According to the United Nations, plastic pollution will triple in 35 years. The biggest reason behind this impending environmental catastrophe is poor waste management and the fact that less than 10% of the world’s plastic waste is recycled.
The solution to this problem is getting value from plastic waste. The problem is that plastic is made to be strong and durable, so it takes a lot of effort to breakdown and recycle into something new.
“We make plastics to last from the perspective that many of them have to hold a liquid inside them that you don't want coming out of a bottle. So they have to be relatively strong materials,” says Virginia Tech's Head of Chemistry, Amanda Morris. “The bonds that hold the polymer together and give us that strength and give us the properties of the bottles that we use are also really hard to break, and so it's just trying to come up with ways to do it in an energy efficient manner where you get clean product.”
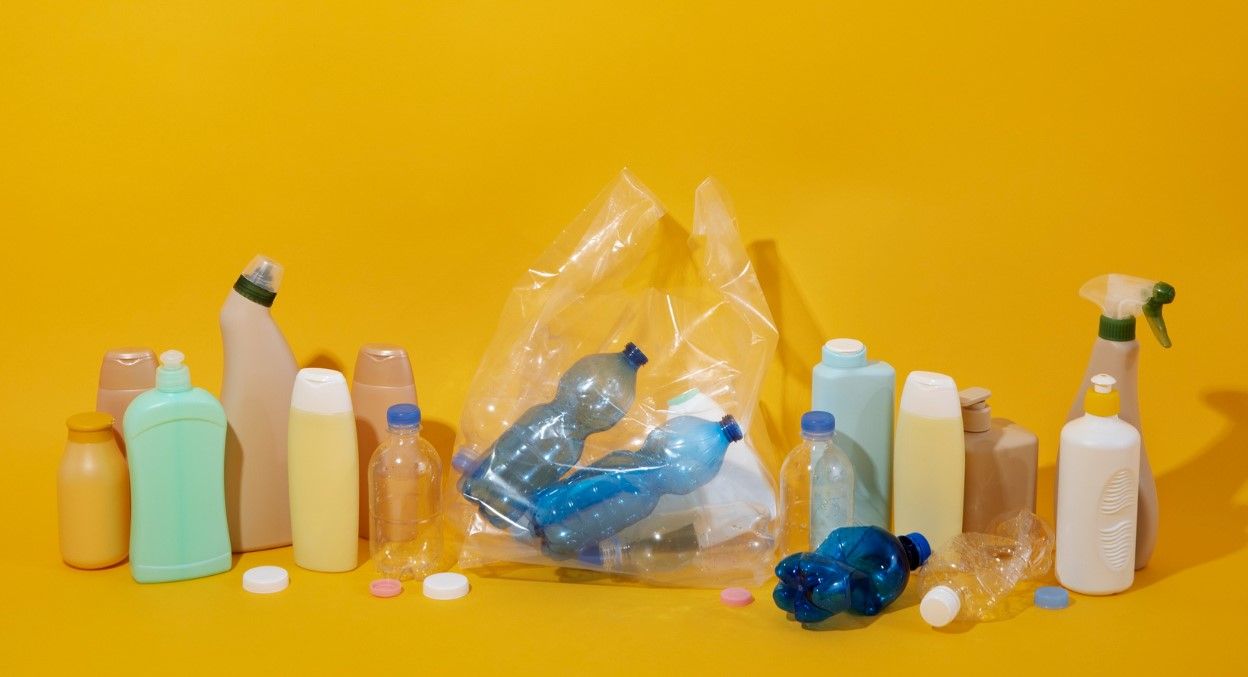
At its core, it was a problem that troubled Greg Liu, an undergraduate student at Zhejiang University in eastern China, when he saw the pollution that industry was creating.
“Pollution was everywhere; water, soil, road, you name it,” he recalls. “I didn't want to be in an environment like that, nor our future generations. That basically drove me to think, ‘OK, I must pursue an advanced degree to change the way we work in the chemical industry.’”
Through years of hard study, Liu was able to earn his doctoral degree from the University of Wisconsin-Madison, and now finds himself researching sustainable routes for polymer chemistry at Virginia Tech.
