Researchers from MIT have discovered a simpler way to recycle thermoset plastics.
It is a discovery that will help to boost sustainability in the plastics industry, as it provides a route to recycling for a wide range of plastic products.
Currently, waste thermoset plastic is typically burnt or buried, as the strong polymer links makes recycling impractical.
“Once they are set in a given shape, they're in that shape for their lifetime,” says MIT’s Prof. Jeremiah Johnson, the study’s senior author. “There is often no easy way to recycle them.”
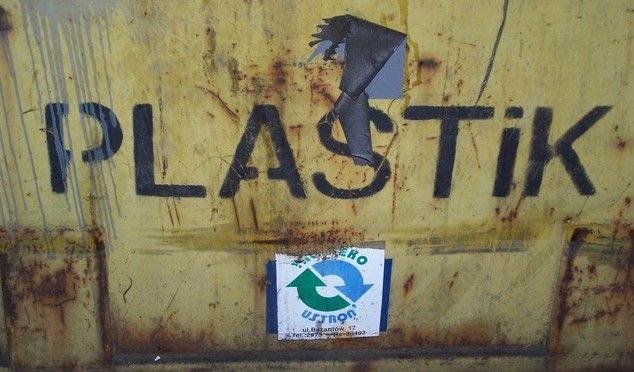
Yet thermoset plastics are often needed for their durability and heat-resistance, meaning that manufacturers often use them to make car parts, car tyres, and electrical appliances. This means that each year millions of tons of products such as polyurethanes and epoxies are sent to land fill.
However, all that may now change, as MIT researchers have shown they can, “produce a degradable version of a thermoset plastic called pDCPD, break it down into a powder, and use the powder to create more pDCPD.” The press release also stating that the team have, “also proposed a theoretical model suggesting that their approach could be applicable to a wide range of plastics and other polymers, such as rubber.”
“This work unveils a fundamental design principle that we believe is general to any kind of thermoset with this basic architecture,” notes Johnson.
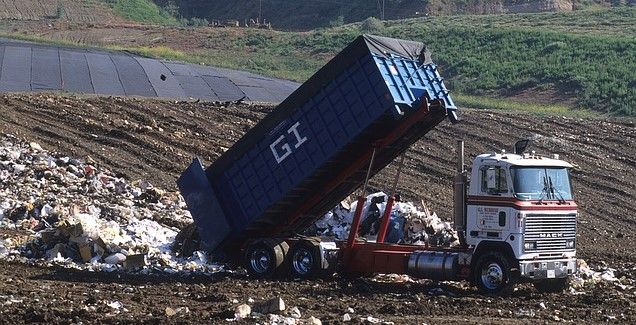
There are two major classes of plastic: thermoplastics and thermosets.
Thermoplastics make up about 75% of all the plastic made and include products such as polypropylene and polyethylene. They usually start life in pellet form, are heated until they melt and can then be reshaped as desired, to form toys, food wrappers, and plastic bags.
To recycle them often requires simple reheating, melting, and reforming.
Thermosets are made from a similar process, but once they have been melted, cooled, and set, they are difficult to remelt. This is because, as the MIT website explains, “… the bonds that form between the polymer molecules are strong chemical attachments called covalent bonds, which are very difficult to break. When heated, thermoset plastics will typically burn before they can be remolded.”
Despite this, demand for thermoset plastics remains high. As the study in the journal Nature highlights, “The high density of crosslinks that gives thermosets their useful properties (for example, chemical and thermal resistance and tensile strength) comes at the expense of degradability and recyclability.” Observing that, “Thermosets have a key role in the modern plastics and rubber industries, comprising about 20 per cent of polymeric materials manufactured today, with a worldwide annual production of about 65 million ton.”
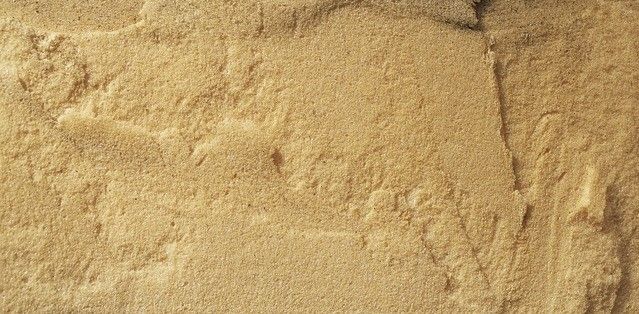
Knowing that the chemical bonds holding thermosets together are stronger than those found in other materials such as thermoplastics, Johnson’s study group began looking at way to modify the plastic with a chemical linker. In 2019, this led them to creating degradable polymers useable for drug delivery, by having a silyl ether monomer spread throughout its mixture.
When the monomer is “exposed to acids, bases, or ions such as fluoride, the silyl ether bonds break.”
As the same chemical reaction is used to make some thermoset plastics, such as polydicyclopentadiene (pDCPD) which is used for body panels in trucks and buses, the team focused on applying the same technique to recycle industrial thermoset plastics.
The team found that, “… if the silyl ether monomer made up between 7.5 and 10 percent of the overall material, pDCPD would retain its mechanical strength but could be broken down into a soluble powder upon exposure to fluoride ions.”
“That was the first exciting thing we found,” Johnson says. “We can make pDCPD degradable while not hurting its useful mechanical properties.”
A precursor solution, used to make pDCPD, then dissolves the powder into a form that the team used to make new pDCPD thermosets.
