The world has a petrochemical addiction.
Through better insulation and heat exchangers homes can be carbon neutral. With wind turbines, solar panels, and electric vehicles transport can also become more sustainable. But oil and natural gas are still needed as an industrial feedstock to make the chemical products for the paints, plastics, coatings, dyes, fabrics, packaging, explosives, batteries, cleaners, adhesives, and cosmetics that everyone uses.
The global industrial chemicals industry is a powerhouse for the economy, worth $5 trillion. But it is also a major polluter with the world’s third-largest carbon footprint. The result is a chemicals sector that is under tremendous political and public pressure to improve its practises. A chemical industry that needs to step away from its conventional energy-intensive, inefficient, and contaminating operations.
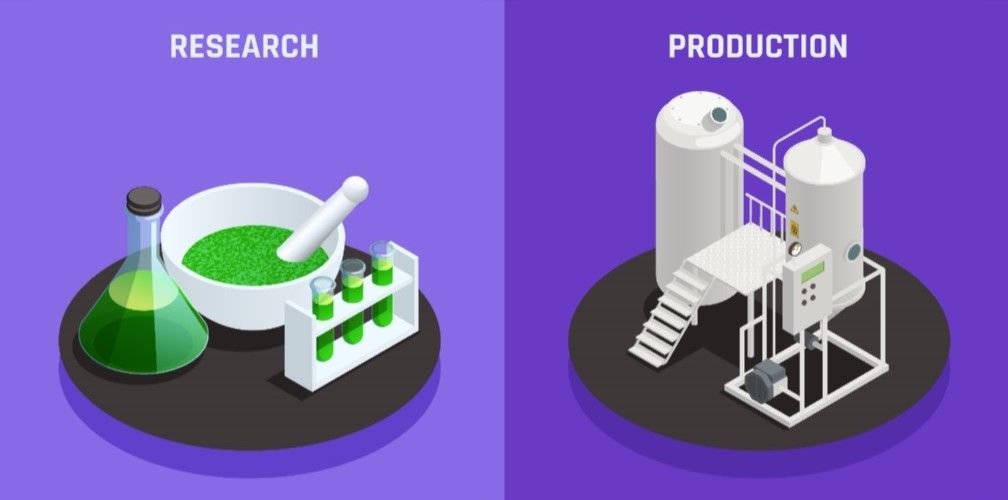
Now a start-up from Texas appears to have found a way. Combining the right chemical process and business model to make an economic success of industrial green chemicals.
Founded only seven years ago, the company is called Solugen. During this short time, it has developed a method that uses biology to create a variety of products, such as corrosion inhibitors and plant nutrients, without the need for the carbon-intensive fossil fuel feedstocks and dangerous chemical waste streams that come with traditional petrochemicals.
A clear sign of its success has been the announcement that the company is expanding to build a new 46,000 m2 biomanufacturing facility, known as Bioforge 2, in Marshall, Minnesota. A move which science journalist Tom Howarth, who holds a master’s degree in Chemical Engineering from the University of Cambridge, describes as “the beginning of a new era for the chemicals industry, wherein a wide range of the chemicals can be produced at scale at a single plant with no carbon emissions or waste.”
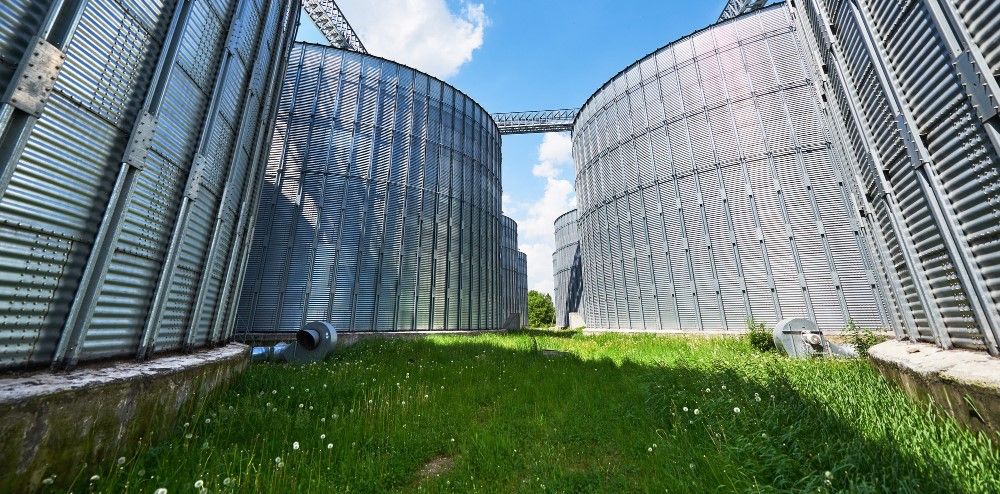
“One of the biggest challenges for the chemical industry is speeding up the pace of innovation to develop new catalysts for desired chemical transformations quickly,” notes the California Institute of Technology’s Prof. Karthish Manthiram. “[This start-up] has proven that their platform leads to fast results, alleviating this bottleneck.”
