Economics and technology are forcing a sea change in the chemical recycling industry.
By demonstrating its financial feasibility and capacity to expand to meet the demands of a shifting plastics recycling sector, chemical recyclers and polymer feedstock suppliers are finding niche markets to survive alongside the bigger players in mechanical recycling.
Many of the scientific advances that are enabling today’s chemical recycling sector to flourish were still in the initial stages of research only a few years ago, with the main challenge being to gain sufficient funding for pilot projects and upscaling.
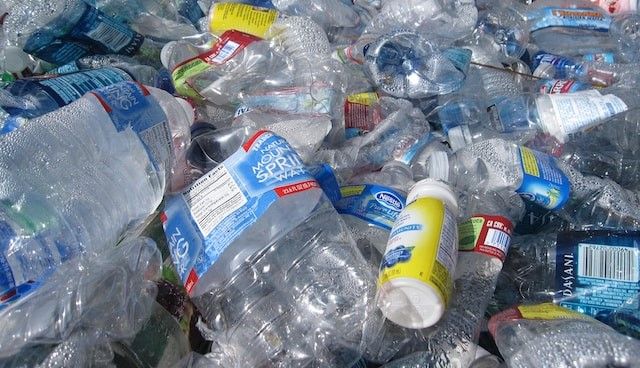
Now released from the lab, chemical recyclers have full backing from both huge chemical corporations, such as LyondellBasell, ExxonMobil, and Dow, as well as more specialist recycling companies like Cyclyx and PureCycle.
The goal is to process hard-to-recycle plastics so that can re-enter the economy without going to landfill.
Chemical recycling, as the journal Waste Dive explains, is, “also called advanced recycling or molecular recycling by the plastics industry, is a broad term for numerous processing technologies that break down recovered plastics to the molecular level to become ‘building blocks’ for new plastics or other products. Common techniques include pyrolysis, gasification and depolymerization.”
It is a technology which is drawing great attention as consumer demand for recycled plastics is rising at the same time that company and governmental commitment dates to lower emissions are fast approaching. Consequently, industry insiders are predicting that the coming years will determine how deeply ingrained chemical recycling becomes in the polymer feedstock landscape and whether many companies' scale-up plans will succeed in achieving commercial scale substantial enough to deliver on their promises.
“The fight comes as the plastic recycling rate has stagnated in the U.S.,” says Megan Quinn, a recycling industry analyst, “and lawmakers and local recyclers are pushing for more and better recycling infrastructure. At the same time, the public is putting more pressure on major brands to use more recycled content, prompting companies to make public recycled content goals they’ll need to meet by as early as 2025.”
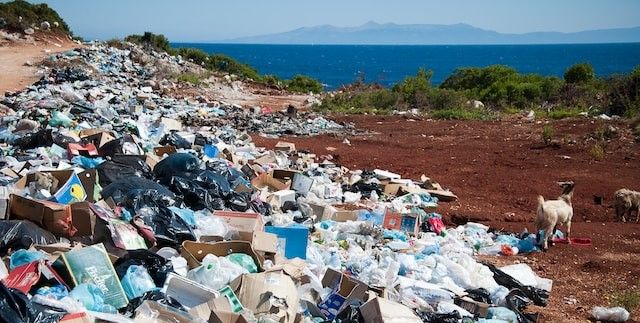
As this pressure builds, a coalition of leading brands and chemical companies has been formed with the aim of making up to 800,000 metric tons of chemically recycled plastics available by 2030. At the same time, the UN is working on an international legally binding agreement on plastic pollution, which it hopes will encompass chemical recycling as a means to clean up the world’s oceans, reduce landfill, and switch to a more circular economy.
Involving all levels of stakeholder to make this shift is complicated. Many developing nations lack even basic waste management systems, while 75% of plastic waste in the sea originates from Asian nations. America’s waste streams are well-managed, but its per capita plastic consumption is high, and it recycles only 5%. Europe leads the way with its Green Deal, but it still exports much of its waste plastic overseas for processing.
As a result, a large amount of diplomacy must be done before a streamlined, global system can be established to fully capture chemical recycling’s potential. Part of this involves chemical recyclers positioning themselves as an important partner to mechanical recycling, rather than existing in competition. Doing so would allow both sides to gain from accelerating waste separation systems.
