Plastic is the product of our times. A world changing substance that plays a role in so many products. Kitchens, cars, toys, containers, bags, furniture, baths and showers, fabrics, fishing nets, electronic devices, rope, floors, footwear, circuit boards, windows, domestic appliances, clothes, and jewellery and once upon a time, even soap had plastic in it.
Plastic is everywhere, literally.
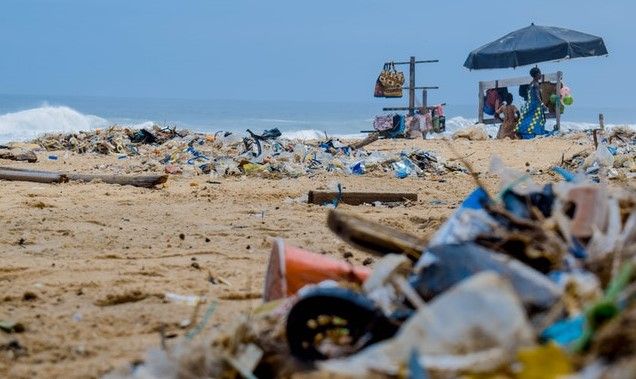
So much so, that today, the problem of waste plastic is a global problem talked about by environmentalists, chemical companies, and world leaders everywhere.
Key to solving the problem is chemical recycling. While some plastic is already mechanically shredded and recycled into new plastic products (typically lower grade plastics for use in bin liners, disposable cutlery, or other low-cost products), chemical recycling could find a use for waste plastic as a chemical raw material.
When discussing the issue of the chemical recycling of plastic, it is important to highlight that this does not include burning.
This was an issue recently raised by the Global Anti Incineration Alliance (GAIA) who issued a report on the matter stating that, “Industry uses the term ‘chemical recycling’ to deliberately blur the distinction between recycling (plastic to plastic repolymerization) and incineration (plastic-to-fuel).”
While in its most elemental form, burning plastics is a chemical reaction, it is clear that this is not recycling nor is it environmentally friendly. Consequently, the report was glad that, “The European Union’s Waste Framework Directive is crystal clear that producing fuels from waste cannot be labelled or counted as ‘recycling.’
So, what is chemical recycling, and can it really solve the problem?
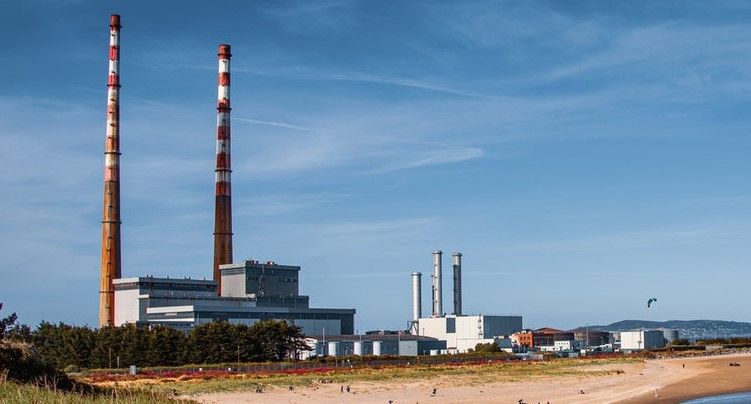
What is Chemical Recycling?
According to the American Chemical Council (ACC), “Chemical recycling, also called advanced plastics recycling, refers to several different technologies that convert post-use plastics into their original building blocks, specialty polymers, feedstocks for new plastics, fuels, waxes, and other valuable products.”
It does this through three basic methods:
· Solvent Purification. A process where plastic is dissolved in a solvent to remove contaminants and hazardous chemicals. This approach has found limited success with two main plastic products: polystyrene and PVC.
1. Polystyrene. A pilot program is now under way through the Loop Company which is hoping to recycle polystyrene from industrial insulation waste by removing the brominated fire retardant chemical Hexabromocyclododecane (HBCD).
2. PVC. In 2003, Solvay developed a VinyLoop technology to recycle PVC and accordingly opened a processing plant. While originally a profitable enterprise, changes to REACH legislation on phthalates (a plasticiser used to soften PVC) meant that the plant had to be closed as there was no economically viable way to separate the phthalates to comply with the law change.
· Chemical Depolymerisation. In this process, the long polymer chains that are the basis of plastics are broken down into simpler monomers using industrial chemicals. The monomers can then be purified and recombined to make new polymers in the same way that virgin plastic is made. This approach has already found success with PET, polyester, and a number of similar products. However, in a recent report, industry consultants at Eunomia found that there is a “general lack of understanding around the level of contamination that the technologies can handle, nor how the contaminants are dealt with following monomer purification”.
· Thermal Depolymerisation. Here the polymer chains are broken down using a heat treatment, with the most common process being called pyrolysis (heating with limited oxygen). When applied to waste plastic, this process results in a mixture of chemicals called pyrolysis oil. This can be purified and used again to make virgin plastics.
