Plastic is fantastic. It is versatile, strong, flexible, and widely used to manufacture everything from windows to packaging, and from furniture to clothing.
However, it is also one of humankind’s greatest challenges – plastic waste.
Each year, as much as 14 million tonnes of plastic waste enters the ocean and waterways, and a further 230 million tonnes end up in landfill. Resulting in nano-plastic particles being prevalent in almost every living organism on the planet.
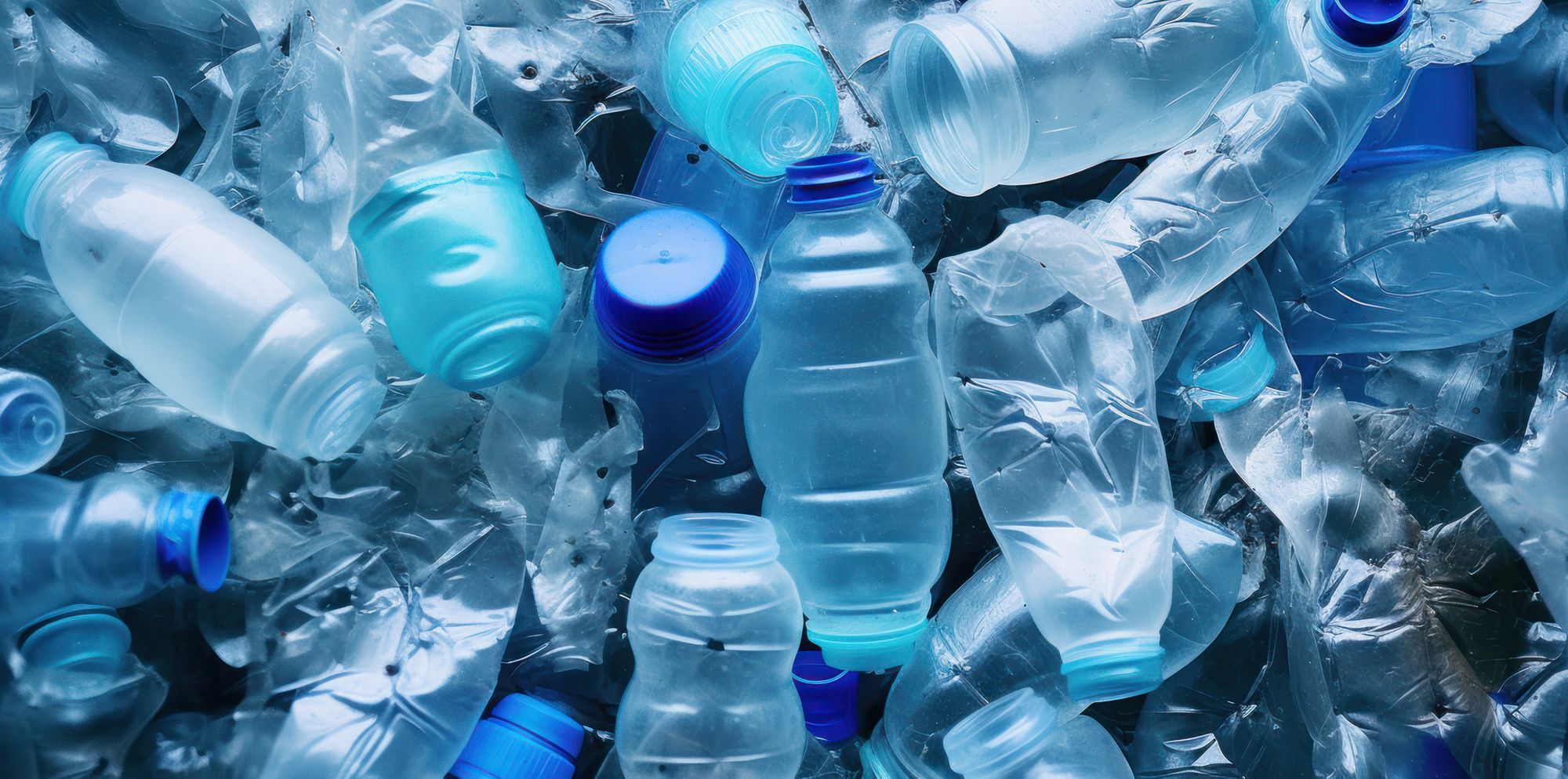
Knowing this has made the issue of sustainability a central pillar of the reform needed in the plastics industry. It is an issue which is being led by the market, with sustainability becoming a major factor for consumers who frequently make buying decisions based on avoiding plastic waste. A 2023 McKinsey study finding that, “consumers are willing to pay more for sustainable products.”
