Japan is hoping to revive its stagnant economy with a recycling model that could change how raw materials are sourced.
Unable to compete with super-sized Chinese chemical facilities, the low-cost oil of the Middle East, or the shale gas fortunes of America, the Japanese are looking at ways to increase recycling efficiencies to the point of economic viability. A plan that means developing technologies and a business model where manufacturers will look to recyclers as a long-term, affordable, and reliable source of raw materials. Here’s how they are moving forward with the strategy.
Microbe Recycling
Some of the most promising processes for chemical recycling use microbes to convert waste into basic chemical building blocks, such as ethanol.
“Our process uses microorganisms that exist in the stomachs of rabbits,” says Satoshi Koma, head of corporate new business development in Sekisui’s biorefinery group.
The process works by using combustible garbage such as food leftovers and plastic film which is gasified into carbon monoxide and hydrogen and then purified using Sekisui’s patented technology. The microorganisms then consume the gases and excrete ethanol as waste.
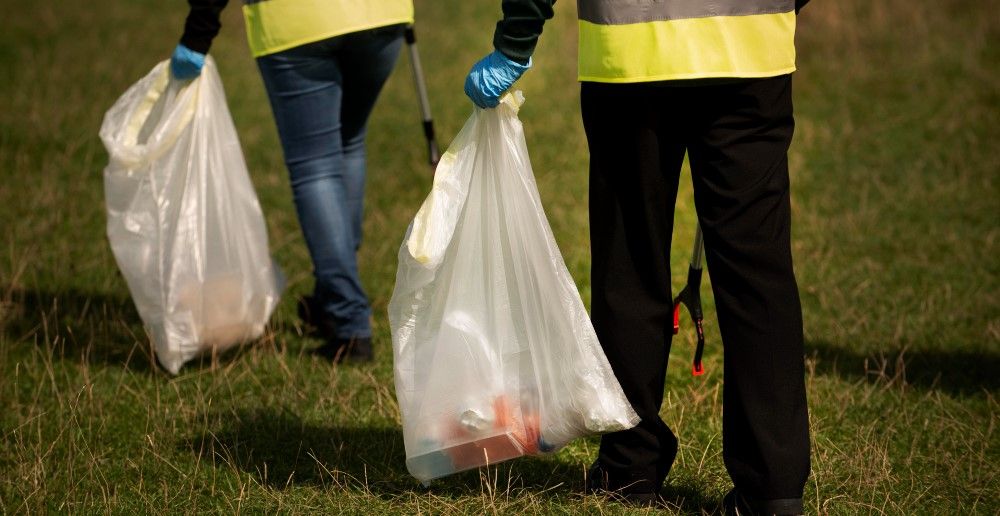
After being extracted to a purity of 99% or above, the ethanol is recovered as a roughly 5% solution and used as a chemical raw material.
“Currently, the biggest challenge in the demonstration test is to stably produce 1,000 to 2,000 L of ethanol from 20 metric tons of combustible waste per day,” says Koma. The other issue is matching the dietary needs of the microbes with the waste produced, as each collection of household waste is slightly different in what it contains. “Meanwhile, the specifications of the microbial feed are fixed,” notes Koma.
Despite these issues, the maths strategy for Japan is simple: each year, the country creates combustible waste with an energy content of about 800 trillion kJ. The basic feedstock for many of Japan’s petrochemical facilities is naphtha. To meet Japan’s plastic feedstock needs, the chemical companies use 630 trillion kJ of naphtha.
“It is mathematically possible to produce domestically all the plastic materials from combustible waste,” says Koma.
For this reason, Sekisui is investing heavily in technology to convert household waste into raw materials for the chemical industry. Armed with a $100 million Green Innovation Fund grant from the Japanese government, the company plans to start building a recycling facility in 2026.
In fact, the chemical process owners are so confident in their plan they have already signed an agreement to sell the ethanol it will produce to Sumitomo Chemical to make ethylene and propylene.