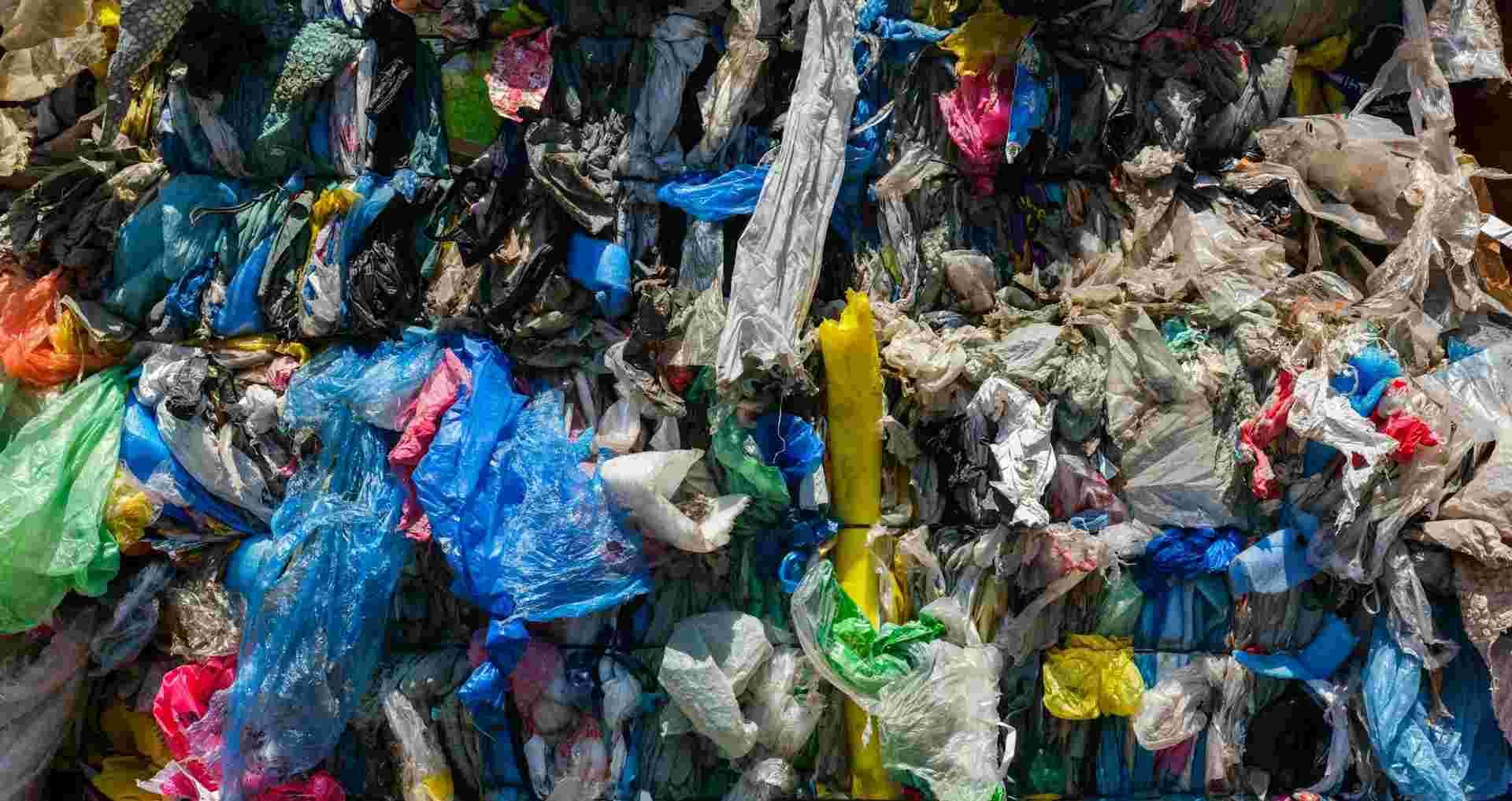
It was here that he and his colleagues made the breakthrough to convert plastic waste into soap and detergent. A discovery which has now been published in the journal Nature Sustainability where the details of “upcycling polyolefins to sulfate detergents” are discussed.
“Firewood is mostly made of polymers such as cellulose. The combustion of firewood breaks these polymers into short chains, and then into small gaseous molecules before full oxidation to carbon dioxide,” explains Liu. “If we similarly break down the synthetic polyethylene molecules but stop the process before they break all the way down to small gaseous molecules, then we should obtain short-chain, polyethylene-like molecules.”
Related articles: The Automotive Sector’s Latest Raw Material Trend: FRPCs or New Polymer Production Method for a More Pliant, Eco-Friendly PVC
To test this theory, Liu constructed a tiny reactor that resembled an oven so the team could use a technique known as temperature-gradient thermolysis to heat polyethylene.
“In simple terms,” the Virginia Tech press release explains, “Liu's system has two steps. It first involved using thermolysis, or breaking down a substance—in this case, plastic—by using heat. Plastic placed in a reactor built by Liu's team and heated to between 650 and 750 degrees Fahrenheit broke down into chemical compounds, leaving a mixture of oil, gas, and residual solids.”
Similar to clearing soot from a chimney, they collected the residue after the thermolysis and discovered that Liu’s theoretical chemistry was accurate: the plastic bag was made up of ‘short-chain polyethylene’ or, more specifically, waxes.
