The European chemicals industry has plenty of problems to deal with. High wages, high regulatory constraints, high energy prices, high feedstock costs, and a near stagnant domestic economy.
However, adding to that list is the issue of complex supply chains, as the Red Sea route from Asia through the Suez Canal to Europe continues to suffer from Houthi Rebel attacks. Despite a notable naval presence, several transport ships have been damaged by rockets, drones, and missiles. While most attacks are thwarted, only a handful need to be successful to make chemical traders think twice about how to deliver their raw materials.
The result is that Asian manufacturers are facing competition from the considerably more costly and time-consuming maritime route that circumnavigates the southern tip of Africa, via the Cape of Good Hope. This longer route has increased shipping time, leading to a reduction in global shipping capacity.
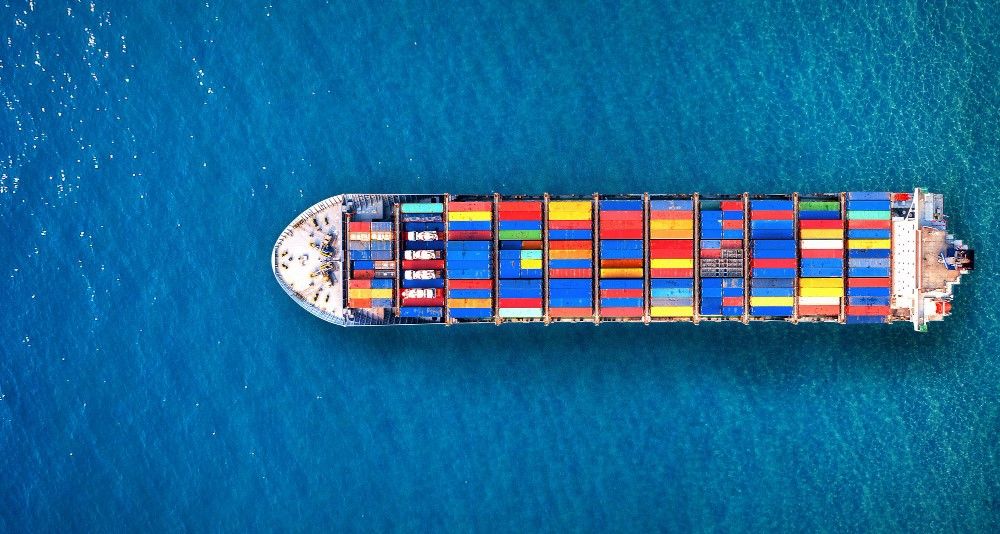
Specifically, a US Defence Intelligence Agency reports that, “Between December 2023 and February 2024, the number of container ships transiting through the Red Sea dropped by 90 percent.” Further data found that only 24 transport ships transited the Red Sea during June 2024 compared to 118during the same month during the year prior.
The timing for this lack of containers and the vessels to transport them is significant as, “… there is increased demand for shipping ahead of the introduction of new trade tariffs,” a recent report in Chemistry World notes. “In recent months, Chinese exporters had been front-loading shipments to get ahead of EU tariffs on electric vehicles imported from China initiated on 4 July.” Adding that, “This frontloading has been exacerbated, he says, in anticipation of additional US tariffs on Chinese electric vehicles and batteries that are set come into force on 1 August.”
The result is a backlog of cargo waiting to be moved.
“Add that to the economic recovery in Asia and you get an ugly picture,” observes Al Greenwood, a chemical industry analyst and a deputy editor at the ICIS chemicals consultancy.
Owing to the scarcity of container ships and the ensuing reduction in shipping capacity, a number of importers from Europe, Türkiye, and India have switched to breakbulk ships, which transport cargo without the need for containers. While this results in extended loading and unloading times, it is better to move the stock rather than waiting for available shipping containers or the vessels to carry them.
Elsewhere, in South Korea, high freight costs have resulted in the cancellation of polymer material shipments.
American exporters and chemical companies are not facing the same issues, as they operate on simpler, more direct routes that avoid the Red Sea. However, US shipping is being impacted by a drought which has reduced capacity through the Panama Canal. Fortunately, for American chemical producers the Panama Canal Authority is set to increase the number of daily slots in August as local rains relieve the difficult conditions.