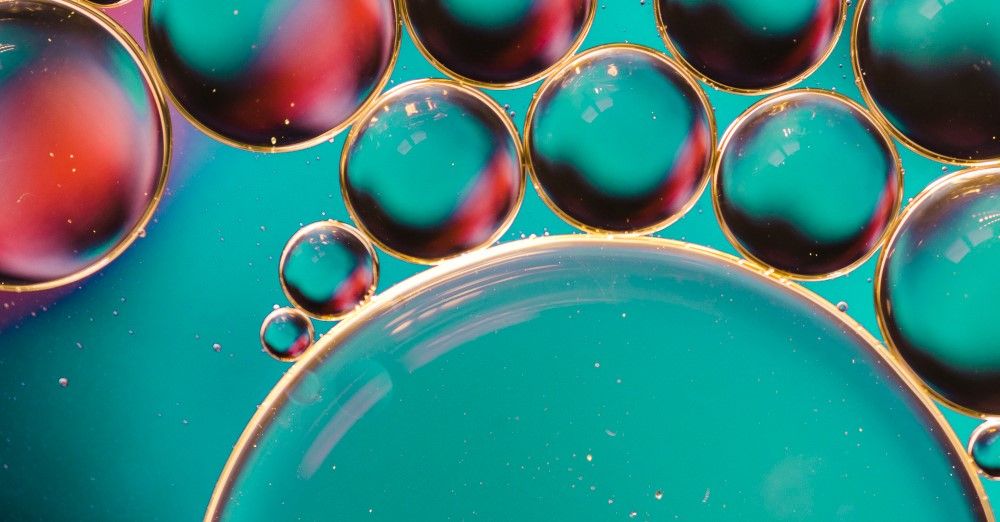
Another chemical company at the forefront of making recycling technology into an economic model is Resonac Holdings, who for the last 20 years have been running a recycling plant that turns waste plastics into hydrogen in Kawasaki, Japan,
“We found raw materials for producing hydrogen, the raw material for ammonia, in used plastic waste,” says Hiroshi Ito, the company’s general manager.
The hydrogen that is produced is then utilised as a starting point for fertilisers that contain nitrogen, acrylonitrile, or ammonia.
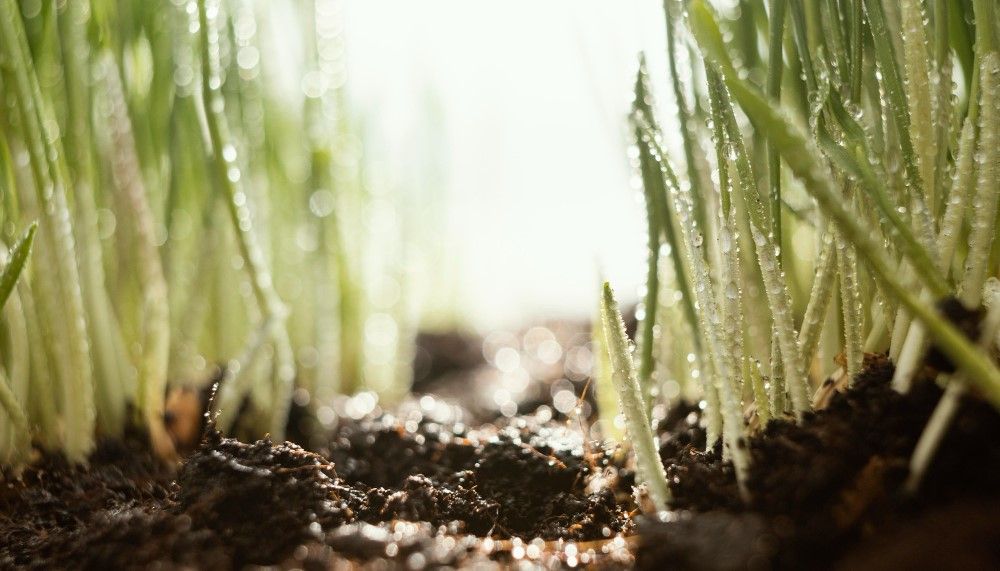
Aided by strict recycling laws and a law-abiding public which is happy to separate waste, the company has been successfully making a profit from household plastic waste with a simple chemical method.
The process starts with a pretreatment of plastics followed by a two-step gasification process to obtain hydrogen and carbon dioxide. Both processes are partial oxidation reactions that are powered by internal heat production as opposed to external heat sources. Any slag that remains is sold for use in road construction.
“The plant is unique,” says Ito, “it has no chimney.”