This is successfully being done to make polyolefin plastics (such as polypropylene and polyethylene) by using pyrolysis oil to replace naphtha in a petrochemical steam cracker.
However, a report into this process by industry consultants at Burns McDonnel found that “pyrolysis itself produces a complex mix of chemicals and can lead to the formation of toxic by-products such as dioxin, polycyclic aromatic hydrocarbons and hydrogen chloride. The pyrolysis oil must therefore be purified (and diluted) prior to being used in the cracker, and this purification stage will require further chemicals and will generate wastes that are likely to be hazardous – it will also have energy and financial costs.”
Pyrolysis oil can also be burnt as a fuel, but by definition this is not a form of chemical recycling.
Gasification. This is another heat treatment for plastic waste, but one which uses hot gases such as oxygen, air, or even steam. Like pyrolysis, gasification has been around for almost 70 years. It is a process of turning solid waste into a synthesis gas, such as ethanol or methanol. This can then be used to make virgin plastics or can be burnt as a fuel.
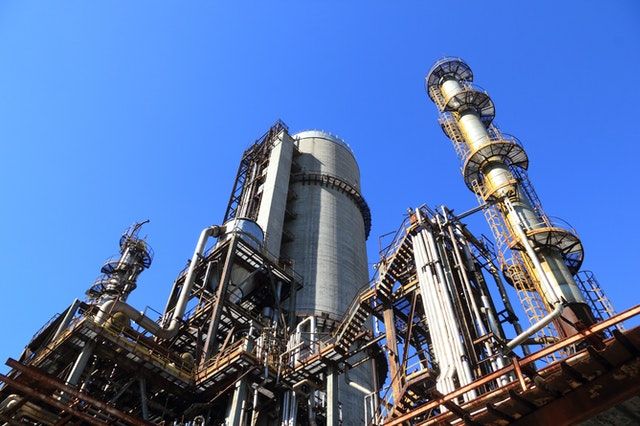
While these process are not cheap, they do provide some economically viable approaches to chemically recycling plastics. Further progress on the amount of plastic being recycled this way could be achieved through government support and subsidies for recycling plants, by raising taxes on fossil fuels, or by forcing plastic makers to recycle their used products.
The later seems less likely, as the plastic industry in the U.S., Canada, and Europe has already committed to “the goal of reusing, recycling or recovering all plastic packaging in these regions by 2040.”
Achieving this will be a massive undertaking, as plastic demand continues to soar.
The International Energy Agency reporting that “global demand for plastics has nearly doubled since 2000,” adding that, “Most of that uptick stems from the growth of the middle class, the fastest growing segment of the global population, projected to reach 5.3 billion by 2030.”
As at present, 90% of global plastic waste is being sent to landfill there is a pressing need for progress in building chemical recycling projects.