Breaking down the polypropylene and polyethylene molecules that comprise plastic within a specific carbon range was crucial to this initial phase.
The gas could be recovered and used as fuel and there were very few solids left behind; however, it was the oil that was of most interest to Liu and the other researchers.
Liu was then able to convert the molecules in the oil into soaps, detergents, lubricants, and other products.
“These materials are stable,” notes Liu. “This vial of soap [which he holds as he speaks] has been in my office for, I would say, a year already. … You could use it to wash your hands and dishes. We have used it to wash our lab glassware in the laboratory.”
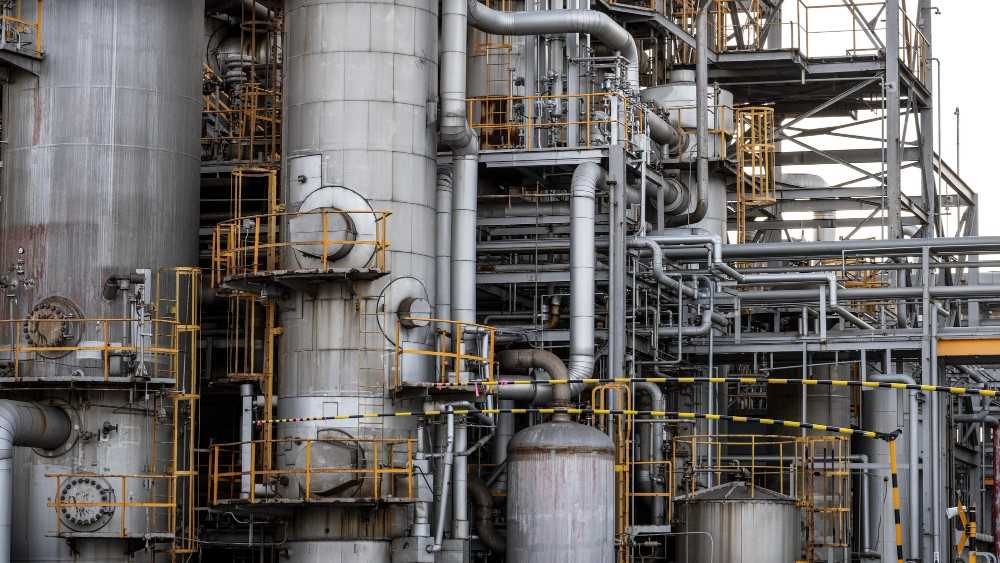
However, the difficult part has now begun: ensuring the process is scalable to an industrial level and making it a continuous process all while maintaining financial viability.
This is a common situation for chemical researchers, as they frequently come up with solutions to problems which are later found out to be prohibitively expensive or inefficient when conducted in bulk.
According to Liu, industry has shown interest in his process, but any investment provided is based only on the goal of profitability.
So, Liu is now in the business of finding the capital (he estimates hundreds of thousands of dollars) to build a test reactor in the lab or to create a start-up company to see if the process is scalable.
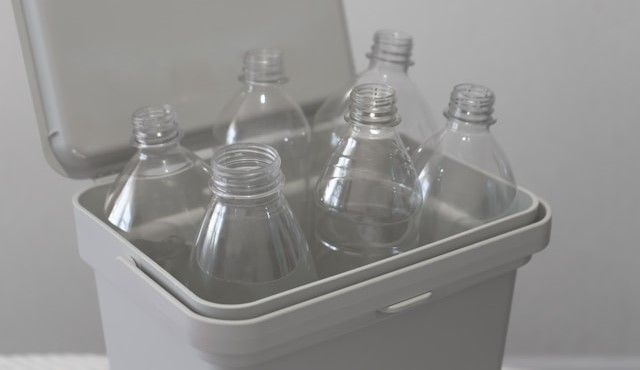
“There will be a lot of demand on our end to further derisk the process,” says Liu. “We have to derisk it so they [businesses] can see real value out of it, and they can potentially adopt it.”
For now, then, the dream of converting waste plastic into useful products like soap and detergent remains only half-fulfilled. Soap can be derived from the fatty acids present in certain plastics, while lubricants leverage the slippery, friction-reducing properties of plastics like polyethylene. A circular approach which not only diverts plastic waste from landfills and oceans, but also generates sustainable, practical alternatives to conventional products.
A chemical process which can employ the versatility of waste plastic and use it as a raw material presents an exciting opportunity to transform a global pollution crisis into a source of practical, eco-friendly solutions that benefit both people and the planet.
However, as always the science still has one key question without a satisfactory answer. “Yes, soap can be created from a few pieces of plastic, but can tons of plastic generate soaps and detergents profitably?”
Photo credit: Freepik, Freepik, Engin Akyurt on Unsplash, Freepik, & Arnepi Stocker