Hydrogen peroxide is one of the most in-demand products in the chemical industry. It is used in industrial cleaners, disinfectants, stain removers, as a paper pulp whitener, in medicines, household cleaners, in the manufacture of polyurethanes, printed circuit boards, and even semiconductor production.
But while it is a practical and versatile chemical product, it also has many drawbacks. Firstly, the process to manufacture hydrogen peroxide is neither very safe, straight forward, or ecological, as it begins with a highly flammable and toxic solution that is mixed with hydrogen, then filtered, and combined with oxygen and water. This solution is then concentrated to extremely high levels before it is ready for sale.
However, transporting hydrogen peroxide is not a smooth journey either, as most of the chemical on the market is made in huge chemical facilities in Russia and China from where it must be shipped to consumers.
One of the biggest users of hydrogen peroxide is the oil and gas industry who use it to treat the billions of gallons of waste saltwater that fossil fuel extraction creates. As the wells are often inland, in places like Texas, Alaska, and Saudi Arabia, the hydrogen peroxide must be transferred to trucks or rail tankers, before it can be put to use.
The costs of such a laboured chemical supply chain combined with the energy intensive, potentially dangerous and toxic production methods have now reached a limit. The result is a start up chemical company with a business model and greener chemical process that is reinventing this part of the chemical industry.
Co-founded in 2016 by two former students from MIT, Solugen claims to be the world’s first and only producer of bio-based peroxide, and has a mission ‘to decarbonize the chemical industry.’
Based in Texas, the company makes hydrogen peroxide by combining genetically modified enzymes with organic compounds, such as plant sugars. The resulting bio-based hydrogen peroxide (as well as organic acid by-products) are safer, cheaper, and less toxic than the conventional production methods used in larger chemical plants.
At present, the chemical company has only two pilot facilities which together produce a little over 10 tons of hydrogen peroxide per day but has big plans for expansion duo to a chemical supply chain discovery. However, the story starts earlier than that.
In 2015, Solugen co-founder Gaurab Chakrabartiwas at medical school doing research on pancreatic cancer when he came across enzyme in cancer cells that could function in extremely high concentrations of hydrogen peroxide.
However, the enzyme needed another expensive chemical to be useful in reactions, so Chakrabarti started looking for help with developing the enzyme into a practical tool. Eventually he met Sean Hunt, the husband of his medical school colleague, who was working on his conventional chemical PhD at MIT.
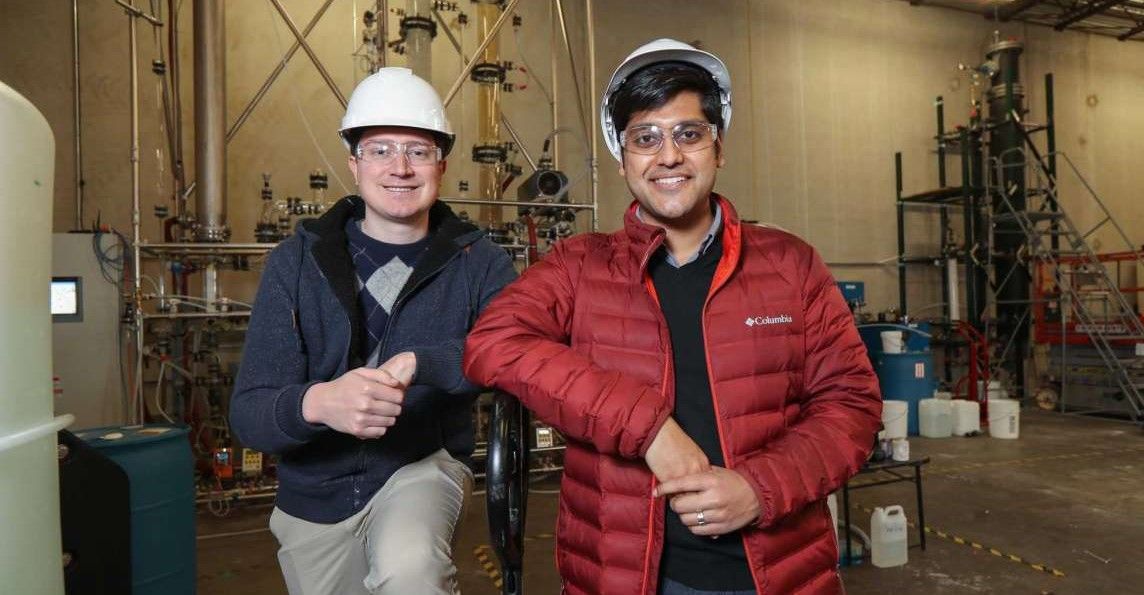
“My background is not in biotech, so I’m kind of the recovering biotech sceptic,” says Hunt. “I learned about enzymes in school, and everyone knew how active and selective they were, but they were just so unstable and hard to manufacture.”