At the same time, investors are also keen to put their money into projects that encourage the circular economy even if it means a reduced return on investment. With a recent survey by industry consultant at EY stating that, “78% of investors were willing to take a hit on profits to support more sustainable products.” Adding that, “55% of business leaders were willing to sacrifice some profitability to [achieve sustainability].”
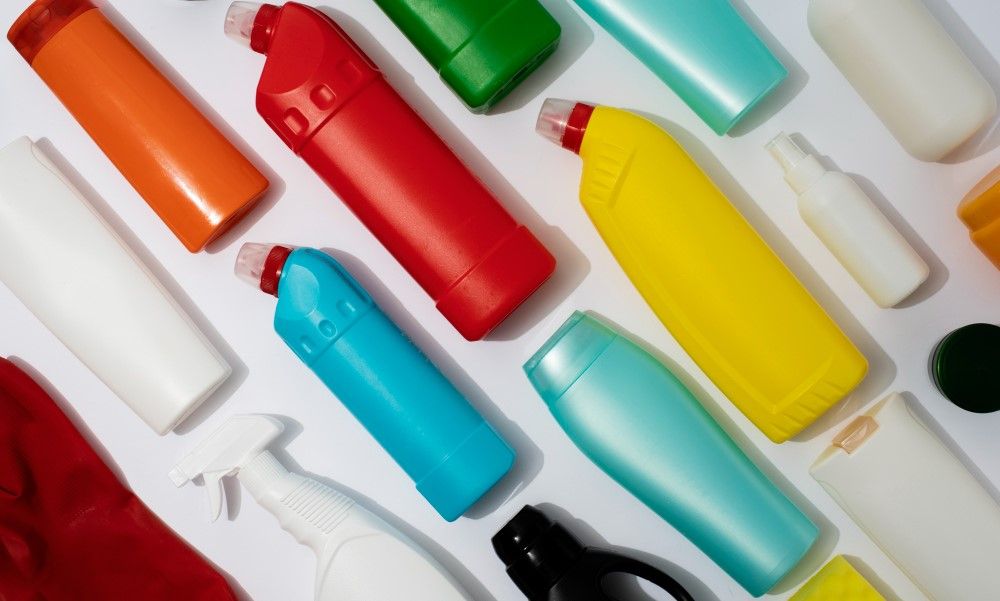
It is a situation which begs the question: Why doesn’t the plastics industry make the leap that investors and consumers say they want?
To answer this, the Engineering Research Visioning Alliance (ERVA), a think tank funded by the US National Science Foundation (NSF), set up a brain-storming exercise attended by 55 scientists, business leaders, legislators, and financiers to find novel, innovative, and ‘less-explored lines of research’ that could help transform the plastics industry into a more sustainable model.
Specifically, the future of sustainable materials was discussed on three different industry verticals, namely:
· raw materials in the construction sector
· single-use consumer goods
· chemicals
“Our concentration was looking 20-plus years down the road and how we get there,” explained Prof. Yael Vodovotz, who participated in the round table talks. “What are some of the issues and what resources do we need to get there?”
While these topics were analysed in some depth, the overall take away from such thinking covered the following key points:
1. Engineering Research with a Sustainable Goal
The panel agreed that multidisciplinary engineering is required throughout the design, scale-up, manufacturing, and end-of-use phases of sustainable materials.
“Our focus is to find the most transformative engineering research needed to create a very sustainable material environment,” explains Vodovotz. “Very different materials are involved, which is why we had so many subject matter experts.”
