The coronavirus pandemic has changed people’s perspectives on many aspects. An appreciation of quality time with family, an increased love of the outdoors and nature, greater pleasure in spending time with friends. Even just going to a restaurant now seems like a luxury.
But what impact will it have on industry’s perception of raw material sourcing?
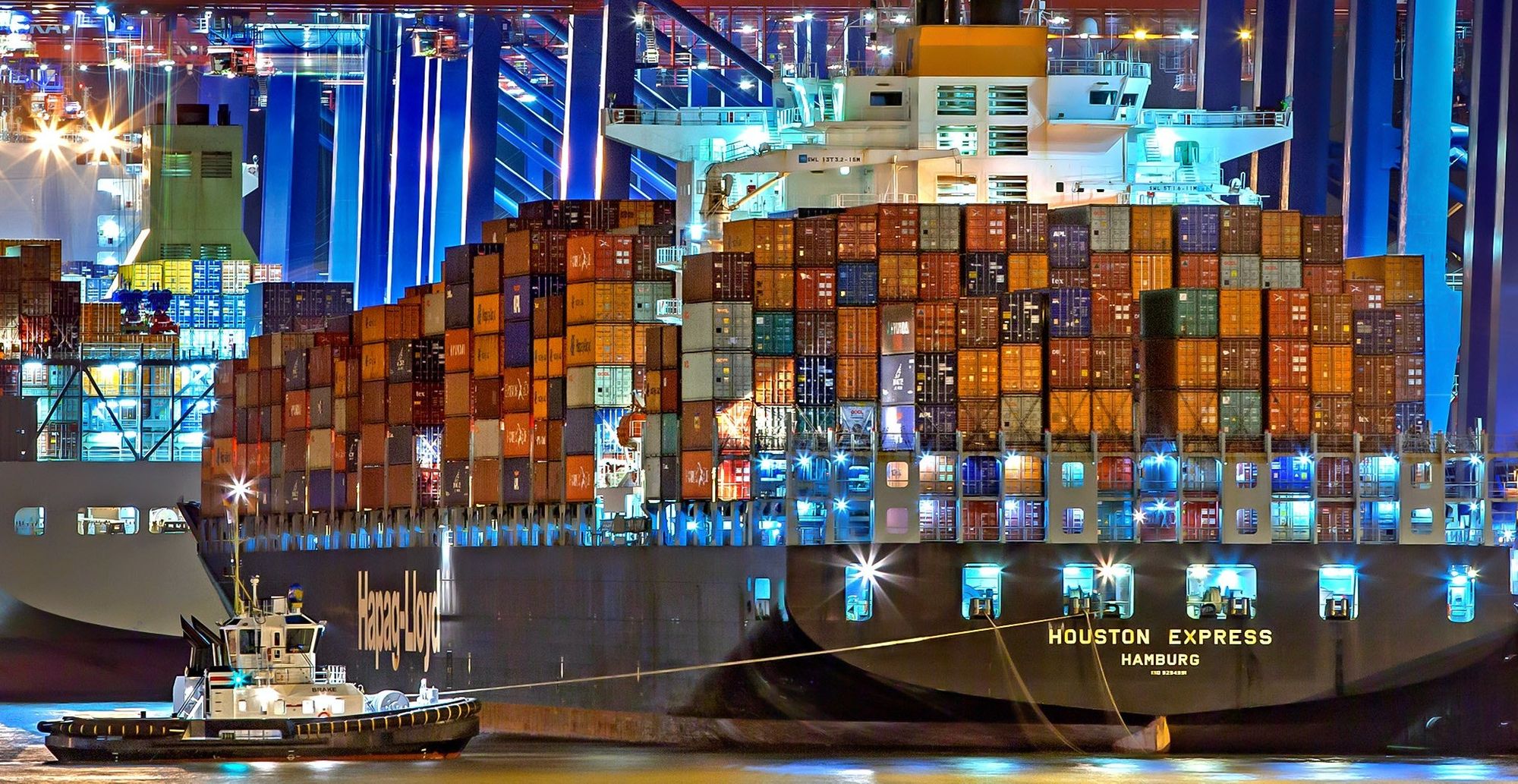
With the coronavirus exposing weak supply chains, will manufacturers relocate their facilities and suppliers?
