Within living memory of many chemical suppliers are the glory days of China’s economic boom. Back then, the country focused on basic industrial output, such as steel and textiles, becoming an excellent customer for industrial feedstocks.
Fast forward to today, and an increasingly self-sufficient China has become an unstoppable force in chemical markets.
Nowhere is this more apparent that in the aromatic chemicals sector, where upstream growth has left China by far the largest producer of polyethylene in the world with 75% of market share. Moreover, China is currently looking at bigger and better facilities to gain larger economies of scale and market dominance. It is now closing its early refining plants – the so-called teapot refineries (due to their shape) - and instead, is investing heavily in mega-production units.
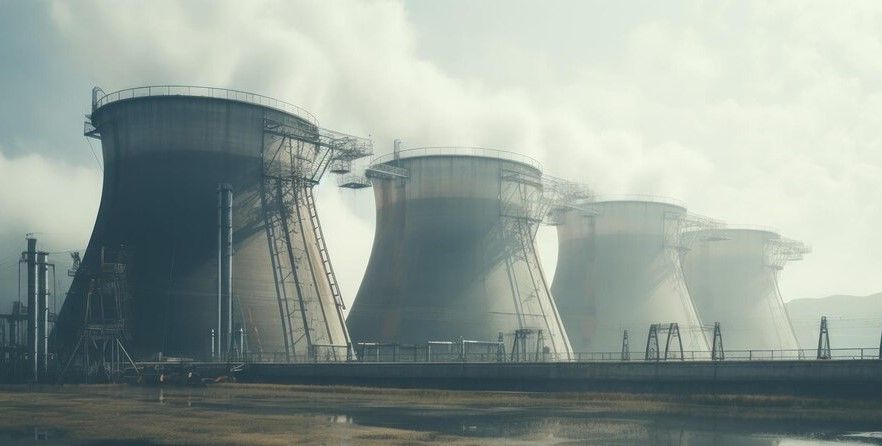
The Zhejiang Petroleum and Chemical (ZPC) chemical complex on Dayushan Island, is a classic example of the staggering boost in chemical output. Built in 2019 near the Chinese ports of Shanghai and Ningbo, the chemical facility originally had an enormous refining capacity of 20 million metric tons (t) of oil per year. Yet that soon doubled in 2022 to make it one of the largest refineries in the world.
“In just 6 years,” notes the chemical industry journal CE&N, “ZPC built facilities with nearly the basic chemical output of LyondellBasell Industries, one of the world’s largest established chemical makers.”
“It’s worth looking at the history of some of these new major producers,” explains Katie Elliot, a research director for aromatics at S&P Global Commodity Insights,. “China has built its weaving and clothing industry, developed upstream into polyester, then PTA, and now is building [p-xylene] and refining capacity.”
Hengli Petrochemical is another example of the progression that the Chinese chemical industry has made. Originally a specialist in polyester production for Chinese textile manufacturers. However, in 2019, the company constructed an integrated refinery and petrochemical complex in Dalian, China, which is able to process 20 million t of oil annually to produce 4.5 million t of p-xylene and 1.2 million t of benzene per year.
This upstreaming into refining feedstocks outside of its traditional markets, means that today the company also operates an ethylene cracker, as well as an aromatics derivatives complex that is far removed from its early polyester aims.
