Because plastic manufacturers are good at their jobs, most of their products are strong and durable.
While this is of great benefit to consumers, it also means that plastic waste can accumulate in the environment for generations. Even once invisible to the naked eye, nanoplastics persist in the soil and water and are now present in every living creature on the planet.
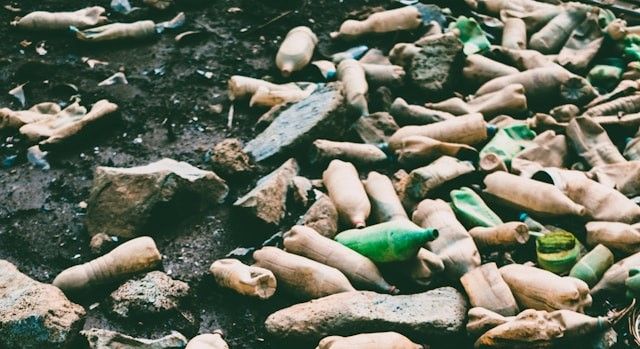
Polyesters are widely used in daily life because of their affordability, adaptability, and durability. PET, for example,is used in bottles, packaging, and textile fibres, and a host of other household and industrial products. Even though PET is mechanically recycled extensively, the quality of recovered PET (rPET) is sometimes compromised by current processes, yet rPET is still more expensive than making new plastic from raw materials.
Research into improving chemical recycling and upcycling techniques frequently assumes that there is an easily accessible supply of PET available to be recycled. Yet the majority of PET waste is contaminated with dyes and other polymers.
Current processes for separating PET from other plastic waste are expensive and time consuming. For instance, separating PLA and PET is complex because they have similar densities and properties. PET waste streams are often contaminated with PLA which leads to poor recovery and expensive separation costs, as the two forms of polymer have distinct depolymerisation temperatures.
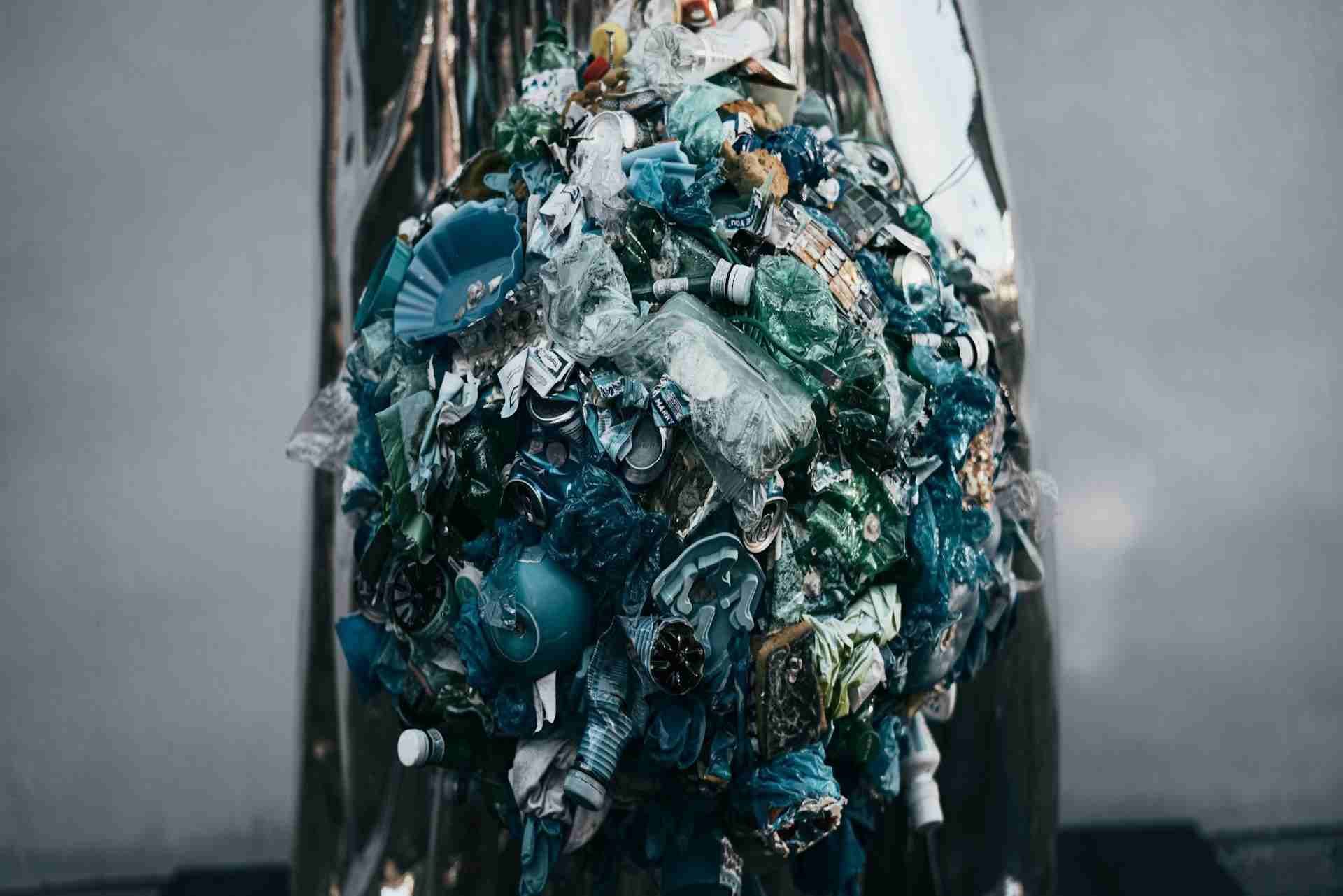
Now a team of polymer researchers from Washington State University have discovered a major advance in recycling technology. The breakthrough is based on using a metal-free catalytic sorting technique which can deconstruct polyester from post-consumer plastic waste, including textiles, plastic mixes, and multilayer packaging materials.
Related articles: Plastic to Soap: Young Chemist’s Eco-Dream Turns to Reality or New Polymer Production Method for a More Pliant, Eco-Friendly PVC