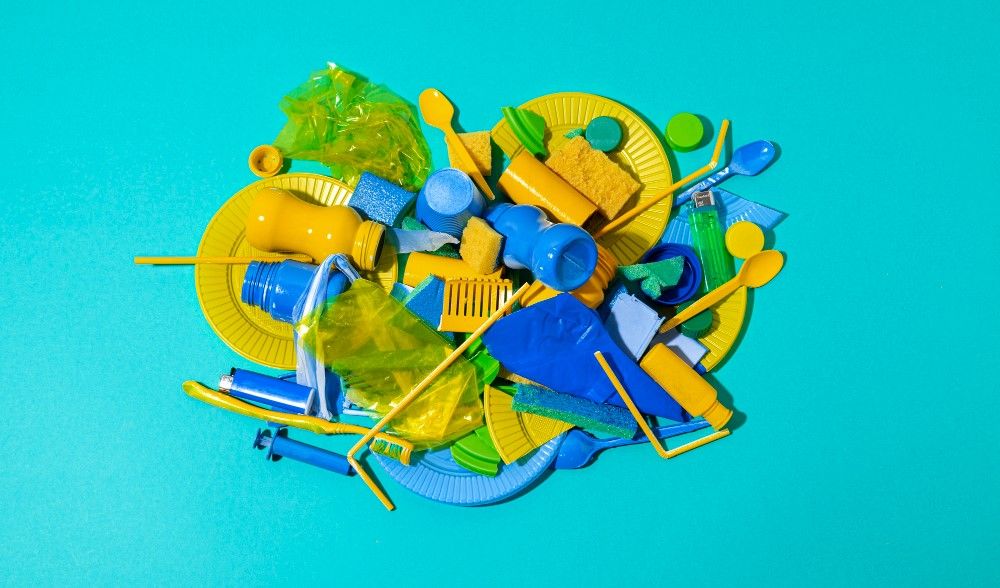
2. Business and Academic Cooperation
Business leaders need to work more closely with the scientific community to develop organic or regenerative biological processes and materials for polymer products.
This study needs to include process and performance research to make bio-based materials that satisfy product requirements and offer a viable alternative to petroleum-based feedstocks. Research areas such as the engineering of microorganisms or the use of natural enzymes were seen as most likely to succeed, either to help sustain a longer life span for a material or to cost-effectively break down materials when their useful lives are coming to an end.
3. The Application of AI in Raw Material Design
Artificial intelligence and machine learning are excellent, yet currently underused, tools in the research for novel industrial ingredients. Through computer modelling and simulations the discovery of new sustainable materials can be speeded up.
This should include all stages of material development encompassing atomistic-to-continuum structure property analysis, with simulations that accurately model any new materials' properties, processability, and performance.
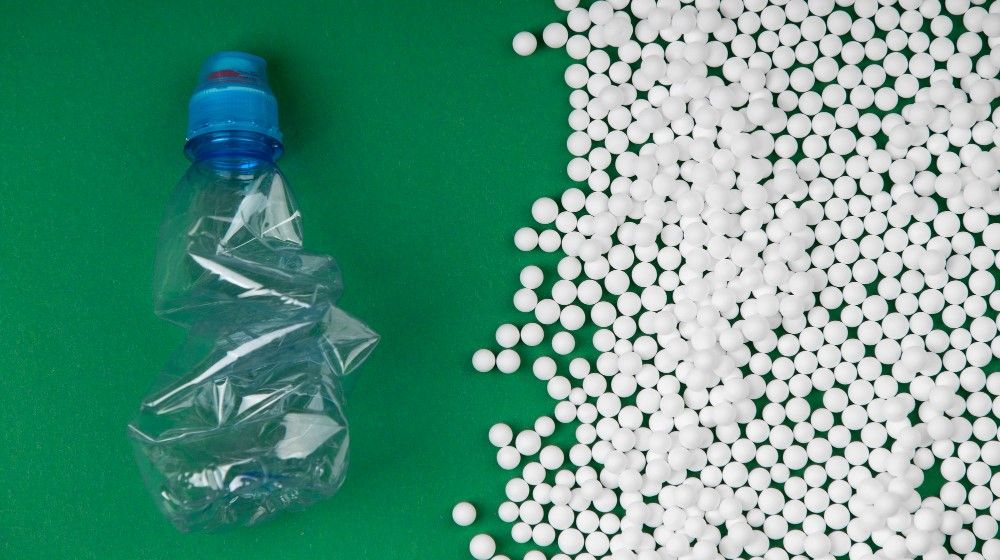
“There are many different parts of the design paradigm that need to be addressed when we are looking at sustainability,” notes Vodovotz. “Predictive models are helpful to the designer. AI is critical to minimize the number of experiments and speed up the process and look at a number of potential solutions.”