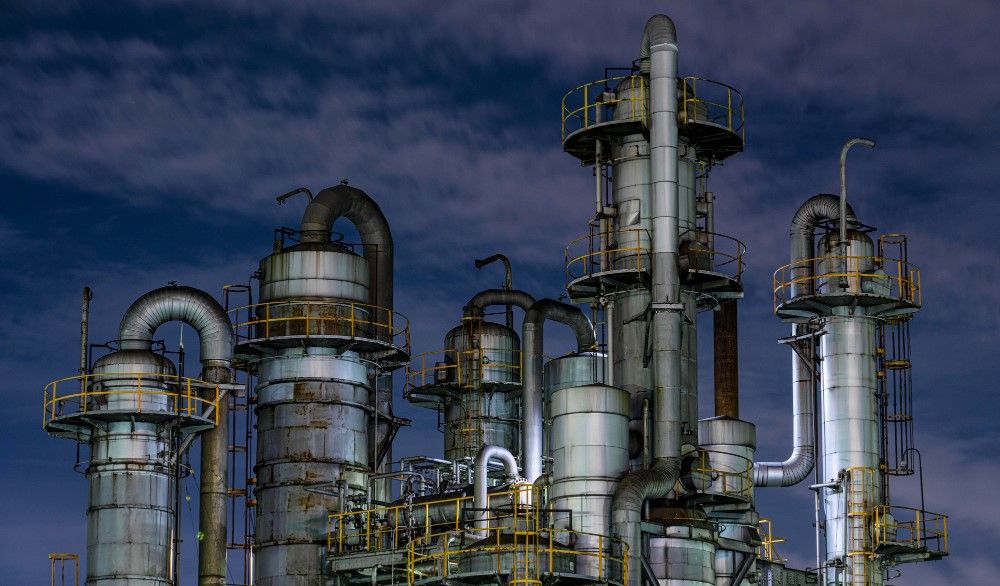
The reason for such expansive growth is based on predictions of falling fossil fuel demand. Many experts already believe that oil production has peaked as more fuel-efficient vehicles and electric cars begin to enter the market.
Those same experts are also predicting demand of oil-based chemical feedstocks to remain buoyant, peaking in about 20 years’ time.
The result is chemical production geared heavily into this sector. As the CE&N report notes, “Integrated refining and chemical complexes typically produce 15–20% of their output as chemicals like olefins and aromatics. ZPC’s chemical yield is 40%.”
It is a smart strategic move. “Aromatic manufacturing plays to China’s strengths,” says Elliot. “Other regions, such as North America and the Middle East, have access to cheap, local natural gas. They can make gas-based chemicals like ethylene, propylene, polyethylene, and polypropylene at much lower cost than China can.”
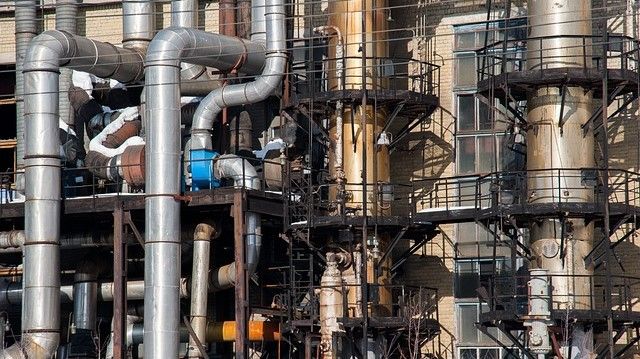
Crude oil, on the other hand is shipped and priced globally. This puts all chemical producers on the same feedstock price list. Where China can gain an advantage is from its low capital costs, large economies of scale, and huge local markets.
The trouble for the rest of the world is that those local, Chinese markets are slowing down. This is leaving a lot of spare aromatic chemical feedstock available for export.
“We’ve seen a significant deterioration in polycarbonate, ABS, and polystyrene,” Frank Bozich, CEO of the styrenic polymers maker Trinseo. “And what those chemistries all have in common is significant overhang in capacity in China.”
It is a deluge on the market which is having catastrophic consequences for other aromatics producers around the world. This is especially true in Europe and Japan, where energy costs have surged as quickly as natural gas prices.
“China has indeed been the main source of capacity growth in aromatics over the last few years,” notes S&P’s Elliot. “With multiple integrated complexes coming onstream in a short period of time, multiple products have moved into an oversupply situation.”
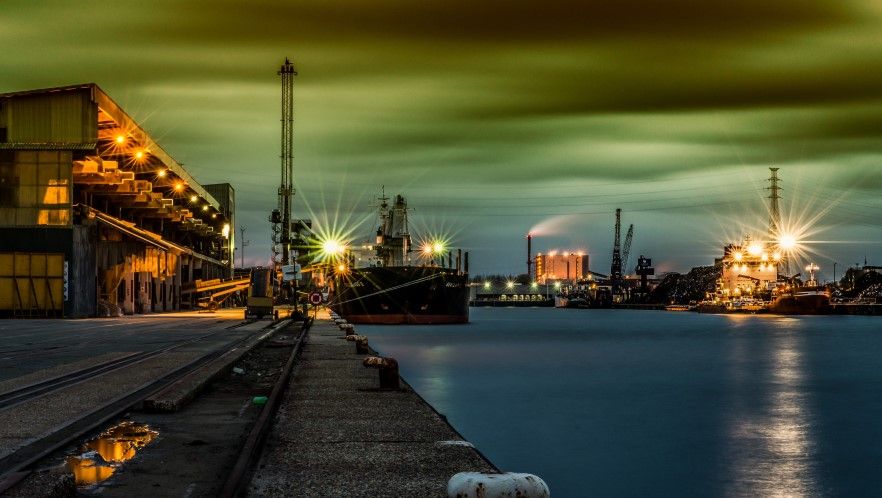
European businesses involved in the polyester chemical industry have been forced to close factories due to Chinese exports. The European Commission has even put taxes on PET product imports.
