For decades, the plastics industry has relied heavily on fossil fuels—not just for energy, but as a primary feedstock in the production process. As global efforts to reduce carbon emissions and mitigate climate change intensify, the pressure on the industry to find sustainable alternatives is mounting.
Fortunately, emerging technologies and innovative materials are offering a glimpse into a future where plastics can be produced without fossil fuels. From bio-based feedstocks derived from plants and waste to advanced recycling methods that give new life to existing plastics, the industry has multiple pathways to explore.
Here is a brief overview of the most promising alternatives to crude oil as a plastic feedstock and the options coming online which will pave the way for a future that balances performance with environmental responsibility.
Net Zero Carbon Cracker
One of the largest projects going online to provide net zero feedstocks for the polymer industry is Dow’s Path2Zero project in Alberta, Canada. Currently only Phase 1 is under construction with a completion date set for 2027 when it will produce 1.3 million tonnes/year of ethylene and polyethylene. Phase 2 should be finished by 2029 to add a further 600,000 tonnes/year of capacity.
While this represents a massive increase in global low-carbon plastic capacity, Dow estimates that it will only represent less than 2% of predicted market demand. By 2030, Dow’s highest estimate for demand is in excess of 200 million tonnes per year, whereas the highest estimate for global output is only 75 million tonnes.
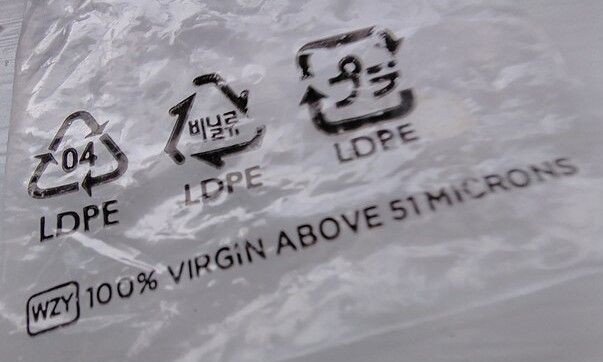
“That is the largest dislocation in supply and demand that I’ve seen in my 36-year career,” acknowledges Dow’s chief commercial officer, Dan Futter. “We’re starting to see the first signs of the market emerging… What we’re seeing is a market for something like 200 million tonnes of low carbon chemicals by 2030. If you compare that with what we would estimate the supply side to be, it is much smaller.”
E-Naphtha
A further new entrant to the market is Borealis (a leading producer of plastic and chemical products for industry) which last year announced an agreement with Infinium for a supply of e-naphtha produced from green hydrogen and captured waste CO2. The e-naphtha will then be used as a feedstock to a conventional naphtha cracker to produce ethylene and propylene, which in turn would be used to make PE and PP.
At present, Infinium produces e-naphtha at its Project Pathfinder plant in Texas, with commercial quantities being delivered to Borealis' facility in Porvoo, Finland which has ethylene capacity of 400,000 tonnes/year.
According to the ICIS Supply and Demand Database, “downstream capacities include 102,000 tonnes/year of high-density PE (HDPE), 150,000 tonnes of low-density PE (LDPE), 153,000 tonnes/year of linear low-density PE (LLDPE), and 220,000 tonnes/year of PP.”
Hopes are high for the project’s success, with notable demand growth across Europe for more sustainable plastics as well as low or zero emission polymers for consumer goods.
As a Borealis spokesperson noted, “We already see interest in the market from brand owners/OEMs that are leading in sustainability efforts and incorporating alternative feedstock in their products.”
Green Methanol
Another new company entering the market for low-emission plastics is Vioneo, a polymer producer owned by the global conglomerate AP Moller. With this backing, the company has invested €1.5 billion in a facility in Antwerp which will use an “innovative and proven technology” to produce fossil-free polypropylene (PP) and polyethylene (PE) at scale, using green methanol as a feedstock.”
While a new entrant to the market, the chemical business is headed by the experience of Jan Secher (former CEO of Clariant and Perstop) as well as Alex Hogan (former business director at INEOS Olefins & Polymers).
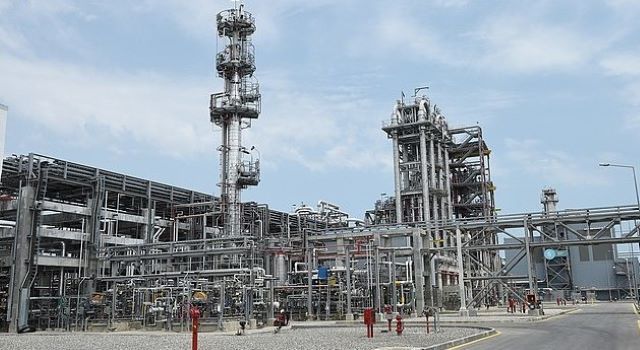
The project is planned to have capacity of around 300,000 tonnes/year of polypropylene (PP) and polyethylene (PE) when it starts commercial production in 2028. Although to get to this point will, according to the UK’s Chemical Industry Journal, require “front-end engineering and design (FEED) in Q4 2024 with a potential final investment decision (FID) in 2025.”
