Car tyres are a major problem for the automobile industry. They are heavy, energy-intensive to manufacture, require large quantities of non-renewable, fossil fuel raw materials, and worst of all, they are difficult to recycle.
The result is that car tyres are a frequent challenge for the waste disposal industry. They are too bulky and toxic to bury in land fill, they too noxious and toxic to burn, and they are bad for the environment if dumped out at sea.
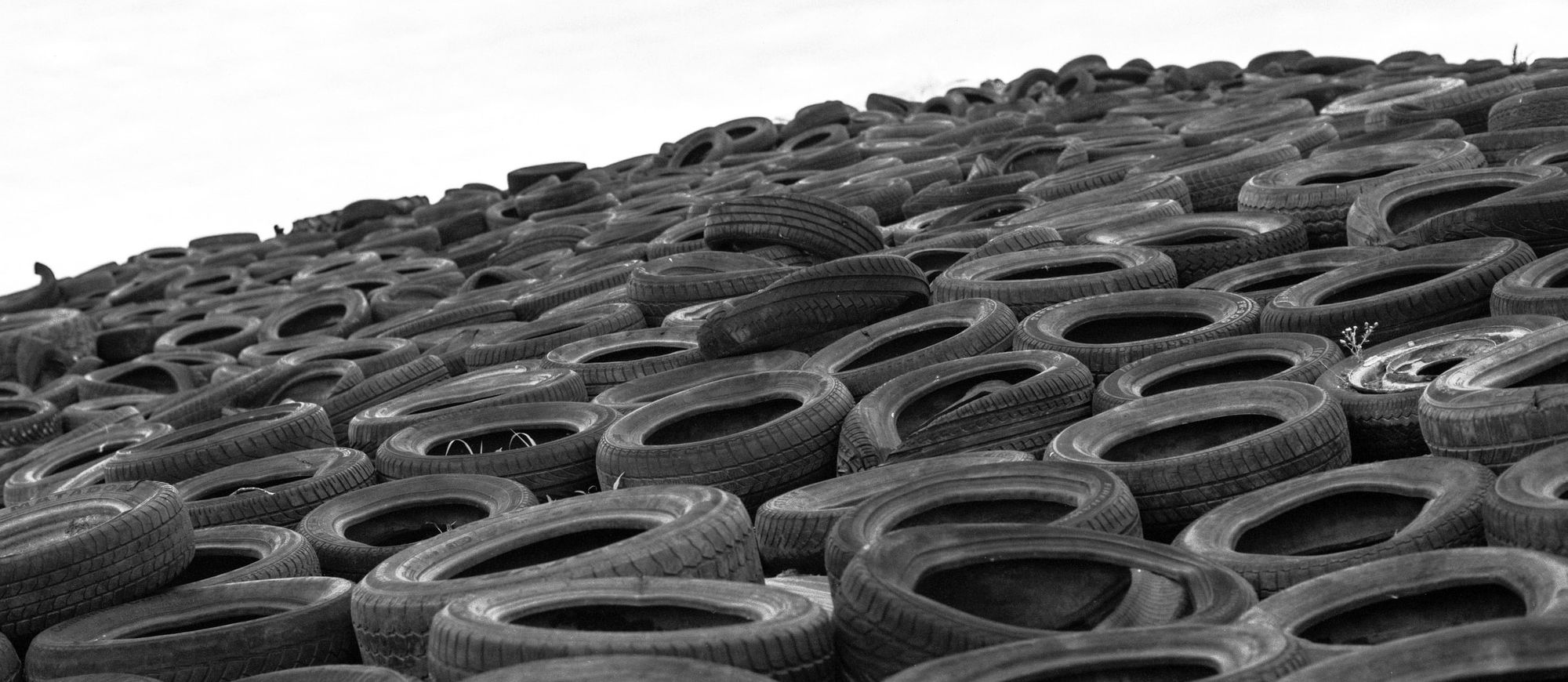
Yet, a used tyre (one that has worn down so much that it can no longer be driven on) still has great potential. It is largely unchanged since the day it was made and still has a lot of material that could be used again. If only the process of recycling tyres was not so expensive.
Consequently, the low-cost options for re-using tyres is limited. Some are ground down into rubber crumb that can be used to make asphalt for roads or flooring in children’s playgrounds. If you have 42,000 used tyres they can be used to make an Olympic sized artificial grass pitch. 13,500 old tyres and you can make a running track. Unfortunately, many, many more are burnt for fuel in the cement manufacturing process.
