It only takes a quick glance of data on global raw material prices to see instability and uncertainty. Concerns over the supply of key raw materials coupled with demand fluctuations from national economies, and supply chain disruption from geopolitical events will always provide anxiety for commodity markets.
For example, rare earth elements, a group of minerals such as lanthanum, cerium, and indium, on which our digital lives depend, are currently under threat of tariffs or even an embargo, as the US-China trade war rages on.
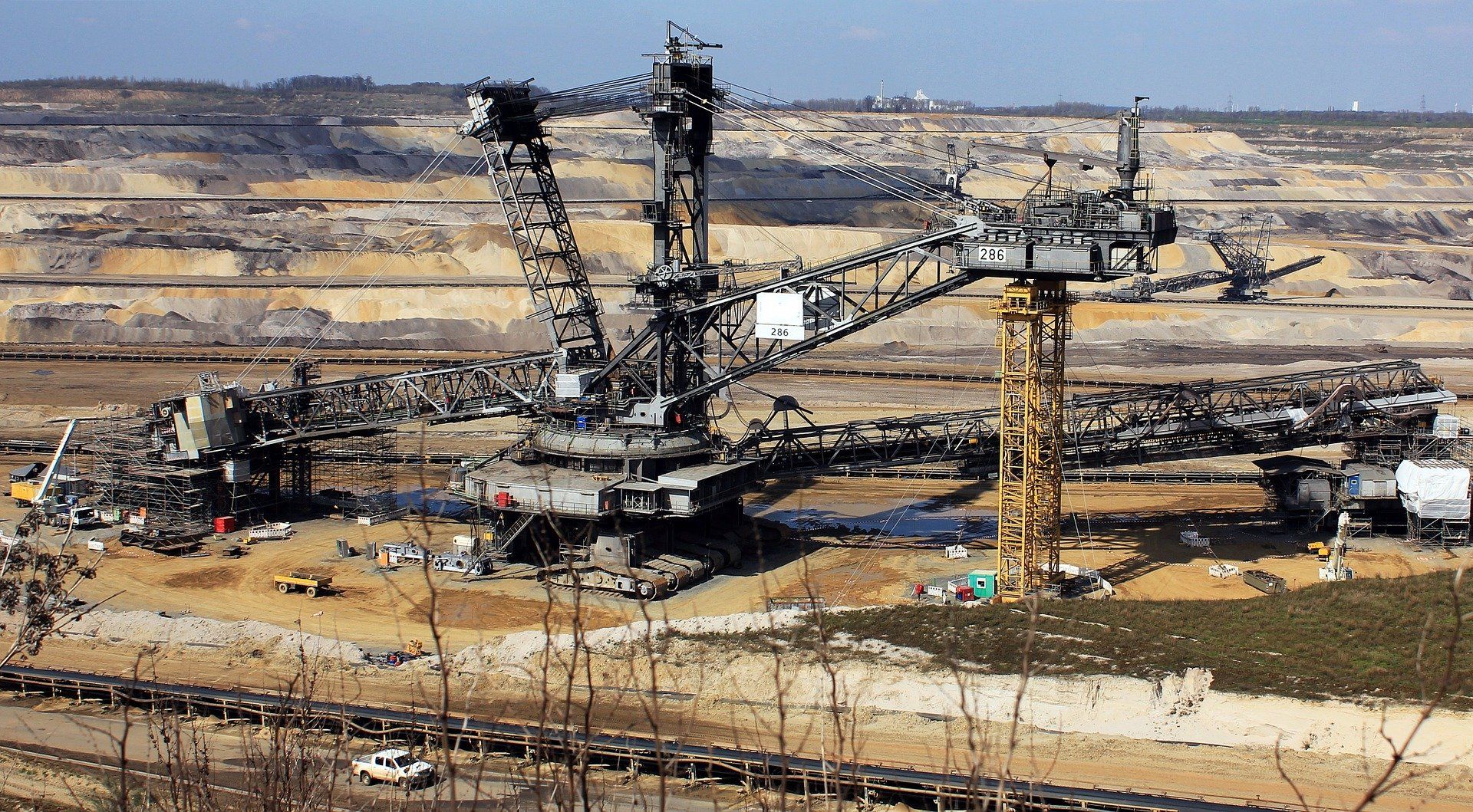
As the Financial Times reports, “Just as in 2010, when the price rise accompanied a dispute between China and Japan, rare earth elements (REE) are again facing disruption to the supply of raw materials.”
Unexpected and unsolvable disruptions like these can have a massive impact on business. For example, Ian Higgins, the owner of the British metal alloy maker Less Common Metals, relies on supplies of REE from China. On the latest threat to his supplies he said, “If you do get prices spiking again for a second time the fundamental question is how much damage could it do to the rare earth magnet industry.”
