There is a desperate need to increase the amount of clothing that is recycled.
Data compiled by the EU parliament shows that, “The amount of clothes bought in the EU per person has increased by 40 % in just a few decades, driven by a fall in prices and the increased speed with which fashion is delivered to consumers.” The result is that, “Clothing accounts for between 2 % and 10 % of the environmental impact of EU consumption.”
As discussed in part one of this three-part article, there are two methods for recycling clothing. Mechanical recycling has its shortcomings in the damage it causes to the fibres.
Here we will therefore focus on chemical recycling; the dissolving or chemically manipulating of fibres into a simpler chemical form. A process which is not as easy as it might seem at first glance.
To learn more about the basics of recycling textiles, read: The Chemical Recycling of Clothes looks to be Big Business. Part 1; The Challenges
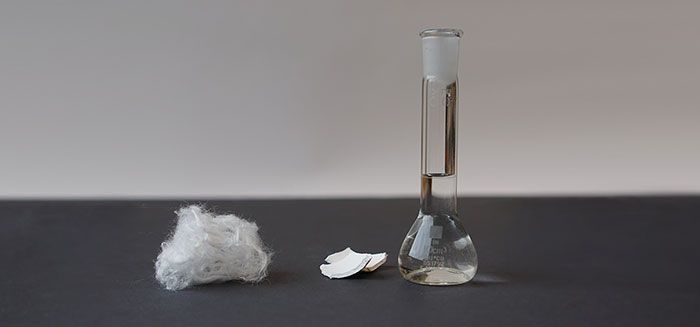
As the Guardian newspaper reports, “When it comes to chemical recycling, only polyester and certain nylons can currently be reprocessed. However, new technologies are being developed and cotton could be up next.”
With cotton accounting for almost a third of all fibres in textile production, it remains the holy grail for chemical recycling. As the environmental website, Medium, reports, “The annual production of cotton fiber is about 26 million tons with the yield about 823 kg per second! Cotton fibres contain more than 80% cellulose, with the remaining constituents which include waxes, proteins, and pectinic substances.”
With this in mind, a number of start-up companies are making progress towards chemically recycling cotton at an economically viable rate.
As the Guardian notes, “These pilots all have the same basic steps: mechanical removal of items such as zips and buttons, washing to remove dyes and the like, dissolving the cotton cellulose in a solvent and then spinning new fibres from the resulting pulp.”
The final product varies greatly from the chemical process used, either well-known fibre types or novel yarns.
For example, the American-based Evrnu produces what the company’s co-founder Christopher Stanev, describes as, “… ready to license technology to produce fibres from 100% post-consumer cotton using all currently available regenerated cellulose systems such as Lyocell, Rayon, Cupro, and Acetate.” Yet, it also makes a product called NuCycl from chemically recycled cotton. A new fibre which Stanev believes is, “… stronger than the cotton in its original form.” It is a fibre that is already being used (when mixed with virgin fibres) by both Adidas and Levi Strauss.

Similarly, the Swedish company Södra has also recently begun to commercially recycle cotton from polycotton. Starting in the autumn of 2019, the business converted 30 tonnes of waste textiles, but has long-term plans to operate their ‘OnceMore’ process on a larger scale, aiming to recycle 25,000 tonnes of used clothing each year.
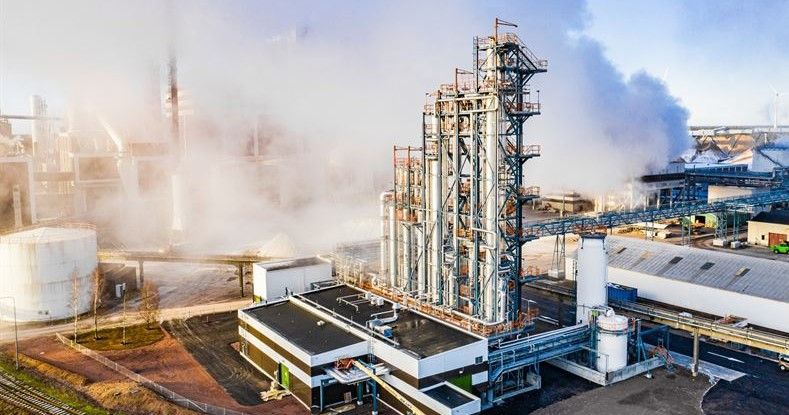
Meanwhile, in Finland, the company Infinited Fiber (a spin-off from research conducted at the VTT Technical Research Centre) produces a novel cellulose carbonate fibre from recycled cotton. The recycling process uses urea to modify the cellulose before the dissolution phase. By heating the urea, isocyanic acid is formed, which the hydroxl groups on the cellulose react with to create carbamates. This is then dissolved into a pulp from which fibres are spun via a viscose process.
