Environmentalists have major problems with advanced chemical recycling. They see it as a greenwashing of the chemicals industry which is the third largest sector for pollution, producing 5% of global carbon emissions.
“The major problem with chemical recycling is that it absolves the plastic industry of responsibility,” notes a recent Earth Day report. “By offering this ‘perfect’ solution, companies can continue to produce just as much plastic as ever or even scale up their operations. It does not change the bigger picture, which is that plastic is created from our highly pollutive dependence on fossil fuels.”
But are efforts to make the plastic industry more sustainable really to be dismissed so easily?
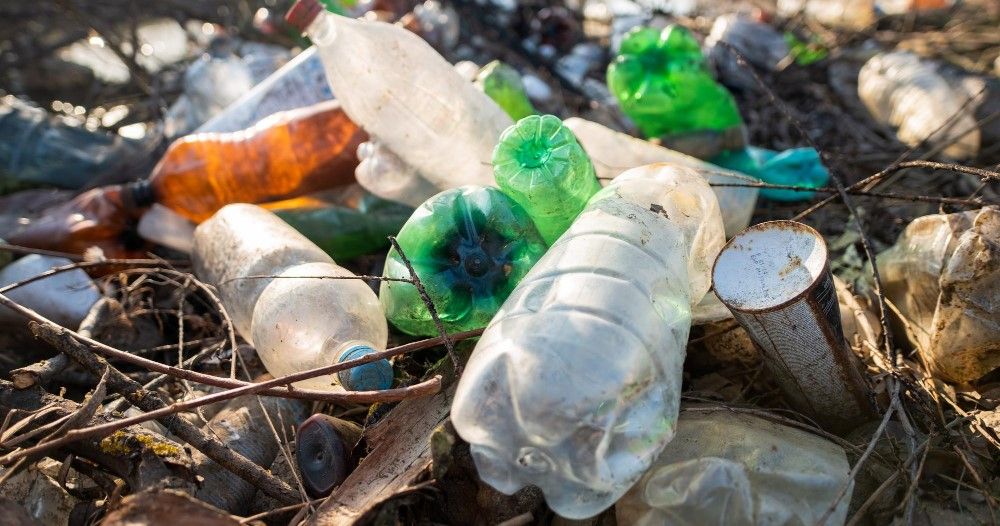
From a purely ecological standpoint, it would be beneficial to stop using any fossil fuels for transportation, heating, or as a feedstock. But the reality is that people depend on oil and gas for their everyday lives. For its part, the chemical industry is attempting to adapt to the reality of climate change by creating more circularity while still meeting demand for plastic products which is growing year on year.
As a recent analysis by the Nova-Institute reports, advanced recycling production capability is rocketing in the wider EU. From approximately 50,000 tonnes per year in 2018, rising to 100,000 in 2023, and is now set to hit almost 500,000 by 2027 – a ten-fold increase in less than ten years.
But what are the processes involved in chemical recycling? Are they sustainable? Are they profitable?
Let’s take a look.
Pyrolysis
Pyrolysis is a thermochemical process that uses heat in anaerobic conditions to transform mixed plastic waste (mostly polyolefins) and biomass into liquids, gases, and solids. The conversion process yields syngas, char, waxes, oils, diesel, naphtha, and monomers. A portion of these chemical products can even serve as raw materials for the synthesis of new polymers.
“[Pyrolysis] is a process which holds great potential because it can convert plastic waste into oil that can be used for furnaces, boilers, turbines, and diesel engines, thereby keeping plastics out of landfills while simultaneously reducing our reliance on extracting additional fossil fuels for plastic production,” notes Kate Bertrand Connolly, a journalist at Plastic News. “In addition to plastic and energy outputs, pyrolysis results in byproducts such as char, a carbon-rich material that can be sold off and used for cookstoves, road surfacing, and improving soil quality.”