What is most notable about the chemical business is the speed at which it scales up combined with its versatile green chemistry. It does this by employing processes based on genetically modified enzymes. These function as biological catalysts to help a molecule combine with another while staying unchanged themselves, enabling the synthesis of a variety of molecules from similar chemical techniques.
The conventional chemical processes used by its competitors can take a decade or more to progress from concept to market. But with this innovative idea, a green chemical producer can now grow much faster.
“The efficiency and scalability of our process mean we can provide our customers with the same chemistries they know and trust at a lower cost, higher performance and much more favorable environmental profile,” explains Tom Richardson, the company’s interim chief commercial officer.
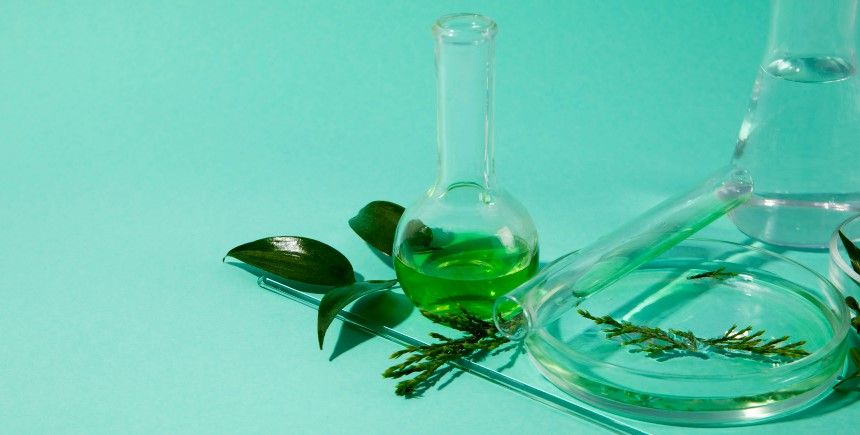
In comparison to conventional petrochemical processes, green chemical production can be extremely straightforward. Feeding maize sugar into a reactor allows the enzymes to transform it into an energetically desirable intermediate. Subsequently, the intermediate is converted into a final chemical raw material using conventional chemical reactions.
In order to obtain the concentration that the customer requires, water and trace contaminants are evaporated off in a third purifying step.
It is a concept born from the latest breakthroughs in synthetic biology – a field of science that reengineers organisms, such as microbes, to give them new capabilities. Today’s redesigning is sped up by using artificial intelligence to form new enzymes much faster than could be achieved in the early days of the bio-chemical production.
While a traditional petrochemical process might turn 50 percent of its fossil fuel feedstock into chemical products, the Bioforge converts about 96 percent of its corn sugar feed, with the company still working to increase this efficiency rate to 100% over the next few years.
