Nanomaterial researchers are making great strides in improving polymers, resins, and plastics.
They are widely employed to enhance properties of thermal conductivity, strength, and electroconductivity, as well as abrasion, chemical, and crack resistance. This has enabled their use in plastic products such as epoxy resins to make coatings or fibre glass composites, methyl methacrylate resin-based concentrates to make ESD flooring, or even polyester resins to make printer rollers.
To learn more about this topic read: Why Use Nanoparticles as a Raw Material in Epoxy Resins? or The Power of Nanoadditives in Polyester Resins
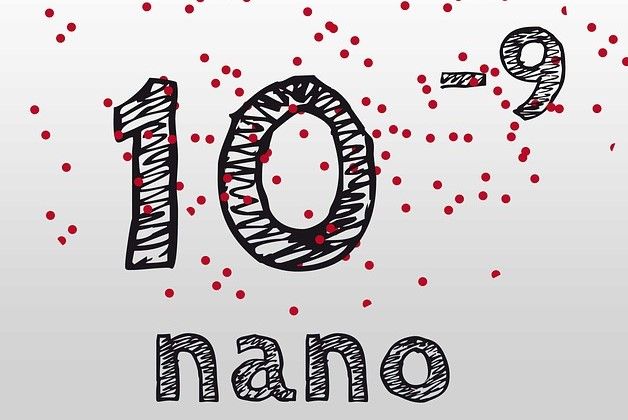
However, one of the largest markets for plastics is in the packaging sector.
Here, nanomaterials are being applied as a means to make stronger or more flexible packaging, as well as being used to implant tiny chemical sensors that can indicate if a food stuff is bad or not.
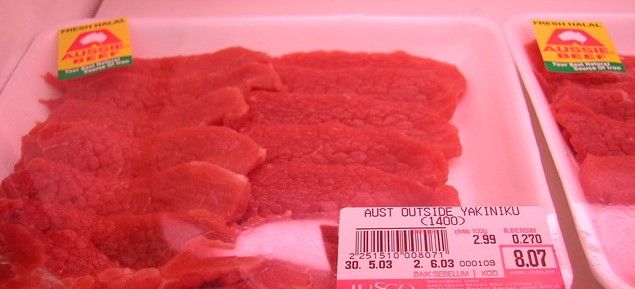
Recently though, nanotechnology researchers from Brazil made a breakthrough in using materials at the nanoscale to develop packaging films made from industrial waste. It is a process that not only removes petroleum-based plastic as a packaging material, but also employs bacterial cellulose scraps from the production of bandages as a feedstock – thus including the nano-film in the circular economy.
The discovery was made at São Paulo State University (UNESP)and is based on what the university press release describes as, “[A film] made from hydroxypropyl methylcellulose (HPMC) and bacterial cellulose scraps left over from industrial processing. Both raw materials are sustainable. They are combined to produce a biodegradable film of bacterial cellulose nanocrystals and HPMC.”
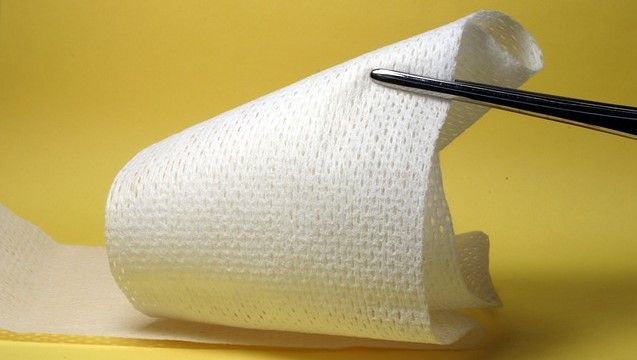
“We set out to fill the HMPC matrix with bacterial cellulose nanocrystals in order to enhance its properties,” says Márcia Regina de Moura Aouada who is the study’s co-author and an expert on renewable feedstocks and biodegradable films. “We also wanted to create greener protocols for the development of novel composites, from the material itself to its origin, so we included the reuse of industrial waste in the project.”
However, working with renewable polymers has challenges that need to be overcome.
“One of the limitations of films made of HPMC and other biopolymers is their low mechanical strength compared with traditional films derived from petroleum. They are also highly permeable to water vapor, which limits the available applications,” explains Pamela Melo the study’s first author. “We improved these properties by adding bacterial cellulose.”
While cellulose can be derived from algae and marine invertebrates, the most common source of cellulose is from plant waste. However, using plant-based cellulose requires the removal of impurities such as lignin. Doing so requires a process which uses organochlorine compounds which are harmful to the environment.
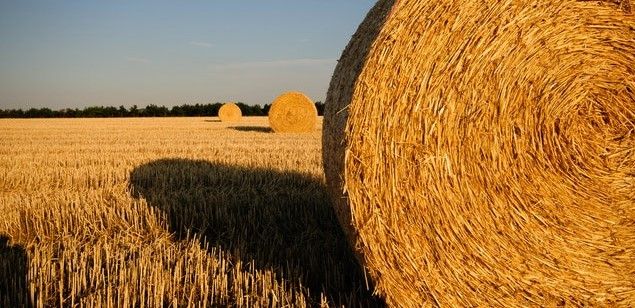
Hoping for a truly green approach, the Brazilian team took an alternative route, deciding instead to use cellulose produced by bacteria.
