Everyone knows HDPE. It is the universally used plastic with the No2 Triangle. It is the substance that makes milk jugs and shampoo bottles, irrigation pipes and beer crates.
Now polymer researchers from Cornell University have discovered a new lower-energy route to its production. With an estimated 60 million tonnes of high-density polyethylene plastic made globally, ever year, even a small saving in the power consumption of HDPE manufacturing could make a significant difference.
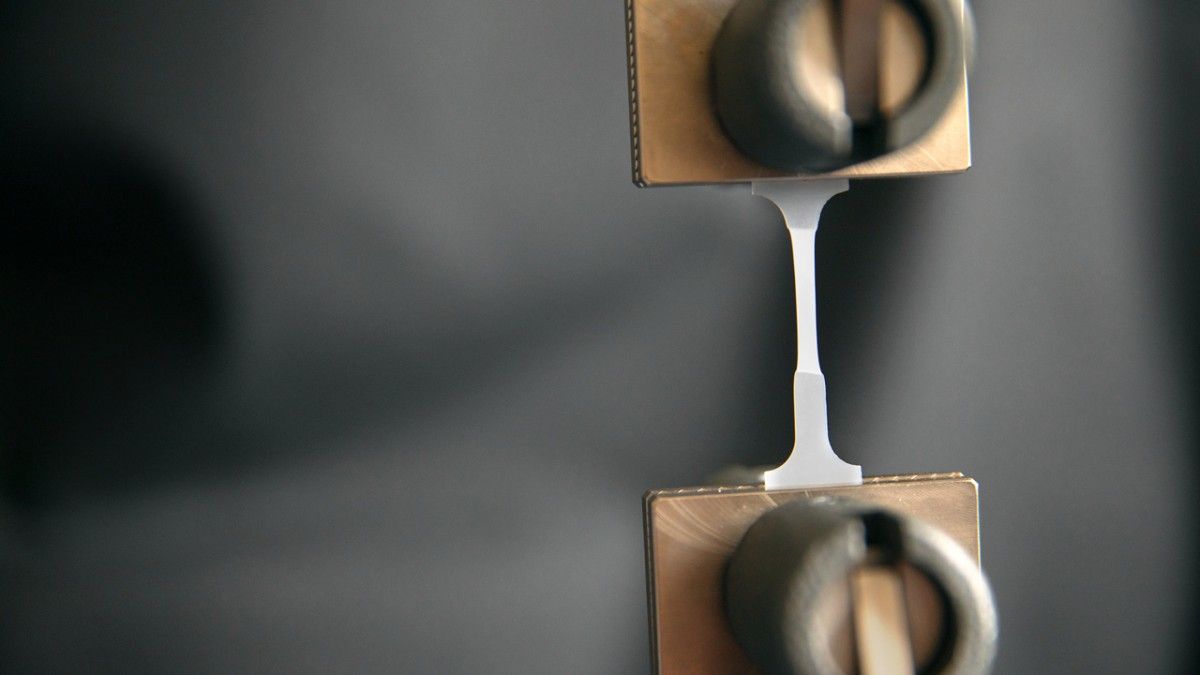
High-density polyethylene is the ‘go to’ substance because of its strength and durability combined with a relatively low weight. The key to controlling these advantageous properties is through understanding and manipulation of the polymer chains.
As the journal Science Daily, outlines, “Plastics consist of polymers, which are bonded together chemically into chains. Long chains create stronger materials, …while shorter chains allow for easy processing. Commercial polymers are commonly produced with a range of chain lengths, to optimize performance and processability.”
However, the way that the chains are used affects not only the properties of the final plastic product, but also the amount of energy required in manufacturing. As plastic producers and recyclers add different materials to their mixes to control these properties, they alter the amount of energy needed to melt and mould the final product.
“The grand challenge,” says Renee Sifri, one of the research team and a doctoral candidate in chemistry at the College of Arts and Sciences, “has been to minimize the energy cost of plastic production and to create new ways to precisely tune the properties of consumer plastics.”
Analysis of the raw materials and processes used in the production of HDPE by a team of polymer specialists from Cornell has found that molecular weight distribution plays a key role in the strength and recyclability of plastics. Furthermore, they have developed laboratory procedures to control this variable.
“Developing new ways to reduce the amount of plastic production is vital to minimizing plastic waste,” said Omar Padilla-Vélez, another team member and doctoral candidate in chemistry at the Department of Chemistry and Chemical Biology.