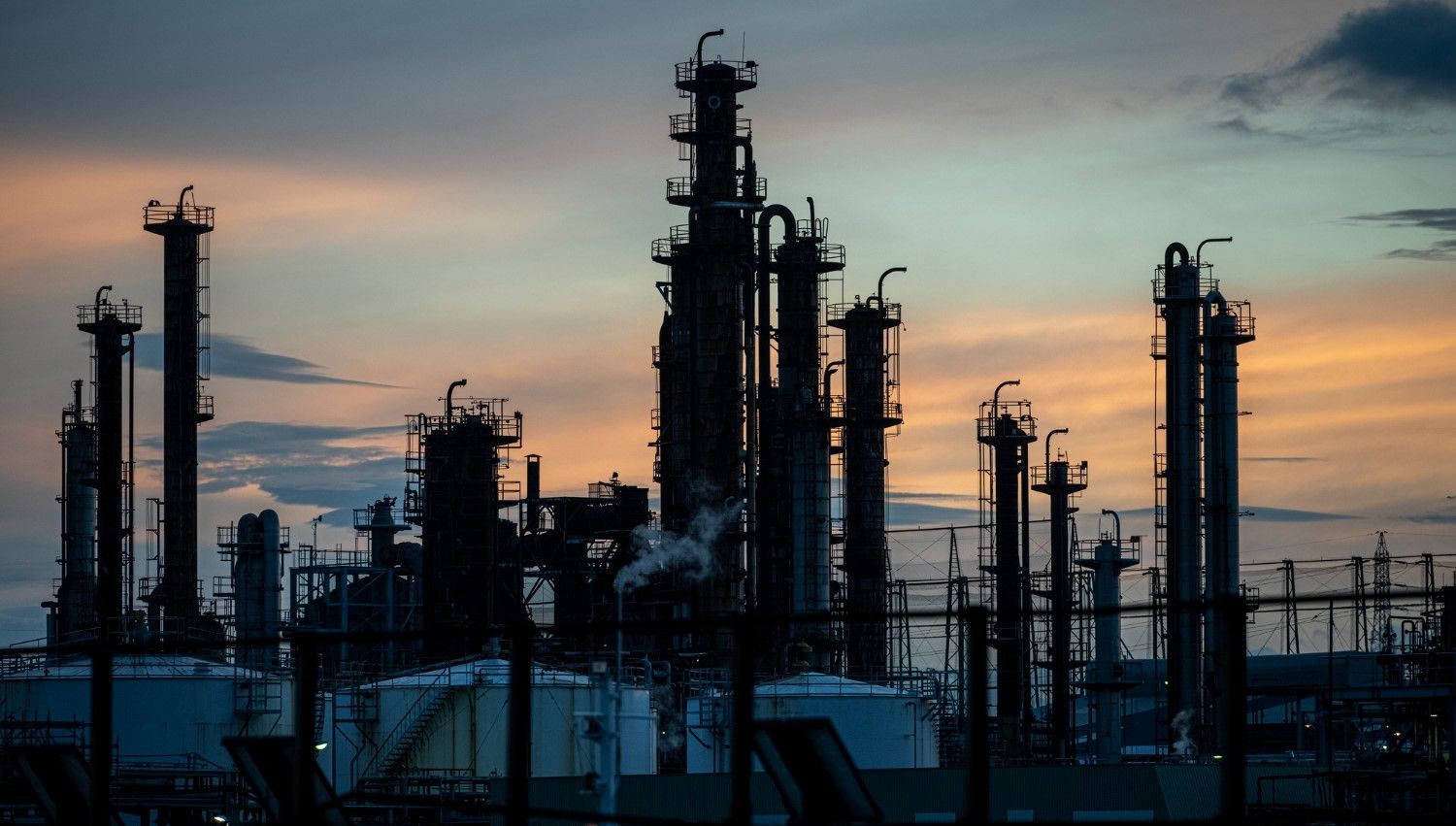
On the positive side for European chemical suppliers, the logistics issue is playing a hand in deglobalizing chemical supply chains. While chemical output may be much cheaper in China, the product is worthless if it cannot be transported to market. Those chemical products that can make the crossing have a greatly increased cost due to the longer journey and the higher prices which shipping companies can charge,
‘If the material is available,” notes Greenwood, “we’ve seen companies turn to European producers, and that’s giving some chemical producers in Europe a break.’
As an April earnings report from LyondellBasell, one of the largest polymer producers in Europe, stated that, “logistics disruptions in the Red Sea restricted competitive imports and led to increased volumes from LYB's local assets for olefins, polyethylene, polypropylene and propylene oxide and derivatives.”
With no clear end in sight to the Houthi insurgency, the future reliability of the Red Sea as a shipping lane remains uncertain, casting a cloud of instability over the chemical industry and other manufacturing sectors. Mitigating these supply chain risks has become a top priority for chemical producers, requiring them to pursue alternative transportation routes, stockpile reserves, and invest in more resilient, diversified sourcing strategies - all of which comes at a significant financial cost.
Ultimately, the conflict's impact on global industry underscores the far-reaching economic consequences that can arise from regional political and military tensions. All without knowing when it will end.
Photo credit: Freepik, tawatchai07, & Wikimedia