The world is awash with plastic – literally.
Mankind has already made more than 8.3 billion tons of it but continues to make more as it is cheaper and easier to produce and throw away than it is to recycle.
Solving this problem requires major breakthroughs from both science and industry to find and adopt more economically viable approaches to plastic recycling.

One such method has now been discovered at the University of California, Santa Barbara, where researchers Susannah Scott, Mahdi Abu-Omar and Fan Zhang have developed what the journal Science Daily calls, “a one-pot, low-temperature catalytic method that upcycles polyethylene.”
Of all the plastics to focus on, the team chose polyethylene as it is “a polymer that is found in about a third of all plastics produced, with a global value of about $200 billion annually.” They have now reached their goal, with a cost-effective approach to turn polyethylene into, “high-value alkylaromatic molecules that are the basis of many industrial chemicals and consumer products.”
Plastic is such a versatile material because of its chemical inertness. It simply doesn’t react to the substances around it.
“Plastic pipes don't rust or leach into the water supply, plastic bottles can store caustic chemicals, and plastic coatings can resist high temperatures,” notes the university press release. “But this quality of inertness also makes plastics very slow to break down naturally and very energy intensive to do so artificially.”
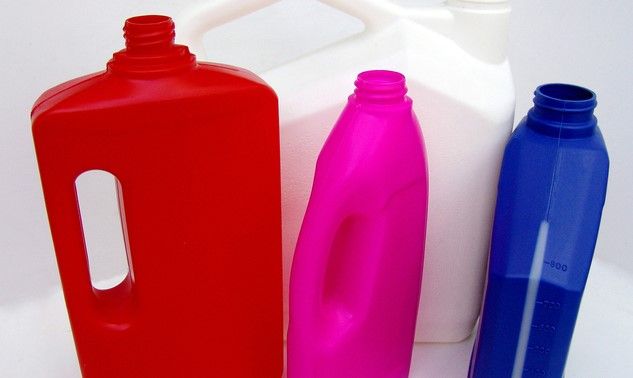
“They're made with carbon-carbon, and carbon-hydrogen bonds,” explains Professor of chemical engineering Abu-Omar, who specializes in energy catalysis, “and they're very difficult to chemically recycle.”
At the heart of breaking down a polymer like polyethylene, is that so much energy is needed to return it to the chemical building blocks used to form high-value molecules. This means that it is cheaper to convert petroleum into the desired feedstock, than it is to recycle waste plastic.
“On the other hand, if we could directly convert the polymers to these higher-value molecules and completely cut out the high-energy step of going back to these building block molecules, then we have a high-value process with a low energy footprint,” says Scott, a professor of chemistry and chemical engineering, who specialises in sustainable catalytic processing.
This novel approach to the problem led the team to create a new tandem catalytic method that can form high-value alkylaromatic molecules directly from waste polyethylene plastic - doing so with little energy requirement, thus keeping costs low.
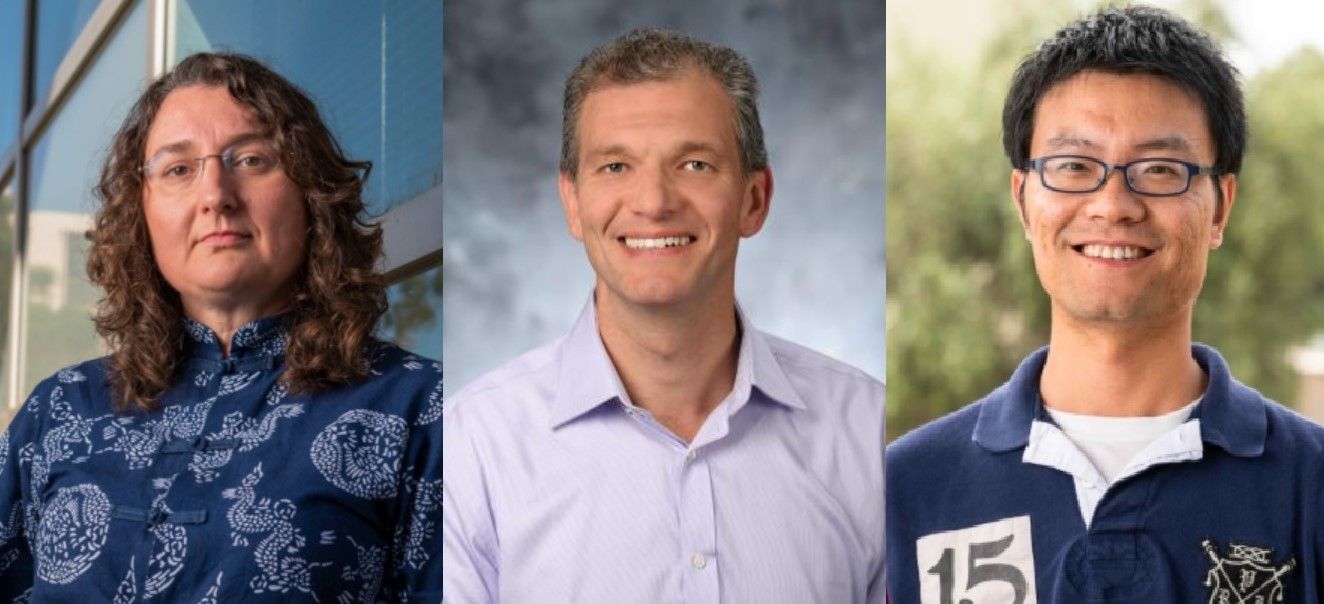
“We brought the temperature of the transformation down by hundreds of degrees,” says Scott. “And we simplified the number of steps in the process because we're not doing multiple transformations.”
