Potassium carbonate has many uses in manufacturing. It is a key raw material for the production of items as common as paper and soap. However, one of its most valuable applications is the manufacture of glass. But why?
Glass production is a 5,000-year-old technology that was originally used to make simple objects such as jewellery and drinking vessels, but the glass of today needs to be much stronger as it needs to do so much more.

Today glass is used in household ovens, furniture, barriers and walls in public spaces, high-temperature glass-walled furnaces, telescope and camera lenses, car windscreens, scientific equipment such as test tubes and beakers, lightbulbs, TVs, and more recently, any one of the six billion smartphones, tablets, touchscreens, and electronic devices worldwide.
Achieving these many roles is possible because of the strengthening properties supplied by potassium carbonate (or K2CO3).
How is Potassium Carbonate Used in Glass Production?
There are three elements to making glass:
1. Formers: Most types of glass use silica (in the form of sand) as a former. It makes up the bulk of what glass is.
2. Fluxes: Used to control the temperature at which the formers melt. Potassium carbonate is a common flux as it not only helps control the process, but also aids the transparency, clarity, resistance, and refractive coefficient of the final product.
3. Stabilizers: As the formers and fluxes are water soluble, stabilizers are used to make sure that the glass doesn’t dissolve due to water or humidity. They also help make the glass strong and water resistant.
To make glass, the formers, the fluxes, and the stabilizers are ground into a fine powder which is fused together and then melted.
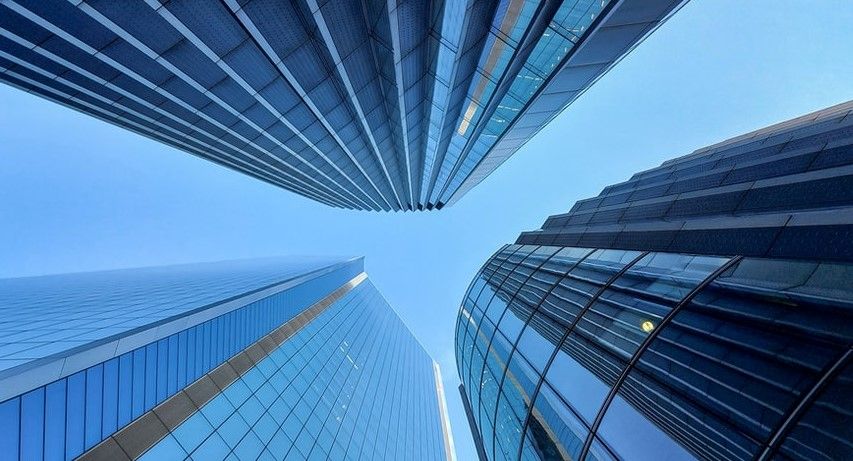
Adjusting the mixtures, temperatures, and rate of cooling, changes the properties of the glass being made. As the experts at Corning (the 3rdlargest producer of glass in the world) note, “Different formulas affect the mechanical, electrical, chemical, optical, and thermal properties of the glasses that are produced. There is no single chemical composition that characterizes all glass.”
But beyond its use as a flux, potassium carbonate is also used in a further process to make specialised, strengthened glass.
AG CHEMI GROUP has been a trusted and well-respected supplier of raw materials to industry since 1994. During that time it has been supplying quality K2CO3 to glass manufacturers in the Czech Republic, Spain, Italy, Germany, and Austria. To learn more about what we can supply your business, visit our website at AG CHEMI GROUP or contact info@agchemigroup.com
How Potassium Carbonate Makes Extra-Strong Glass
To know how potassium carbonate can be used to make glass strong enough for smart phone screens and airplane windows, it is necessary to understand how raw materials work at an atomic level.
A sheet of glass is excellent at handling compressive forces, but it also has many tiny (but invisible to the naked eye) defects on its surface. These defects make it very weak when handling tension forces.
As making glass without any defects is impossible with current technology, manufacturers employ chemistry (and specifically potassium carbonate) to make super-strong glass.