While the details behind the process are still not publicly clear, the company is promoting is as “pioneer fossil-free plastics production.”
“To make green methanol, Vioneo would use biogenic CO2 and presumably green hydrogen from an electrolyzer,” explains the Chemical Industry Journal. “Then presumably again, methanol-to-olefins (MTO) would yield propylene and ethylene, which would be polymerized to PP and PE.”
The company has stated that its technology ensures a completely segregated and traceable supply chain, preventing the mixing of non-certified and approved feedstocks. Renewable electricity will also be used to power production, lowering greenhouse gas (GHG) emissions dramatically.
Vioneo claims that its PP and PE process will save up to 6kg of CO2 per kg of plastic and will be drop-in, virgin quality, ideal for applications in various industries, including domestic products, medical applications, packaging and automotive parts. However, the project is being launched with caveats, primarily that the €1.5 billion in funding will, according to Vioneo, “depend on broad stakeholder support, including updated regulatory frameworks and policies supporting a competitive environment for fossil-free plastics, as well as better conditions for the European chemicals industry such as lower energy costs.” Also adding that, “the success of the venture requires long-term offtake agreements of its customers.”
Low-Carbon Methanol
Celanese is another firm which is looking to utilise commercial volumes of low-carbon methanol and derivatives sourced from waste CO2.
As the Chemical Industry Journal reports, “In January 2024, the company announced it started running a CCU project at its Clear Lake, Texas, site as part of its Fairway Methanol joint venture with Mitsui & Co. The project is expected to capture 180,000 tonnes/year of CO2 industrial emissions and produce 130,000 tonnes/year of low-carbon methanol.”
Low-carbon methanol is a chemical raw material which can be used to make vinyl acetate monomer (VAM), vinyl acetate ethylene (VAE) emulsions, and other chemical products.
“We actively capture carbon off some of the major producers in Clear Lake, Texas, at our site and we take those CO2 emissions… and we recycle it back into the ATR (autothermal reformer),” explains the company’s CEO, Lori Ryerkerk. Noting that there is plenty of demand for polymers with an eco-friendly label. “We have customers like Amazon that want a lower carbon footprint product, and we are able to meet that customer need,” she adds.
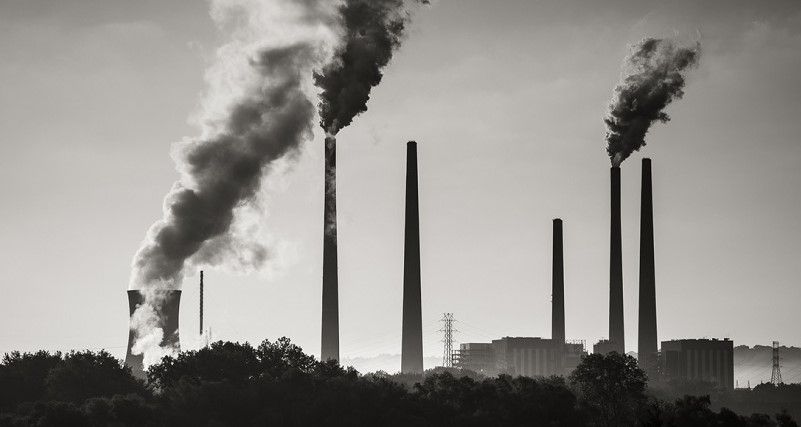
The transition away from fossil fuel-based feedstocks in the plastics industry is both a technological and an economic challenge, but it is also an essential step toward a more sustainable future. Advances in bio-based alternatives, chemical and mechanical recycling, and carbon capture technologies demonstrate that viable pathways exist for reducing the chemical industry’s reliance on non-renewable resources. However, widespread adoption will require significant investment, policy support, and collaboration across industries to scale these solutions effectively.
As consumer demand for sustainable products grows and regulatory frameworks tighten, the incentive for the plastics industry to innovate has never been stronger. By embracing alternative feedstocks and circular economy principles, the chemical industry can not only reduce its environmental footprint but also secure its long-term viability. The shift away from fossil fuel dependency is no longer a question of if, but rather of how quickly and effectively the transition can be achieved.
“It’s a brave new world of decarbonized chemicals and plastics,” notes the Chemical Industry Journal. Adding that, “Meaningful quantities will take time to develop but if there is demand, the volumes will come.”
As Dow’s Dan Futter concludes, “This is going to be a fascinating period.”
Fascinating for us all.