“If you want to deconstruct multi-layer plastic films, the first step is to deconstruct the PET,” explains Prof. Hongfei Lin who co-authored the research. “The catalyst used in the reaction was very selective, so they can pull out and break down the PET in the mixed plastics.”
The research team have now published their findings in the journal Cell, which states that, “The method employs N-methylpiperidine, a tertiary amine catalyst in methanol, to depolymerize polyethylene terephthalate (PET).”
Despite being conducted at a temperature of only 160°C for one hour, all of the plastic was broken down to yield dimethyl terephthalate and ethylene glycol. The process was even able to breakdown PET from multilayer plastic films, such as vacuum-sealed storage bags.
“The concept is to convert the polyesters to monomers. Those monomers can be re-synthesized to the polymers, and the new polymer is like brand new polymer,” notes Lin. “The quality is going to be the same as the polymers when they are first made — and that’s the uniqueness about chemical recycling.”
The study also highlights the versatility of the new chemical recycling process. Explaining how it, “… also effectively breaks down other polyesters, including polylactic acid, polycarbonate, and polybutylene terephthalate, yielding high-yield monomers at relatively low temperatures.”
“The catalyst works very well and is very efficient, so we got very high yields, and the operating conditions are mild,” says Lin who led the research alongside Dr Shaoqu Xie.
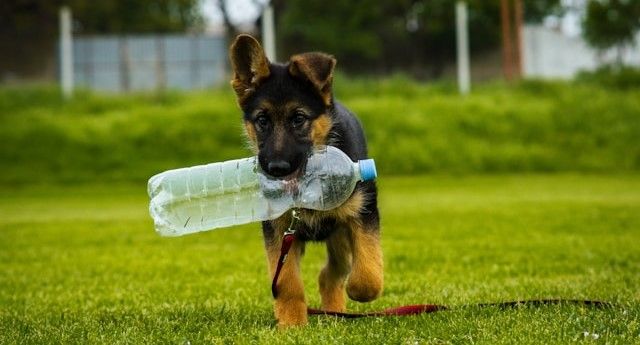
The battle to make chemical recycling more cost efficient is key in solving the problem of plastic waste. By developing a process which is able to extract monomers from PET, even when mixed in with other household waste, such as polyethylene, polypropylene, and nylon the chemical industry will be able to take a major step towards plastic circularity.
Then, at last, raw material suppliers will be able to offer manufacturers sustainable feedstocks which are economically viable and of equal quality to virgin-plastic.
Photo credit: Claudio Schwarz on Unsplash, Julia Joppien, Mihaly Koles, & Nyegi