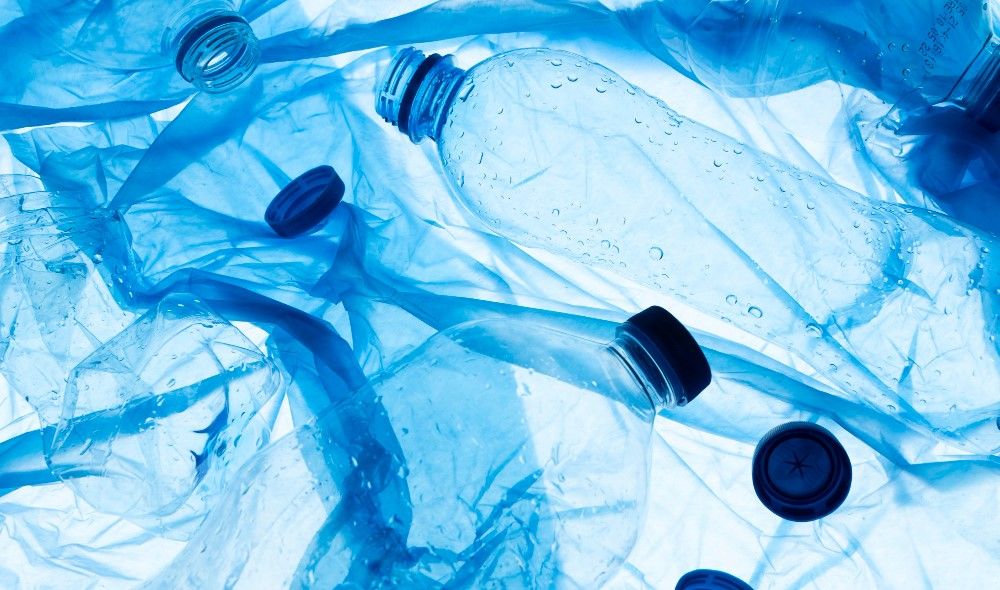
Dissolution
By using a solvent, the dissolution process removes specific polymers from mixed plastic waste while preserving the chemical structure of the polymer. In doing so, the additives, pigments, and fillers which are present in plastic, and which do not dissolve, can be isolated from the dissolved polymer. The target polymer is then precipitated from the clean solution using an anti-solvent. Unlike solvolysis, dissolution does not require a polymerization phase.
Solvolysis
Like dissolution, solvolysis is also a solvent-based process, using them to depolymerize polymers (mostly polyethylene terephthalate {PET}), into simpler polymer building blocks such as monomers, dimers, and oligomers. After being isolated from additives and other plastic constituents during depolymerization, the building blocks are cleaned and then repolymerized.
Gasification
Gasification is also a thermochemical process which can convert mixed plastic waste and biomass, in the presence of heat and oxygen, into syngas and carbon dioxide.
Enzymolysis
Enzymolysis is a biochemical process that depolymerizes polymers using biocatalysts. However, it is currently still under research in laboratories, and has yet to be conducted at scale.