While both companies are expanding their production capacity, Japan still has some way to go before its plastic production sector is circular.
“The country generated 8.2 million t of plastic waste in fiscal 2022, split about equally between consumer and industrial waste,” notes a CE&N report on the topic using data supplied by Japan’s Plastic Waste Management Institute. “The country recycled an impressive 87% of its plastic waste, but more than two-thirds of this was incinerated. Only 280,000 t was recycled by chemical means such as those used by Resonac.”
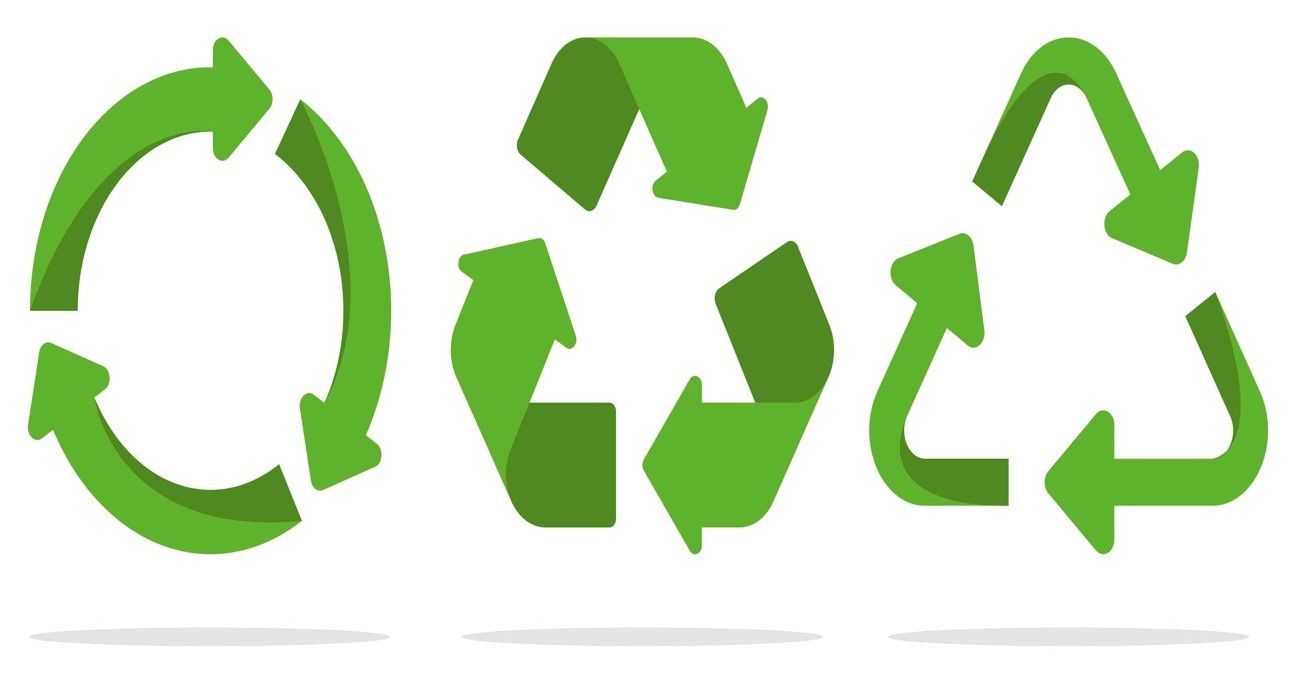
However far the country has yet to travel, the progress being made is promising and a sign of what can be achieved.
“If the recycling business is linked to oil refining and petrochemistry,” says Toshiaki Yoshioka, a professor in Tohoku University’s Graduate School of Environmental Studies, “the recycled products themselves will be directly linked to the circulation of basic chemicals and chemical raw materials and products.”
Japan is a land of few natural resources - it has almost no oil or gas, and very little coal. As such it provides a glimpse into Europe’s not-too-distant future. As like Japan, Europe may well have consumed all of its oil and gas, while its coal reserves will be deep underground and uneconomical to mine.
Given these similarities, maybe it’s time Europe took note of the progress being made in Japan and learnt about the business model and processes for the efficient recycling of raw materials.
Photo credit: Freepik, Juicy_fish, Freepik, Freepik, & Freepik