In the early years of using nanotechnology, manufacturers had huge problems ensuring the smooth and constant dispersion of nanomaterials throughout a substance.
For example, a paint producer may add nanoparticles to the coating mixes to increase strength (so that the paint is more scratch resistant), improve durability (so that the colour does not fade), and to boost flexibility (so that the paint can expand and contract when with the weather, and so prevent flaking). To achieve these properties, it is important that the particles are evenly spread through the mix.
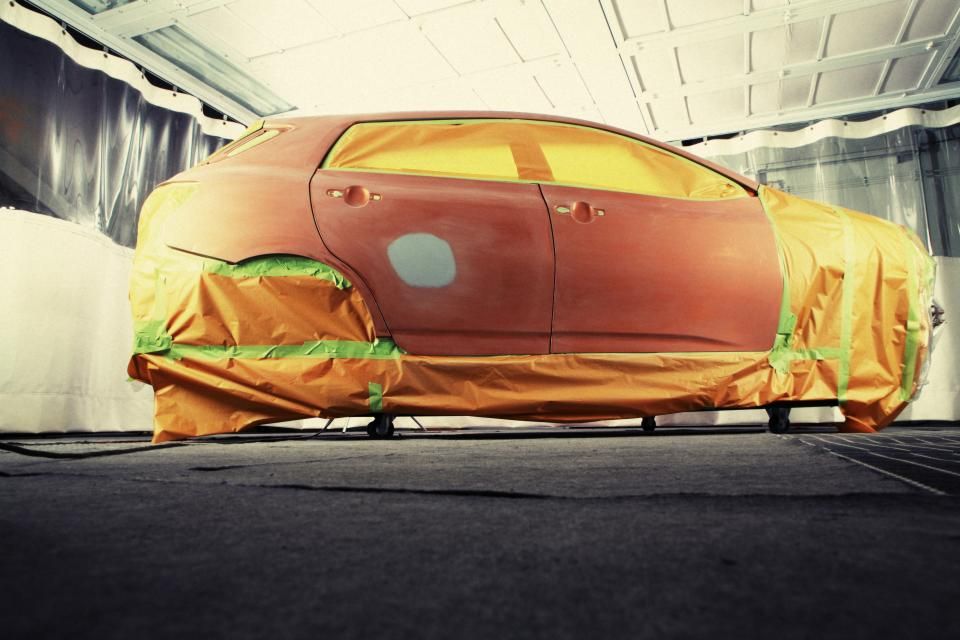
Until recently, ensuring that there were sufficient nanoparticles throughout a substance meant adding ‘more than enough’ into the mix. While usually effective, this approach was expensive and sometimes limited the nanoproduct's abilities.
Since those days, major breakthroughs have been made that not only ensure the nanoproducts are spread evenly through the core of the product, but if desired, can keep the nanoparticles evenly distributed at the surface of a material where their effects are often needed.
For example, the Prague-based company AG CHEMI GROUP has cooperated with nanotechnology specialists to improve the distribution of granular polymer nanomaterials.
As Lev Lyapeikov, the product development manager at AG CHEMI GROUP, explains, “This patented technology is a procedure similar to the procedure for bulk nanostructuring of materials, but instead of a complete melting of the polymer, only the surface treatment of polymer granules with a layer of nanoparticles are treated. This technology makes it possible to obtain high-quality dispersion and distribution of nanoparticles on the polymer surface, thus reducing the consumption of expensive nanomaterials and increasing the efficiency and functionality of nanomaterials in modified materials.”
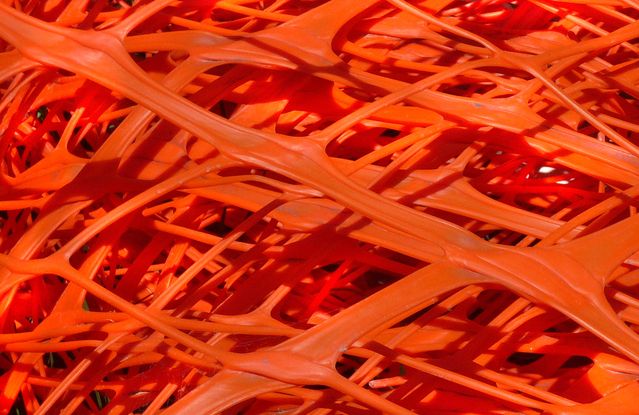
One area where this technology is being applied is in the distribution of nanomaterial additives which provide active biocidal and virucidal properties. By allowing to remain at the surface of a substance, cost savings are made as the nanomaterials that kill pathogens on contact are only required on the surface of a material.
Another example of how nanomaterials are no longer required throughout a material was recently discovered at Nagoya University in Japan.
Here nanotechnology researchers discovered that, “Azobenzene-containing film, important for many industries, does not need to be made entirely of light-sensitive material to function.”
As the university press release explains, “Azobenzene-containing plastic film is a peculiar material; its surface can change shape when exposed to light, making it a valuable component in modern technologies/devices like TV screens and solar cells. Scientists now show that only a thin, topmost layer of the light-dependent azobenzene-containing plastic film needs to be light-sensitive, rather than the entire film, opening up new ways to potentially reduce production costs and revolutionize its use.”
The team have now published their findings in the journal Nature, which succinctly describes the breakthrough as, “The presence of only a molecular level skin layer at the free surface is sufficient to promote or terminate a large-scale surface deformation.”
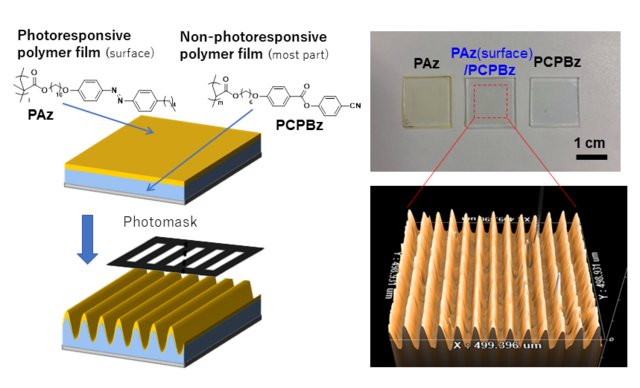
“Many optical devices like photocopiers, printers, and monitors depend on the light-based surface change in azobenzene polymer film,” notes Dr Takahiro Seki, the study’s lead author. “Based on our findings, azobenzene film can also act as an ‘actuator’ (that part in a device that moves other parts) in nanomachinery. We are only at the cusp of developing this discovery onto an industrial scale, but you can imagine how needing only a very small amount of light-sensitive material can reduce costs.”
The discovery will not only lead to thinner and more energy efficient screens, but in the future may also help pave the way to more flexible screens and wearable technology.
While nanotechnology researchers are glad that the problem of nanomaterial distribution has been solved, industrialists are being drawn to the cost savings that can be made and in finding out how less nanomaterial can now achieve so much more.
Photo credit: Scientific Reports, Stocksnap, Jenny Rollo from FreeImages, & andrea jaccarino from FreeImages