To the naked eye microspheres look like an ineffective white or grey powder. Yet for something so small, microspheres are an incredibly useful, powerful, recycled, and versatile raw material.
In fact, the industry journal Industrie & Technologies, notes that, “Because of their low density, small size, spherical shape, mechanical strength, high melting temperature, chemical inertia, insulating properties and low porosity, microspheres find a wide range of applications in industry.”
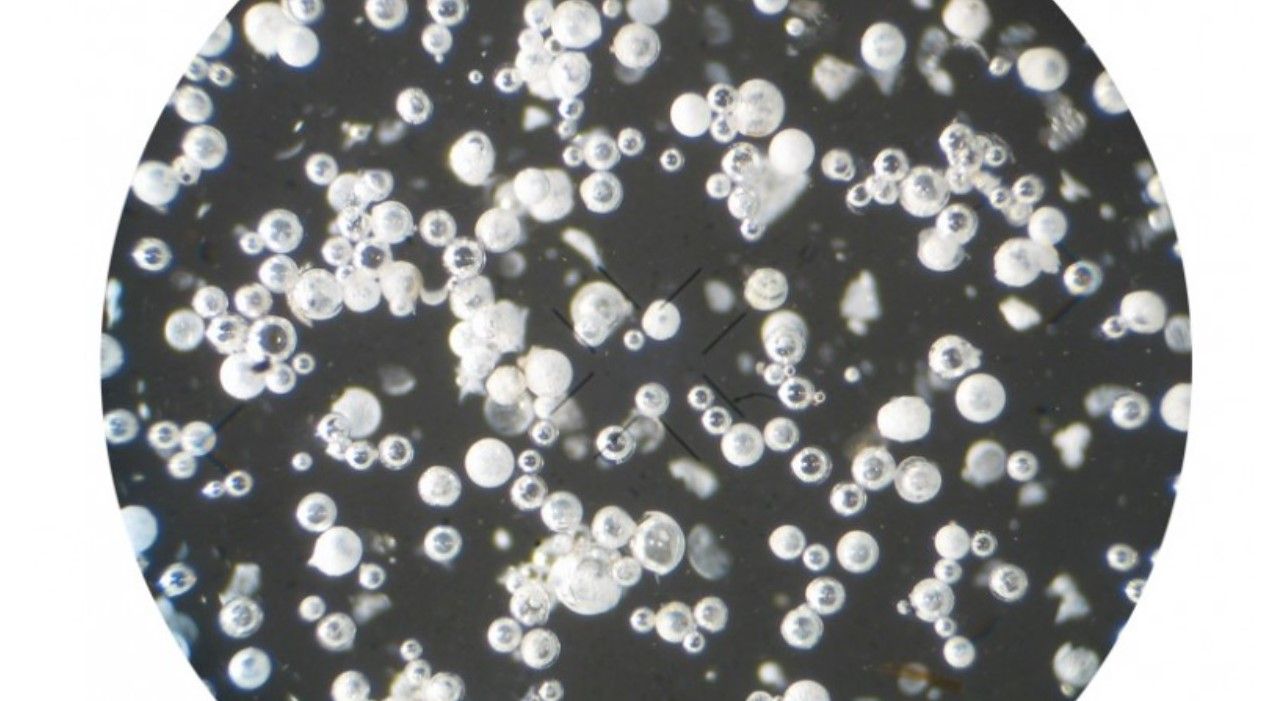
What are Microspheres?
Microspheres are spherical microparticles that have been extracted from the fly ash waste of coal-fired power stations.
They are sometimes called cenospheres, have a high content of silica (SiO2) and aluminum oxide (Al2O3), and measure less than 1 mm in diameter.
This gives them multiple uses, “In particular, for reinforcing materials or imparting properties of resistance to corrosion, or thermal and sound insulation to coatings or paints. They can be described as multifunctional fillers and integrate well in resins and binders such as thermoplastics and thermosetting.”
Here are just a few of their many applications:
Microspheres for use in paints and coatings
Microspheres are used in the coating industry to add volume and density to a paint. The tiny beads also shrink when they dry out, tightening the coating into a stronger defensive barrier.
Their excellent resistance to heat can also improve a coating’s thermal conductivity. While BAE Systems is even attempting to use microspheres in coatings to reduce reflection in the infrared spectrum, potentially enabling aircraft to have ‘invisibility cloaks.’
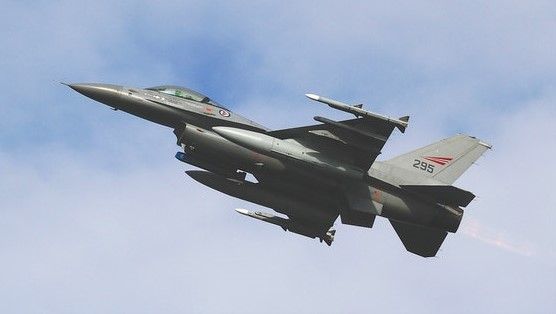
Microspheres in plastics and polymers
Microspheres’ re-formable shape and good mechanical strength helps to reduce shrinkage when used as a raw material in thermoplastics.
