Following COVID, the supply chain crisis, the war in Ukraine, and energy market fluctuations, what are the trends that will help the chemicals sector transition over the coming months and years?
While the disruptions have been chaotic on an economic, social, and political level, the chemical industry has actually improved its position over other industries. This is a true sign of the resilience of chemical demand and the security of the industry’s place in modern living.
Consequently, the chemicals sector is now well placed to take the lead in the upcoming changes to how business is done and how things are made.
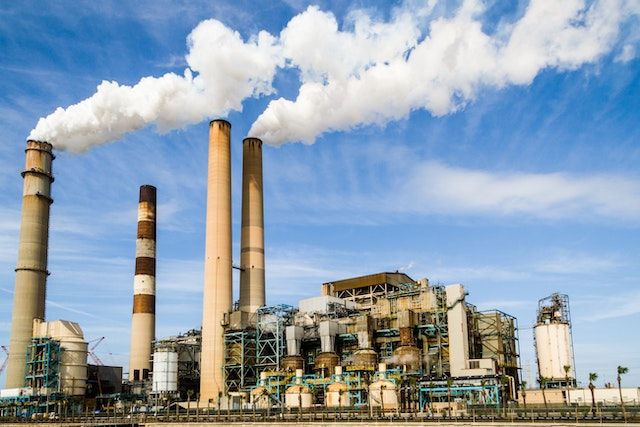
But how can chemical companies make plans to overcome impending challenges and set themselves up for a successful long-term future when macroeconomic influences imply unpredictability in the global economy?
The regular paths to profit in the chemical industry have significantly altered over the last decade. The flow of fossil fuels from Russia and the Middle East have been hampered by war and embargo. The political and social demand for net zero has shone a spotlight on chemical processes and materials. Markets have shifted from West to East and supply chains have proven to be fragile by the COVID pandemic.
These factors have set the course for where successful chemical producers need to be – adaptive to consumer preferences, solid in supply chain, and prepared for economic uncertainty.
In light of these factors, 2023 may be a pivotal year, with these four trends likely to have the largest impact on the path the chemical industry takes.
Sustainable Energy
Larger chemical producers need to focus on achieving their stated emission reduction objectives. Many targets set during the last decade are now rapidly approaching, with those 2030 deadlines now only a few years away.
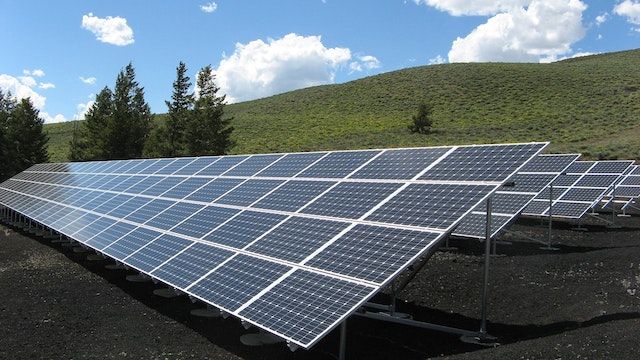
Key to these goals will be rethinking energy sources. The recent energy crisis has fortunately focused governments on the need for energy security for both industry and households. This will mean an expansion of cleaner sources such as nuclear, wind, solar, as well as improved insulation and energy capture and recycle systems.
Like most homeowners, energy price spikes have forced chemical producers and suppliers to reconsider how they power their processes and the cost of long-distance logistics.
Innovative Raw Materials
With long supply chains suddenly seeming a less attractive proposition, traditional feedstock suppliers such as Russia or the Middle East being banned or labelled unacceptable, chemical producers and their customers are attempting to either source closer to home or to do more with less.
This can be achieved through innovation.
Nanotechnologies for example, can reduce polymer requirements by using easily accessible carbon to make nanomaterials a suitable replacement feedstock.
