It is common knowledge in the chemical industry that the future of sourcing chemical raw materials lies in sustainability. Knowing how to recycle waste efficiently and move the chemical industry into the circular economy is a key part of solving climate change.
However, turning that dream into a reality is incredibly difficult.
“Anyone who has ever hesitated in front of a trash bin knows the problem: It’s hard to determine what can be recycled,” says Kathryn O'Neill of MIT’s Energy Initiative. “Consider the average potato chip bag. It’s got film plastic, metal, dyes, and food residue; it’s complicated. Today’s recycling doesn’t handle complexity well, so the typical chip bag is destined for the landfill.”
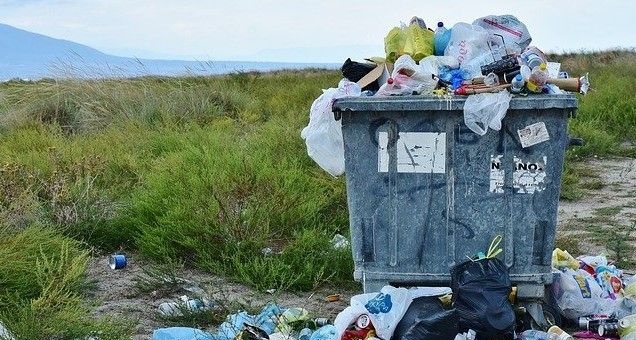
While burying waste hides the problem, the pressing issue for today is that as it decomposes it emits greenhouse gases, mostly methane - a gas that is even worse for climate change than carbon dioxide.
Plasma Gasification
Knowing this led one of the MIT Energy Initiative’s researchers, Daniel Cohn, to look into solving the problem using plasma gasification. It is a process that heats waste (including biological, hazardous, and even radioactive waste) to a very high temperature and then captures the gaseous elements and molecules produced for reuse in industry.
“Unlike incineration, which releases contaminants into the air,” explains the MIT website, “[the new] process traps hazardous elements in molten glass while producing a useful feedstock fuel called synthesis gas, or ‘syngas,’ which can be transformed into such fuels as ethanol, methanol, and hydrogen.”
It is a solution that was inspired by the need to stop burying waste.
“About 130 million tons of waste per year go into landfills in the U.S.,” notes Cohn, “and that produces at least 130 million tons of CO2-equivalent emissions.”
Yet beyond this ecological goal, was the importance of making the process financially viable. A blueprint on how waste can be profitable for future businesses.
It is a plan that led to Cohn founding the company Integrated Environmental Technologies.
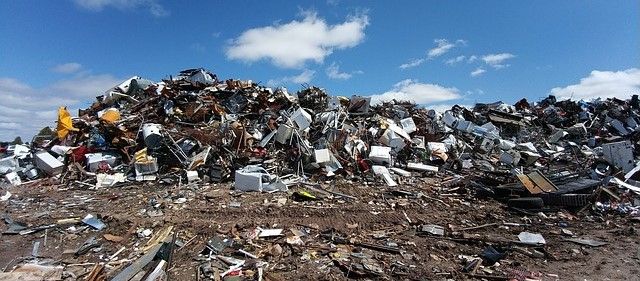
A Business Model for Recycling Waste into Chemicals
Originally, the business model was largely based on solving industrial and highly toxic waste for heavy industry, however Cohn soon saw the benefits to the environment and the company’s bottom line of solving the problem of everyday waste.
Teaming up with Jeffrey Surma, who at the time was studying how to clean up nuclear waste, they applied for a US government grant to build an experimental waste treatment furnace facility at MIT using plasma - a superheated, highly ionized gas.
The success of that research led the pair to combine the plasma furnace with a joule-heating melter. It was a device that could trap hazardous waste in molten glass.
“When waste material enters that zone, it breaks down into its elements,” says Surma. “It’s an extremely clean process, [as it] allows waste to come into a chamber and be exposed to extreme temperatures — a controlled bolt of lightning of over 10,000 degrees Celsius.”
After a great deal of experimentation, the team built its first commercial recycling plant in 2008 under the shortened company name of InEnTec.