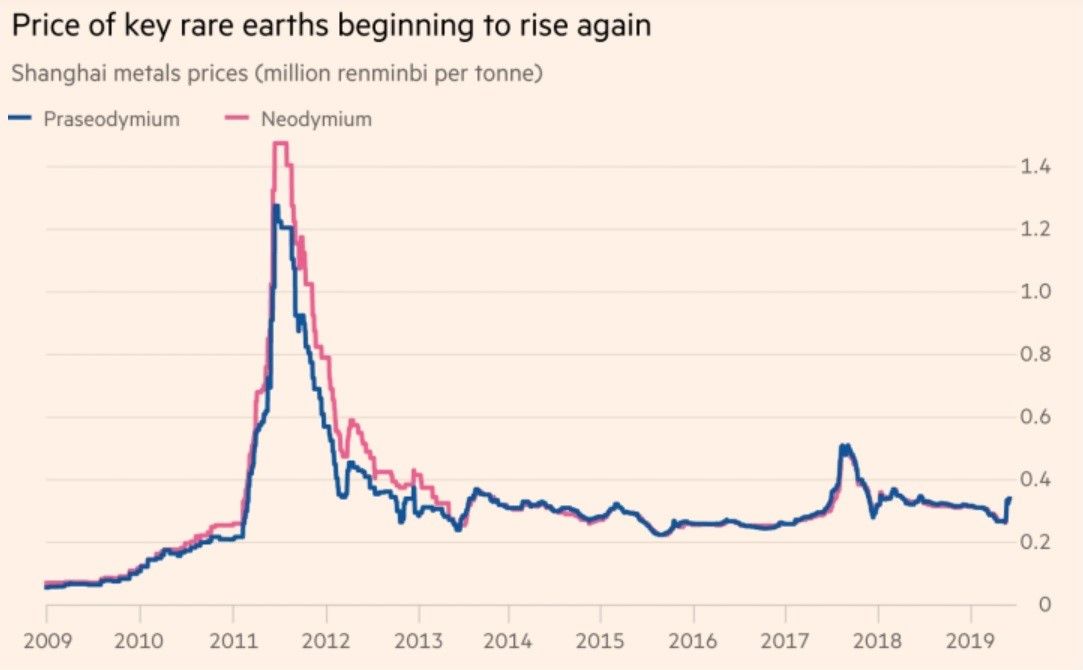
This has significance to specialised sectors of the economy. As the FT notes, “The magnets are used in electric vehicles, and are almost all reliant on rare earths mined in China. Prices for neodymium and praseodymium, the two main rare earths used in magnets, have risen from about $32 per kilogramme in early May to about $42/kg [in June], according to UBS. In 2011, prices rose to over $160/kg”
Other raw materials, even more commonly sourced minerals, have an equally unsteady past and an unforeseeable future.
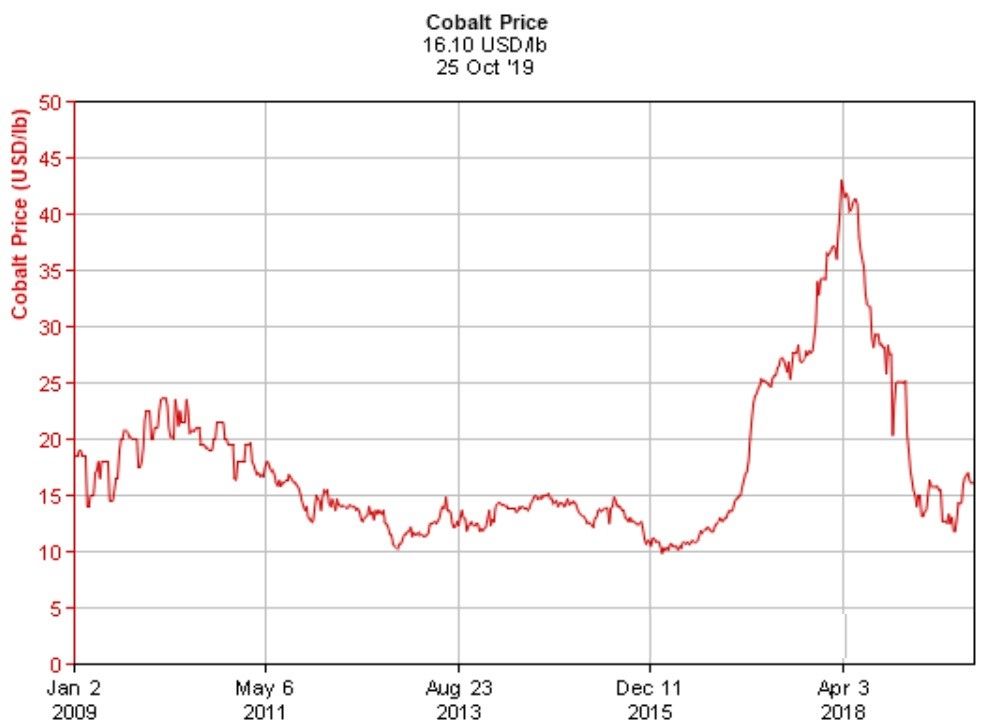
If wars, tariffs, sanctions, and politics cannot be controlled, can raw material suppliers find solutions to global disruptions to supply?