In fact, such is the scale of the amount of plastic waste that needs to be handled, it is unlikely that chemical recycling will be the sole answer.
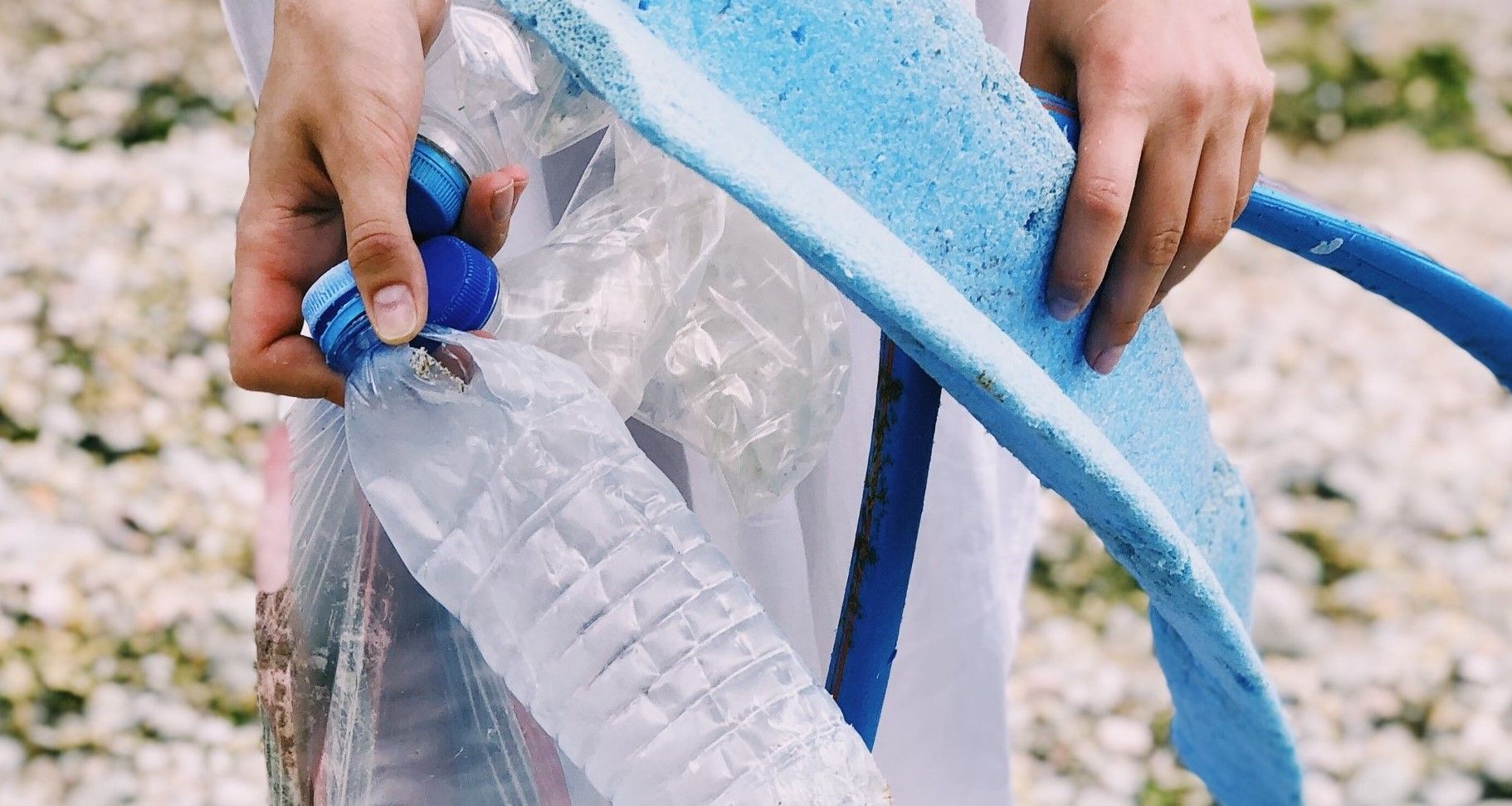
As The Huffington Post reports, “… the problem requires a slew of solutions, such as eliminating unnecessary packaging, transitioning to return-and-reuse systems, substituting virgin with recycled plastic or switching to other materials like paper, collecting and disposing of waste plastic properly, and recycling.”
A further possible response to boost plastic recycling is through the application of nanotechnology.
How Nanotechnology can help Boost Plastic Recycling Rates
One such company that has found a way to apply nanotechnology to plastic recycling is AG CHEMI GROUP, a Prague-based supplier of raw materials, which has patents pending on a process that can give new life into waste plastic, even improving it at the same time.
Building on their more than 25 years’ worth of experience in supplying the plastics industry the company noticed an increase in demand for recycled feedstock.
Whereas today, most plastics degrade when recycling as the polymer chains are corrupted in the recycling process, the AG CHEMI GROUP (who sponsor this webpage) has developed nanotechnology which allows for plastics to be given new qualities.
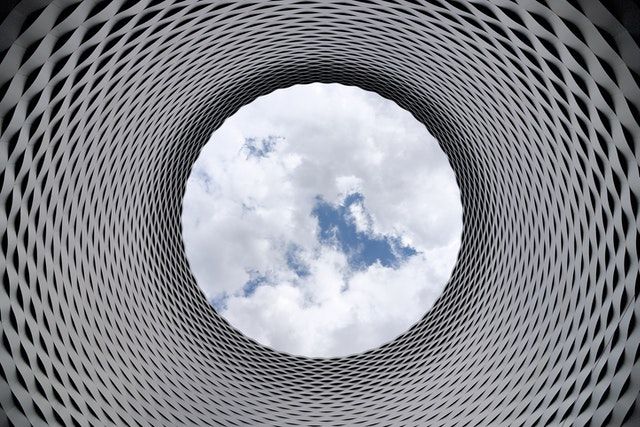
The process is called nanostructure technology, and it allows for the total modification of waste materials such as plastic in order to maintain the original properties of the material at a required level (for example, impact strength), as well as to add new material properties, such as thermal or electrical conductivity.
“The use of nanomaterials with a particle size in the nanometer range requires thorough preparation of the nanoadditive and pure polymer, as well as the use of special technology of two-phase modification, developed and tested by our company,” says Lev Lyapeikov, the product development manager at AG CHEMI GROUP. “Examples of the use of this technology can be found in our product portfolio and in our projects in the development and commercialization phase.”
To learn more about this topic, read How Nanotechnology Can Recycle Waste Plastic or visit the AG CHEMI GROUP website.
Photo credit: Daria Shevtsova from Pexels, Lucien Wanda, Karolina Grabowska, pexels, pexels, & Lucian Petronel Potlog from Pexels