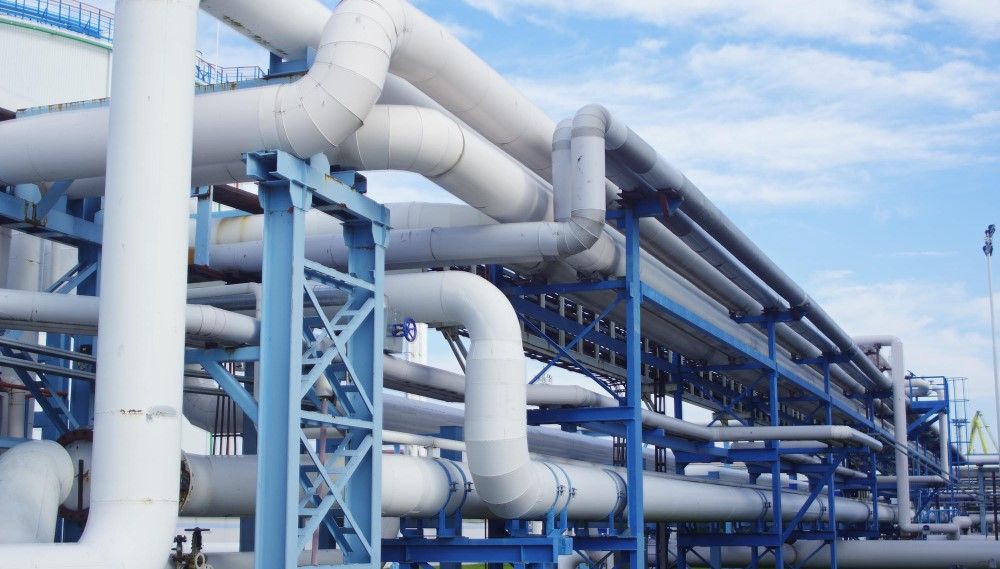
Profitability
The growth of chemical recycling points to the money to be made in this sector. “From start to finish,” notes Connolly’s report, “chemical recycling has the potential to be incredibly profitable.”
For example, a recent study by chemical industry consultants at McKinsey & Sons found that if plastics recycling was fully invested in, allowing for 50% of plastics worldwide to be reused or recycled by 2030 (a fourfold increase over today’s rates), then “… plastics reuse and recycling could generate profit-pool growth of as much as $60 billion for the petrochemicals and plastics sector.”
The problem is that the petrochemical industry can make more money from extracting oil from the ground and using that as a feedstock for plastics. It saves time and money on the complex issue of waste plastic collection and sorting, is not in competition with the mechanical recycling sector, and produces whichever grade or type of plastic is desired.
For the chemical recycling sector to meet its full potential, a marked change from virgin feedstock to recycled is required.
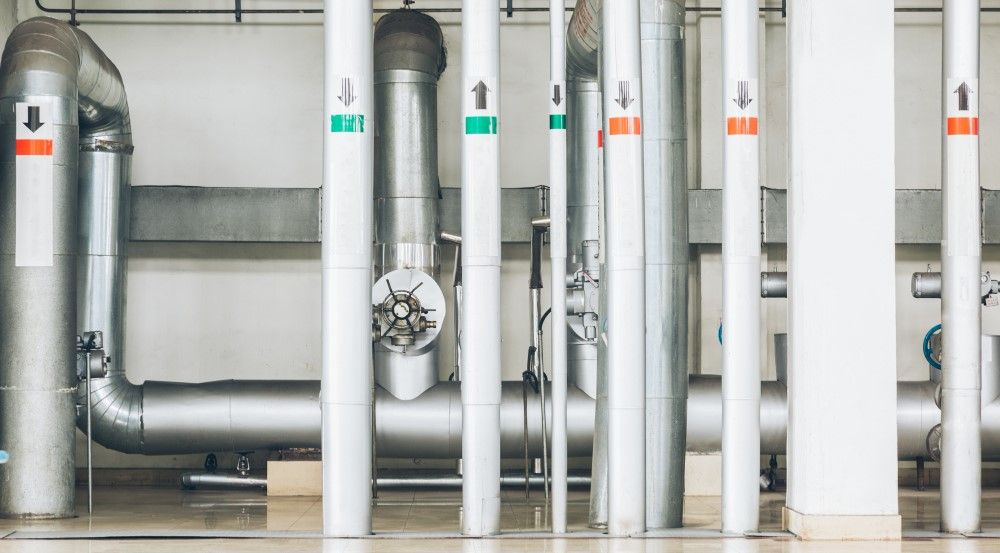
Sustainability
Environmentalists argue that the consequences of chemical recycling are too high for the sustainability benefits. They highlight the waste products (toxic gases and char) generated by processes such as pyrolysis, all of which are heavily polluted due to the chemical additives utilised in the recycling process. Some of the compounds used in chemical recycling that are known to be harmful to human health include benzoene, lead, cadmium, and chromium. While most are treated and disposed of responsibly, some of this waste contaminates local air and water. In addition to this, the collected plastic waste which cannot be recycled is merely burnt or put into landfill.