For example, Paul Sturgeon, the CEO of the plastic industry’s executive recruitment agency KLA, writes in the industry journal, Plastics Today, that he was “… shocked when the COVID-19 situation revealed the extent of U.S. dependence on certain foreign countries, like China.” Noting that, “Ninety-seven percent of plastic artificial flowers come into the United States each year from China.”
While it has long been known that China is the workshop of the world for the 21st century, it has taken a global event the size of the current pandemic to open business leaders’ eyes to the fragility of their supply chains.
Supplies of plastic flowers may be an exceptionally low priority, but if one single country becomes the source for almost all antibiotics, anti-viral drugs, disinfectants, rare earth elements, or any other essential raw material, then glitches in the system can become insurmountable problems.
To discover how the pandemic is changing the way the raw materials used for making medicines and active pharmaceutical ingredients, read: Coronavirus Challenges Pharmaceutical Industry Supply Chain.
Procuring raw materials and finished goods from the Far East may be cheaper, but its distance from Western markets, geopolitical manoeuvres, trade wars, potential conflict in the South China Sea, tariffs, and now the virus with its associated restrictions on movement and production lockdowns has started business leaders thinking.
For example, in an interview with Plastics Today, Tom Star, President of Molded Devices Inc., said: “Many of our industrial customers are contemplating changes to their supply chains, as well as several large medical device companies. For strategic reasons, those companies may not want their names out there right now.”
An opinion supported by Ketan Deshpande, General Manager with custom moulder Pioneer Plastics Inc. whose order book was also being bolstered by customers looking away from Asian suppliers.