4. Facility Design
The brainstorming also highlighted the need to rethink the way production facilities are designed, believing that more focus should be given to new reactors and reactor configurations, such as large-scale low-temperature conversions and novel feedstocks.
“If we are looking at more sustainable feedstocks, they might be waste-derived or [something] that is not currently being used, and maybe getting away from the petroleum-based products,” says Vodovotz. “We might be able to develop and use some hybrid biological and chemical catalysts.”

5. Redirecting Investment
All too often, investment funds are spent on tried-and-tested chemical projects and polymer manufacturing processes. Enterprises that source sustainable feedstocks, such as organic raw materials, are frequently seen only as side-projects or prototype models. Bold investment is needed to construct (or reconstruct) production facilities which can produce sustainable, organic, or compostable feedstocks at scale.
6. Recycling
Everyone on the panel agreed that recycling rates need to improve, but were undecided on the exact route to take.
“Do we make sure that the mono materials have the same performance properties, and/or look at ways to take all that material apart?” asked Vodovotz. “Perhaps something that triggers the end of life and allows it to degrade. Mono materials can be recycled much easier, but they also can be composted in the right conditions. Can we move packaging and other materials into the composting arena?”
Alongside the materials being recycled, the discussion also examined ways that end-of-life recycling processes could be more cost-effective.
“Automated sorting technologies are something that help us sort for very specific plastics, but we need to sort for more,” observed Vodovotz. “There is quite a bit that ends up in landfills despite the sorting, so we need to work on these technologies.”
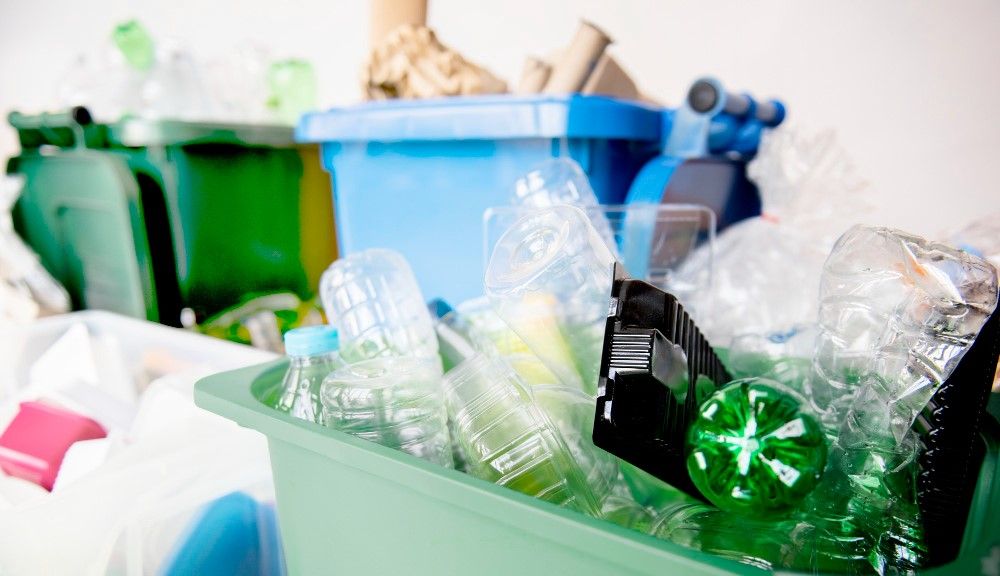
While much of the discussion may read like a long wish list, the participants were keen to keep suggestions realistic and something which investors and polymer manufacturers would find practical.
“We want to make sure that the findings here are actionable and valuable to the stakeholders in the community, so they pick them up and put resources into them,” explains Rebecca Silveston, executive director of Engineering Research Visioning Alliance (ERVA).
However helpful these suggestions are to polymer manufacturers it is clear that something needs to be done to resolve the current economy’s dependence on fossil fuel-based plastics that are not recycled - and that requires a major rethink.
As Vodovotz concludes, “We need to design for sustainability from cradle to grave. This is very, very critical.”
Read more on this topic: Playmobil Toys Act on New Plant-Based Industrial Feedstock or Is this the Year of the Bioplastic?
Photo credit: Nuraghies on Freepik, Freepik, Freepik, Rawpixel, Freepik, Freepik, & Freepik