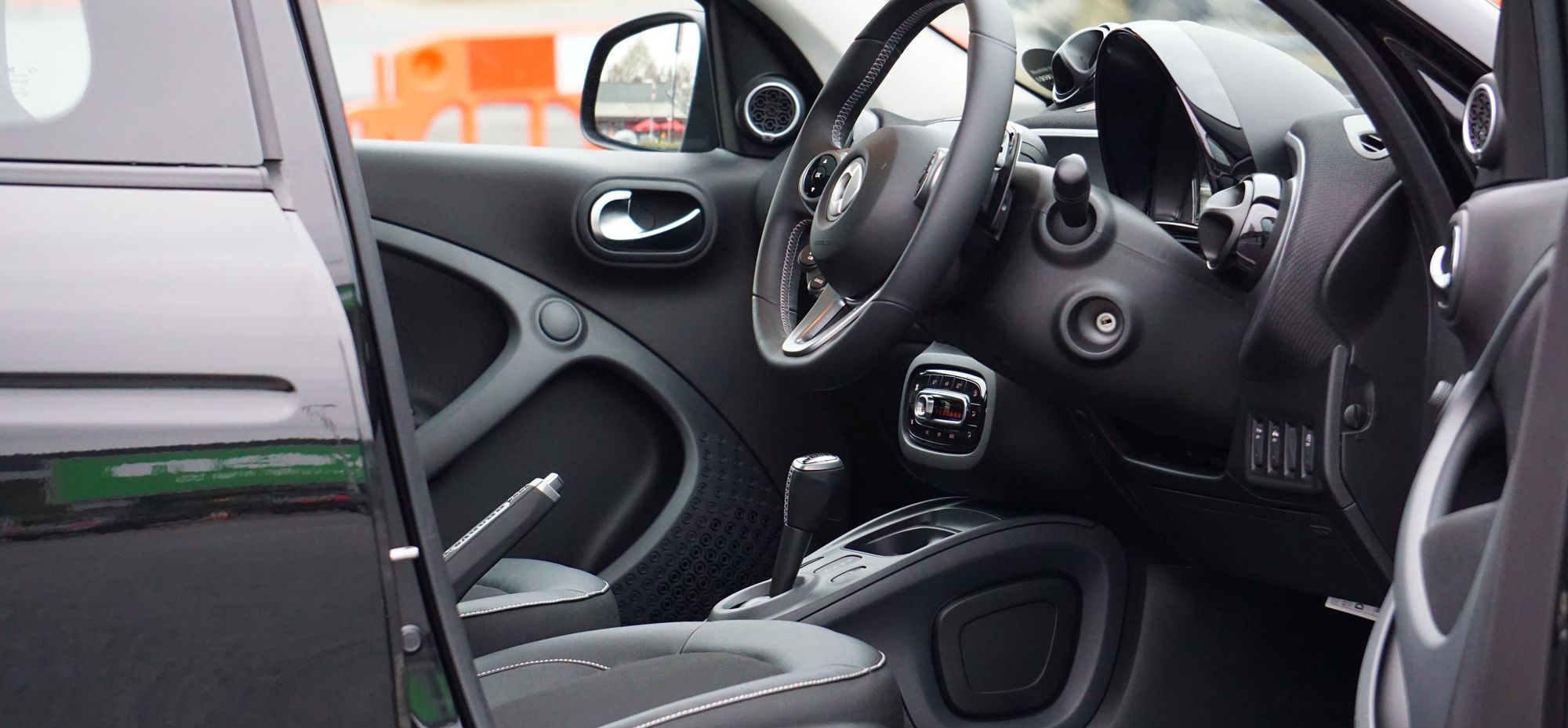
“That new material has nearly indistinguishable, and in some ways improved, mechanical properties compared to the original material,” explains Johnson. “Showing that you can take the degradation products and remake the same thermoset again using the same process is exciting.”
The novel idea to ‘cleave’ apart the polymer strands with degradable monomers is being hailed as a major breakthrough. For years, researchers had attempted to find a way to recycle thermoset plastics by using degradable bonds, but always without success.
Now a world of recycling has opened up, as the researchers believe that the ‘cleaving’ process will work for all thermosets, not just for pDCPDs.
“This is an exciting advance in engineering thermoset plastics,” says Jeffrey Moore, a professor of chemistry at the University of Illinois, who was not involved in the study. “Chemists have spent most of their effort learning to synthesize better plastics, and far less chemistry research has been invested into the science of polymer deconstruction. Johnson's work helps to fill this important gap in fundamental knowledge while providing advances of technological significance.”
The team is now looking at ways to commercialise their discovery, possibly through licencing.
One businessman who has been helping Johnson and the team assess the technology and its financial viability is Patrick Casey, who is a new product consultant at SP Insight.
“We have discussed this technology with some leading industry players, who tell us it promises to be good for stakeholders throughout the value chain,” says Casey, who has already begun looking at business models for the project, as well as secondary market research. “Parts fabricators get a stream of low-cost recycled materials; equipment manufacturers, such as automotive companies, can meet their sustainability objectives; and recyclers get a new revenue stream from thermoset plastics. The consumers see a cost saving, and all of us get a cleaner environment.”
Photo credit: Wolfgang Eckert from Pixabay, Mike Birdy from StockSnap, andy bahn from FreeImages, prvideotv from Pixabay, & Sándor Balázs from FreeImages