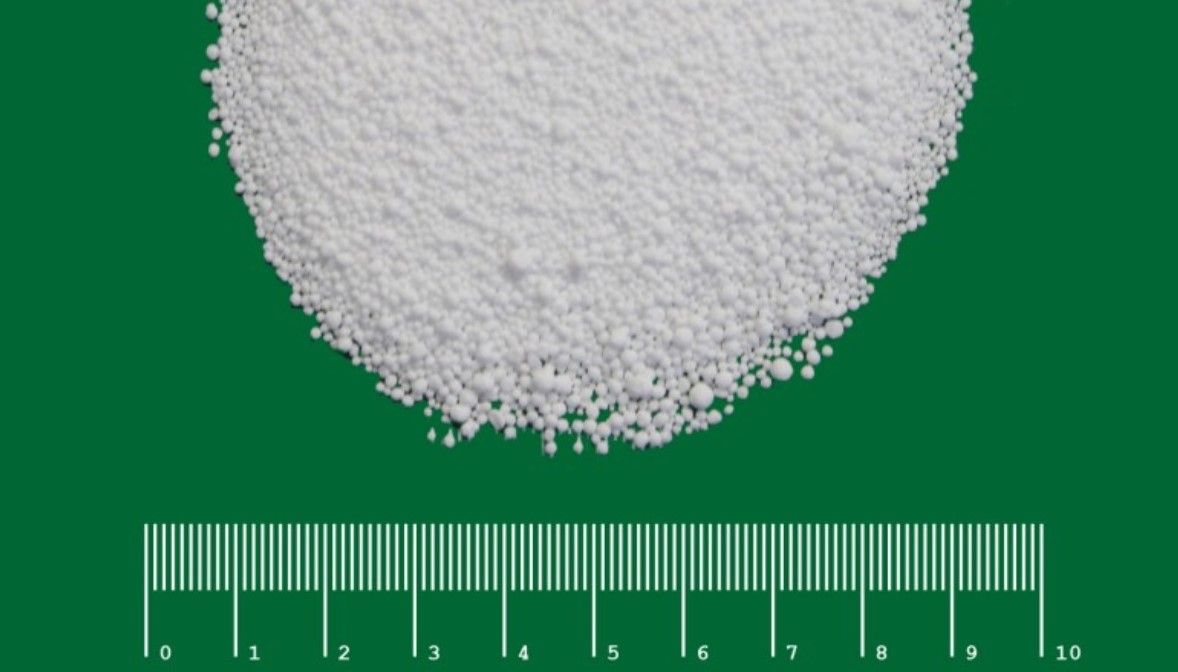
Most glass contains sodium to lower the melting temperature of the silica.
Using potassium carbonate to strengthen glass happens only once the glass has cooled a little and is in a solid state.
“By submerging a piece of glass in a potassium salt [such as potassium carbonate], some of the potassium atoms will take the place of the sodium atoms in the glass through the natural process of diffusion,” explains Ben Krasnow, Sr. Staff Hardware Engineer at Verily (Google Life Sciences). “As the larger potassium atoms are shoved into the spaces where the smaller sodium atoms used to be, it creates an effect which is basically putting the glass in compression by having the larger atoms inside it.”
The glass manufacturers then allow the glass to cool still further. This stops the process and prevents the potassium atoms from penetrating beyond the outer layer. As the larger potassium atoms compress the glass together, they form a compressive stress layer which is a sturdy, impact resistant surface.
