Love it or loathe it, plastic is a highly practical material. It is strong, flexible when needed, lightweight, transparent or opaque, and relatively cheap. For these reasons it is used in a million different products; from window frames, to forks, from furniture, to fabrics, plastic is the material of our time.
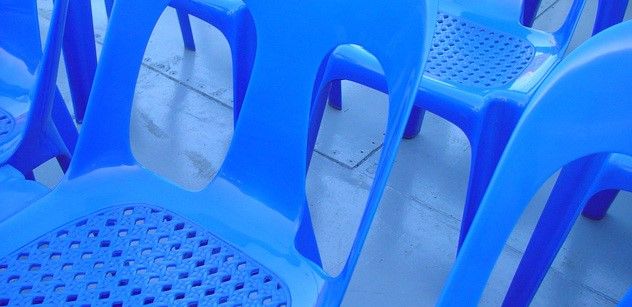
But while the industry works hard to resolve its environmental impact, boosting recycling rates and lowering fossil fuel consumption, plastics producers are also working hard to improve plastic performance.
One of the leading ways to do this is through nanotechnology.
By altering the structure of polymer substances at the nanoscale (modifying particles about the size of a single virus), polymers can be given new properties, such as added strength, crack resistance, thermal integrity, or electroconductivity.
Given that plastic already has so many uses, improving its performance and range of properties even further is certain to find new applications and open new markets for plastic producers.
One of the earliest parts of the plastic industry to embrace using nanocomposites was the food packaging sector, as nanotechnology researchers found that plastics could be modified or have nanoparticles added to them which provided antibacterial properties. Nanoadditives or nanostructuring of polymers soon became an economically viable solution for keeping food fresh for longer.
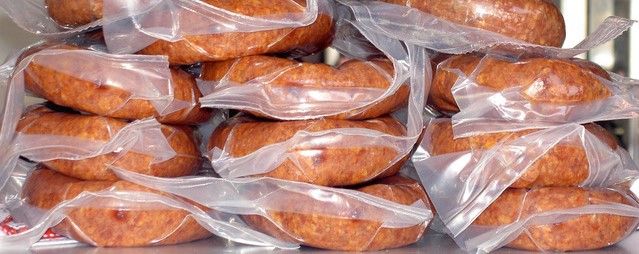
Since those early days, the range of properties and the type of plastic available for nanoindustry modification has grown considerably.
The manufacturing journal MultiBriefsexplains how originally, nanocomposites focused on nylon and polypropylene base polymers, but as the industry continues to mature and research funds grow, nanoproducts can now be made from a broad range of resins. These include: “… epoxy, polyurethane, polyetherimide, polybenzoxazine, polystyrene, polycarbonate, polymethyl methacrylate, polycaprolactone, polyacrylontrile, polyvinyl pyrrolidone, polyethylene glycol, polyvinylidene fluoride, polybutadiene, copolymers and liquid crystalline polymers.”
The report continues to speculate that improvements in nanocomposites, particularly in boosting tensile strength and heat distortion temperature limits, could push the boundaries of thermoplastics engineering, possibly leading the plastics industry to, “… challenge metal and glass applications in many new areas.”
For example, in the field of medicine, most medical instruments are made of metal, yet nanotechnology developments into the polymer sector may provide a range of nanomaterials with superior properties to commonly used stainless steel or silver.
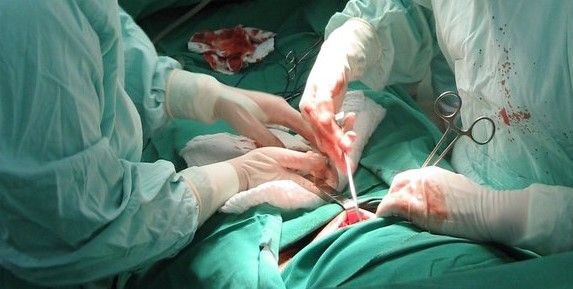
Nanomaterials can provide minimally invasive devices with smooth services and extremely thin walls. They can also provide robust, yet flexible substances for medical implants, prosthetics, and nanoscale sensors (minute polymer implants which are electrically conductive and so able to report on a patient’s internal health).