“Last November,” reports CE&N, “Indorama Ventures said it would mothball its PTA plant in Portugal because it would be cheaper to buy the raw material it needs for PET. Ineos recently decided to close a PTA unit in Belgium. JBF Global Europe, an affiliate of India’s JBF Industries, idled a PET plant adjacent to Ineos’s complex.”
Meanwhile, Trinseo has also shut down two of its styrene plants: one in the Netherlands and one in Germany, finding it cheaper to import the styrene it needs rather than produce its own.
“If we were producing it now,” confirms David Stasse, the company’s CFO, “we would have significant losses, as are other European styrene producers now as we speak.”
The situation is the same in Japan, with both Idemitsu Kosan and Mitsui Chemicals announcing that their PET and bisphenol A facilities will close before the end of the year.
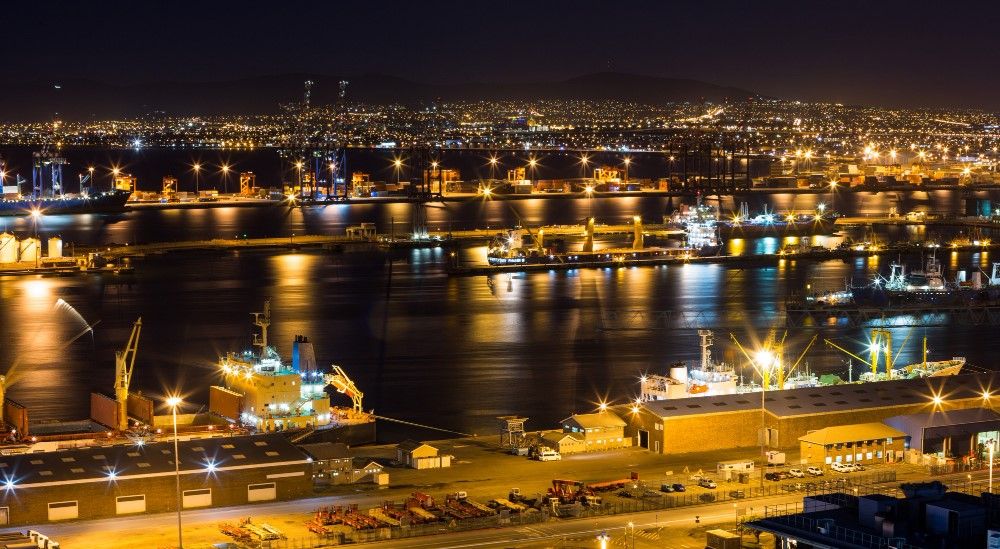
The best hope for aromatic chemical producers outside of China is a rebound in the Chinese domestic market. If the Chinese economy can return to double digit growth, or if the uncertainty in its housing market can foster improved consumption, then its chemical exports to Japan and Europe may ease off.
Unfortunately, the outlook does not look too promising.
“Recovery in aromatics chains is expected to be slow,” says Elliot. While she believes that the styrene market has already reached its lowest ebb, she predicts that PET prices will continue to fall steadily for years to come.
How many more chemical plants in Europe and Japan will close as the surge in Chinese exports continues is not yet known, as many still hope that the global chemical market will adjust.
As the CE&N report concludes, “The global chemical industry might eventually absorb the new Chinese capacity. But for companies in Europe and Japan that closed plants, a recovery will never come.”
Photo credit: Freepik, Nuraghies on Freepik, Wavebreakmedia_micro, Alexey Klen on Pixabay, Robert Jones, & Wirestock