“Bacterial cellulose can be produced in the laboratory all year round, regardless of weather and environmental conditions. It’s a purer molecule and the production process generates less pollution,” said Aouada.
Its structure also contains nanometric fibres.
“This is very interesting because it gives the material distinct properties such as high tensile strength,” adds Aouada, “meaning it can withstand certain loads or stresses without breaking.”
For their source of bacterial cellulose, the researchers used scraps from a factory making wound dressing biofilms, a common use for bacterial cellulose. The first step of the process was to grind the scraps into a powder, before submitting it to sulfuric acid hydrolysis.
The result of this, according to the scientific journal Phys.org, was a, “bacterial cellulose nanocrystal suspension, which they mixed with HPMC diluted in water to produce a film-forming dispersion, a target of interest for the bioplastics industry.” Then, “The film-forming dispersion was deposited on a substrate. The solvents evaporated after 24-48 hours. The result was a stronger, less permeable product than HPMC-only film. The amount of water absorbed by the material is currently a constraint on its use in packaging.”
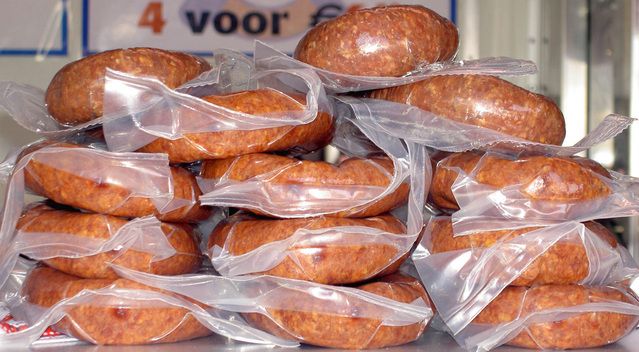
“How the nanocrystals interact with the HPMC matrix and are distributed within it will determine film quality,” explained Melo, “so we conducted tests and arrived at the optimal distribution via high-energy dispersion using a Turrax disperser.”
Significantly, the nanocrystals do not alter the transparency of HPMC.
The study has now been published in the ACS journal Applied Material & Interfaces, where the team explain how their new packaging film not only avoids fossil fuels but is also superior in many ways to conventional plastic packaging. The paper stating that, “As far as performance, the optically transparent hydroxypropyl methylcellulose (HPMC) films presented improved tensile strength (from 61 ± 6 to 86 ± 9 MPa) and Young’s modulus (from 1.5 ± 0.2 to 2.7 ± 0.4 GPa) while reduced elongation at break (from 15 ± 2 to 12 ± 2%) and water vapor permeability (from 0.40 ± 0.02 to 0.31 ± 0.01 g mm h–1 m–2 kPa–1) when filled with only 5 wt % of (120 ± 31) nm long, (13 ± 3) nm wide, 88% bacterial cellulose nanocrystals (BCNC).”
Describing the “effect of BCNCs on the mechanical and barrier properties of HPMC films” as a “dual, win–win”.
While the product is not currently ready for industrial production as its permeability is not yet up to market standards, the team are continuing to test other “film-forming dispersions” and “polymer dispersion techniques” to find the best approach.
“Our main focus,” said Aouada, “is on finding substitutes for materials not considered ecologically correct, such as petroleum products. Such substitutes include biodegradable composites derived from renewable resources.”
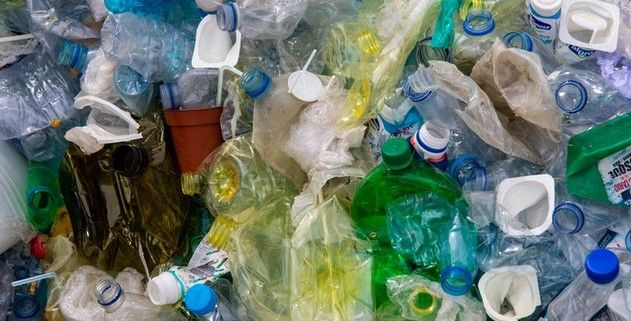
Given that the primary reason for using fossil-fuel plastics in packaging is low-cost, the researchers are confident that they will achieve their goal, as the cellulose raw material is even cheaper as an industrial waste product.
With plastic waste being one of the planet’s greatest challenges and nanotechnology one of mankind’s greatest research tools, combining the two to make practical and economic industrial products is the mark of what nanomaterials can do for manufacturing.
Photo credit: HeungSoon from Pixabay, Karin Muller from FreeImages, Alex Ling, Pexels, & Magda Ehlers from Pexels, Sabine Hueber from Pixabay, Juraj Lenhard from Pixabay