Recent headlines have drawn attention to Europe’s dependency on Russian gas, highlighting how badly the chemical industry will be damaged. There are also fears for populations in poorer countries who import massive quantities of Russian and Ukrainian wheat.
However, the rubber industry is also suffering as raw material supplies stutter and prices climb.
While rubber processing rarely makes headlines, it is a key component of a healthy economy and a provider of 300,000 direct and indirect jobs globally. Many of which are now under threat from the worsening conflict in Ukraine.
“Russia is one of the most important suppliers to the global rubber industry,” notes a recent report by Jager Group- a specialist producer of rubber. “Russian suppliers of polybutadiene (BR) and isobutene-isoprene rubber (IIR) each have double-digit market shares. In 2021, Russian companies supplied about 550,000 tons of carbon black and 240,000 tons of synthetic rubber to the European Union.”
Consequently, purchasing officers are desperately seeking alternative sources. But it is becoming apparent that in the short term, demand is outstripping supply. At the same time, bottlenecks are forming and logistics for essential raw materials are being entangled in the global supply chain crisis.
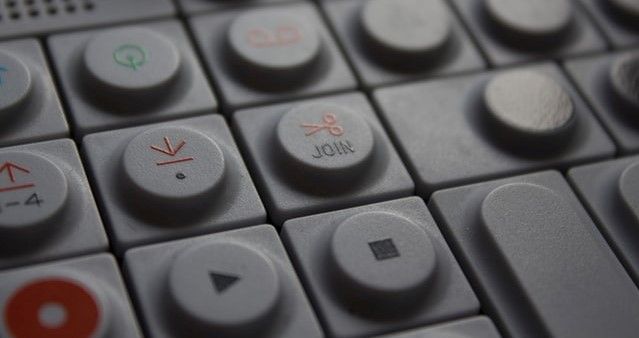
Combined with the war, the situation is showing the fragility of having a complex, international supplier structure. It is a situation which is causing manufacturers to re-examine the efficiency benefits of just-in-time deliveries.
If you want to learn more about this topic then read: How the Chemical Industry can Respond to a Russian Feedstock Embargo or 7 Ways that the War in Ukraine is Changing Raw Material Procurement.
Specifically, what is different about the bottlenecks being created by the Ukraine war is that the level of destruction is creating a long-term shortage for a number of key industrial ingredients. Even if the war ends tomorrow, it will take years to reconstruct the industrial capacity which Ukraine previously provided.
With the head of NATO now warning that the war could drag on for years, then the damage to supply chains is not a standard correction between supply and demand as experienced in previous crises, but is instead a long-term supply chain failure.
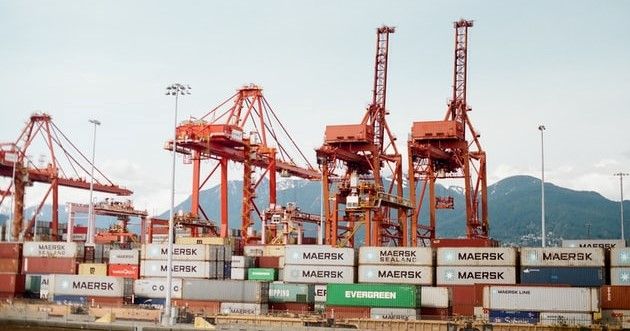
To reflect this new position, more and more governments are realigning their trade and resource policies on protecting national interests. Many are also leveraging their natural resources and production advantages for geopolitical manoeuvring. If this trend continues, then it is likely that international trade will be more frequently disrupted in the future by conflicts, trade wars, and embargoes.
It is what headline writers call ‘the new normal’ and means that manufacturing companies must adjust their current raw material purchasing practices, as well as be prepared to react for future changes. But how?
How can rubber processors better handle current and future shortages of raw materials?
1. Supply Chain Restructuring. The global pandemic, Trump trade wars, and the Russian invasion are highlighting the importance of local, stable suppliers. Consequently, more rubber processing companies are attempting to source feedstocks within their home regions. This avoids bottlenecks, shortens supply routes, and avoids border tariffs and paperwork.
2. Monitor geopolitical developments. Recent events have made it apparent that timely decision making and being aware of global events can avoid disaster. Many Ukrainian companies were able to quickly move stock and production capacity away from the Russian border in anticipation of the conflict. While wiser overseas companies bought Ukrainian supplies in January and February and had them shipped out before the war began. This was achieved only by anticipating the oncoming war.
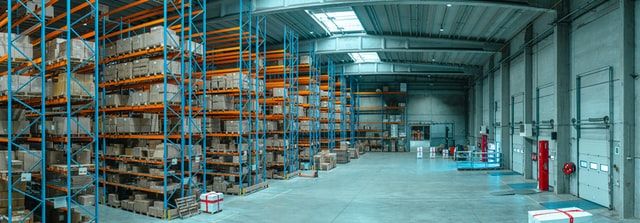
3. Simplifying supply chains. While just-in-time strategies seemed the best option just a few years ago, global events have proven how fragile this system can be. By ‘taking the warehouse off the road’, reducing supply chain complexity to avoid sanctions and tariffs, and holding reserve stock (despite the higher costs) production losses can be avoided when the unexpected happens. These measures can at least buy time during critical situations.