Together, Hunt and Chakrabarti began working on computational protein designs until they were able to genetically modify the enzyme so that it produced hydrogen peroxide at room temperature when mixed with cheap organic compounds such as sugar.
The idea soon won them $10,000 as finalists in the 2016 MIT $100K pitch competition, however they were unsure as to whether to continue with the process as a commercial concern.
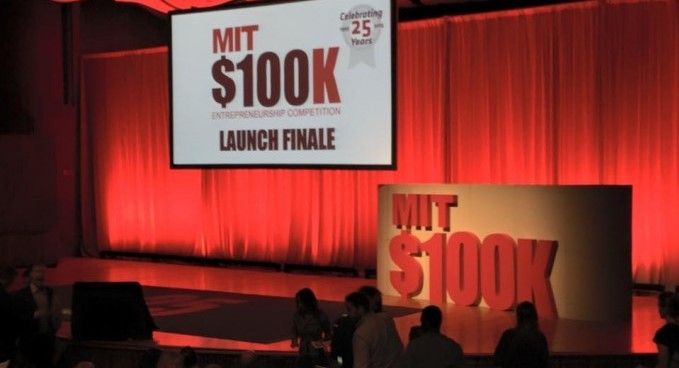
That was until a Facebook group of float spa enthusiasts read about their win. As the name suggest, float spas are baths filled with salty water where people float in the dark and in silence to help them relax by achieving sensory deprivation. Float spas need hydrogen peroxide to keep the specialised waters clean.
“There’s about 400 float spas in the U.S., and they’re all on one Facebook group, and one owner saw our MIT $100K pitch video and shared it to the Facebook group,” explains Hunt. “That’s really what made us continue Solugen that summer. Because we were contacted by these float spa owners saying, ‘This is how much we pay for peroxide. If you guys can make it, we’ll buy it.’”
It was this that convinced the pair to proceed with their chemical company start up. As the MIT press release describes, “The founders rented cheap lab space in Dallas and sent one of their early enzyme designs to a protein manufacturer in China. Then Hunt spent $7,000 at Home Depot to create a pilot reactor he describes as ‘this little PVC bubble column’.”
But the business soon ran into trouble. “Running out of money, the founders bought 55-gallon drums of sugar and ran them through the reactor with their enzyme, watching triumphantly as organic acids and hydrogen peroxide came out the other end. The founders began selling all the peroxide they could produce, sometimes sleeping on the floor to keep the reactor running through the night. By December of 2016, they were making $10,000 a month selling pails of peroxide to the float spa community.”
By the end of the summer of 2017, the company had progressed beyond a PVC bubble reactor by building a fully automated reactor, with a hydrogen peroxide production capacity 10 times greater than before.
It was at this point that the company began to consider the largest market for hydrogen peroxide in the world; the oil and gas industry. Hunt and Chakrabarti knew that the current supply chain for the chemical was long and expensive, they also knew that conventional production methods were energy intensive and dangerous, as well as leaving a large carbon footprint as the working solution needed constant venting.