“Most of our manufacturing is already done in Los Angeles,” says Ervin Issagholian, President of Thermoformer EPI Packaging, “but our goal is to reposition everything from China to a different country.”
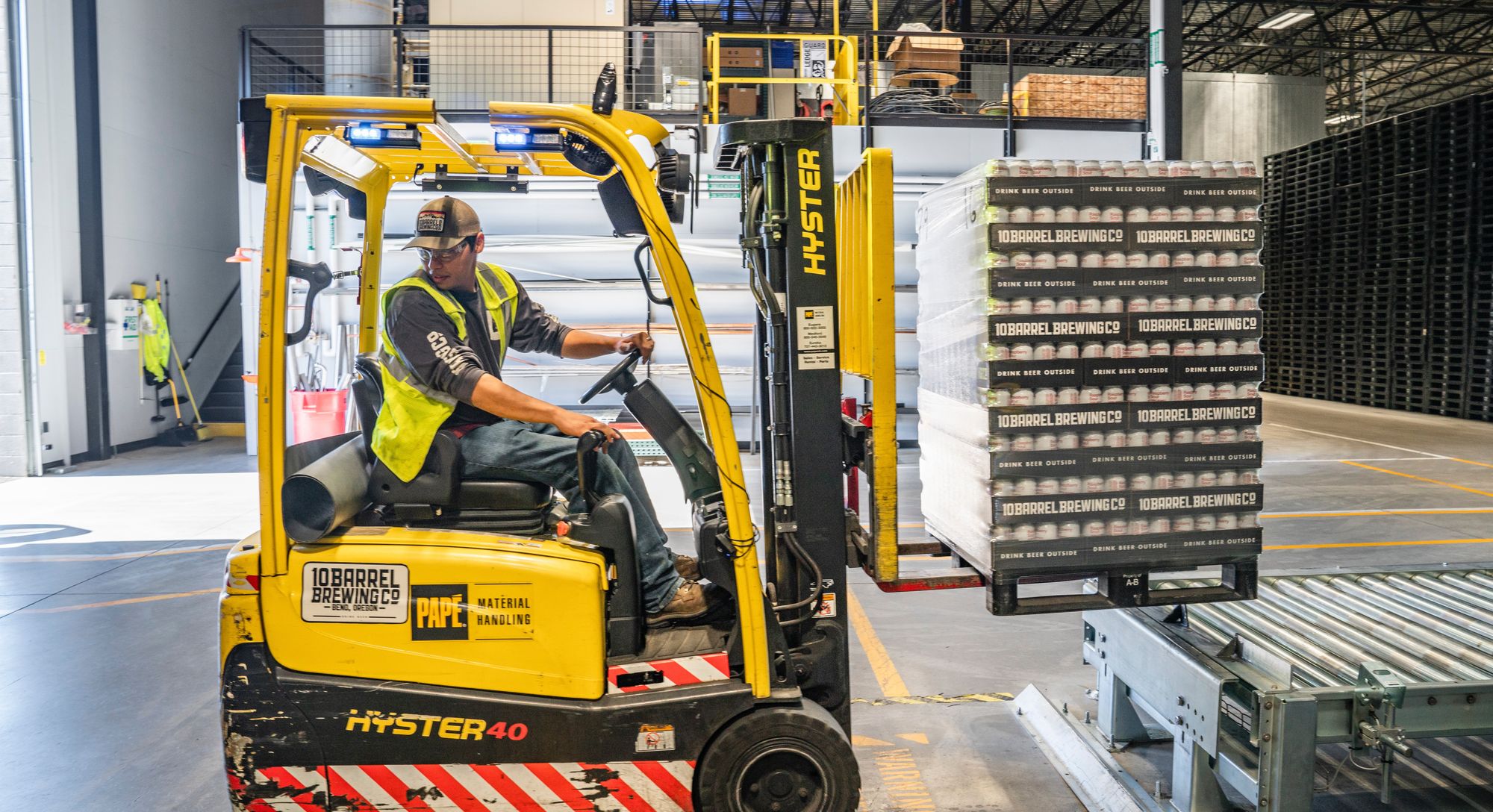
Although not everyone agrees that these exceptional circumstances will create a sea change.
In an interview with the chemical industry journal CE&N, James Bruno, president of the consulting firm Chemical and Pharmaceutical Solutions, said, “I don’t expect manufacturing to move back to the United States.” Instead he believes that costs, taxes, and regulatory considerations will continue to dominate sourcing decisions. Strategically it may make sense for production of some vital raw materials to be kept inside domestic markets, but otherwise economics will remain key.
However, relocating production or raw material sourcing closer to home does have clear business benefits.
As Jon Hubers, Sales and Operations Manager at custom extruder Crescent Plastics, notes, “Reshoring can solve the problems of long lead times associated with shipping product overseas, issues with quality, political instability, communication, and most recently, countrywide industry shutdowns.”
Whether material pricing or supply chain security will prove more important in future sourcing decisions remains to be seen. Certainly, any wholesale changes that do take place will not happen suddenly. The drift of manufacturing overseas took several decades to take place, so its full return will likely take as long.
Even in the short term, the time it takes to relocate, establish new production facilities (especially in the middle of an expected global recession), or the simple act of waiting for contracts to expire means that Western companies will not be changing tack overnight.