As material price analysts are aware, history often repeats itself. Similarly, fixes to present day problems can often be found in the past.
For example, the collapse of Bronze Age civilizations around 1200 BC caused by decades of bad harvests and freak natural disasters, led to the destruction of trade routes that limited supplies of the copper or tin used to make bronze around this time. As a result, metal smiths looked again at inferior iron, and shortly developed steel, which has many advantages over bronze.
Maybe today, raw material suppliers need to rethink how they handle supply chain disruptions to their key products if they are to avoid becoming bronze age warriors in an iron age world.
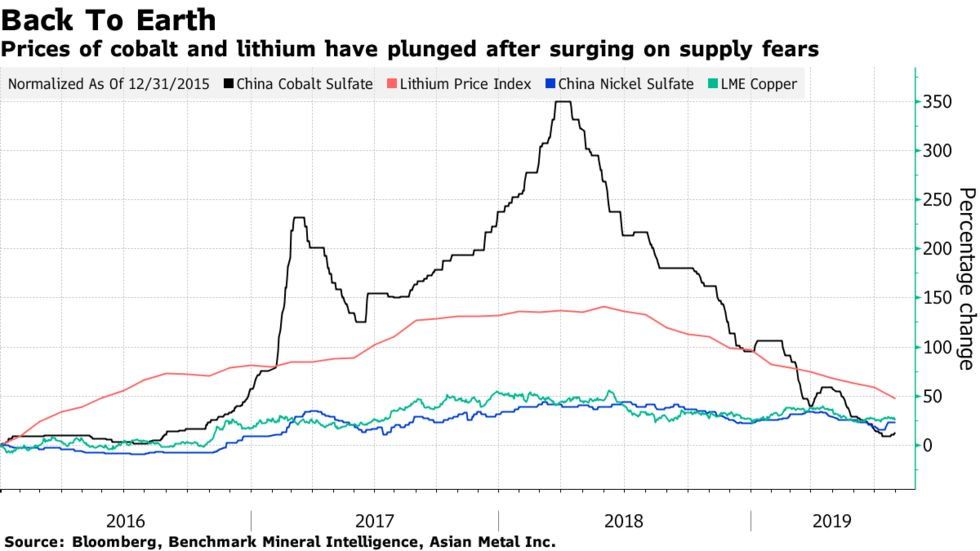
Raw Materials from Urban Mining
One such example of original thinking is the development of ‘urban mining’, the practice of extracting or recycling raw materials from discarded electronic devices. As the NY Post reports, “As China’s aggressive hunt for overseas cobalt and lithium for electric vehicles pushes up prices and causes a global shortage of key metals, South Korea is increasingly turning to ‘urban mining’ to recover cobalt, lithium and other scarce metals from electronic waste.”
The report notes that the most recent data from 2016 shows that more than $18 billion worth of metals were extracted from recycled materials, almost a quarter of national demand.
“SungEel HiTech is South Korea’s largest battery recycler,” writes the Post. “A decade ago, the company was at a crossroads as plasma TV panels, from which it extracted gold and silver, began to phase out. Now it is part of a supply chain for some of the world’s major battery makers, including Samsung SDI and LG Chem.”
The resulting switch has led to a threefold boost in capacity for the firm.
Raw Materials from Biocatalysis
But beyond improved recycling techniques, research is advancing in the use of biocatalysis as a method of replacing specialized raw materials.
These catalysts are created by biochemists who are able to ‘engineer’ natural enzymes to perform different chemical reactions. By fine tuning the chemistry it is possible for these enzymes, particularly bacterial enzymes, to work as replacements for critical materials.
As an article published by the Journal of the Royal Society describes, the use of green chemistry has, “ … been widely embraced by industry and academia worldwide. The pharmaceutical industry in particular has made great strides in reducing their chemical waste and avoiding the use of toxic or hazardous solvents and reagents. Catalysis, both chemical and biological, has played a pivotal role in this ‘greening’ of the pharmaceutical industry.”
Also noting how, “More recently, much attention is being diverted to a third aspect of green chemistry and sustainability: the use of renewable raw materials as an alternative to the unsustainable use of fossil resources. In this context, the valorization of unavoidable waste lignocellulose and triglycerides is particularly attractive and fits well with the current trend towards a circular economy. In short, we expect that current developments in chemistry and biotechnology, especially from an industrial viewpoint, will continue.”
While today’s use of green chemistry has mainly focused on replacing fossil fuel materials, advances in bioengineering could also help ease future supply pressures imposed on other limited raw materials.
To find out more read: Solutions to Global Disruption of Rare Raw Materials part 2
Photo credit: ACS, Iopscience, Infomine, Financial Times, Twitter, Bulkdistributor, Resource, RSC, ScientificAmerican, Thermofisher, & Airliquide