Achieving this synergy will require acknowledging that some mixed plastics with lower values can be accepted by chemical recyclers but are not of interest to mechanical recyclers. This is partly because chemical recycling processes can handle mixed colours by filtering out dyes before breaking them down to the monomer level.
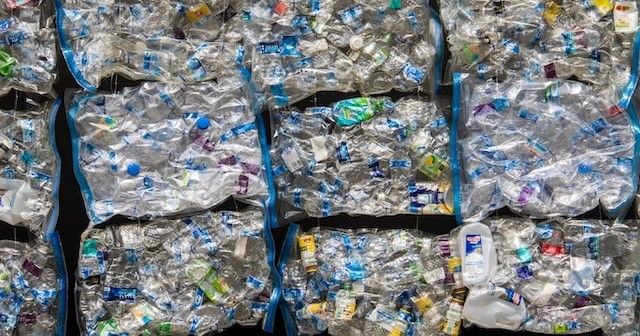
“If you look at the issue that we have in front of us, which is the challenge of plastic waste, it requires some really innovative solutions, but especially solutions that can give you scale because of the scale of the challenge,” observes Manav Lahoti, Dow’s global sustainability director for Hydrocarbons and Business. “Mechanical recycling is an important component, but it doesn't allow you to recycle these plastics at scale. That’s what advanced recycling does.”
It is a message that is frequently stressed by chemical recycling businesses, as they are not seeking to outbid mechanical recyclers for materials with established secondary markets, such as PET bottles and HDPE jugs.
“We're focused on streams that do not have good options or good homes within mechanical recycling,” said Holli Alexander, director of sustainability for specialty plastics at Eastman. “We want to expand the pie.”
It is an argument that is well accepted across the polymer feedstock supply chain.
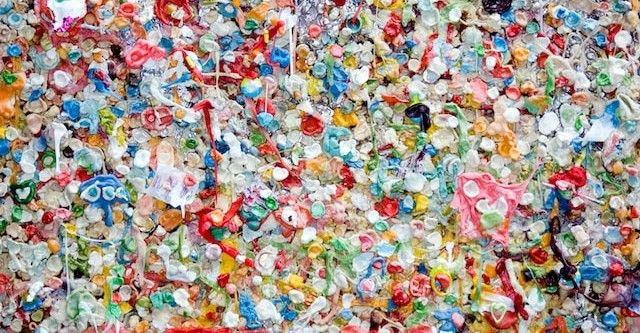
“We don't feel threatened by advanced recycling because it is going to have an operational cost that's significantly higher than mechanical recycling, so they're not going to be willing to pay the same amount for a bale,” says Will Sagar, executive director of the Southeast Recycling Development Council in America. “The mechanical recycler still has the competitive advantage to use the good material.”
“You'll hear from most everybody, whether you're on the chemical or mechanical side, that mechanical recycling should always get first priority [on recyclable material],” notes Brent Bell, WM’s vice president of recycling. “Even the big chemical recycling backers tell us that.”
Adding that, “I think there is still a heavy demand for chemical recycling facilities in the U.S., because naturally, mechanical recyclers can't take everything.”
Plastic film for example, is an ideal raw material for chemical recycling but is largely unsuitable for the mechanical sector. By working together, it is hoped that both sides of the polymer recycling sector can gain advantages over their common competitor - virgin plastic producers.
People are constantly looking to replace plastic with other raw materials, but its durability, pliability, strength, and other properties give it clear advantages over paper, metal, wood, and other feedstocks. Given that the technology now exists to chemically recycle so many plastics into a basic monomer building block, then the expansion of the chemical recycling sector should be a clear goal for any business or government striving to achieve circularity. Especially considering the sheer volume of plastic that world markets demand.
“Some people say the solution is to get rid of plastic or come up with some kind of magic chemistry — but each of those ‘solutions’ cannot handle [that many] pounds of plastic a year,” reasons the University of Buffalo’s Prof. Paschalis Alexandridis. “As a result, we need many different approaches, and need them soon.”
To learn more about the polymer feedstock sector, read: Can CO2 Become the Ultimate Polymer Feedstock? or The New Economic Value of Sustainable Plastic Feedstock
Photo credit: Tanvi Sharma on Unsplash, Nick Fewings, Antoine Giret, Marc Newbury, & Alexander Grey