Furthermore, whatever recycling process is used requires a significant amount of energy, producing more greenhouse gas emissions and somewhat negating the benefits from recycling.
Even supporters of chemical recycling note that considerable infrastructure investment is needed to improve waste plastic collection and sorting to further upscale the current rate of recycling. Sourcing the correct type and quality of plastic waste is already a challenge in some areas, so governments will need to promote and invest heavily in any expansion of the chemical recycling sector. But could this investment be better spent elsewhere?
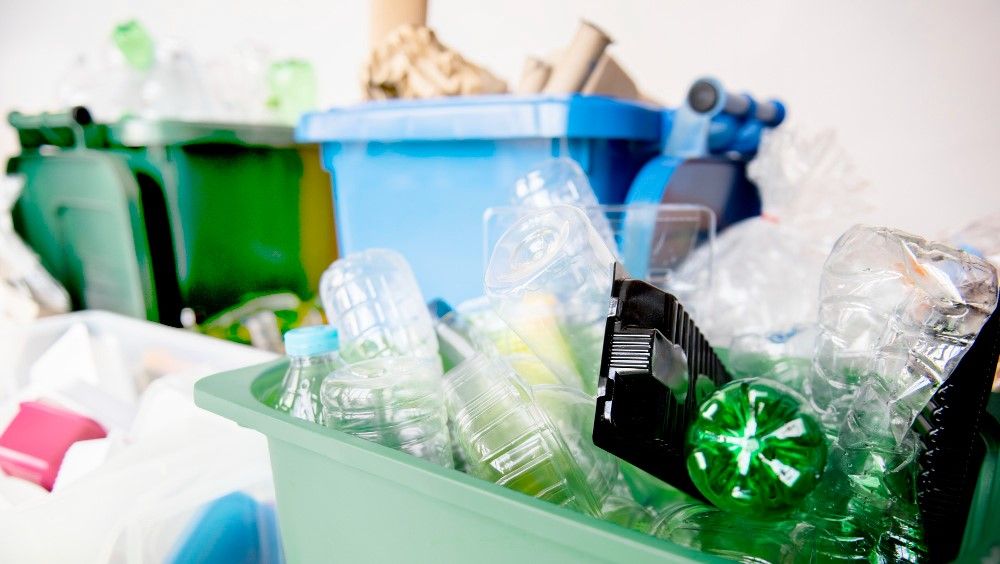
That said, plastic pollution is a major issue of our times which advanced chemical recycling can help address more efficiently than mechanical recycling methods which have limitations in terms of the types of plastics that can be recycled and the quality of the recycled material. Advanced chemical recycling can potentially overcome these restrictions by breaking down plastics into their basic components to be used to create high-quality recycled materials in a closed-loop model.
While this technology has the potential to address the issue of plastic waste and pollution, there are also concerns about its environmental impact and resource requirements. Further research and development is being conducted to better understand the implications of advanced chemical recycling and to ensure that it is implemented in a sustainable and responsible manner.
At the same time, biopolymers and plastic alternatives are also being further researched with the ultimate goal of looking beyond fossil fuel as an industrial feedstock. Until then, the chemical recycling of polymers is an essential tool to manage the vast amount of plastic that is created each year. With plastic production and use growing annually, so to must the plastics industry’s methods for managing plastic waste.
As the IEA states, “Recycling offsets the need for primary production, but globally only about 10% of plastic is recycled. While the share is increasing, progress needs to accelerate.”
Read more on this topic: Playmobil Toys Act on New Plant-Based Industrial Feedstock or What Brainstorming for Sustainable Polymer Raw Materials Found
Photo credit: Raw Pixel on Freepik, Freepik, Fanjianhua, Freepik, Wirestock, & Frimufilms