To expand the options available, nanotechnology specialists have been looking at ways to recycle car tyres so that they can be turned into useful raw materials at a cost-effective price.
The result is a process that involves the nanorestructuring of elastomers. As Lev Lyapeikov, the product development manager at AG CHEMI GROUP, explains, “The technology of nanostructuring elastomers is a modern trend in recent years, especially in the field of increasing the quality of recycled materials.”
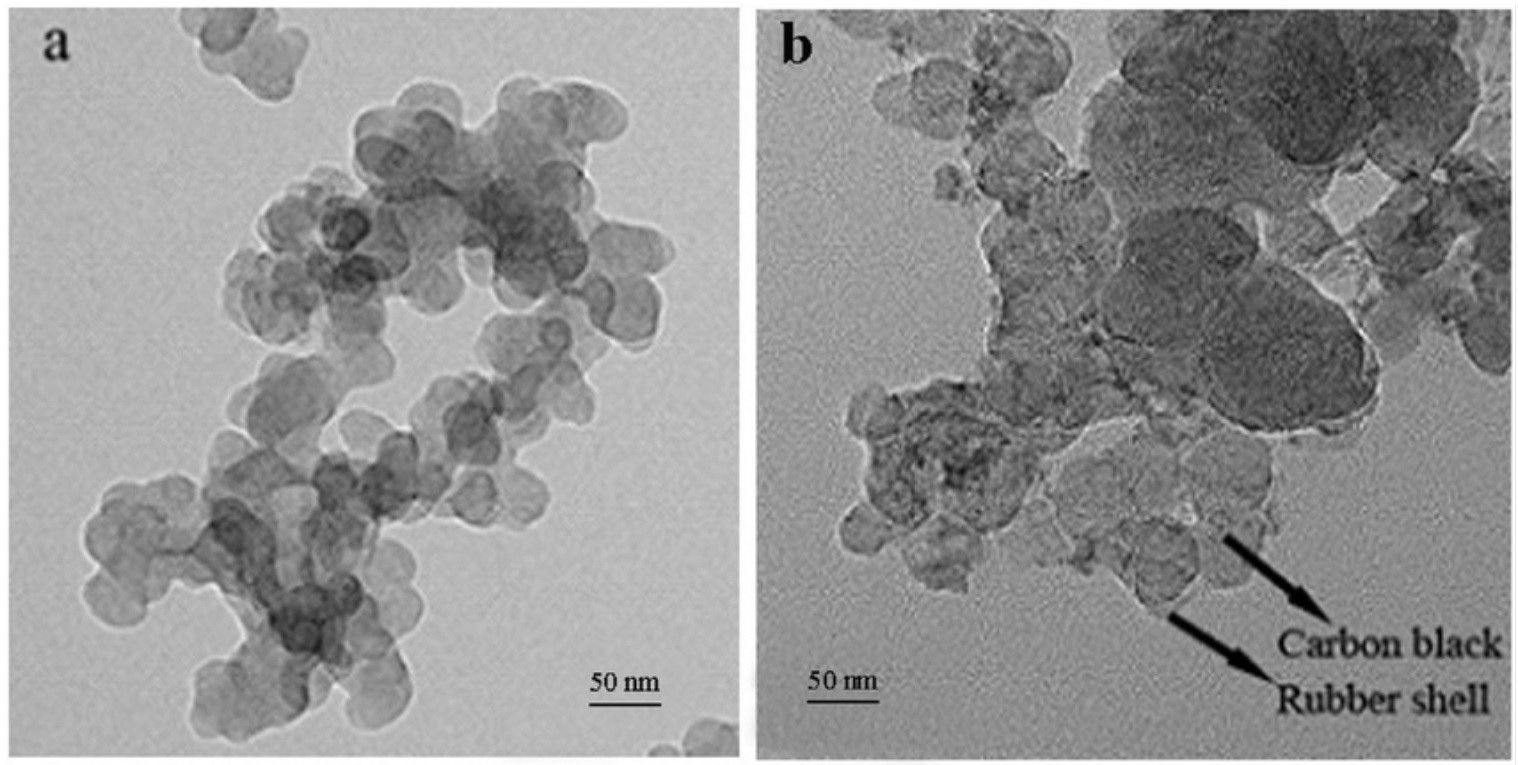
For this reason, AG CHEMI GROUP has cooperated with nanotech researchers to develop a process that can ensure an even distribution and dispersion of nanoparticles across a recycled tyre. It is an approach that can drastically increase tyre recyclability.