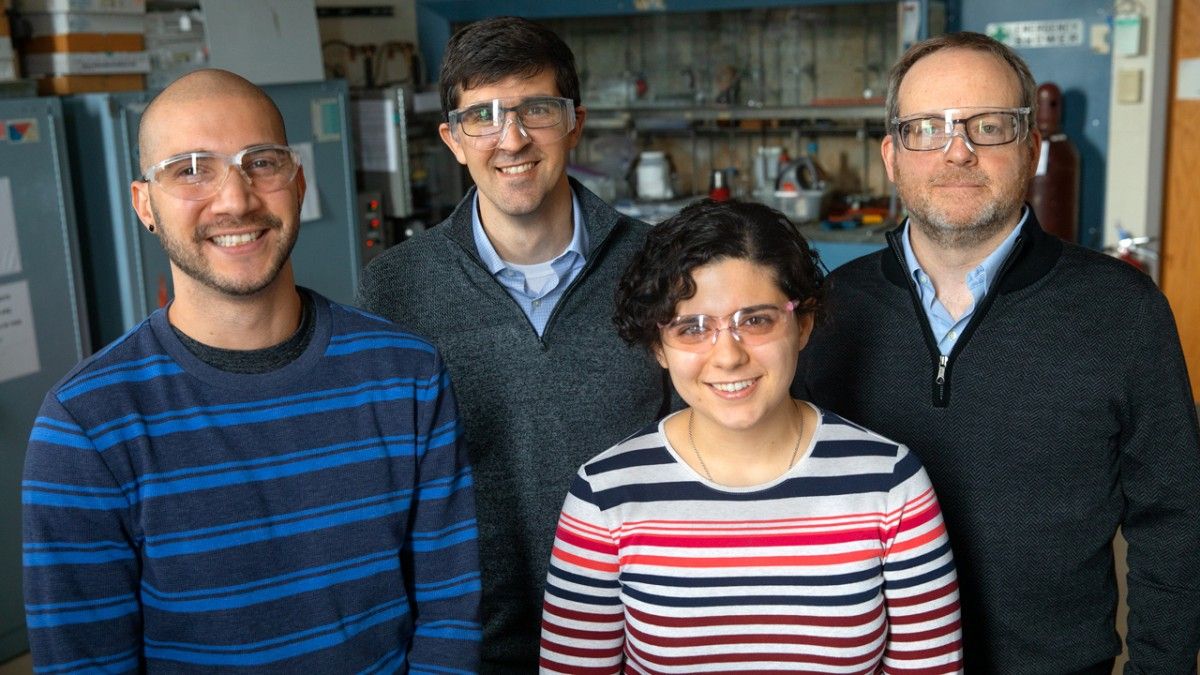
In describing the research, the university press release states that, “To test the tensile strength of the plastic, the researchers molded the new plastic into tiny, flat pieces shaped like dog bones. Tensile testing revealed that the molecular weight distribution (polymer chains) does not impact the strain at its breaking point, which shows that the updated ability to influence HDPE processing does not compromise material strength.”