Additionally, due to their excellent low-weight to strength ratio, they are widely used to make composites for the automobile industry. For example, microspheres were used in the manufacture of the . As Plastics News reports, “… microspheres have replaced the traditional calcium carbonate filler in a sheet moulding compound. Doing so has reduced the weight of a typical sports car by nine kilos.”
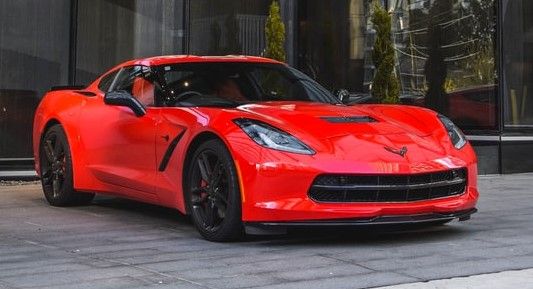
Furthermore, the use of microspheres does not make the car more expensive. As Probir Guha, Vice President of Continental Structural Plastics Inc. (the compound’s manufacturer) explains, “This new SMC [sheet moulding compound] is cost competitive with aluminium.” Adding that, “tooling costs are [also] low. For a production run of fewer than 150,000 vehicles, such composites can lower tooling costs by as much as 50 to 70 percent versus steel or aluminum.”
Microspheres in concrete
Microspheres’ high silica content makes them a suitably strong filler for concrete.
Their low density helps reduce weight to make a practical substitute for conventional raw materials. According to Jeff Girard, President of The Concrete Countertop Institute, “1 pound of microspheres takes up the same absolute volume as about 3.8 lbs. of sand.”
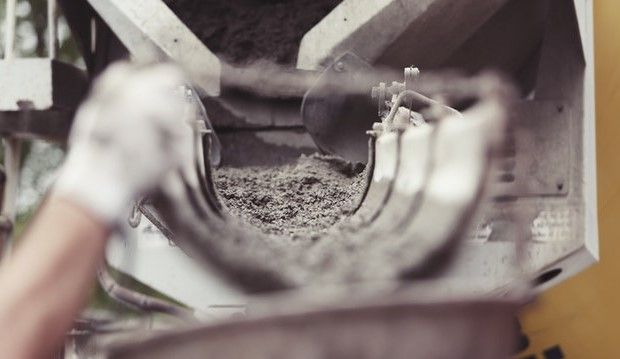
Their hollow interior also aids the insulation and deadening of sound. One study found that microspheres applied in concrete reduced traffic noise on a bridge. Specifically stating that, “Experimental results showed that a 40% volume fraction addition of cenospheres to a cement matrix increased the Noise Reduction Coefficient by 100%.”
Microspheres can also improve thermal insulation in plasters and mortars used in the construction of walls, floors, and ceilings.
Microspheres for use in syntactic foams
Specialized solids made of ceramic, metal, polymer, or resin, can be filled with microspheres to form a syntactic foam.
The addition of the microspheres increases strength, buoyancy, sound proofing, radar transparency, and thermal protection. These properties make microspheres a practical raw material in the manufacture of ship and aircraft components, buoys (especially more resilient deep-sea markers, blast mitigating materials, sports paraphernalia, and other equipment and engineering parts which may benefit from low-weight, good strength, and high-resistance to extreme conditions.
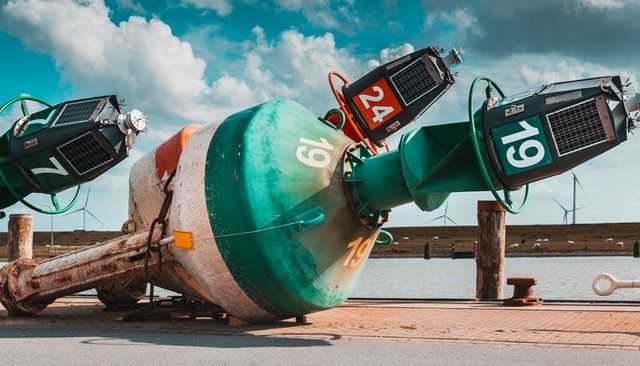
Other uses for microspheres
Microspheres are also widely used in the oil and gas extraction industry as a raw material which can reduce the density of a petroleum cement paste without increasing water content.
They can also be coated with pharmaceutical chemicals and so function as a drug delivery ingredient for numerous medicines. Or even coated with silver-oxide and applied to wound dressings to reduce the risk of infection.
This brief analysis of the applications of microspheres is far from exhaustive. As long as engineers require strong, yet light-weight, fillers, with good thermal and sound insulating properties then there will be a need for microspheres.
Beit in a coating, a foam, a polymer, a pharmaceutical, a bandage, or even in concrete, microspheres are a raw material with purpose.
Interested in sourcing good quality microspheres from a reliable and trusted supplier of raw materials?
AG CHEMI GROUP (who host this website) have been supplying microspheres to industry for many years and have been trading industrial ingredients to manufacturers since 1994.
For more information about microspheres, product specifications, delivery terms, and pricing, please visit AG CHEMI GROUPor call +420 233 371 850 or contact info@agchemigroup.eu
Photo credit: Nicolas Savignat on Unsplash, Matthis from Pexels, Life Of Pix from Pexels, Inge Wallumrød from Pexels, 愚木混株Cdd20 from Pixabay, & AG CHEMI GROUP