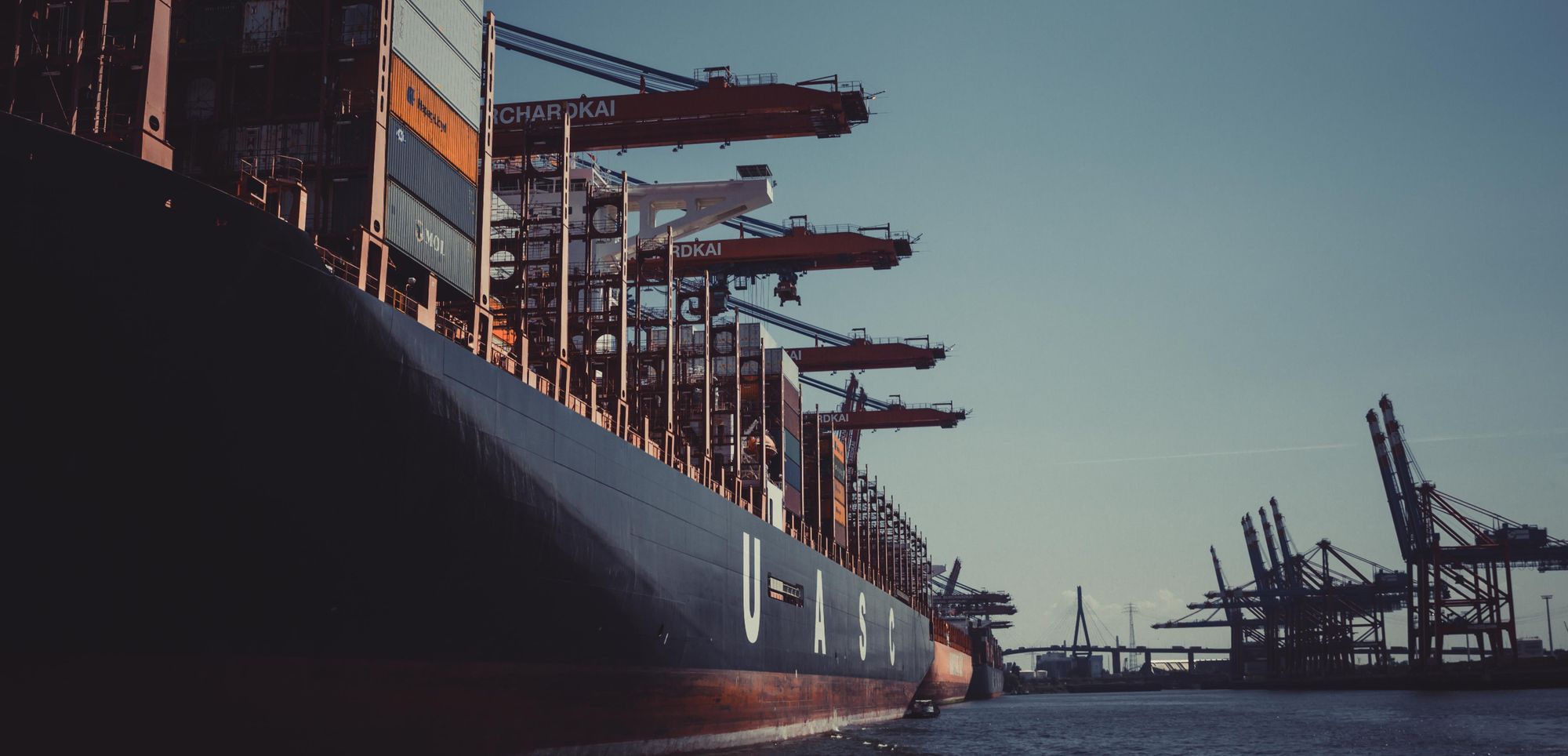
However, some global events do revolutionise everything; and maybe the coronavirus pandemic is one of them. A shock to the world so deep that it has jolted supply chains into such a stutter that it will lead procurement officers into rethinking the way they source materials.
Epidemiologists talk of coronavirus having a second and third wave as it repasses through populations. But maybe the virus will also bring about a flow of manufacturers moving closer to markets.
Maybe COVID-19 will bring on a wave of reshoring?
Photo credit: Julius Silver from Pexels, Sascha Hormel from Pexels, ELEVATE from Pexels, & Tom Fisk from Pexels