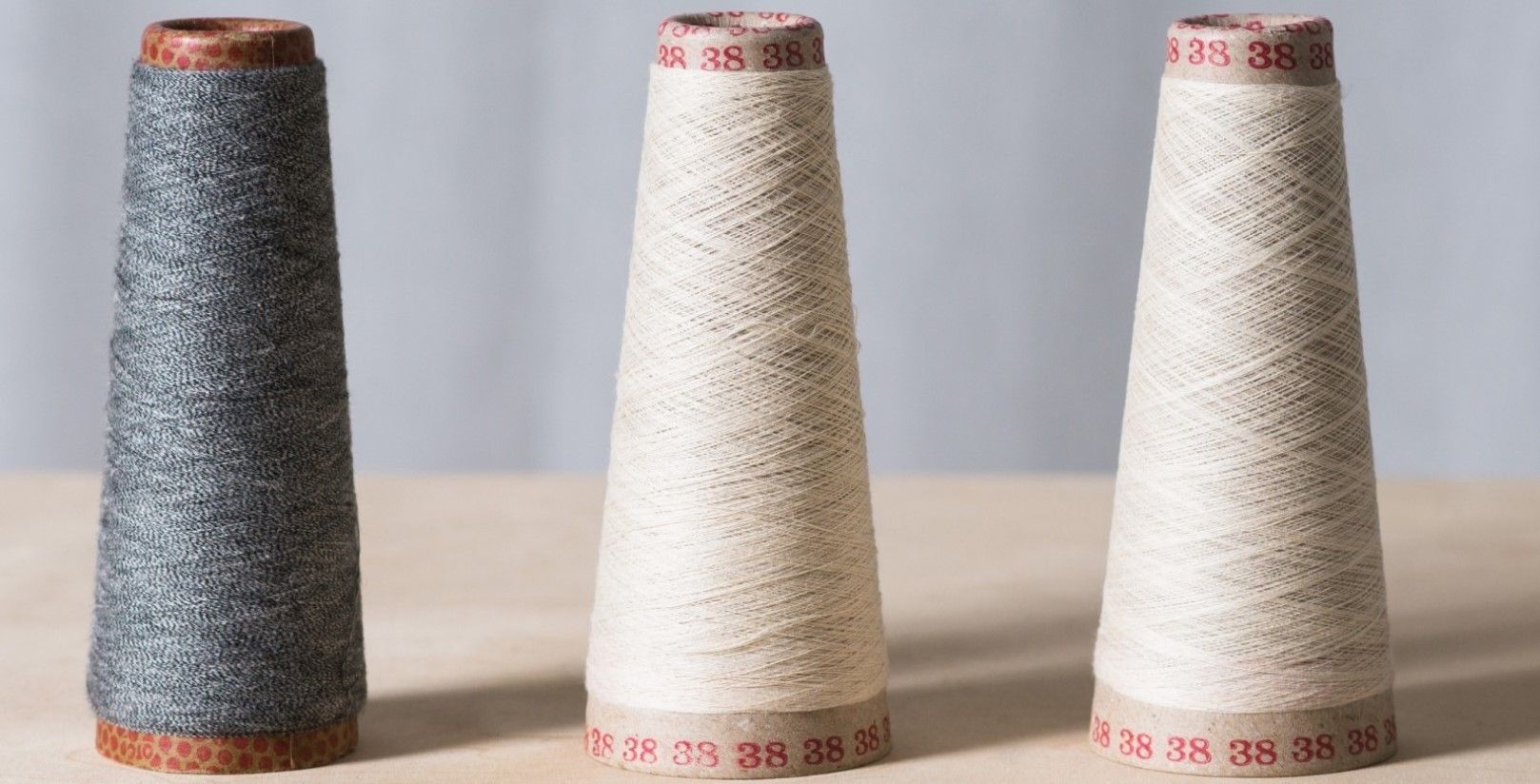
The final product has a strength and texture similar to virgin cotton fibres and can be used as such.
“We have applied them to make T-shirts, sweaters, jeans and towels,” says Harlin Ali, a textile research professor at VTT and the company’s co-founder. To date, Infinited Fiber has been operating a 50 ton per annum pilot plant near VTT in Espoo. However, the company has big plans for expansion. “A new 500 ton per annum plant will start operations early next year and a 25,000 tons per annum factory is planned late 2021,” says Ali, with the fibres being tested by major clothing companies such as H&M and VF Corporation.
With big names like these showing an interest, can it be long before the chemical recycling of clothing becomes mainstream?
Maybe, but the future is never laid out so clearly.
To find out what lies in store for chemical companies investing in the recycling of textiles, read: The Chemical Recycling of Clothes. Part 3; The Future
Photo credit: Aboutbiosynthetics, Designforlongevity, Wornagain, Mistrafuturefashion, BBC, JapanToday, Qz, Globalrecycling, Spectralengines, Medium, Theretailbulletin, Newsweek, Infinited Fiber, & Womensvoices