In the automobile industry, electroconductive nanopolymers have become a common raw material in more than 70% of American-made cars. While previously made of steel, automobile fuel delivery lines often use a polymer containing carbon nanotubes which prevent the accumulation of static electricity.
Nanopolymers are also playing an ever-larger role as a raw material in electronics, such as thin-film capacitors, micro-optical switches, solid polymer electrolytes for batteries, as well as nanoscale smart switches and sensors.
They are being used in paints and coatings for corrosion protection, in body armour, in aerospace and military hardware, as well as improved optical devices and solar panels.
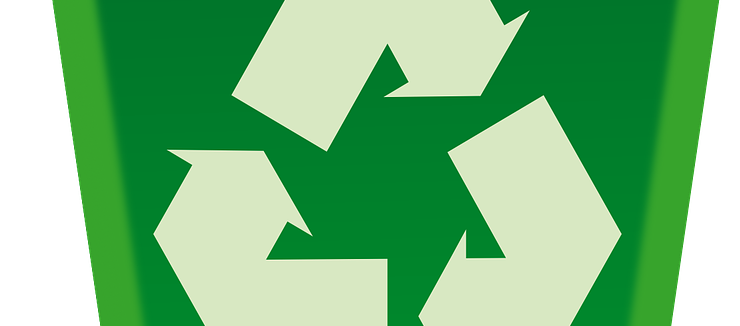
Given the plastics industry’s poor environmental record, it is also worth noting the role nanotechnology can play in boosting a polymer’s recyclability.
Whereas today, most plastics degrade when recycling as the polymer chains are corrupted in the recycling process, the latest nanotechnology allows for plastics to be given new qualities.
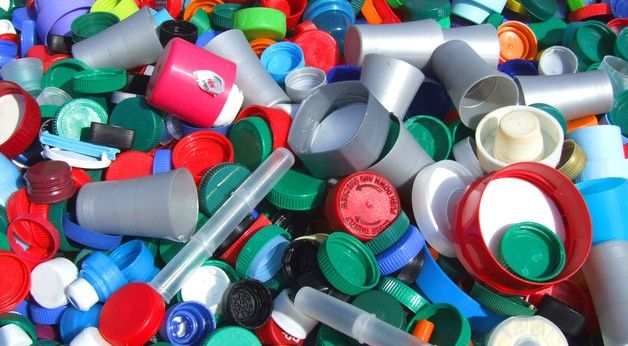
“Nanostructure technology allows 100% modification of secondary raw materials both in order to maintain the conventional properties of materials at the required level (for example, impact strength) and in order to obtain new material properties (for example, obtaining thermally or electrically conductive plastics).” says Lev Lyapeikov, the product development manager at AG CHEMI GROUP.
“The use of nanomaterials with a particle size in the nanometer range requires thorough preparation of the nanoadditive and pure polymer, as well as the use of special technology of two-phase modification, developed and tested by our company.” Adding that, “Examples of the use of this technology can be found in our product portfolio and in our projects in the development and commercialization phase.”
As Dr. Donald V. Rosato, author of Vols. 1 & 2 of the Plastics Technology Handbook, notes, “… the nanocomposites future is now.”
To find out more about AG CHEMI GROUP’s nanoproduct and nanoprocess portfolio and the company’s plans for expansion then visit: AG CHEMI GROUP
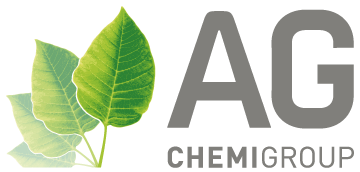
Photo credit: Ilja Wanka from FreeImages, Pexels, Dean Simone from Pixabay, Karin Muller from FreeImages, Chris Richardson from FreeImages, Clker-Free-Vector-Images from Pixabay, & Fernando AUDIBERT from FreeImages