic or The Polyurethane Problem of Mattress Recycling
Significantly, the polymer researchers focused on a variety of plastic waste to prove the versatility of the new recycling method: this included polybutadiene (a common industrial feedstock for car tyres) and acrylonitrile butadiene styrene (the stiff plastic used to manufacture computer keyboards, kids’ toys, kitchen appliances, and ventilation pipes).
“This is a waste stream that's really not recycled at all,” notes Foster. “We’re addressing a significant component of the waste stream with this technology. That’d make a pretty big impact just from conservation of mass and energy from materials that are now going into landfills.”
The process begins by dissolving the waste polymers by first mechanically shredding them before immersing them into the solvent dichloromethane for less than two hours at 40 degrees Celsius. A ruthenium catalyst (common in the plastics and biomass processing sectors) is then used to aid polymerization.
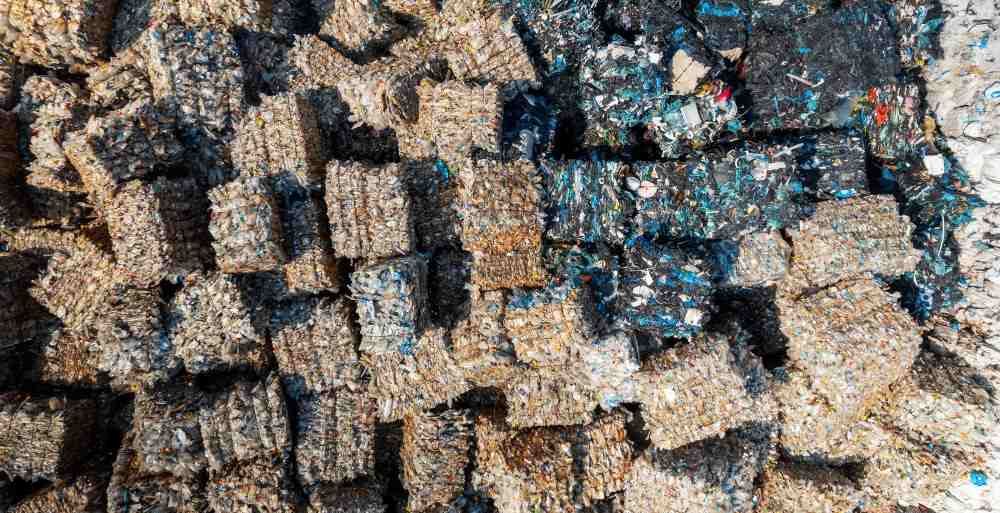
“The molecular building blocks of the polymer backbone contain functional groups, or clusters of atoms that serve as reactive sites for modification,” explains the industrial chemical journal Azom. “Notably, the double bonds between carbons increase the chances for chemical reactions that enable polymerization. A carbon ring opens at a double bond to create a polymer chain that grows as each functional polymer unit directly slips in, conserving the material. The plastic additive also helps control the molecular weight of the synthesized material and, in turn, its properties and performance.”
It is at this stage that the synthesis strategy can be adopted to modify the polymers into a new chemical product, creating a feedstock for a polymer which could be softer or more malleable than the original plastic. Alternatively, a harder or more durable thermoset may be required, so the process could be adapted accordingly.
The researchers then used two different chemical processes simultaneously to efficiently complete the recycling.
“One process,” the university explains, “called ring-opening metathesis polymerization, opens carbon rings and elongates them into chains. The other process, called cross metathesis, inserts chains of polymer subunits from one polymer chain into another.”
Because traditional recycling uses polymers that degrade with each melt and reuse, it is unable to recover the value in wasted plastics. However, as this new process can selectively modify the polymers, value can actually be added instead of lost.
“The new process has high atom economy,” notes Foster. “That means that we can pretty much recover all the material that we put in.”
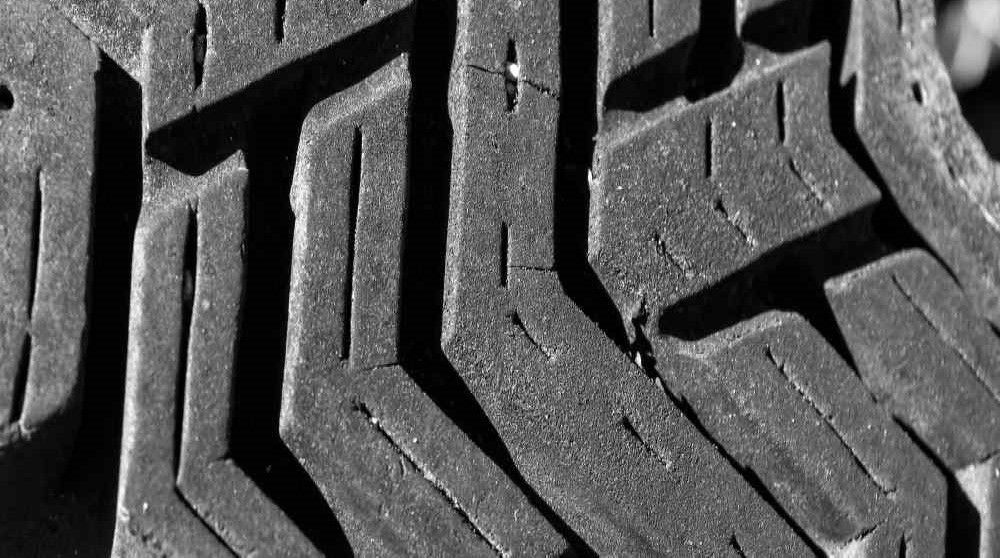
The team are now looking into ways in which the process can be upscaled to an industrial level, as well as studying what other polymer waste can be used. Possibly even high-performance thermoset materials, like polyurethane, silicone, epoxy resins, and vulcanized rubber.
“The vision,” explains Foster, “is that this concept could be extended to any polymer that has some sort of backbone functional group to react with.”
The development of this groundbreaking polymer editing technique represents a major leap forward in the quest to tackle plastic waste. By transforming discarded plastics into high-value materials through a versatile and efficient chemical process, researchers at ORNL have opened the door to sustainable and economically viable recycling solutions. Unlike conventional methods that degrade the quality of plastics with each cycle, this innovative approach not only preserves but potentially enhances the material's value.
This ultimately opens up the prospect of a future where plastic waste becomes a valuable resource rather than an expensive, ecological burden.
Photo credit: Freepik, Frimufilms, Wirestock, & Freepik