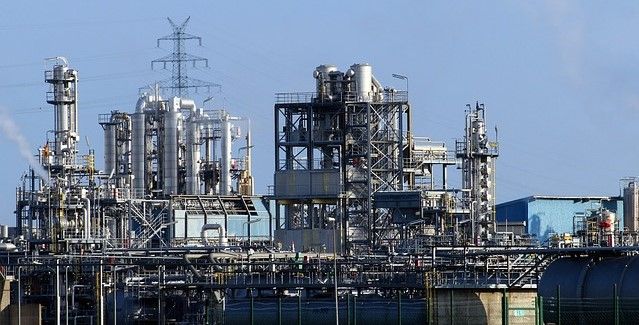
Fuel Cell-Grade Hydrogen from Garbage
The first units were very small, and even today InEnTec’s waste processors can handle only about 25 to 150 tons of waste per day. But this was never a problem for the company, as their small size means that the waste recyclers take up less than two acres of land and can fit snuggly into the communities which they serve. Converting household waste into useful hydrogen without any other direct emissions.
“You’re reducing the distance waste has to travel and converting it into a virtually zero-carbon fuel,” says Surma.
“Hydrogen is a key product focus for InEnTec,” notes the MIT report, as 99% of hydrogen sourced by industry is currently made from fossil fuels.
If the use of electric cars takes off in America as predicted, then this could be game-changing for the company, as it, “hopes to produce inexpensive, fuel cell–grade hydrogen at sites across the country.” Each ready to refill the hydrogen fuel cells powering electric vehicles.
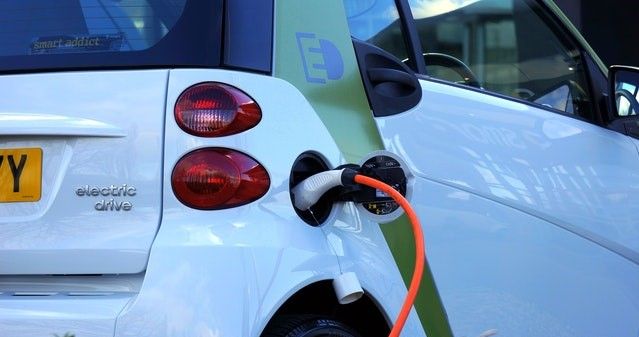
“We can generate hydrogen at very low cost, which is what’s needed to compete with gasoline,” explains Surma. “We see this as an enormous opportunity.”
Molecular Recycling
However, it is perhaps the process’s application in recycling plastic which is experiencing the largest growth.
The problem for the plastics industry is that all the different grades of plastic have different chemical compositions, so recycling it is not simply a case of melting it all down to make new plastic.
Instead, waste plastic must be separated, especially items that are glued or bolted together. This is expensive and time consuming and means that less than 10% of America’s plastic waste is currently recycled.
But with InEnTec’s approach, the different types of plastic do not need sorting, as everything is reduced to a virgin state. Only then does separation of raw materials occur, at a level where they can easily be reused. It is a process called ‘plastic circularity’, as it makes new plastics from old plastics.
“We’ve partnered with chemical companies pursuing plastic circularity, because our technology allows us to get back to molecules, the virgin form of plastics,” says Surma.
This has allowed the company to team up with mechanical recycling companies, such as a major car-shredding company to process its plastic waste.
“We can recycle the materials back into molecules that can be feedstock for new dashboards, seats, etc.,” notes Surma. Given that modern cars are made up of 40 to 45% plastic, there is plenty of work and business for the company in this sector.
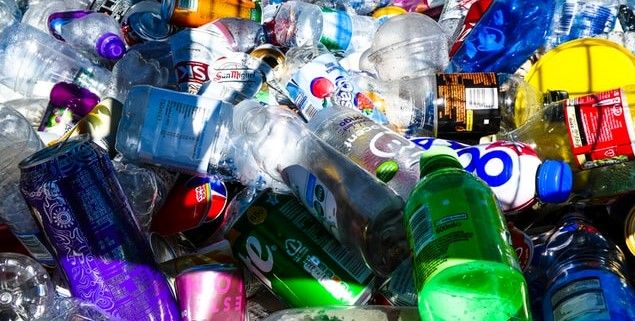
“We think this will be a very significant part of our business going forward,” he adds.
Other initiatives by the company, such as a boat that collects and recycles ocean plastic, requires subsidies, but does show how versatile, mobile, and small the process can be. It also maintains the company goal of diverting waste away from landfill and recycling it into raw materials.
“We initially put a lot of effort into medical and hazardous waste because we got more money for disposing of those,” recalls Cohn.
But today, the dream is less about making huge profits and more about developing a business based on a healthier planet and more sustainable production. Showing that there is a way to avoid burying waste by turning it into something useful. A market for recycled chemical feedstock.
“It’s taken a long time to get to this point,” says Cohn. “[But] we’re just arriving now at the point of getting more customers who believe that an environmentally superior product has more value.”
Photo credit: RitaE from Pixabay, vkingxl, Nick Fewings on Unsplash, Mike from Pexels, Frauke Feind from Pixabay, & Pexels