Now the team have now published their findings in the journal Science, which explains how conventional methods of recycling polyethylene require temperatures ranging from 500-1000 degrees Celsius, leaving a mix of gas, liquid, and coke. However, the new catalytic process works at about 300 degrees and breaks the polyolefins down into larger molecules within a lubricant range.
The process requires no solvent or added hydrogen and creates a high value alkylaromatic molecule with multiple industrial uses for the manufacture of solvents, paints, lubricants, detergents, pharmaceuticals and more.
“Forming aromatic molecules from small hydrocarbons is difficult,” says Fan Zhang, the study’s lead. “Here, during aromatics formation from polyolefins, hydrogen is formed as a byproduct and further used to cut the polymer chains to make the whole process favorable. As a result, we get long-chain alkylaromatics, and that's the fascinating outcome.”
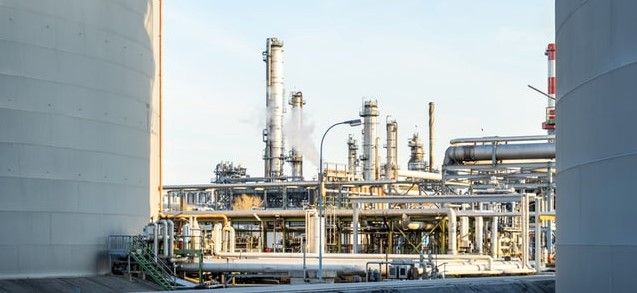
Meanwhile, in the Czech Republic, the company AG CHEMI GROUP (who sponsor this website) has been combining with nanotechnology researchers to create an industrial process for recycling plastics.
The result is a polymer nanostructuring technology which enables the modification of a wide range of plastics (including polyethylene) for secondary use.
This novel, nanostructure technology allows 100% modification of waste plastics, both in order to maintain the conventional properties of the original materials, such as impact strength, and in order to obtain new material properties (for example, obtaining thermally or electrically conductive plastics).
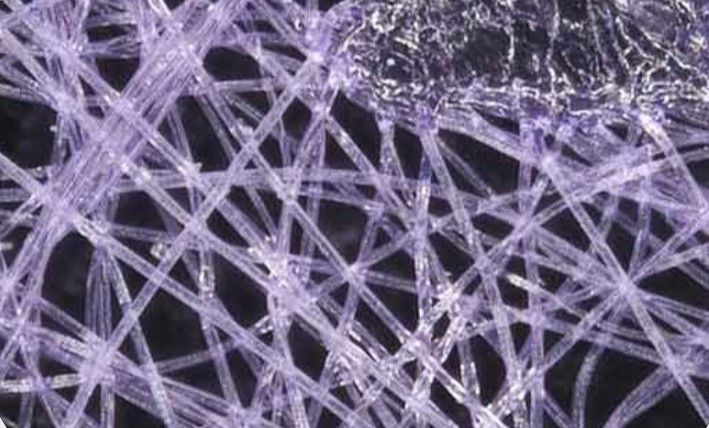
Like the method developed in Santa Barbara, the plastic can be modified in a cost-effective way as, if necessary, the nanostructuring can be carried out only on the surface of the material. This means that the whole volume of the polymer does not need to be treated.
“The use of nanomaterials with a particle size in the nanometre range, requires thorough preparation of a nanoadditive and a pure polymer, as well as the use of special technology in a two-phase modification, which has been developed and tested by our company,” explains Lev Lyapeikov, the product development manager at AG CHEMI GROUP. “Examples of the use of this technology can be found in our product portfolio and in our projects in the development and commercialization phase.”
If you are interested in learning more about investing in nanotechnology or in buying bonds in a patent holder of nanoproduction processes, then visit: AG CHEMI GROUP.
Photo credit: Magda Ehlers from Pexels, Nick Fewings on Unsplash, Jose Alfredo Gomez Soberano from FreeImages, & AG CHEMI GROUP, Dimitry Anikin on Unsplash