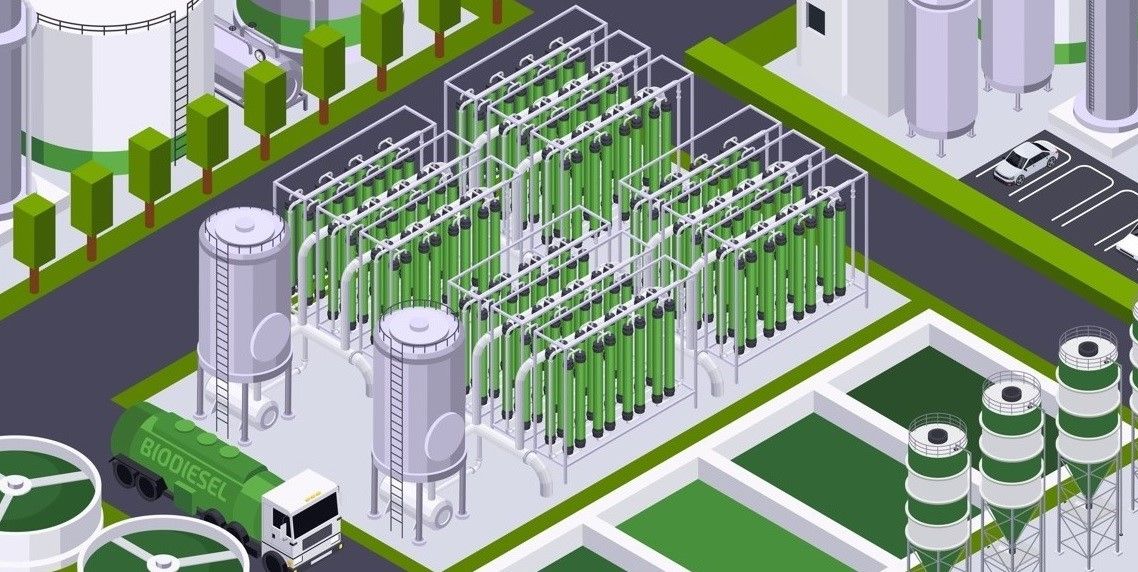
By using a plant-based feedstock, the process is carbon-negative, as the corn absorbs carbon when growing. Additionally, bio-chemical facilities are able to function much closer to markets than conventional, high-polluting, and potentially dangerous, chemical plants. A vision which Richardson calls a ‘decentralised bioeconomy’ based on a technology that can create a wide range of goods with zero waste and carbon emissions.
“We envision a world where you can have entirely carbon-negative cities where every single material that you can see, feel and touch can be produced with Solugen’s chemistry that is sequestering CO2 from the atmosphere,” notes Richardson.
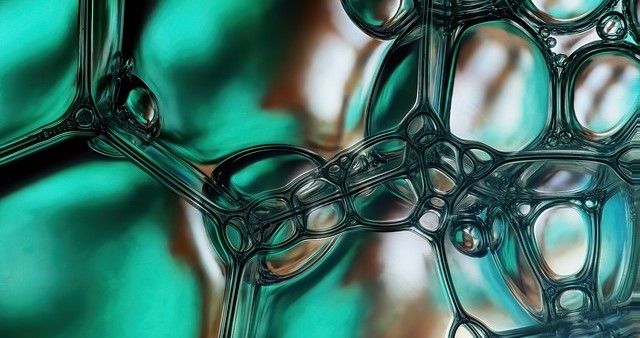
Fortunately, Solugen is not alone in making headway in biochemistry.
California-based Newlight Technologies, for example, has been utilising the power of microbes to capture greenhouse gases since 2020. It uses an eco-process which produces a resin for use in the manufacture of textiles and foodware. Origin Materials, meanwhile, converts wood chips into a chemical feedstock for the manufacture of polyethylene terephthalate (PET). Its first commercial-scale facility opened in the summer providing a green feedstock for plastic bags and packaging.
Chemical companies such as these are drawing attention from investors the world over, each looking to profit from the growing demand for eco-friendly chemical products.
At present, the global green chemicals market is valued at less than $100 billion. A far cry from the huge value of the multi-national petrochemical giants, such as BASF and Sabic. However, it is predicted to grow at more than 12% every year until 2030.
If start-ups continue to show good profits making carbon-negative chemical products, then surely it won’t be long before the larger chemical manufacturers follow suit.
A revolution in chemical production that could make a safer, cleaner world for everyone.
Read more about this topic at AG CHEMI GROUP.
Europe’s Chemical Industry Challenge and Plan
Chemical Industry Chief Explains Way to Realise Eco-Vision
Mixed Polymer Recycling Made Simple
Photo credit: Freepik, Macrovector, Freepik, Standret on Freepik, Macrovector, & Binärius from Pixabay