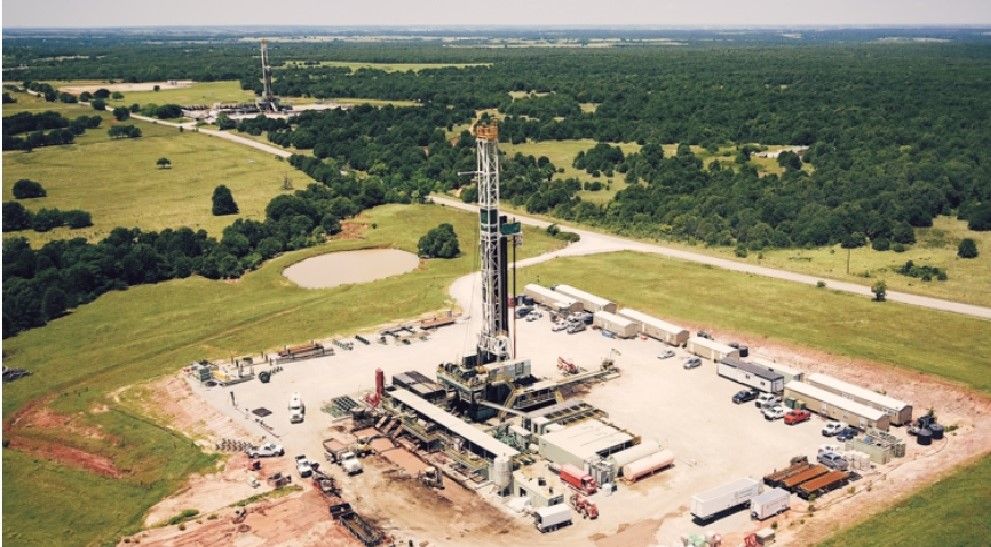
While originally Solugen had to concentrate the hydrogen peroxide for practical shipping to the float spas around America, the pair soon realized that as their chemical production process was safe, non-toxic, and bio-based, they could construct ‘mini-mills’ right next to the oil and gas plants. Without the need to make a concentrated chemical, the ‘mini-mills’ could produce already diluted hydrogen peroxide, thus further saving money.
Their new business model would not only under-cut the prices of the massive chemical plants in China and Russia, but also provide a greener supply chain and lower the carbon footprint.
“When we were building these things out, we realized that because we’re doing all this chemistry with enzymes where it’s room temperature, in water, and low pressure, it’s very safe, and as a result we can build these small plants,” says Hunt. “That’s really exciting for us. For instance, you can sell hydrogen peroxide for $2 a gallon [but] it costs $1.50 a gallon just to ship it to the customer. The freight is almost the price of the chemical. And in some instances, it’s more than the chemical itself.”
Furthermore, the chemical process the company has developed is itself based on the latest technology. As the scientific journal Phys.org outlines, “To make its proprietary enzymes, the company is leveraging fairly new methods for computational protein design and genetic engineering. It also relies on an industry of protein contract manufacturers that can produce large amounts of engineered enzymes for far cheaper than what would have been possible even five years ago.”
However, it is the ecological side of the business that really spurs Hunt on, as many wastewater cleaning processes use extremely toxic chemicals that don’t biodegrade like hydrogen peroxide does. “What I really love about this, is it’s a true environmental crisis that I think we’re making a big difference on,” he says.
The company is also looking at altering their recipe to co-produce different organic acids to meet chemical industry demand. For example, by changing the enzymes and compounds being mixed, Solugen is able to create acetic acid, a chemical that is used to make a wide variety of products, including plastics, polyester fibre, and even vinegar.
“Hydrogen peroxide and acetic acid are fundamental building blocks for our economy. We see Solugen as a platform [for other solutions],” Hunt says. “In the long term, that’s what really excites us.”
Now the company is looking at major expansion with a much larger site opening next summer. However, it is hoping to make an even bigger impact, especially if backing can be secured from one of the big oil companies.
Solugen may be just a small start up from Texas, but it runs on technology which has the potential to decarbonize the production of an extremely common chemical. It has a business created around a safe and non-toxic supply chain. And it provides a chemical used for a host of consumer and industrial applications at a lower price.
Maybe the guys from MIT are on to something big.
Photo credit: MIT, HoustonChronicle, Solugentech, Donstaniford, InnovationMIT, IHSMarkit, Essentialchemicalindustry, & Industrysoup.