4. Diversifying supply chains. While having local and stable raw material supplies is high advisable, diversification also has its benefits and actually provides its own stability.
For example, an American manufacturer may source raw materials from a secure and safe fellow-American supplier – the most stable option. However, natural disasters may disrupt even local supply chains. In this case, having some diversity and sources from multiple regions can be beneficial.
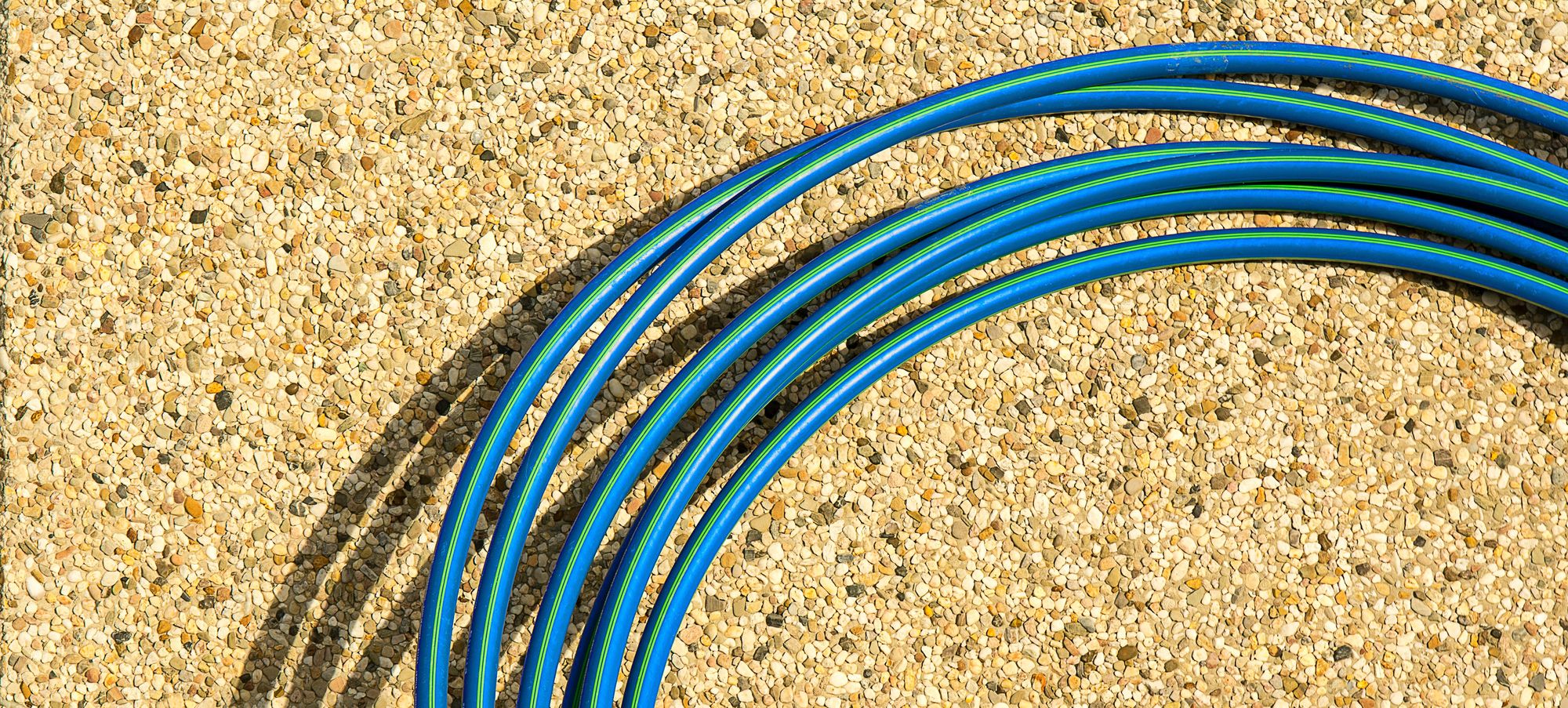
“The war in Ukraine and the sanctions against Russia have hit the rubber processing industries hard,” notes the Jaeger report. “Numerous supply chains have been cut off and it is unclear if and when the situation will return to normal. This is exacerbating the pandemic-related shortage of raw materials and putting industrial companies in a tight spot due to rising raw material prices.”
The human cost in Ukraine has been even worse, causing untold hardship and misery across the region.
While further afield, the economic ramifications of the war are also mounting, putting rubber manufacturers under enormous pressure just to survive.
Photo credit: Kyle Ryan on Unsplash, Vallentin Muller, Jacques Dillies, Monstera on pexels, & Jan van der Wolf