“By using our technology,” explains Lyapeikov, “new tyres can utilize up to 30% of recycled rubber without losing desired properties.”
The process of nanostructuring elastomers controls how nanoparticle additives are spread through the recycled tyre. By selecting nanoadditives with sought for properties, the company has found a practical approach to reusing of car tyres.
“The properties of nanomaterials are largely determined by the nature of the distribution, dispersion, form, and chemical composition of the crystallites (nanomaterials) of which they are composed,” notes Lyapeikov. “Therefore, the right choice of nanoadditive, which will be included in the structure of the newly modified material, is a very important point in the nanostructuring process.”
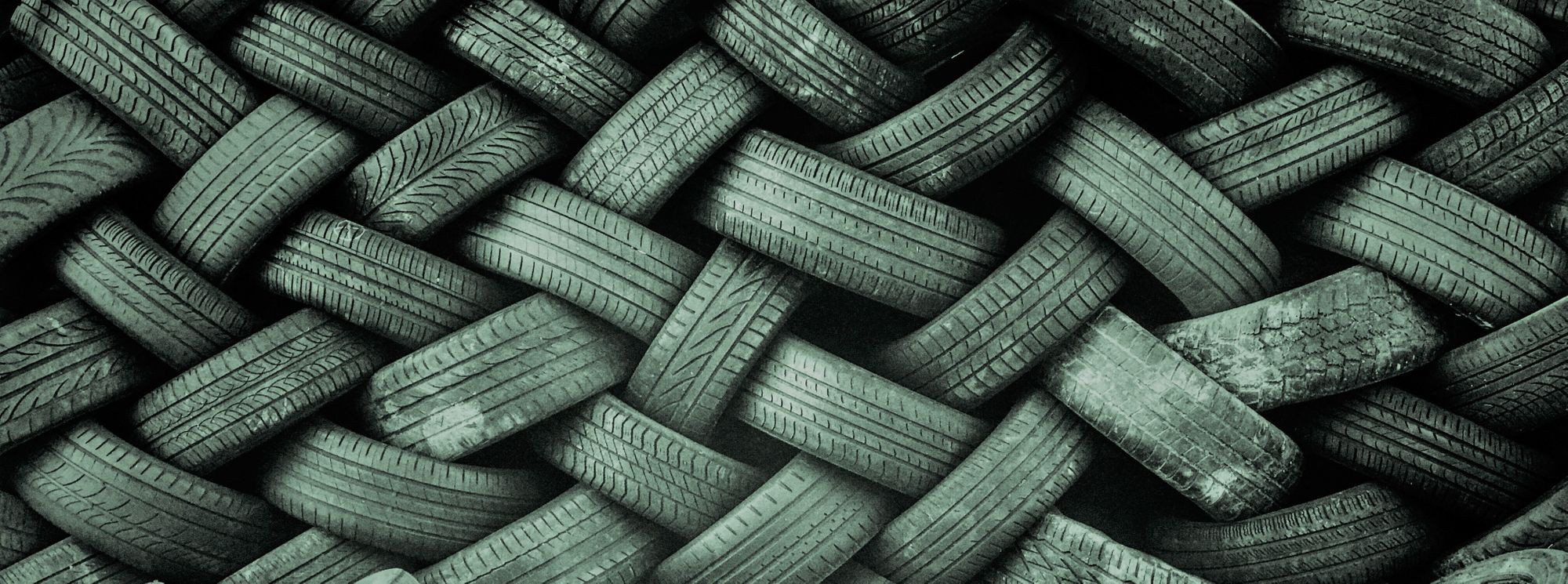
There is a huge market for car tyres, with as many as three billion new automobile tyres produced in 2019 alone. It is a figure that is likely to grow as car ownership in the developing world continues to expand.
Now that plans are proceeding to commercialise the nanostructuring of elastomers in tyres, a greener future may have been set for the automobile industry.
Photo credit: Frank Albrecht on Unsplash, Markus Spiske on Unsplash, & mthaz Ahamed on Unsplash