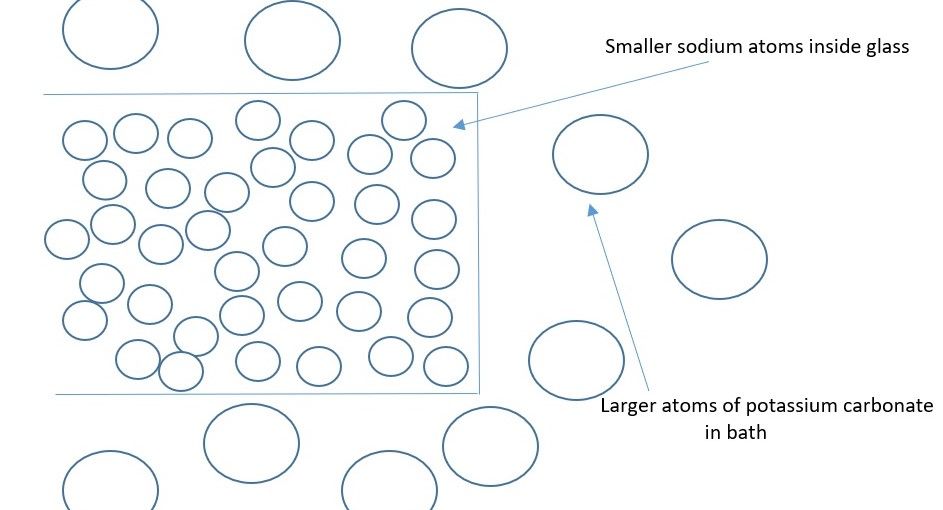
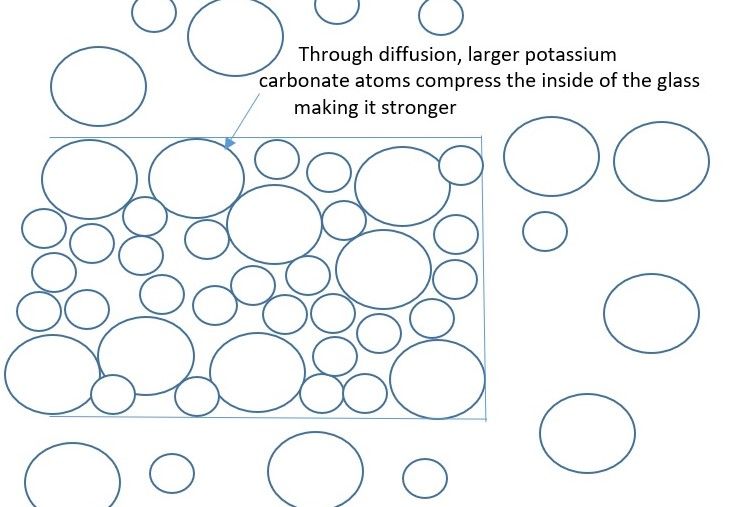
One analogy is to imagine a bag of oranges which have just enough room in the bag to jostle and move around. If the oranges were replaced with grapefruit, then the bag would be so full it would become rigid and strong.
It is the process used to make the trade marked Gorilla glass for high end smart phones.
However, more than just making glass stronger, potassium carbonate is also useful for making other specialist types of glass, such as potash glass, borosilicate glass, optical glass for telescopes and microscopes, as well as lead crystal.
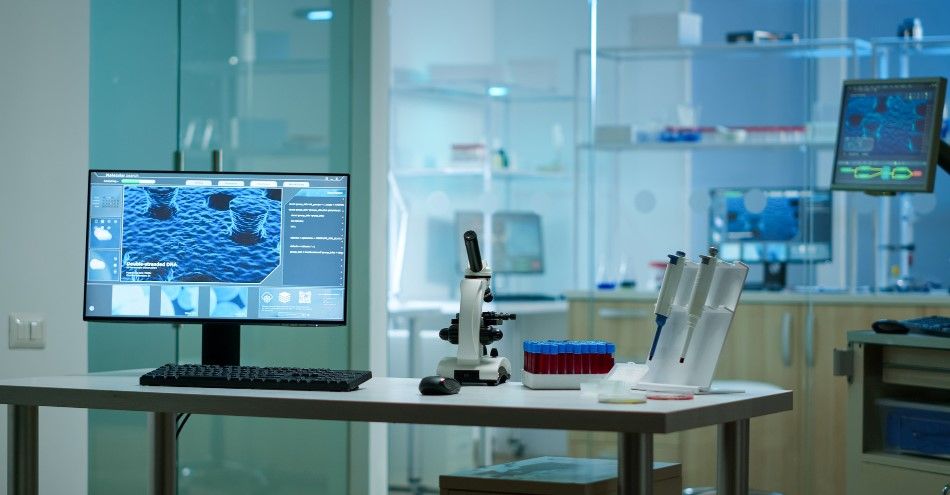
Glass production is a science that dates back to as early as 3,500 BC, and while the most basic forms include a general mix of sodium silicate, calcium silicate, and silica, there are a thousand different approaches and raw materials that can be used.
Thanks to potassium carbonate, many of these recipes and manufacturing processes make glass that is clear enough, strong enough, and with enough heat resistance for use in the modern world.
Photo credit: Wikipedia, Freepik, freeimages, Martin Kozon on Unsplash, & AG CHEMI GROUP