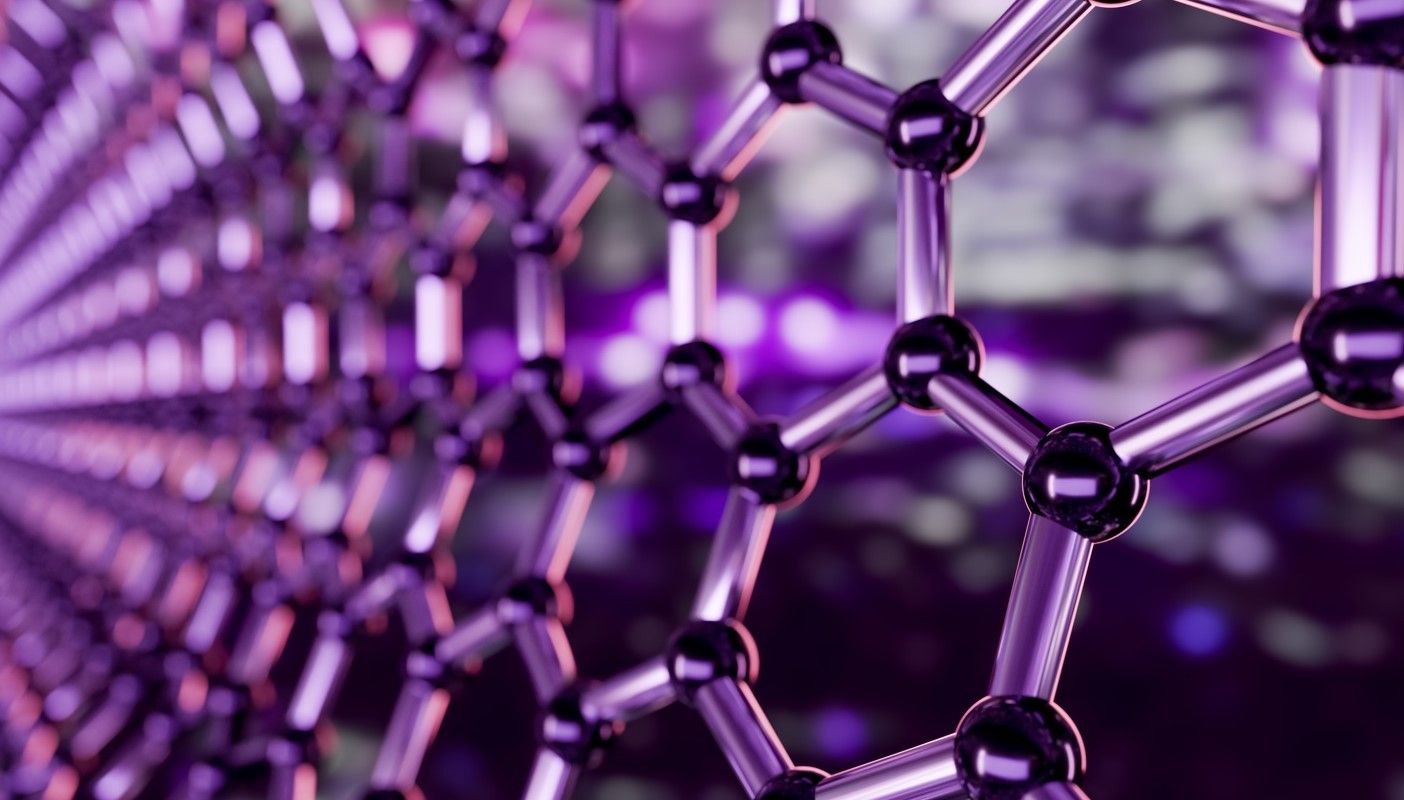
With incredibly low loading (often as low as 0.5 wt.%), polymer manufacturers using carbon nanotubes are able to increase strength, improve scratch and chemical resistance, vary electrical and thermal conductivity, and even add antimicrobial properties – all while reducing overall raw material usage.
To learn more about achieving these innovative gains through nanomaterial application read: Nanotechnology: The Future of Raw Materials
Supply Chain Transformation
The shock waves that the COVID pandemic sent through the supply chain are still being felt so many months later. This has left chemical producers to never again take for granted the ability to get product to market or to freely be able to source raw materials. With the next global health pandemic possibly just months away, avoiding future calamities will require making changes.
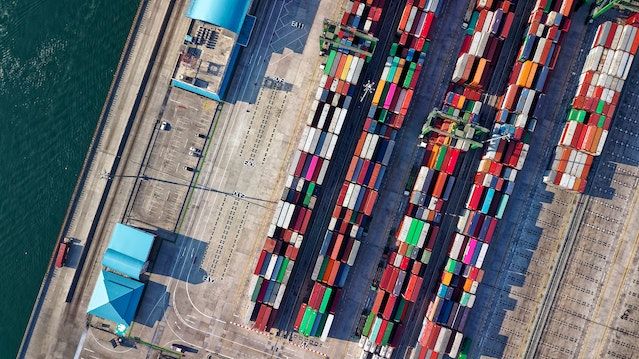
As the chemical industry consultants at Deloitte highlight, “Over the coming year, re-evaluating supply-chain structures will be critical for producers to meet the scale of changes required for the next decade. Overall, supply chains will need to balance costs and carbon footprint while managing resiliency—a tough act that will require companies to consider strategies markedly different than those of the past three decades.”
Digitalization
Chemical companies' decision-making processes are evolving as a result of digital implementation. To monetize current investments before extending to fresh areas, the near-term focus will be on maintaining current platforms. By analysing and optimizing digital capabilities, producers may increasingly embrace technology to bolster customer relations, streamline processes, and speed up product development.
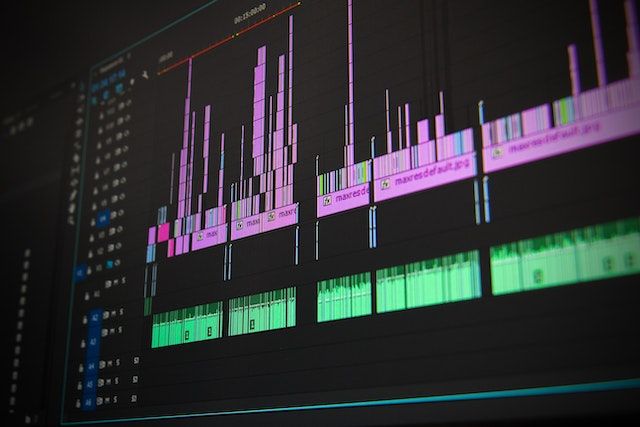
For these precarious times, chemical corporations have prepared a strong ‘war chest’, while smaller chemical producers and suppliers have also performed well right across the industry.
Using this wisely, chemical manufacturers can play a critical role in meeting climate change targets, calming markets, and supporting supply chains while still maintaining the standards in chemical products and raw materials that modern life demands.
However, to meet these challenges chemical firms will need to undertake fundamental changes to remain competitive in an ever-changing geopolitical environment. These changes may be proactive or reactive, but however they are made chemical firms will need to prepare for the difficulties in the upcoming year, such as global inflation and oil price instability.
With the disruptions of 2022 now left behind, the chemical sector must learn from the past and look to the years ahead.
Photo credit: Pixabay on Pexels, Tom Fisk, Pixabay, Freepik, Pixabay, & PchVector