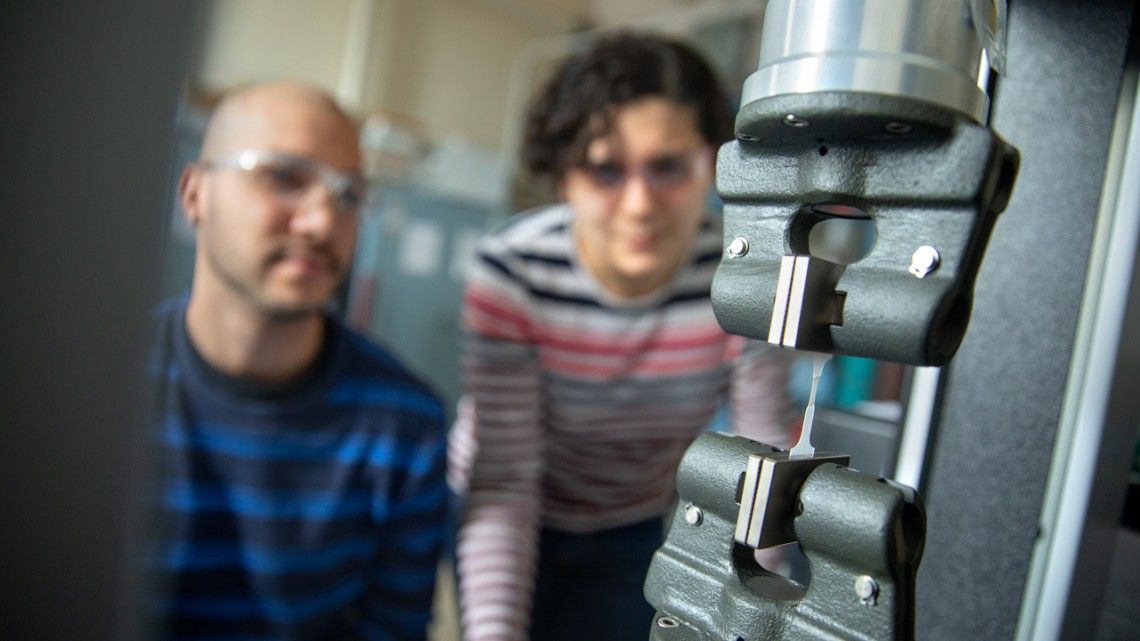
The researchers have now published their study in the Journal of the American Chemical Society, where they announce a, “method [that] provides precise control over the Molecular Weight Distributions (MWD) shape which, in turn, offers a systematic study on the influence of MWD shape on the physical properties of HDPE.” Specifically adding that, “Through rheological testing, we observe a difference in complex viscosity and shear thinning with opposite MWD skew. However, tensile testing reveals that the MWD skew does not impact the strain at break, signifying the ability to influence HDPE processing without compromising material strength.”
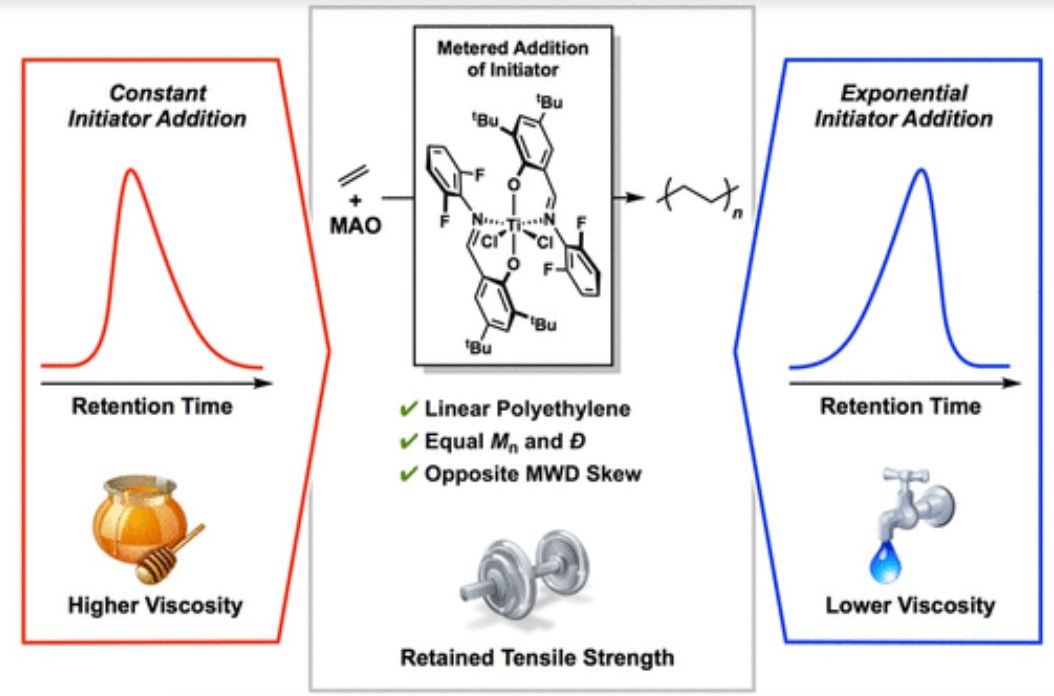
“Our work shows promise for lowering the amount of energy needed in processing without compromising polymer strength,” notes Sifri. “The take-home message - reduce the processing energy while ensuring the strength is not compromised. That way the plastic containers don't fall apart.”
Photo credit: CornellUniversity, Frank Habel from Pixabay, & Journal of the American Chemical Society